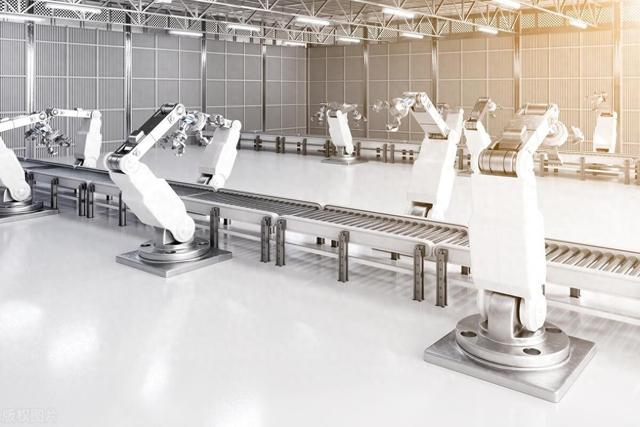
在现代工业的宏大舞台上,车间宛如一座繁忙的战场,流水线则是冲锋陷阵的主力军。那震耳欲聋的轰隆声,是机器们在高速运转时奏响的激昂战歌,象征着生产力的蓬勃与活力。然而,就像战场上随时可能出现的意外状况一样,这些看似坚不可摧的流水线也会突然“哑火”。
想象一下这样的场景:在一家大型汽车制造工厂里,车间里的流水线正有条不紊地运作着,工人们各司其职,紧张而有序地忙碌着。突然,那熟悉的轰隆声戛然而止,整个车间瞬间陷入了一种诡异的寂静之中。原本快速移动的传送带停止了转动,机械手臂也僵硬地停在了半空中。工人们先是一愣,紧接着便意识到大事不妙,纷纷停下手中的工作,脸上露出了焦虑和担忧的神情。
与此同时,维修团队得到消息后,如同接到紧急作战命令的士兵一般,抄起扳手等工具,风驰电掣般地冲向故障现场。然而,当他们赶到时,整条产线已经瘫痪了整整三个小时。这三个小时,对于工厂来说,意味着大量的生产时间被白白浪费,意味着无数的订单可能无法按时交付,意味着巨大的经济损失。而这样的场景,并非个例,它每天都在全球各地的工厂中不断地上演着。
传统的“故障后维修”模式,就如同给机器看急诊一样。只有当设备出现明显的故障症状,甚至到了“口吐白沫”的严重程度时,维修人员才会慌忙进行抢救。这种被动的维修方式,往往是在问题已经造成了严重后果之后才采取行动,就像是亡羊补牢,虽然能够解决当下的问题,但却无法避免之前已经造成的损失。而且,由于缺乏对设备故障的提前预判,维修人员在面对故障时,往往需要花费大量的时间和精力去查找问题的根源,这进一步延长了设备的停机时间,给企业带来了更大的损失。
相比之下,基于深度学习的预测性维护则像是给每台机器都配备了一位经验丰富、时刻守护的老中医。这位“老中医”能够在设备还没有出现明显故障症状的时候,通过对设备各项数据的细致分析和监测,提前发现潜在的问题,并及时采取相应的措施进行预防和修复。
工业传感器就像是机器的“脉搏”和“体温表”,它们不断地吐出温度、震动、电流等各种数据。在经验丰富的老师傅眼里,这些数据只是跳动的数字,虽然他们凭借多年的经验能够从中察觉到一些端倪,但却很难做到精准的预测。而在AI的眼中,这些数据却是流淌的生命体征,它们蕴含着机器运行状态的丰富信息。
以某车企的变速箱产线为例,在过去,这条产线每个月都会因为轴承故障而停机6次。每次停机都需要花费大量的时间和人力进行维修,严重影响了生产效率。为了解决这个问题,企业决定采用基于深度学习的预测性维护技术。他们在齿轮箱上安装了振动传感器,这些传感器就像是一双双敏锐的眼睛,时刻监测着齿轮箱的振动情况。同时,企业利用LSTM网络对传感器采集到的时间序列数据进行分析。LSTM网络就像是一个聪明的大脑,它能够学习和理解数据中的规律和模式,从而对设备的故障进行准确的预测。
这就好比给机器戴上了动态心电图仪,能够实时记录机器的“心跳”情况。通过对大量数据的分析和学习,LSTM网络能够提前72小时对轴承故障进行预警,而且预警的准确率飙升至91%。这意味着企业在设备出现故障之前就能够得到通知,有足够的时间做好维修准备,从而避免了设备的突然停机,大大提高了生产效率,减少了经济损失。
二、CNN和LSTM这对工业神探,怎么破译机器"临终遗言"?第一招:卷积神经网络当"火眼金睛"在液晶面板质检车间里,质量检测是一道至关重要的工序。每一块液晶面板都需要经过严格的检查,以确保其没有任何缺陷。然而,由于液晶面板的生产工艺非常复杂,即使是微小的划痕或裂纹也可能会影响其显示效果,因此检测的难度非常大。
传统的质检方式主要依靠人眼来进行检测。工人需要长时间盯着8K摄像头拍摄的屏幕,仔细查找面板上的缺陷。然而,人眼的注意力和精力是有限的,长时间盯着屏幕会导致眼睛疲劳,从而出现漏检的情况。据统计,在传统的质检方式下,缺陷识别率只能达到92%左右,这意味着每100块面板中就可能有8块存在缺陷却没有被检测出来。
为了解决这个问题,某厂商决定采用卷积神经网络(CNN)来搭建视觉检测系统。CNN就像是拥有一双“火眼金睛”,它能够在百万张缺陷图中进行学习和训练,从而练就“像素级敏感”的能力。在训练过程中,CNN会对大量的缺陷图像进行分析和处理,学习不同类型缺陷的特征和模式。通过不断地调整和优化网络参数,CNN能够逐渐提高对缺陷的识别能力。
当实际进行检测时,CNN视觉检测系统能够快速、准确地识别出液晶面板上的各种缺陷。即使是比头发丝细三十倍的裂纹,也无法逃脱它的“法眼”。经过实际应用验证,该系统将缺陷识别率从92%提升到了99.8%,大大提高了产品的质量和生产效率。
在这个过程中,CNN的工作原理就像是一个经验丰富的侦探,它会对每一个像素点进行细致的分析和比对,寻找其中的异常特征。一旦发现可疑之处,它就会立即发出警报,提醒工作人员进行进一步的检查和处理。这种高效、准确的检测方式,不仅节省了大量的人力和时间成本,还提高了产品的质量和市场竞争力。
第二招:LSTM化身"时间捕手"空压机在工业生产中扮演着重要的角色,它为各种设备提供压缩空气,确保生产的正常运行。然而,空压机的电机轴承在长时间的运行过程中,容易出现损坏的情况。一旦电机轴承损坏,不仅会影响空压机的正常运行,还可能导致整个生产线的停机,给企业带来巨大的损失。
传统的维修方式往往是在空压机出现明显故障症状之后才进行维修,这样做不仅会增加维修成本,还会影响生产进度。为了实现对空压机电机轴承故障的提前预测,某装备厂决定采用长短期记忆网络(LSTM)来处理空压机的时序数据。
LSTM就像是一个“时间捕手”,它能够捕捉到数据中的时间依赖关系。在这个案例中,装备厂收集了空压机三个月的时序数据,包括电流、温度、振动等各种参数。LSTM对这些数据进行深入分析和学习,发现电机轴承在损坏前48小时会出现特定频率的“死亡颤音”。
这种“死亡颤音”是电机轴承即将损坏的一个重要信号。通过对这个信号的监测和分析,装备厂能够提前48小时得知电机轴承可能会出现故障,从而有足够的时间做好维修准备。这就好比老维修工凭借多年的经验听声辨故障一样,LSTM通过对数据的分析和学习,实现了这种能力的数字化升级。
在实际应用中,装备厂利用LSTM的预测结果,提前安排维修人员对空压机进行检查和维护,及时更换即将损坏的电机轴承。这样一来,不仅避免了空压机的突然停机,还延长了设备的使用寿命,降低了维修成本。
第三招:数字孪生玩转"平行宇宙"在工业生产中,如何快速、准确地制定设备的维护策略是一个难题。传统的维护方式往往是基于经验和规则,缺乏针对性和灵活性。为了解决这个问题,数字孪生技术应运而生。
数字孪生的概念就像是给整条产线造了一个虚拟分身,这个虚拟分身与真实的物理设备实时映射,能够反映出物理设备的运行状态和性能。某半导体厂就是数字孪生技术的积极实践者。
在这家半导体厂中,生产线上的设备非常复杂,一旦出现故障,维修难度和成本都非常高。为了提高设备的可靠性和维护效率,该厂将物理设备与数字模型进行了实时映射。通过传感器和数据采集系统,将物理设备的各种数据实时传输到数字模型中,数字模型会根据这些数据进行实时更新和模拟。
同时,该厂还利用强化学习在虚拟世界中模拟十万次故障。强化学习就像是一个智能的决策者,它会在虚拟世界中不断尝试各种不同的维修策略,并根据维修效果进行奖励和惩罚。通过大量的模拟和学习,强化学习能够找出最优的维护策略。
当真实设备出现异常时,系统会立即调取“平行时空”的维修方案。由于虚拟世界中的模拟和学习是在计算机上进行的,速度非常快,因此决策速度比人类快200倍。这意味着在设备出现故障的瞬间,系统就能给出最优的维修方案,大大缩短了维修时间,提高了生产效率。
数字孪生技术就像是为企业打开了一个“平行宇宙”,在这个“平行宇宙”中,企业可以对设备进行各种模拟和测试,提前发现潜在的问题,并制定相应的解决方案。这种创新的技术不仅提高了企业的生产效率和竞争力,还为工业生产的智能化发展提供了新的思路和方法。
三、智能运维的尽头,是机器给人开诊断书?在广东的一家注塑车间里,一场悄然的变革正在发生。车间里的每一台机器上都贴着一个小小的二维码,这个二维码就像是机器的“身份证”,里面蕴含着机器的各种信息。而现在,这些机器开始反向输出健康报告,为自己的运行状态进行“诊断”。
每天晨会的时候,厂长不再像过去那样焦急地询问“机器能撑多久”,而是平静地查看系统推送的维保清单。这个智能中枢就像是一位贴心的管家,它已经学会了根据设备的寿命、生产排期、备件库存等各种因素,自动生成最优的维修日历。
在过去,注塑车间的设备维修往往是被动的。当设备出现故障时,维修人员才会匆忙进行维修,这种方式不仅效率低下,还会影响生产进度。而现在,有了智能中枢的帮助,维修人员可以提前做好维修准备,合理安排维修时间,避免了设备的突然停机,提高了生产效率。
例如,智能中枢会根据设备的运行时间和性能数据,预测设备可能出现故障的时间。如果发现某台设备的某个部件即将达到使用寿命,它会提前提醒维修人员进行更换。同时,智能中枢还会根据生产排期,合理安排维修时间,避免在生产高峰期进行维修,从而保证了生产的连续性和稳定性。
更具颠覆性的变革正在悄然发生。某风电集团采用了迁移学习技术,将东南沿海风机的故障模型直接套用到西北高原的新机组上。在过去,每一个新的机组都需要重新进行故障模型的训练,这不仅需要大量的时间和数据,还需要专业的技术人员进行操作。而迁移学习技术的出现,打破了这种“一个萝卜一个坑”的定制化困局。
迁移学习就像是一个知识搬运工,它能够将已经在一个领域中学习到的知识和经验,迁移到另一个相似的领域中。在这个案例中,东南沿海和西北高原的风机虽然所处的环境不同,但它们的基本结构和工作原理是相似的。因此,风电集团可以将东南沿海风机的故障模型进行适当的调整和优化,然后直接应用到西北高原的新机组上。
这种技术的应用,省去了重新训练的时间和成本,大大提高了故障预测的效率和准确性。这预示着未来工业AI或将实现故障预测的“西医标准化诊疗”。就像西医在诊断疾病时,有一套标准化的流程和方法一样,工业AI也可以通过建立统一的故障模型和诊断标准,对不同的设备进行快速、准确的故障预测和诊断。
当深度学习穿透钢铁躯壳读懂机器语言时,制造业正经历着一场从“坏了再修”到“未病先治”的范式革命。在过去,制造业的维修模式主要是基于故障后维修,这种模式往往是被动的、滞后的。而现在,随着AI技术的发展,制造业逐渐转向预测性维护,通过对设备数据的实时监测和分析,提前发现潜在的问题,并采取相应的措施进行预防和修复。
或许在不久的将来,车间的维修工将转岗成AI训练师。他们不再需要拿着扳手和螺丝刀去维修设备,而是需要掌握AI技术,对设备的故障模型进行训练和优化。同时,每台机器都会用数据流讲述自己的生命故事。它们会通过传感器和数据采集系统,将自己的运行状态和性能数据实时传输到智能中枢中,智能中枢会对这些数据进行分析和处理,生成设备的健康报告和维修建议。
这才是工业4.0最性感的模样。工业4.0不仅仅是技术的升级和变革,更是一种全新的生产理念和管理模式。它将人工智能、大数据、物联网等先进技术与制造业深度融合,实现生产的智能化、自动化和高效化。在工业4.0的时代,机器不再是冷冰冰的生产工具,而是具有自我诊断和自我修复能力的智能伙伴。它们与人类共同协作,创造出更加美好的未来。