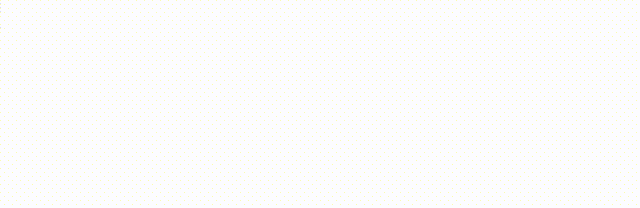
文|煮酒
编辑|煮酒
前言复合材料因其优异的力学性能而在航空航天等领域得到广泛应用。制造工艺的改进对提高复合材料部件的性能起着至关重要的作用。近年来,自动化制造技术如自动光纤铺放(AFP)和树脂传递模塑(RTM)得到了快速发展。这些技术实现了高精度、高效率的制造,降低了劳动力成本。
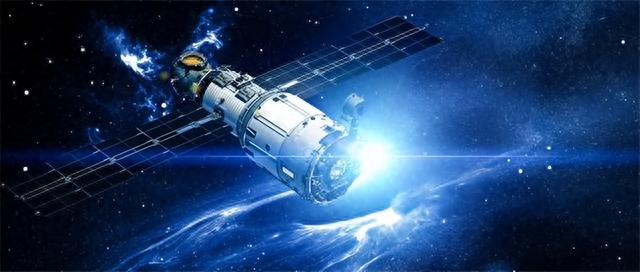
然而,自动化制造过程会向复合材料内部引入残余应力,影响材料的力学性能及结构完整性。因此,准确测量和表征复合材料中的残余应力显得尤为重要。
目前,X射线衍射、层去除法、光纤传感器等多种技术已被用于复合材料残余应力的测试。但钻孔法因其高精度、无损伤等优点,在测量复合材料内部残余应力方面具有独特优势。大量研究工作致力于探究不同制造工艺诱导的复合材料残余应力。
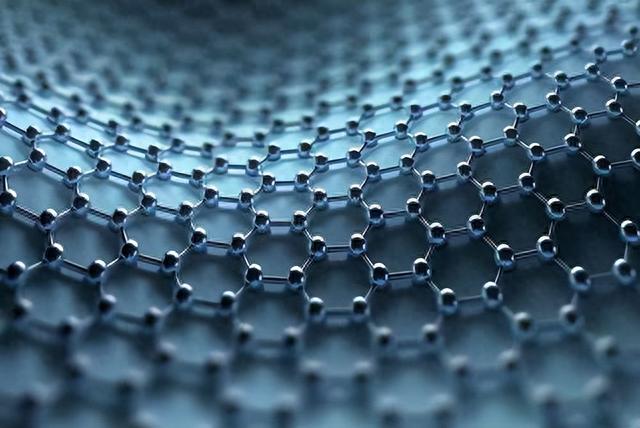
然而,对自动化制造过程诱导残余应力的研究相对较少。增量钻孔法已被证实是一个有效的残余应力测试手段,但未广泛应用于自动化制造的复合材料。
RFP 流程制造如前所述,在电流分析中研究了贴装速度、压实力、贴装温度、热通量(氮气流量)以及气体割炬尖端与工件之间的距离。每个实验在相同条件下重复三次,表总结了当前分析中制造和测试的试样。
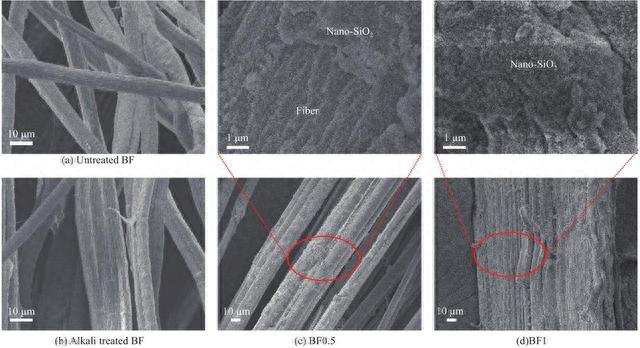
每个工艺参数的中性值设置为100 mm/s的贴装速度、250 N压实力、250°C加热温度、最大流量的70%,最后是与压实辊尖15 mm的割炬距离。样品被制造和固化,然后在测量RS之前,热固性复合材料结构在没有固化的情况下不能承受载荷,这归因于缺乏材料强度。
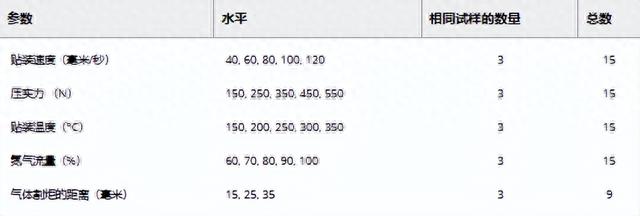
然而,据信AFP会影响最终复合材料产品中的诱导RS,原因有很多,包括每个叶片的边界条件和约束的变化,由于加热温度升高在材料加工过程中层内发生局部和局部固化,以及树脂的化学结构随温度的变化。
放置速度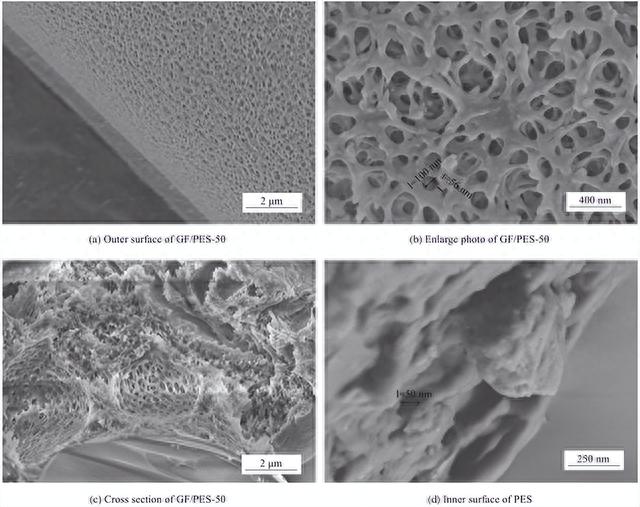
制造过程中贴装速度的变化对复合材料结构内部的感应RS有重大影响。目前的实验是在一系列贴装速度下进行的,从40毫米/秒开始,到120毫米/秒结束。
上限是根据最大速度设置的,该速度可用于确保有足够的时间来加热和压缩预浸料丝束以将它们粘合在工具表面或前几层上。此外,设置下限以避免层压板上出现任何过热和过载。
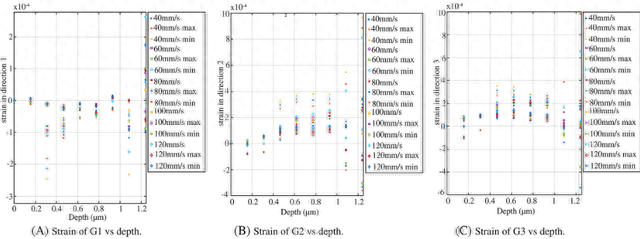
在对复合层压板的每一层钻孔后,读数从量规中存储。这些值显示了三个方向上八层的应变。然而,最后两层的测量应变并不可靠,因为相同测试的最大值和最小值之间存在巨大差异,达到平均值的近300%。
此外,三个量规在所有条件下的值都显示出不一致的趋势,最大值有时会超过材料强度。
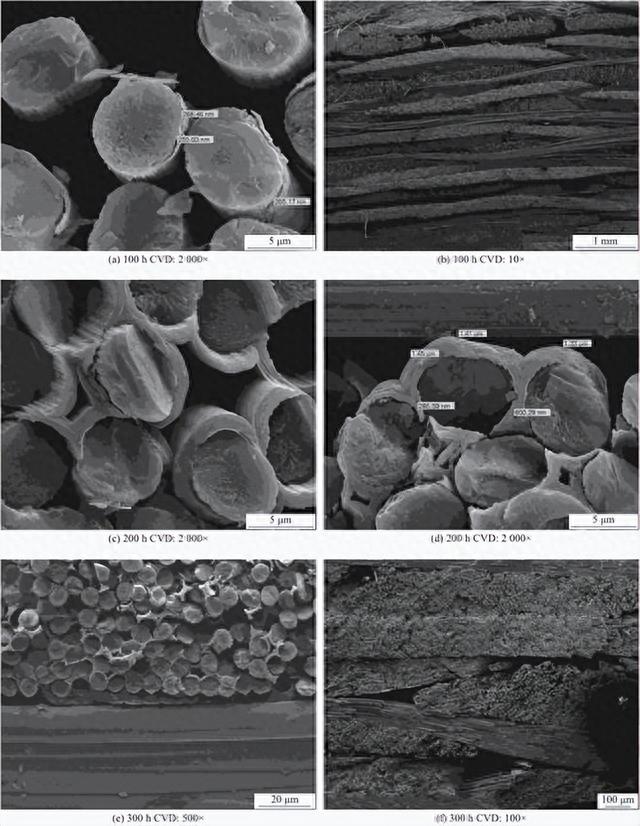
这强调盲孔深度越大,测量的表面应变精度就越低,特别是对于与获得的结果一致的薄层合板。此外,前六层的误差线限制在最大值和最小值之间显示较低的范围,最大跨度为20%。
因此,电流分析仅考虑用于计算感应RS的前六层,给出了五种不同速度下最大测量RS的大小。
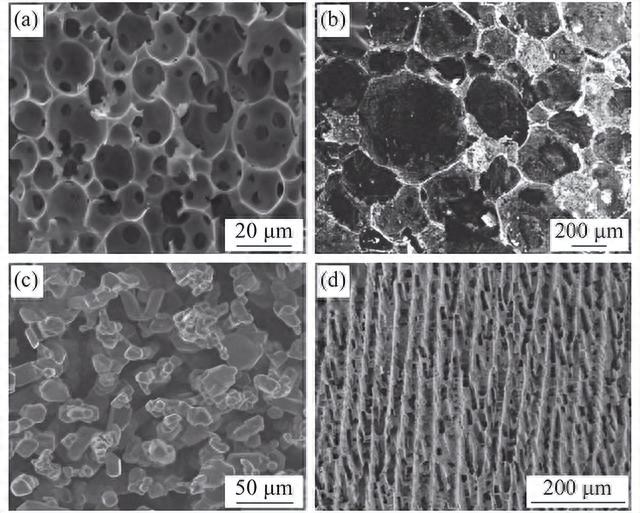
整个情况下的最大应力方向在光纤方向的 ±2° 以内,这是由于纤维和基质在这个方向上的性质存在显著差异。结果表明,当降低贴装速度时,RSs增加,这是由热量和压缩时间的增加引起的。
在 40 mm/s 的贴装速度下测量了大值,因为据信该材料由于在极低的制造速度下 250°C 的巨大热通量而归因于原位固化。
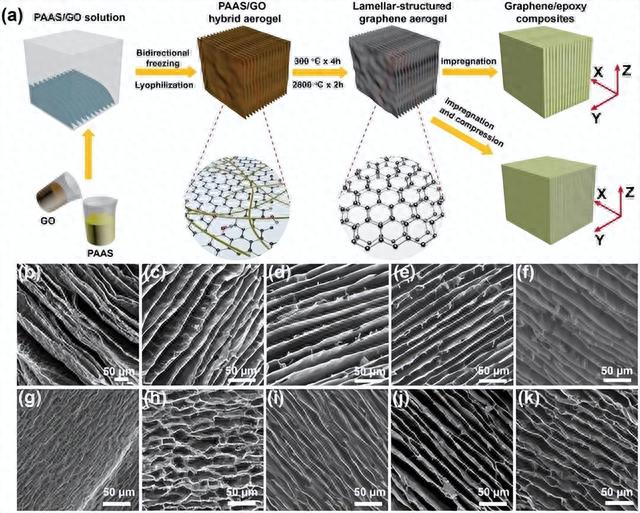
值得一提的是,样品的粘性显著降低,树脂变得更加固体,这被认为是部分固化树脂的明确指示。
此外,在靠近表面的两层中测量的RS之间的间隙主要是由于热边界条件之间的差异,因为表面层受到温度相对较低的空气的热对流,而内层则通过传导到其他加热层进行冷却,这种间隙在较慢的速度下增加,这归因于较高的加热时间以及随后两层热边界条件之间的差异。
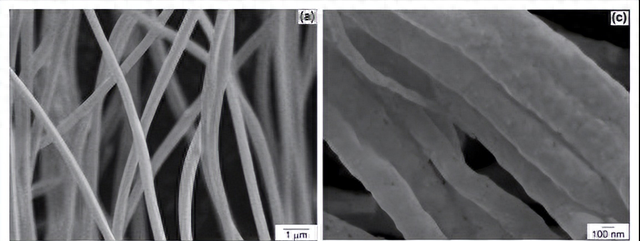
AFP 依赖于压实,以在模具或前一层顶部沿特定方向铺设丝束。改变施加的压力会影响层压板的最终几何形状,从而影响材料内部产生的应力,特别是如果层压板在制造过程中经历部分固化。
数据显示,在较高深度测量 RS 时,不同放置压力之间的间隙增加;此外,在大多数情况下,第7层和第8层的误差幅度很大,这加强了增量HDM可以在当前条件下测量薄复合材料层压板厚度最大40%以内的非均匀RS的论点。
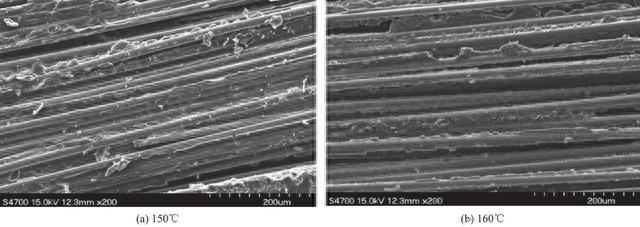
第三个应变片的测量值上升幅度大于其他两个应变片,因为当前样品是单向的,在光纤垂直方向上的刚度较低。然而,这个方向上的大多数应变都是正的,这归因于这个方向的压缩RS。
如果加工温度比树脂的玻璃化转变温度升高10-25°C以上,则原位固化的可能性增加。将复合材料暴露在高温下将显着缩短固化时间。
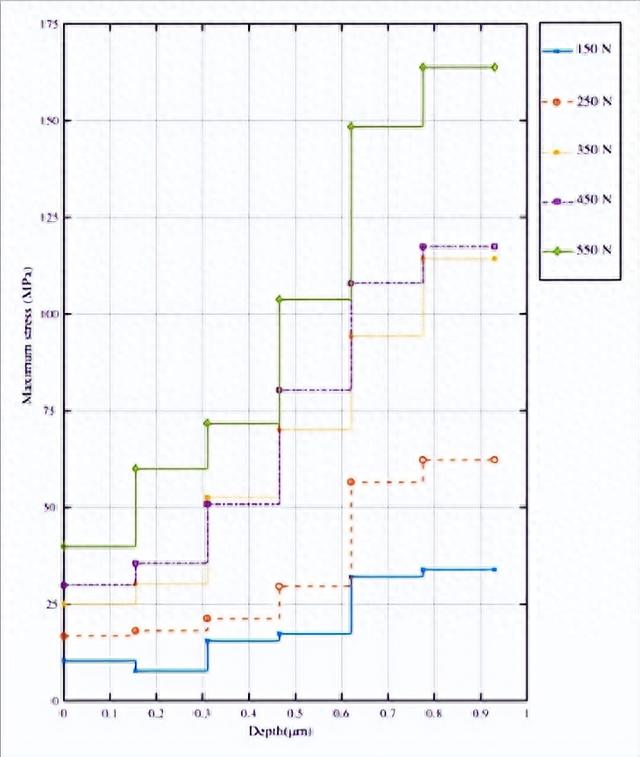
当前材料中的树脂为2510型,玻璃化转变温度为140°C,而目前的实验在250°C下进行。
因此,工件可能会经历一定程度的固化,这在施加更高的压缩力时会导致 RS 的发展。压缩力越大,树脂中发生的变形就越大,产生的拉应力就越大。图中还显示了两个试样之间的厚度减少;第一个试样在低压实力下制造,第二个试样在高力下制造。
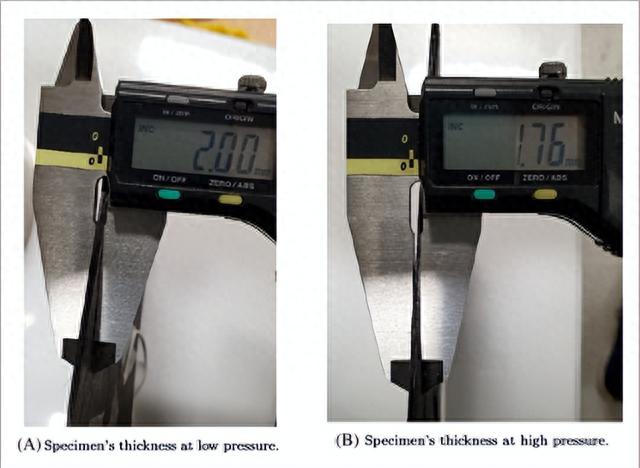
因此,增加层压板的压力也会压缩层并用树脂填充任何内部间隙,从而增加层之间的接触面积。随后,层之间的剪切力可能会增加,并导致冷却时对内层收缩的更多限制。
值得一提的是,由于机器人的每次通过都会增加前几层的机械载荷,因此RS在更高的深度增加,这增加了下层的应力值。
放置温度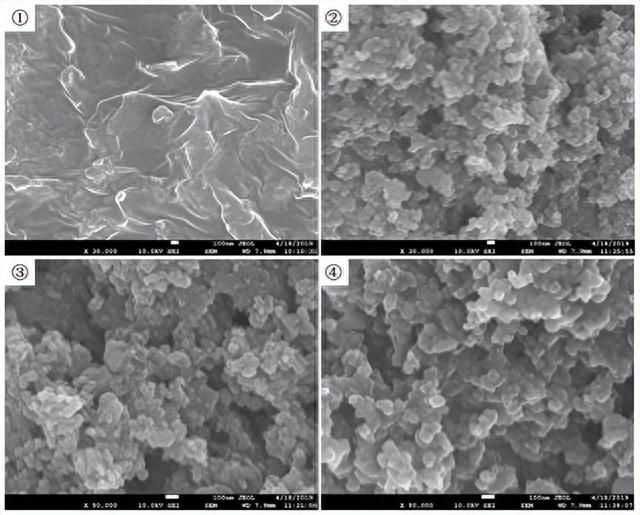
工艺诱导的RS的主要部分是由在贴装过程中暴露于复合材料的热气流产生的。铺层过程中加热过程的一个关键因素是气体温度。在应用RFP制造热固性复合材料时,已经进行了建立工艺温度与复合材料质量之间的关系。
为了获得最佳复合材料质量,贴装工艺的最佳条件为450°C。 然而,在高于树脂玻璃化转变温度的温度下应用贴装工艺,除了增加冷却后基体的热膨胀和化学收缩外,还增加了复合材料层压板原位固化的机会。
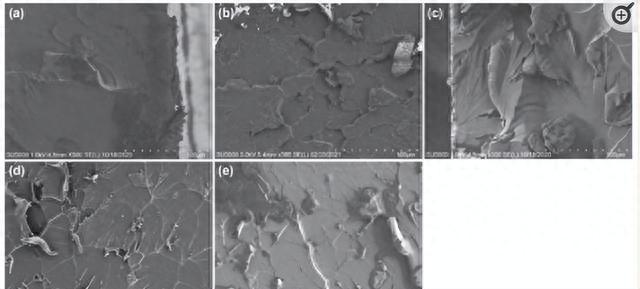
因此,由于更高的热通量,预计在当前的热固性材料中会感应出更多的RS。
更高的温度意味着树脂的热收缩越多,然后更多的诱导RS和更多的环氧树脂燃烧的可能性,而较低的温度意味着热通量不足以达到粘合层所需的树脂粘性。
在300°和350°的高温下,观察到测量的应变显着增加。第 7 层和第 8 层的最大偏差显示不稳定值,类似于之前的发现,这是排除这些结果的另一个证据。
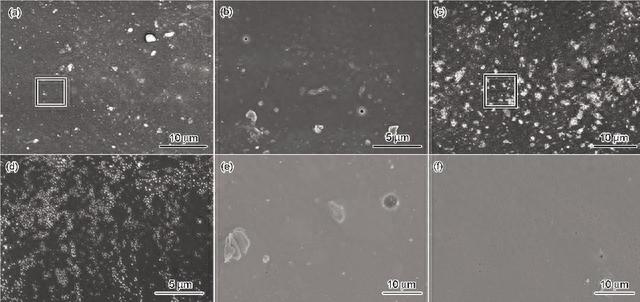
以不同放置温度制造的层压板中产生的应力,当温度与树脂玻璃化转变温度相比变得极高时,固化程度增加,并诱导更多的RS,这表现为在300和350°C下诱导RS与其他较低温度的较大差异。
由于温度升高,树脂经过瞬时固化,样品变得更加坚固。随后,诱导出更多的拉伸RS,从而显着降低材料强度。此外,值得一提的是,在较高温度下,每两层连续层中的RS之间的间隙增加,并在最高温度的最后一层中扩展到40 MPa。
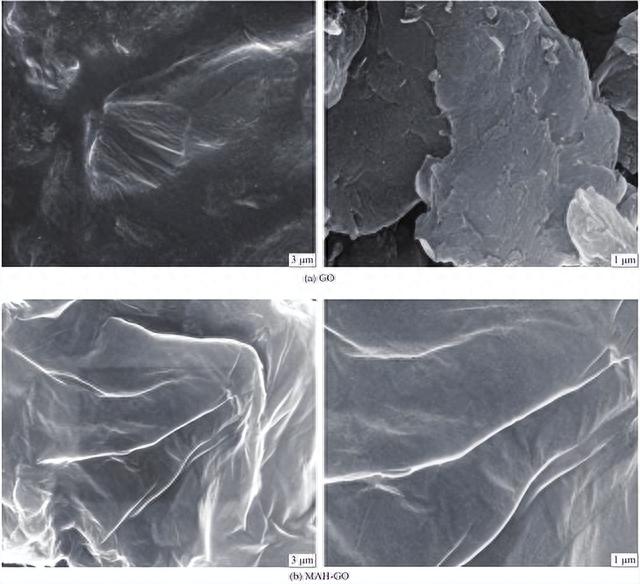
这意味着层温度和热边界条件的差异对RS的影响在较高的放置温度下增加。由于较低的冷却速率和更多的热负荷以及后续层的重复通过,较深的层也显示出更多的应力。
氮气流量实验的当前设置利用氮气作为加热介质,使用热气炬进行材料放置。因此,氮气流速是影响诱导RS的另一个参数,过量的氮气流使受热流影响的区域最大化。因此,除了周围区域的再加热外,由于施加在表面上的过热,将诱导更多的 RS。
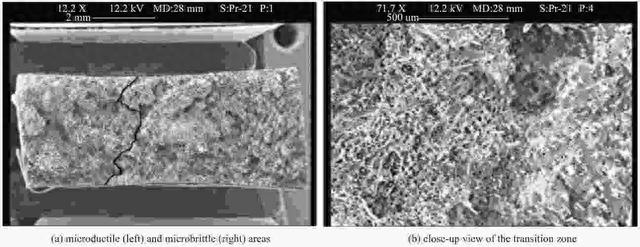
氮气流量由最大容量为25 L/min的流量阀通过贴装头的主控制单元进行控制。通过使用五种不同的阀组来分析氮气流的影响;其满负荷的 60%、70%、80%、90% 和 100%。PLC将流量控制器的读数与用户定义的设定值进行比较,然后通过PID算法调整氮气流量。
流量变化的影响小于温度变化,因为最大差为75MPa。然而,较高的氮气流会触发更多的应变,从而诱导更多的RS,从表面到更深的层逐步增加。
值得一提的是,增加热通量会扩大对铺层的对流,从而导致层的热膨胀差异更大。纤维和基体的热膨胀之间也发生同样的效应。因此,开发了不同的冷却速率,从而触发了更多的RS。这种效应在底层中更加明显,特别是当材料归因于自动化制造过程中原位固化的增加时。
热气割炬位置作为一项综合研究,在当前工作中分析了RFP过程中可能影响RS并且可以控制的每个参数。这包括热气割炬出口(喷嘴)与层压板表面之间的距离,增加这个差距意味着扩大受热流影响的区域。
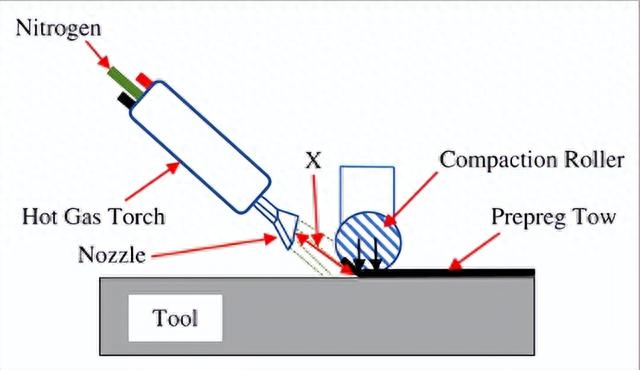
然而,由于到达工件表面需要更多时间,它也可能减少热负荷,并且还增加了与周围空气的接触和对流,从而削弱了热效应。由于割炬运动的可用行程,仅研究了三个不同的位置;15、25 和 35 毫米。
图显示了割炬与复合材料表面不同相对位置的 RS。值得一提的是,距离X对感应RS的影响最小,最低电平和最高电平之间的最大差异为15 MPa。据了解,这种低效主要是因为割炬位置范围小。
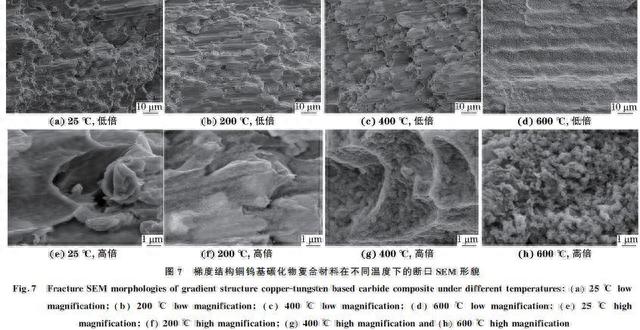
应变测量还显示最后两层的值不一致,在内层中也估计了较高的应力,因为面内收缩远小于复合材料结构的面外收缩。因此,当冷却时,内层内的材料收缩率会受到更大的限制。此外,整个零件在模具中受到限制,这导致在冷却时产生更多的 RS。
通常,在所有情况下,测量RS的最大值不超过与数据一致的材料强度的10%。在大多数实验中,RS的值在过程参数的较低水平上没有明显差异。
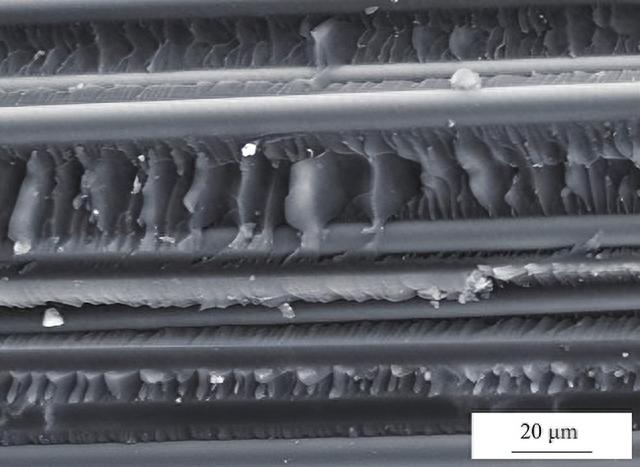
此外,无论最后两层如何,当前的分析都表明,在一定深度后,由量规测量的应变几乎停止变化。重要的是要强调RS是自平衡的,因此,如果我们确定每层中一个方向的应力状态,则应在层压板的整个厚度内进行平衡。但是,当前的工作侧重于每层中获得的最大主 RS。因此,每个应力都有其方向,并且与其他应力不同。
微观结构分析在高放置速度下,样品表现出较高的起伏,层内的空隙和微裂纹增加。在较低的压实力、较低的温度、较低的流速以及割炬喷嘴与工件表面之间的距离较大时,也会出现同样的现象。
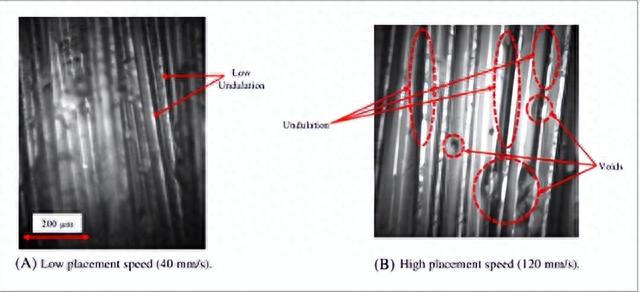
增加压力会挤压树脂并迫使其填充表面之间的间隙和凹槽。此外,注入更多的热气体并提高其温度可能会熔化树脂并使其更柔软,通过压缩,它可以轻松填充层压板内部的空隙并降低层的波纹度。
通常,填充间隙并减少材料的起伏会导致相邻层之间的接触面积增加,从而增加剪切力并限制冷却时层的变形和收缩。值得一提的是,在更高的压实力和较高的温度的情况下,起伏和空隙的减少更为明显,与其他参数相比,这也有助于在这些条件下诱导更多的RS。
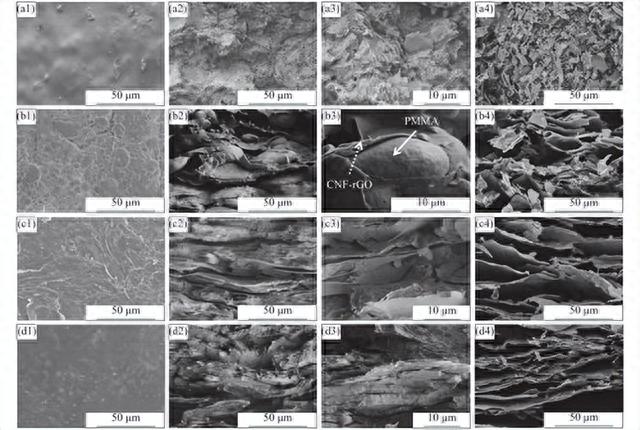
研究结果表明,光纤铺放的参数设置会影响样品的微观结构,从而影响残余应力的大小。具体来说,较低的贴装速度和较高的压实力会增加复合材料中的残余拉应力;提高温度有利于原位固化,但也会由于材料收缩而形成较大的热残余应力。
残余应力主要以拉应力形式存在,最大值出现在纤维方向。在较低的参数设置下,残余应力可以达到复合材料强度的10%,而在较高的参数条件下,残余应力的影响会更加明显。
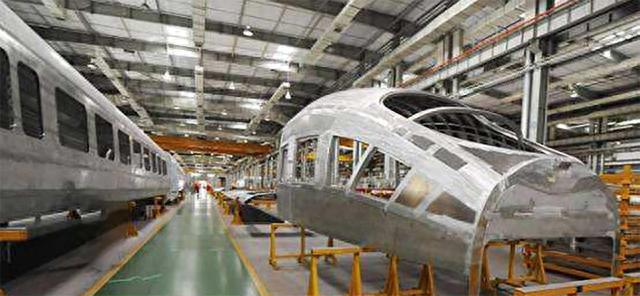
残余应力的存在会降低复合材料的力学性能,增加结构失效的风险,特别是在循环载荷条件下。
因此,进一步减小自动化制造过程中诱导的残余应力,是获得高性能复合材料的关键。未来的研究需采用多轴层压工艺,系统优化光纤铺放的参数,使残余拉应力降到最低。同时,开发更准确、高效的残余应力测试方法,也是实现工艺与材料性能优化的重要手段。
参考文献1M. Elkington, D. Bloom, C. Ward, A. Chatzimichali, K. Potter, Adv. Manuf.: Polym. Compos. Sci. 2015, 1(3), 138.
2T. Z. Sudbury, R. Springfield, V. Kunc, C. Duty, Int. J. Adv. Manuf. Technol. 2016, 90(5), 1659.
3S. Tumkor, N. Turkmen, C. Chassapis, S. Manoochehri, Int. Commun. Heat Mass Transf. 2001, 28(1), 49.