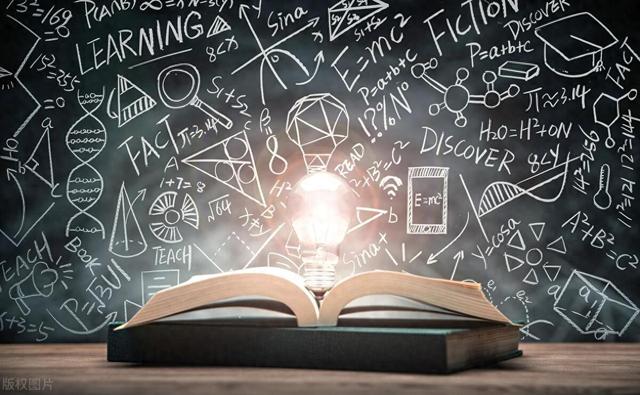
在当今高度工业化的时代,工厂里的机器设备就如同战场上的士兵,是推动生产运转的核心力量。然而,这些钢铁巨兽却常常在关键时刻掉链子,给企业带来巨大的损失。让我们把目光聚焦到深夜的一个车间里,这里是长三角某汽车配件厂的生产现场。
这个汽车配件厂在行业内颇具规模,承担着为众多知名汽车品牌供应关键配件的重任。车间里灯火通明,巨大的流水线在夜以继日地运转着,发出有节奏的轰鸣声,仿佛是工业时代的脉搏。价值千万的精密设备整齐排列,它们是生产高质量汽车配件的关键所在。每一台设备都经过精心调试,承载着企业的希望和无数订单的压力。
然而,就在这个看似平静而有序的夜晚,意外突然降临。流水线毫无征兆地停摆了,原本快速移动的配件瞬间静止,整个车间仿佛被按下了暂停键。紧接着,价值千万的精密设备上闪烁起了故障红灯,那刺眼的红光在黑暗的车间里格外醒目,仿佛是危险的信号。工人们纷纷从睡梦中惊醒,匆忙赶到车间,脸上满是焦急和无奈。
原来,在过去的三年里,类似的设备突发故障已经多次发生。每次故障都意味着生产的停滞、原材料的浪费以及订单的延误。据统计,该厂因设备突发故障损失产能超2.7亿元。这是一个惊人的数字,它不仅影响了企业的经济效益,还对企业的声誉造成了一定的损害。
传统的设备运维方式就像给机器把脉的老中医。经验丰富的工程师们凭借着多年积累的经验,通过观察设备的运行状态、倾听设备的声音、感受设备的振动等方式来判断设备是否存在故障。他们就像一群技艺高超的医生,在设备出现问题时,凭借着自己的直觉和经验进行诊断和治疗。然而,这种方式存在着很大的局限性。一方面,工程师的经验是有限的,不可能涵盖所有的故障情况;另一方面,随着设备的智能化和复杂化程度越来越高,传统的运维方式已经难以满足实际需求。
就在传统运维方式面临困境的时候,机器学习正在悄然掀起一场工业诊疗革命。在珠三角某3C制造基地,强化学习系统已经开始发挥重要作用。这个3C制造基地是全球电子产品制造的重要枢纽之一,生产的产品涵盖了手机、电脑、平板电脑等各种消费电子产品。这里的设备数量众多、种类繁杂,对设备的稳定性和可靠性要求极高。
强化学习系统通过分析主轴电机电流谐波、轴承振动频谱等283个传感器数据,构建设备健康度数字孪生体。这些传感器就像设备的“眼睛”和“耳朵”,能够实时监测设备的运行状态,并将数据传输到系统中进行分析。数字孪生体则是设备的虚拟模型,它能够准确地反映设备的实际运行情况。通过对数字孪生体的分析,系统可以提前发现设备存在的潜在故障。
有一次,热成像图显示某数控机床主轴温度异常波动。按照传统的方式,系统可能只是简单地发出报警信号,通知工程师进行检查和维修。然而,强化学习系统却表现出了更加智能的一面。它不是简单地报警,而是动态调整同产线其他设备负荷。就如同老练的急诊医生在抢救病人的同时,还能合理调配医疗资源,确保整个医疗过程的高效进行。系统通过调整其他设备的负荷,减轻了故障设备的压力,避免了故障的进一步扩大,同时保证了生产线的正常运转。
(二)算法驯服钢铁巨兽在工业生产的各个领域,机器设备的性能和稳定性直接关系到产品的质量和企业的效益。然而,很多企业都面临着设备运行不稳定、产品良品率低等问题。某光伏玻璃厂就是其中之一。
这家光伏玻璃厂致力于生产高品质的光伏玻璃,为太阳能电池板提供关键的封装材料。然而,长期以来,该厂一直深陷良品率魔咒。5毫米超薄玻璃在钢化炉内受热不均,导致玻璃表面出现热应力裂纹,严重影响了产品的质量。每个月,因为热应力裂纹而报废的玻璃价值堪比三线城市的一栋别墅,这让企业的管理层忧心忡忡。
为了解决这个问题,该厂引入了深度强化学习技术。深度强化学习是一种基于机器学习的算法,它通过智能体与环境的交互,不断学习和优化策略,以实现特定的目标。在光伏玻璃生产中,深度强化学习系统将炉温控制分解为728个决策节点,每个节点对应0.1秒的温度微调。这就好比是一场精密的手术,每一个决策都至关重要。
系统就像训练猎鹰捕捉移动目标一样,在虚拟数字孪生环境中进行了18万次试错。在这个虚拟环境中,系统模拟了各种不同的生产条件和参数设置,不断尝试寻找最优的温度控制策略。每一次试错都是一次学习的过程,系统通过分析试错结果,不断调整自己的策略。经过无数次的尝试和优化,系统终于找到了动态平衡点。
在实际应用中,深度强化学习系统发挥了巨大的作用。它将热应力裂纹发生率从23%压至0.7%,大大提高了产品的良品率。这不仅为企业节省了大量的成本,还提升了企业在市场上的竞争力。
更精妙的博弈发生在半导体蚀刻车间。半导体蚀刻是半导体制造过程中的关键工艺之一,它直接影响到芯片的性能和质量。在某半导体蚀刻车间,当某批12英寸晶圆出现膜厚偏差时,传统的控制方法需要停机6小时来校准参数。这不仅浪费了大量的时间和资源,还会影响到整个生产计划的进度。
现在,Q - learning算法登场了。Q - learning是一种基于强化学习的算法,它通过学习最优的动作价值函数,来实现智能决策。在半导体蚀刻过程中,Q - learning算法实时解析等离子体光谱特征,在0.03秒内调整射频功率与气体流速。这就好比是顶级围棋手在棋盘上迅速落子布局,每一步都精准无误。
这套系统在300维参数空间里进行复杂的决策,将工艺波动缩小到原子层级别。它能够根据实时监测到的等离子体光谱特征,准确判断晶圆的蚀刻状态,并迅速调整射频功率和气体流速,确保蚀刻过程的稳定性和一致性。通过使用Q - learning算法,半导体蚀刻车间的生产效率得到了大幅提高,产品质量也得到了显著提升。
(三)黎明前的技术暗礁虽然机器学习和强化学习在工业生产中展现出了巨大的潜力,但在实际推广和应用过程中,仍然面临着诸多挑战和技术暗礁。长三角某重工集团就是一个典型的例子。
这家重工集团是行业内的领军企业,拥有先进的生产设备和雄厚的技术实力。在尝到了机器学习带来的甜头后,集团决定在更多的设备上推广应用相关技术。他们将12台龙门铣床进行联网,希望通过算法实现设备的智能化管理和优化运行。
在北方的工厂里,这套算法表现卓越。北方的气候干燥,环境相对稳定,设备的运行状态也比较平稳。算法能够准确地分析设备的运行数据,提前发现潜在的故障,并及时采取措施进行处理。这使得龙门铣床的生产效率大幅提高,设备的故障率显著降低。
然而,当这套算法被应用到南方的工厂时,问题却接踵而至。南方的气候湿润,尤其是在雨季,空气湿度明显增加。湿度的变化导致振动传感器基线漂移,使得算法接收到的设备运行数据出现偏差。算法基于这些不准确的数据进行判断和决策,结果频频误判。有时候,设备明明运行正常,但算法却发出了故障警报;而有时候,设备已经出现了潜在的故障,算法却没有及时发现。
这就像培养出了一位百米冠军,却要求他立即适应高原马拉松的比赛环境。虽然百米冠军在平坦的赛道上能够发挥出自己的优势,但在高原地区,由于空气稀薄、氧气含量低等因素的影响,他的表现可能会大打折扣。同样,算法在北方工厂的稳定环境中表现出色,但在南方工厂的特殊环境下,却暴露出了现有模型泛化能力的软肋。
某新能源汽车电池厂则遭遇了“数据荒漠”的困境。新能源汽车电池是新能源汽车的核心部件,其生产工艺复杂,对产品质量的要求极高。电解液注液工艺是电池生产过程中的关键环节之一,涉及到商业机密。由于企业对商业机密的保护,可供学习的缺陷样本不足千例。这使得机器学习算法在训练过程中缺乏足够的数据支持,难以准确地学习到缺陷的特征和规律。
为了解决这个问题,研究人员转而采用元强化学习框架。元强化学习是一种能够快速适应新环境和新任务的强化学习方法。研究人员让算法先在虚拟材料实验室合成3.6万组异构数据进行训练。在虚拟材料实验室中,研究人员可以模拟各种不同的生产条件和缺陷情况,生成大量的训练数据。算法通过对这些虚拟数据的学习,掌握了缺陷的基本特征和规律。
然后,研究人员将训练好的算法迁移到真实产线进行微调。在真实产线中,算法根据实际的生产数据进行进一步的优化和调整。这种“先模拟考再实战”的策略取得了显著的效果。通过采用元强化学习框架,电池厂将电芯合格率提升了19个百分点。这不仅提高了产品的质量和生产效率,还为企业节省了大量的成本。
(四)未来工厂的进化密码当清晨的第一缕晨光穿透车间顶棚,洒在那些植入强化学习的设备上时,它们正在书写新的工业史。这些曾经冰冷的钢铁傀儡,如今已经发生了质的变化。它们不再是被动地执行代码,而是成为了懂得权衡短期产量与长期损耗的智能体。
想象一下,一个经验丰富的老工匠,经过半世纪的打磨和实践,积累了丰富的直觉和经验。他能够凭借着自己的直觉,准确地判断出材料的质量、工艺的好坏以及产品的潜在问题。而现在,这些老工匠的直觉被量化成了数学模型,融入到了设备的智能决策中。每一个决策都闪烁着人类智慧与机器算力的双重光芒。
在未来的工厂里,这些智能设备将发挥更加重要的作用。它们能够实时监测设备的运行状态,根据生产需求和设备的健康状况,自动调整生产参数和生产计划。当设备出现潜在故障时,它们能够提前预警,并自动采取措施进行修复或调整,避免生产的停滞和损失。
这场变革远未抵达终点。随着科技的不断发展,5G边缘计算、数字孪生、多模态感知融合等技术正逐渐应用到工业生产中。当5G边缘计算遇上数字孪生,设备之间的通信将变得更加高效和实时。数字孪生技术可以为设备建立更加精确的虚拟模型,通过5G边缘计算,实时获取设备的运行数据,并对虚拟模型进行更新和优化。这使得企业能够更加准确地预测设备的故障和性能,提前采取措施进行预防和处理。
多模态感知融合技术则可以突破数据孤岛的限制。在传统的工业生产中,不同的传感器和设备产生的数据往往是孤立的,难以进行有效的整合和分析。多模态感知融合技术可以将来自不同传感器和设备的数据进行融合,提取更加全面和准确的信息。这使得算法能够更加深入地了解设备的运行状态和生产过程,做出更加智能和精准的决策。
到那时,凌晨三点的故障警报或许会变成一杯机器自愈的庆功酒。在算法的世界里,每一次故障都不再是灾难,而是通向更高维度的阶梯。机器通过不断地学习和进化,能够自动识别和修复故障,实现自我优化和升级。未来的工厂将变得更加智能、高效、灵活和可持续,成为工业4.0时代的典范。
这场工业智能革命正在改变着我们的生产方式和生活方式。它不仅为企业带来了巨大的经济效益和竞争优势,也为人类社会的发展做出了重要贡献。让我们拭目以待,见证未来工厂的辉煌变革。