三元材料(简称NCM)作为锂电池的主流阴极材料,由于其能量密度高,在电池领域具有一定的应用优势,一直受到人们的关注。
当材料中的镍含量大于或等于0.6%时,定义为 高镍三元体 阴极材料。近年来,高镍 三元阴极材料 由于它们的高能量密度和高工作电压被广泛研究。
单晶和多晶三元材料的比较根据材料微观形态的不同,三元材料可分为多晶材料和单晶材料。
多晶材料的制备工艺相对成熟、稳定,目前市场占有率较高。次粒子通常是由较小颗粒的聚集形成的,其形状大多是球形的,颗粒的尺寸通常约为10倍,颗粒内部有大量的晶界。多晶高镍三元阴极材料充电放电过程中产生的微裂纹是制约其大规模应用的重要因素之一。
开发单晶三元材料可以更好地解决上述问题。单晶三元阴极材料由直径为2-5M的初级粒子组成。与多晶材料相比,单晶材料内部没有晶界,粒子的机械强度较高,大大降低了各向异性体积变化引起的微裂纹,提高了材料的循环性能。
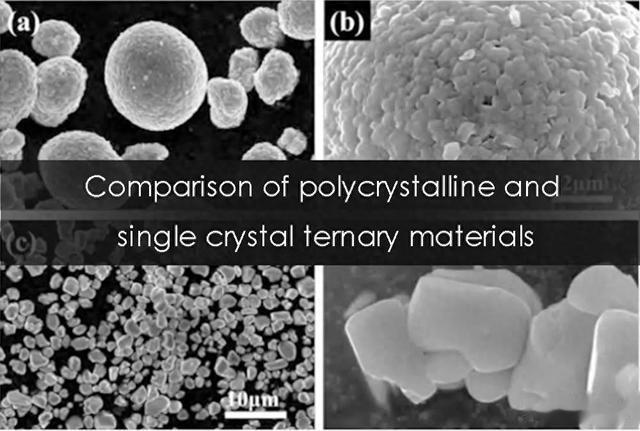
此外,与多晶材料相比,单晶材料在气体生产、压实密度、热稳定性和高温循环性能方面具有显著优势。目前,低镍单晶三元材料的制备已经积累了一定的工艺基础,而高镍单晶三元材料的制备仍面临挑战。
高镍三元阴极材料的合成需要较低的合成温度来维持结构的稳定性,而单晶材料的合成则需要高温和长期的退火过程。两者之间的矛盾使单晶高镍三元阴极材料的工业化面临困难。
单晶高镍三元阴极材料的制备工艺单晶高镍三元阴极材料的常用制备工艺主要有单步高温合成工艺、多步高温合成工艺和熔盐辅助合成工艺。
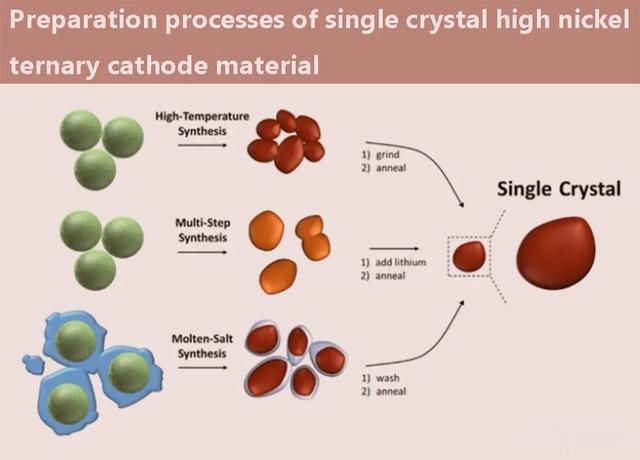
提高烧结温度是制备大型单晶材料的有效方法。较高的温度可以有效地提高离子迁移率,从而促进颗粒的生长。应注意的是,在提高烧结温度的同时,还应增加锂的含量,以抵消高温烧结过程中锂的挥发。
大型单晶颗粒在低温下很难见到,但大型单晶颗粒只有在高锂含量的高温下才能得到。然而,过量的锂会增加材料的残余锂含量,导致电池内气体产量增加。
一般来说,高镍三元阴极材料的烧结温度将明显低于低镍材料。例如,1,1,1,1,1,1,1,2,2,2,2,2,2,2,2,2,2,2,2,2,2,2,2,2,2,2,2,2,2,2,2,2,2,2,2,2,2,2烧结单晶温度分别比烧结多晶材料高80℃和70℃,单晶高镍三元阴极材料烧结温度比低镍材料低。
单晶高镍三元阴极材料在烧结过程中需要高温,这不仅会使初级颗粒生长,而且会使次级颗粒粘在一起,所以烧结后需要研磨和粉碎。
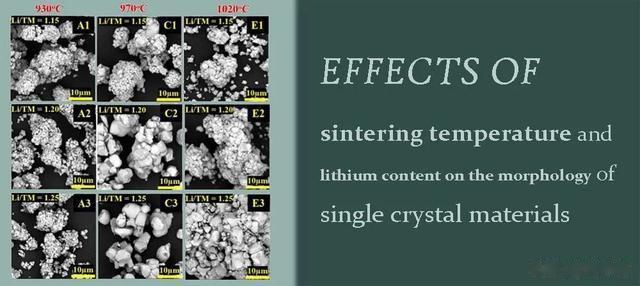
尽管退火处理可以解决单晶材料合成中的一些问题,但研究表明,在NCA材料合成过程中,过高的温度和过高的锂含量会导致L5-a4异相的生成。因此,单步高温合成方法在单晶高镍三元阴极材料的生产和应用中难以应用。
因此,人们开发了一种多步骤的合成方法。在这种方法中,前驱体首先与较低量的锂混合,在低温下烧结多次。最后加入剩余的锂并在高温下烧结。
熔盐辅助合成工艺除了上述高温合成方法,另一种合成单晶高镍三元阴极材料的主要方法是熔盐法。该方法需要在合成过程中加入数倍于前驱体的锂盐。
熔化的锂盐能够有效地促进原子的扩散,从而促进微粒的生长。因此,大颗粒可以在较低的温度下合成,从而有效地降低了阳离子混合和颗粒聚集,但该方法需要在合成后对锂盐进行清洗。
熔盐烧结法的另一个巨大优点是,通过选择熔盐可以调整材料颗粒的形态。同时,过量的锂盐也会对单晶材料的生长过程产生重大影响。越来越多的熔化盐会减少阳离子的混合,从而提高材料的循环稳定性。
单晶高镍三元阴极材料的改性方法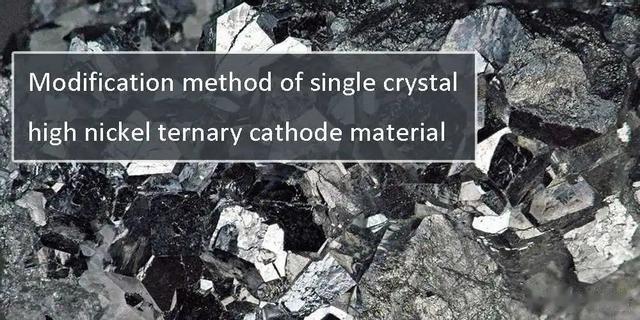
虽然与多晶高镍三元阴极材料相比,单晶高镍三元阴极材料在界面稳定性、气体生成、热稳定性和力学性能方面有显著优势。然而,高镍体系引起的问题不能通过单一结晶完全消除,而且在改进单晶NCM性能方面仍有很大的余地。
因此,需要对单晶NCM进行修改,以进一步拓展其应用前景。对于单晶三元材料的改性,也可以参考其他高镍三元材料的改性方法。主要方法仍然是掺杂和涂层。
结论单晶高镍三元阴极材料同时具有较高的比容和较高的结构稳定性,是一种具有很高研究价值和发展前景的电池阴极材料。目前,单晶高镍三元阴极材料的大规模生产尚未实现,如何获得高性能单晶纳米材料仍是一个迫切需要解决的问题。
现阶段,主要侧重于对其进行涂料和掺杂修饰,以改善其功能的缺陷,如能力的快速衰减和性能差,并取得了一些进展。随着制备工艺的不断深化和电化学机理的探索,单晶高镍三元阴极材料在电化学领域具有广阔的应用前景。 世界上的电力电池公司 在未来。
如何降低锂电池三元材料表面碱性前,用于三元锂电池的三元阴极材料NMC111、NM523和NM622已投入大规模生产。从阴极材料的角度看,镍含量的增加将导致三元材料中的李/镍混合的强化,并缩短循环寿命。
更严重的是,镍含量的增加将导致颗粒之间的残余碱性杂质的大量增加,这反过来又会在充电和放电期间引起严重的气体生产,导致电池膨胀和变形,缩短循环周期和保质期,以及潜在的安全危险。残余碱性杂质已成为制约高镍材料在电动汽车高能量密度电池中应用的关键。
此外,近年来,各种阴离子和阳离子的掺杂或涂覆等方法也被用于稳定三元材料的主体表面结构,达到了改善循环和存储性能的效果。这些方法很难解决高镍材料中高残留碱性杂质的问题。
为此,本文研究了不同烧结温度下的残余碱性杂质及不同烧结温度下的锂/金属比,用高温固态法制备NMC811材料,并验证了各种后处理系统的降碱效果。
实验试验NMC811材料的合成根据设定的化学计量比,分别对NMC811材料前兆氮0.8CO0.1MN0.1(OH)2和LOO进行了混合。在高速搅拌机中,将原料以700R/分钟的速度混合,行驶0.5小时。该混合物被放入刚玉熔炉中,置于羧型大气烧结炉中,在氧气气氛和特定温度下烧结12小时,并在氧气环境中自然冷却到室温,以获得Nc811样品。
在不同的锂比和温度区域选择了三个试验点,表1列出了相应的氮(LI):氮(镍+钴+锰)和每个样品的烧结温度。

表1NMC811样品烧结条件
样品的XRD和扫描电镜分析用粉末X射线衍射仪分析了样品的结构,波长为0.15406NM,管压为40KV,管流为40MA,扫描速度为2(°)/分钟,台阶尺寸为0.02°。用场发射扫描电镜分析了样品的表面形态.
样品中基本杂质残余量的分析和处理以NMC811、NM622、NM523和NM111样品为比较样品,对基本杂质进行了残留分析。特定制造商包括 高镍三元阴极材料公司 作为参考。将5G粉末样品放入95G去离子水溶液中,搅拌5分钟,然后吸入过滤器。用电位滴定仪根据等效点值V1和V2计算溶液中L2CO3和LOO3的含量,并以其中的杂质表示成分。
根据测定样品2中L2CO3和LOO的含量,分别以理论值的20%、50%和80%的上述基本杂质为终点,计算并添加了还原碱物质磷酸二氢铵。在持续搅拌和蒸发至干燥的情况下完全反应后,它们在700℃的氧气环境中进行了5小时的逆燃,以获得2-P-2、2-P-5和2-P8样品。
此外,以1:4的固体-液体质量比为标准,用纯水冲洗制备了比较样品2-水。
阴极板制造和模拟电池组装将nm811样品、聚偏氟乙烯和乙炔黑混合在一起,质量比为92:5:3,把它们磨匀,涂在1.1mm厚的铝箔上。在直径约14毫米的圆形阴极片上打孔,其中含有约10毫克的阴极材料,最后在12小时120℃的真空中干燥。
用锂金属片作负电极,用塞格德2325膜作膜片,用1Mol/L锂6/EC+DMC(质量比1:1)作电解液,将一个Cr2032按钮电池组装在一个含银手套盒中。
电化学性能试验在22℃时,用CT4008电池性能测试系统进行了充电和放电测试。速率性能测试:在3.00~4.30V时,循环在0.10C、0.20C、0.50C、1.00C、2.00C和500C时依次进行,并将比流量与0.01C值进行比较。
自行车性能测试:先充电至4.3伏,电流为1.00C,然后转换为恒压电荷,电流为0.01C;然后放电至3.0V,电流为1.00C。
结果分析烧结材料XRD分析图1是制备的NMC811材料的XRD图案。从图1可以看出,在不同温度和锂比条件下制备的ncm811没有杂质峰,而且每个样品的结构都是OT-NAFO2。(006)/(102)和(108)/(110)晶体平面的分裂度通常可以用来测量分层二维结构的有序度。

在图1中,两组峰(006)/(102)和(108)/(110)分裂得更明显,这表明每个样品具有良好结晶度的分层结构。在高温下制备的样品,峰形更清晰,表明结晶度更高。
残余碱性杂质的比较一般来说,在高温和低锂比烧结条件下,制备的阴极材料中的残余碱性杂质会比低温和高锂比条件下制备的低。高碱性杂质会导致涂层浆在使用期间粘度迅速增加,甚至出现"果冻"现象;
此外,它还会导致一系列的问题,如减少最大压实的杆件和在循环中肿胀。表2列出了制备的NMC811样品和购买的样品的基本杂质含量的比较。
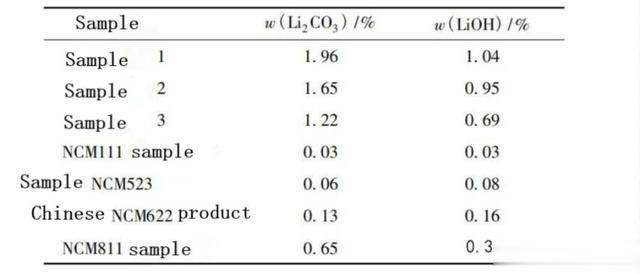
表2制备的NMC811样品与购买样品的基本杂质含量比较
从表2可以看出,虽然对样品3进行了高烧结温度和低锂比的工艺条件的筛选,但制备的NMC811材料中碱性杂质碳酸锂的残留分数仍为1.22%,氢氧化锂的残留分数为0.69%。购买三元材料产品。
随着镍含量的增加,基本杂质的残留量也随之增加,且增加的程度高于线性增长,从商品化的NMC111、NMC523和NMC622材料中基本杂质含量的变化趋势可以看出。
这是由于含有镍的三元材料的固有特性。烧结工艺的优化可以减少基本杂质的残余量,但对于高镍三元材料(如NMC811),必须采用其他方法来减少基本杂质的含量。
碱还原工艺及效果液相环境下的反应是实现碱性杂质分离或转化的直接溶液,其中磷酸盐涂料是一种有效的改性方法。这一思想可以转变为:以NMC811为基质,以磷酸二氢铵为改性物质进行处理,并在700℃下进行二次烧结,试图在NMC811材料表面形成一个稳定的快速离子导体层,以保护材料表面,从而消耗残余的碱性杂质,提高材料的性能。

表3不同碱还原工艺获得的样品碱性杂质含量
从表3可以看出,随着磷酸盐添加量的增加,LIOO和L2CO3的残留量显著降低,表明在处理过程中基本杂质被消耗。与L2Co3相比,李奥的缩减幅度更大,这可能是由于:
①在处理过程中,在处理过程中,李氏转化为L2CO3;在处理过程中,结构中的LI被沉淀,在反燃烧过程中又出现新的碱性杂质;①复杂成分的碱性杂质按反应顺序存在。具体机理需要进一步的实验研究.用纯净水冲洗后制备的样品2-水,材料中的碱性杂质含量显著降低。
碱还原工艺前后样品的XRD分析图2是不同还原工艺前后样品的XRD比较。
从图2可以看出,虽然碱性杂质的含量在处理前后发生了显著的变化,但每个样品的晶体结构并没有改变。结合对表3中数据的分析,原因是添加的磷酸盐消耗了部分基本杂质,在700℃重燃过程中在阴极材料表面形成了磷酸盐掺杂,没有形成新的相。
碱还原前后样品的扫描电镜分析图3显示了样品2和碱还原处理后样品的扫描电镜图像。
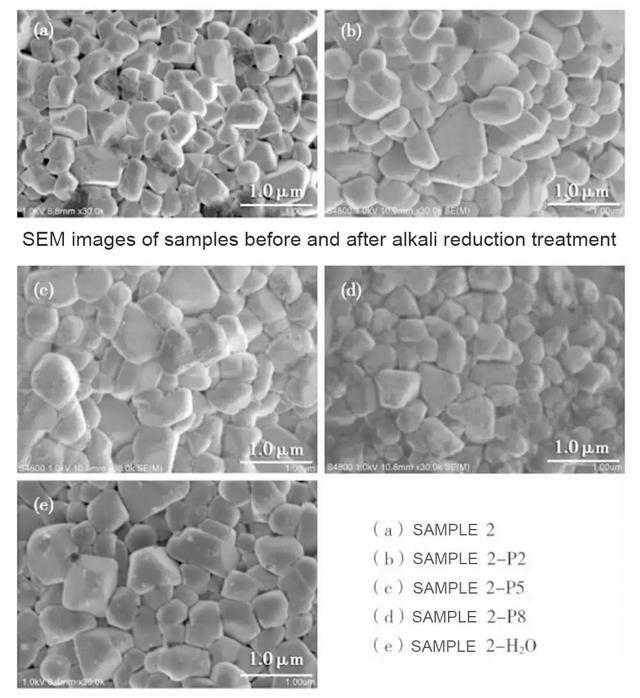
从图3可以看出,样品2表面有明显的暗区域,没有固定的形态,这应该是微粒表面残留的含有锂的弱导电碱性杂质;在处理过的样品2-P-2中,没有观察到明显的暗区域物质。同时,在颗粒表面形成了薄的涂层层.随着磷酸盐添加量的增加,颗粒表面的清晰度逐渐降低,颗粒的边界逐渐模糊。
水洗后的样品2-水具有清洁的颗粒表面、清晰的边界和更大的颗粒间隙。从颗粒形态学的角度来看,两种处理方法都可以实现碱杂质的分离或无害处理。
碱还原前后样品的电化学性质图4显示了样品2和碱还原处理后样品的半细胞速率数据。
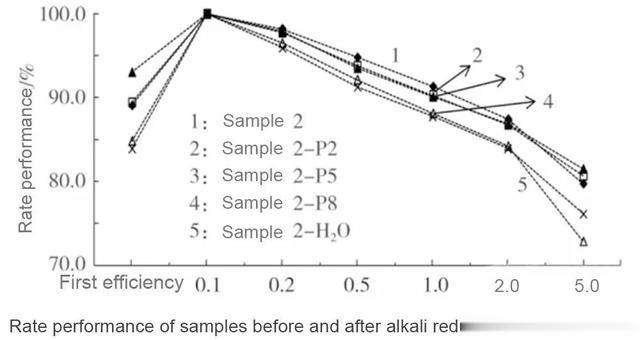
图4加上表3中的数据显示,碱性杂质的残余量越高,半细胞第一周期的库仑效率就越低。水洗后样品的第一电荷释放效率最高,达到93.0%。通过比较不同处理工艺的样品的速率性能,可以看出,样品2-P-2和样品2-水的速率水平相似,略低于样品2。
从图3(b)和(e)中可以看到,2-P-2和2-水样品的主要颗粒表面比未经处理的表面更光滑、更清洁。因此,速度能力的微小下降应该来自于去除颗粒表面上的锂盐,这些锂盐可以作为LI+导体。
随着磷酸盐添加量的增加,样品的速率性能降低。在图3中,样品2-5-5和2-P8在表面和主要颗粒的间隙中富含暗的絮凝物质,这表明在这种情况下添加的磷酸盐含量太高,所形成的物质的电子导电性很弱,这妨碍了阴极材料体相的李氏+导电。
图5显示了样品2和从样品中制备的半细胞在碱还原处理后的循环性能。
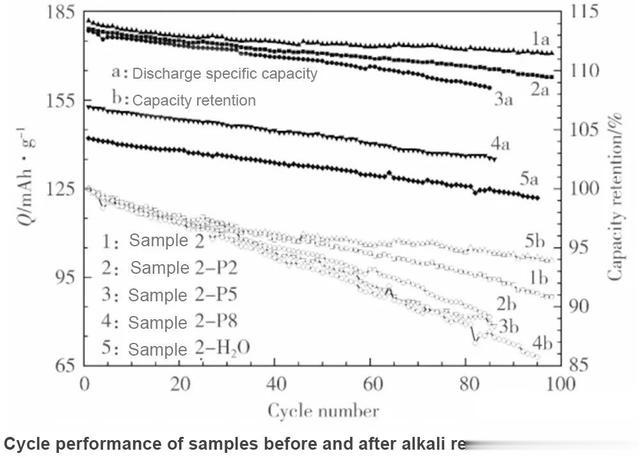
从图5可以看出,用磷酸盐处理过的样品的1C比容比未经处理的样品2明显地低,随着磷酸盐添加量的增加,比容比降低了大约1Mah/克(样品2-P-2)、27Mah/克(样品2-P-5)和37Mah/克(样品2-P8),同时比容保留率也低于样品2。
磷酸盐处理过的样品在表面形成了不提供容量的惰性物种。与未经处理的样品相比,磷酸盐处理样品的循环保留率较低,表明在处理过程中锂原子可能与结构分离。相比之下,用纯净水清洗的样品2-水的比容量首次从179.2Mah/克增加到181.8Mah/克,100次循环后的排放比容仍在171Mah/克左右,比容率达到94.1%。
放电比容的增加可能是由于水洗大大减少了NMC811材料表面的残余电化学惰性碱性杂质,同时去除表面和颗粒之间的杂质,使NMC811材料有足够的活性表面实现主要颗粒和电解质的完全接触。实验结果表明,去除基本杂质有利于提高阴极材料的容量保留率。
结论本文通过高温固态合成的方法制备了高镍三元阴极材料CBM811。该产品具有一种不杂质相结构。在低锂比、高烧结温度的烧结条件下,样品的残余基本杂质含量仍高于NMC523、NMC111等低镍含量三元材料,表明高碱杂质是高镍三元材料的共同特征。
在液相环境下,用不同量的磷酸二氢铵处理并再烧结。结果表明,材料表面的残余碱含量降低,晶体结构没有改变,但颗粒表面仍有电化学惰性物质,导致容量和循环保留率显著降低。结果表明,通过转化来降低剩余碱性杂质是可行的,但需要进一步优化磷酸盐加成和反燃烧温度。
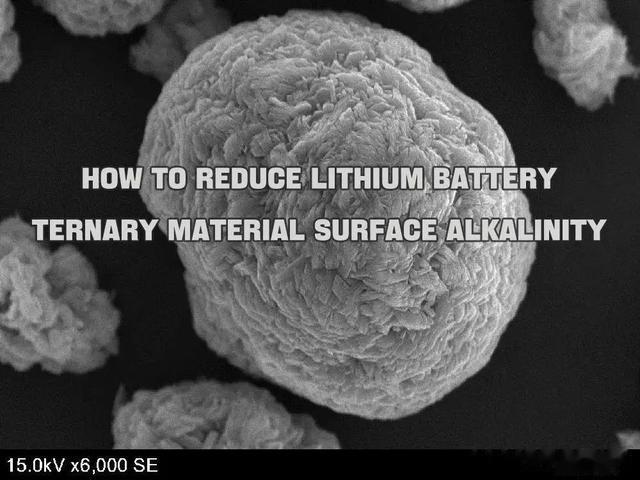
水洗可以大大降低碱性杂质的含量,这比进口产品的含量低。与样本相比,治疗前的比容增加约1.5Mah/g,100周期后的比容保留率也从治疗前的90.8%提高到94.1%。
结果表明,水洗是控制高镍三元材料中碱性杂质含量,提高材料性能的一种方便有效的方法。水洗作为高镍三元材料残碱控制的基本工艺,可以发挥材料本身的性能。
在后续工作中,有必要重点研究如何将水洗相结合,以减少碱和涂层,从而使阴极材料初级颗粒表面的残余碱性杂质直接转化为能够实现LI+导电的涂层层。进一步提高锂资源的利用率,同时提高阴极材料的循环和热稳定性等电化学性能。
硬碳阳极与石墨阳极的优点比较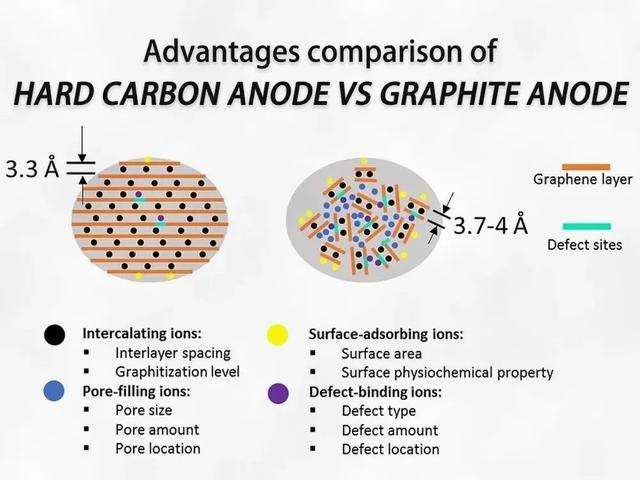
在负极材料的选择上,硬碳负极和石墨负极是两种常用的材料。本文将比较硬碳负极和石墨负极的优点,分析它们在钠电池中的适用性。
硬碳阳极的优点硬碳负极是一种通过高温热解生产的碳材料,因其具有开孔结构、高比表面积和良好的导电性而广泛应用于电池中。与石墨阳极相比,硬碳阳极的主要优点包括以下几点:
更高的比容量
硬碳阳极具有较高的比容量,即单位质量的材料可以储存更多的钠离子。这一特性使得硬碳阳极能够在相同的体积内存储更多的电荷,从而提高电池的能量密度。
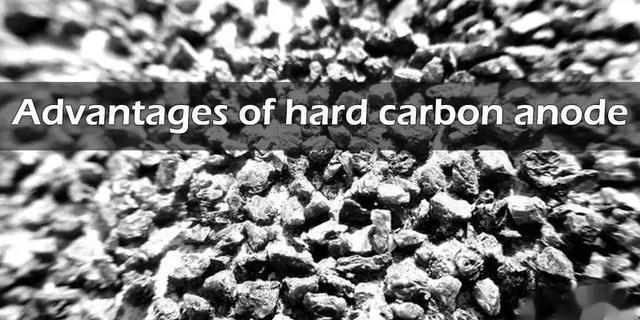
更好的循环稳定性
由于硬碳的开孔结构,可以容纳更多的钠离子,使得充放电过程中电极的膨胀/收缩更加均匀,从而提高硬碳负极的循环稳定性和寿命。
更低的花费
与石墨相比,硬碳负极的生产成本更低,原材料更容易获得,这使得硬碳负极在钠电池生产中成本更低,市场竞争力更强。
石墨阳极的优点石墨是一种天然碳材料,由于其高导电性和高化学稳定性,也广泛应用于电池中。与硬碳阳极相比,石墨阳极的主要优点包括:

更高的比电导率
石墨具有更高的比电导率,可以更快地传输电荷,这意味着石墨阳极可以支持更高的充电速率和更快的充放电响应,从而提高钠电池的输出功率。
更好的身体稳定性
与硬碳负极相比,石墨负极具有更好的物理强度和稳定性,因此不易变形和碎裂,从而提高电池的安全性和使用寿命。
硬碳阳极与石墨阳极——哪一种更适合钠电池?总的来说,硬碳负极和石墨负极都有其独特的优点,因此选择哪种材料作为钠电池的负极需要考虑多种因素。一般来说,如果需要更高的能量密度和更好的循环稳定性,硬碳负极更适合。如果需要更高的输出功率和更好的物理稳定性,石墨阳极更合适。
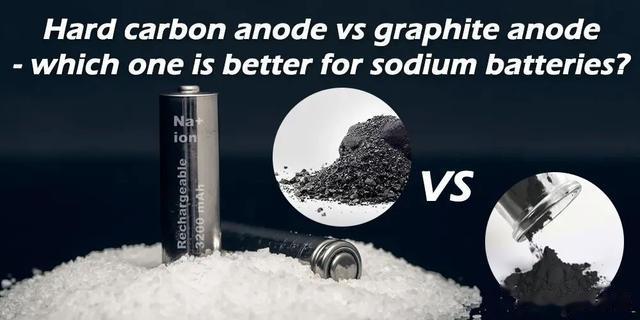
此外,还需要考虑材料成本和可持续性等因素。如前所述,硬碳阳极的生产成本较低,原材料更容易获得,因此在生产过程中更具可持续性。因此,在一些追求低成本和可持续性的应用场景中,硬碳阳极可能更有优势。
需要指出的是,硬碳阳极和石墨阳极的选择并不是非此即彼的关系,而是需要根据具体的应用场景和需求综合考虑。例如,在一些要求较高的应用中,硬碳阳极可以与石墨阳极结合使用,以实现更好的电池性能。
硬碳阳极合成工艺简介与锂离子高尔夫球车电池、锂离子摩托车电池等锂离子电池的合成负极材料石墨不同,硬碳负极的合成需要经过芳构化、缩聚、石墨层形成、石墨层化等过程生长和片材生长堆叠。
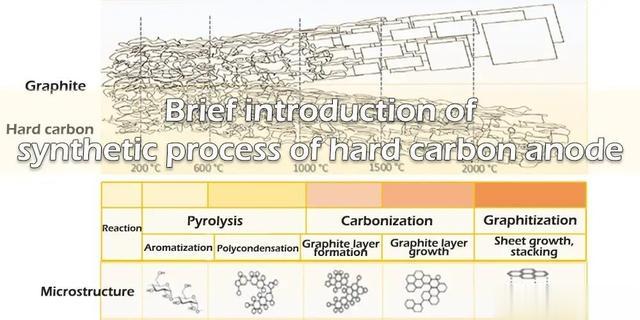
硬碳形成过程
人造石墨主要采用针状焦、石油焦、沥青等化工原料。这些原料在碳化过程中可以在较宽的温度范围内以熔融状态出现,从而使碳层重新排列形成长程有序的片状结构。
用于硬碳阳极的有机前驱体大多具有含有氧、硫、氮等基团的支链结构。碳化过程中,交联形成新的网络结构,不利于碳层的重新排列,因此不可能形成长程有序的石墨片状结构。硬碳阳极使用的前驱体原料主要是生物质、树脂和聚合物前驱体。
硬碳阳极多种工艺路线目前常用的硬碳负极前驱体主要是生物基高分子材料,如毛竹、椰壳、淀粉、核桃壳等,同时还有无烟煤、沥青、酚醛树脂等化工原料也可以使用。
不同前驱体得到的硬碳负极产品性能差异显着,且原材料来源不同,成本结构也显着不同。硬碳阳极工艺多道并行,阳极企业各显其能。
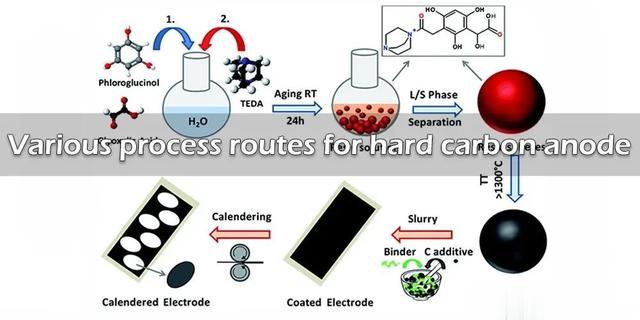
可乐丽使用的硬碳阳极前驱体是椰壳,一种生物质材料。中国传统十大阳极厂商贝特瑞、杉杉、新中和深圳翔丰华科技的硬碳阳极工艺包括生物基材料、树脂基材料和沥青基材料,实现了系统的专利布局。
BEST GRAPHIET作为对标可乐丽的硬碳负极公司,专注于以葡萄糖、淀粉、木质素、椰壳等生物质材料制备硬碳材料。元力采用毛竹、椰壳、稻壳等原料。SQ GROUP 使用稻草。
主流硬碳阳极前驱体的优缺点比较椰壳生物质材料是最早工业化的硬碳阳极前驱体之一。这种材料在自然界中广泛存在,且杂质少,自身强度较高,可以给硬碳阳极产品带来稳定的结构。但目前我国生产硬碳阳极的椰壳原料供应不足,需要依赖进口。
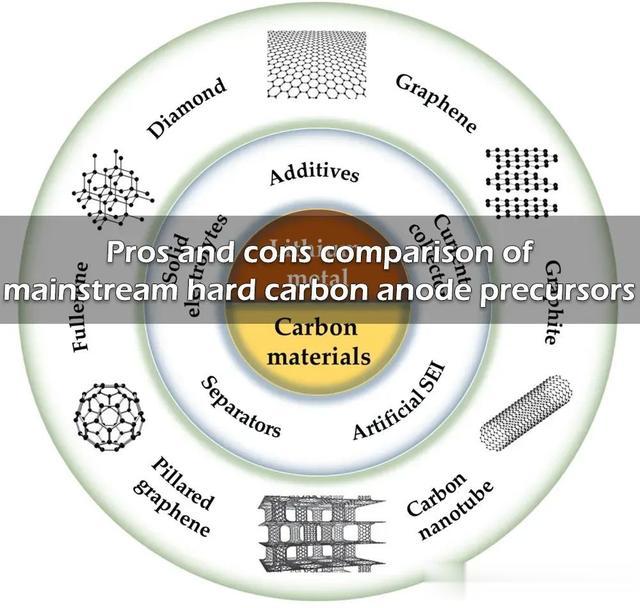
淀粉等多糖类生物质材料作为原料用途广泛、价格低廉、可自然降解。他们在环保方面有优势。目前主要问题是工艺成本高,需要额外添加交联剂或加氢改性等添加剂。
由酚醛树脂前驱体得到的硬碳产品具有更好的均匀性和更高的纯度。产品一般为球形颗粒,且由于原料可控,工艺设计性强,但缺点是成本较高。
沥青基材料来源很广,价格低廉,煤基沥青和油基沥青均可使用。但缺点是沥青中挥发物较多,需要额外进行尾气处理,增加了成本,且目前工艺尚未成熟,产品产能较低。
锂电池导电剂的作用及应用锂电池作为能量密度高、循环寿命长的重要储能器件,近年来发展迅速。就目前商业化的锂离子电池系统而言,限制性能的因素主要来自于电导率。
需要添加合适的电池导电剂来提高材料的电导率,构建稳定持久的导电网络,为电子传输提供快速通道,保证活性材料得到充分利用。因此,与活性材料相比,电池导电剂也是锂离子电池中不可缺少的材料。
电池导电剂是锂电池的关键辅助材料电池导电剂是锂离子电池的关键辅助材料,对于提高电池的导电性、容量、倍率性能、循环性能具有重要作用。由于大多数正极材料活性物质的导电性能较差,内阻较大,因此需要电池导电剂形成导电网络,以提高电极材料活性物质与集流体之间的导电性能。目前电池导电剂主要用在正极片上。
未来,随着硅基负极的加速渗透,电池导电剂在负极片上的应用将会加快。此外,电池导电剂还可以改善极片的加工性能,促进电解液对极片的浸润,有效增加电极材料中锂离子的迁移速率,减少极化,从而提高充电性能和性能。放电效率和电极的使用寿命。
正极:主要提高正极材料的导电性能。锂离子正极材料的导电性较差。需要添加一定比例的电池导电剂,保证导电材料填充正极材料活性物质之间的空隙,形成良好的导电网络,提高正极材料的导电性能。
负极:主要减弱负极材料的膨胀,提高循环寿命。虽然负极材料的导电性良好,但在多次充放电过程中,锂电子的不断嵌入和脱落会引起石墨颗粒体积的膨胀和收缩,导致石墨颗粒之间的间隙变大,电导率降低。
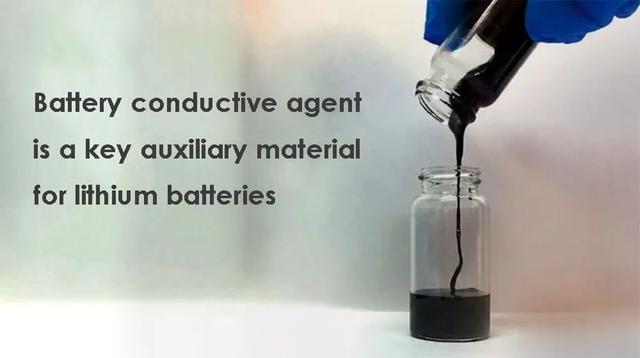
部件甚至可能从电极上脱落,从而降低锂离子电池的容量。添加电池导电剂可以改善负极的表面性能,保持电池的导电性能。
电池导电剂占电池成本约1%,成本敏感度低,下游接受度高。由于电池导电剂在锂电池成本中占比不高,价格敏感性较弱,因此虽然新型电池导电剂的成本高于传统电池导电剂。
然而,新型电池导电剂可以显着提高锂电池的能量密度和快速充电性能。因此,锂电百强厂商的接受度很高,成本可能不是首要考虑的因素。
新型电池导电剂与传统电池导电剂对比多维度综合比较目前锂电池常用的电池导电剂主要有炭黑、导电石墨、VGCF、碳纳米管、石墨烯等。其中炭黑、导电石墨和VGCF属于传统的电池导电剂。碳纳米管和石墨烯是新型电池导电材料。
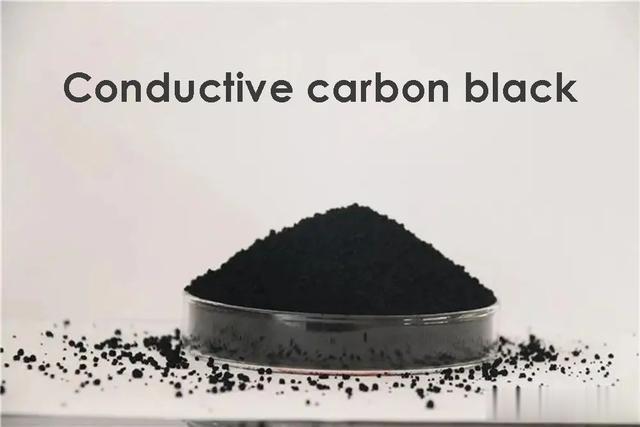
导电炭黑:链状或葡萄状,具有高比表面积。炭黑可以与活性材料形成点对点接触,有利于电解质的吸附,提高离子电导率。添加量约为3%。是一种性价比较高的电池导电剂,但导电性能比较一般,依赖进口。
碳纳米管:可分为单壁管和多壁管。一维碳纳米管呈圆柱形,内部中空,具有良好的电子导电性。纤维结构可以与活性材料进行点对线接触,在电极活性材料中形成连续的导电网络,起到“电线”的作用。碳纳米管电池导电剂有利于提高电池容量、倍率性能、电池循环寿命,降低电池界面阻抗。
石墨烯:具有片状二维结构,与活性物质形成点对面接触,可以最大限度地发挥电池导电剂的作用,减少电池中导电剂的用量。从而提高活性物质的比例,提高锂电池的容量。在少量添加的情况下,石墨烯可以更好地形成导电网络,效果比导电炭黑好得多。
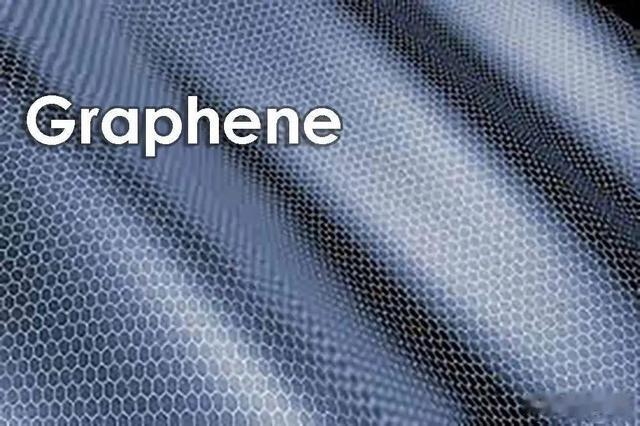
导电石墨:石墨电池的导电剂是人造石墨,其粒径较小,孔隙较发达,比表面积较大,能与活性物质形成点对点接触。有利于提高极片颗粒的压实密度,增加离子和电子的电导率,同时用于阳极时可以增加阴极的容量。
锂电池用炭黑电池导电剂的特点锂电池炭黑电池导电剂产品差异化明显,性能差距较大。低比表面积、高吸油值、低金属离子含量是导电炭黑成功应用的核心技术指标。
粒径和比表面积:炭黑粒径是指炭黑的原生粒径,比表面积是指单位质量或单位体积的炭黑颗粒的表面积之和。粒径小,比表面积大,具有较好的离子和电子传导性,有利于电解质的吸附,提高离子电导率。
支链结构:支链结构可以与活性材料形成链状导电结构,增加导电接触点,有利于提高材料的电子导电率。
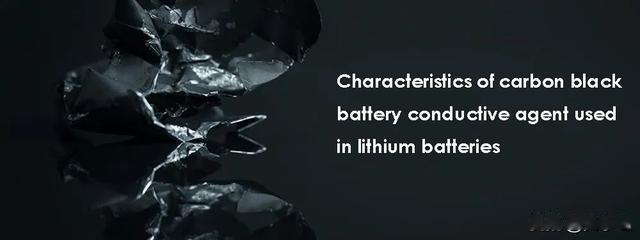
DBP吸收值:炭黑的结构可以通过DBP吸收值来衡量。
表面官能团:表面官能团的多少决定炭黑分散的难易程度。官能团越多越容易分散,但过多会削弱电池导电剂的导电性能。
金属离子含量:金属离子含量过高会引起电池自放电,影响安全性能。一般锂电池用导电炭黑的金属离子含量较高,一般小于10ppm。
目前,我国锂离子电池用电池导电剂仍以传统导电剂导电炭黑为主,其中SP产品为市场主流。SP导电炭黑是一种小颗粒导电炭黑,廉价实用,并且没有储锂功能,仅导电。
电池导电剂的应用及前景每种电池导电剂都有其自身的优点。未来电池导电剂的发展将重点关注以下四个方面:
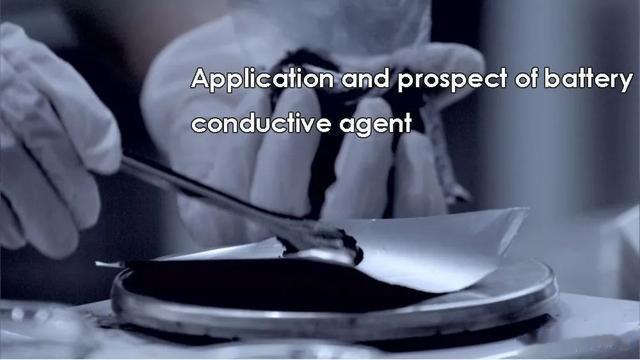
●无论是在水体系中还是在NMP有机体系溶剂中,电池导电剂都应具有良好的分散性;
●与高导电碳纳米管、石墨烯等新型碳材料复合,减少电池导电剂的使用比例,提高电池性能;
●提高比表面积和电解液吸附能力,进一步提高极片的离子电导率。
●无论是碳纳米管还是石墨烯复合材料,与传统材料相比,迫切需要降低成本以满足实际需求。
PVP分散剂在锂电池行业的应用聚乙烯吡咯烷酮(PVP)是N-乙烯基吡咯烷酮(NVP)在一定条件下聚合而成的非离子高分子化合物。PVP可用作锂离子电池电极的分散剂和导电材料的加工助剂。资料显示,在新能源电池领域,1GWh的PVP用量约为15吨,主要使用工业级PVP K30。本文详细阐述了PVP在锂离子电池中如何作为分散剂使用以及PVP在锂离子电池行业的市场需求。
锂电池正极材料用PVP分散剂浆料在锂离子电池生产中非常重要。电池的质量70%与极片的质量有关,极片的质量70%与浆料的质量有关。制作浆料相当于完成了电池的50%,是电池制造的核心工作。锂离子动力电池浆料基本由活性材料、导电剂、粘结剂和溶剂组成。在极片制备工段,材料干燥、溶胶、浆料三个工序直接决定浆料的质量。
锂离子电池正极材料在均质化过程中很难分散均匀,需要添加分散剂。锂电池的正极材料主要有钴酸锂、锰酸锂、磷酸铁锂等,由于其导电率较低,在电池制备过程中,往往需要添加适量的导电剂,如石墨烯、碳纳米管等,提高正极材料的导电率。
但由于磷酸铁锂等超细电池正极材料粒径小、比表面积大,在均质过程中难以分散均匀,导致浆料粘度高或固含量低,这进一步导致涂布困难甚至无法涂布,因此分散剂的选择对于锂离子电池正极浆料的分散尤为重要。
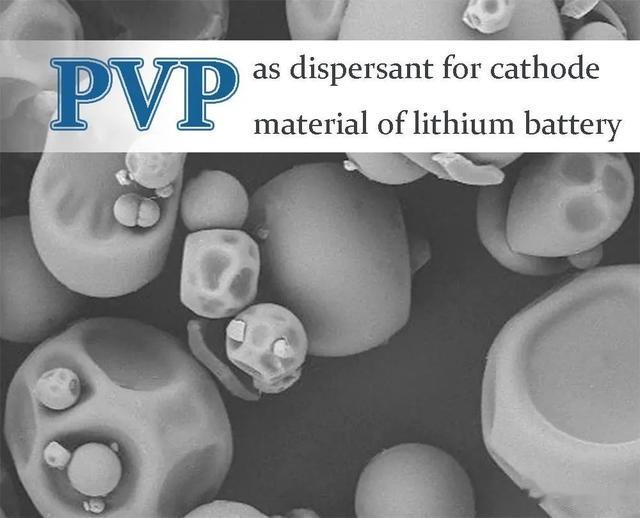
PVP是锂离子电池正极浆料的理想分散剂。PVP分子结构中含有强极性内酰胺亲水基团和CC长链亲油基团,能与多种溶剂良好相容,并可包覆在颗粒表面,通过空间位阻形成良好的分散效果。
在电池正极浆料中添加适量的PVP,可以显着改善浆料的分散性,使浆料由牛顿流体转变为非牛顿流体,浆料粘度稳定在较低水平,有利于降低正极阻抗,提高电池性能。
PVP作为锂离子电池辅助材料加工助剂碳纳米管导电剂可以提高锂离子电池的能量密度。导电浆料是将导电剂均匀分散在溶剂中形成的浆料,而碳纳米管导电剂是将作为导电剂的碳纳米管分散在分散溶剂中形成的浆料。
碳纳米管导电剂作为锂离子电池的新型导电剂,可以提高电池的导电性能,添加量比常规炭黑导电剂减少60%-70%,同时,可以减少粘合剂的用量,可以显着提高锂离子电池的能量密度。
PVP可以显着改善碳纳米管在水、有机溶剂等基体中的分散性能。碳纳米管重量轻,以六角形结构完美连接,并具有许多不寻常的机械、电气和化学特性。由于管间强大的范德华力,碳纳米管形成束或相互缠绕,导致团聚,严重限制了其机械、热学和电学应用。
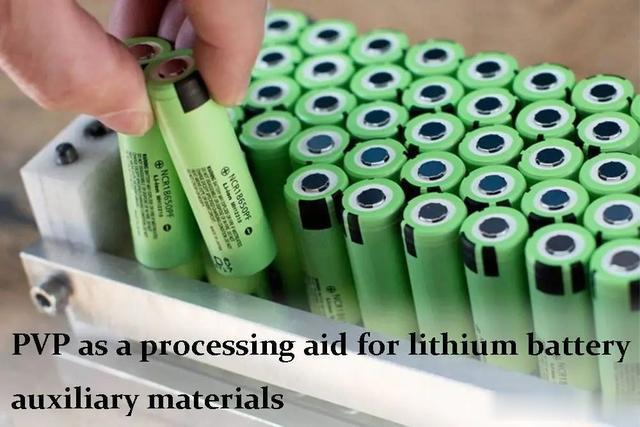
PVP是一种具有特殊结构的两亲性聚合物,吡咯烷酮基团为亲水基团,主链为C−C键合的疏水链段,具有亲油性,因此能溶于水或醇、羧基等有机溶剂。酸和胺烷烃。将具有两亲结构的聚合物PVP引入到CNT表面可以显着改善CNT在水、有机溶剂和其他基体中的分散性能。
中等分子量的PVP K25和PVP K30对多壁碳纳米管的分散效果最好,且浆料粘度较低。呈现出近牛顿流体的特性,多壁碳纳米管颗粒分散均匀,平均粒径较小,具有良好的稳定性。
同时其电阻率也较低,吸附容量高于低分子量PVP K17和高分子量PVP K90,对多壁碳表面具有更好的位阻改性效果碳纳米管,使得多壁碳纳米管几乎分散在单根中,缠结现象显着减少。
锂电池行业PVP分散剂需求分析1、碳纳米管导电剂用PVP分散剂年需求量快速增长
2025年,全球碳纳米管导电剂用PVP分散剂需求量将达到7375吨。据分析,每吨碳纳米管导电剂需添加12.5kg PVP作为分散剂,如果全部使用PVP,2022年全球碳纳米管导电剂用PVP分散剂需求量将达到1975吨,2020年将达到7375吨。2025 年。
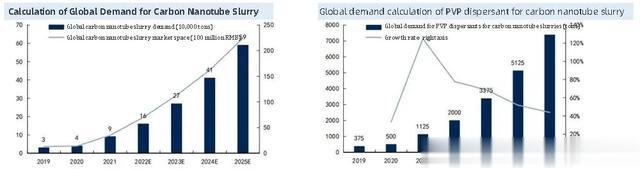
2、未来锂电池用PVP年需求量预计将达到3万吨
全球锂离子电池整体出货量快速增长。数据显示,2021年全球锂离子电池整体出货量为562.4GWh,同比大幅增长91%。从结构上看,全球汽车动力电池出货量为371GWh,同比增长134.7%;储能电池出货量66.3GWh,同比增长132.6%;3C小电池出货量为125.1GWh,同比增长16.1%。相关企业可参考锂电百强。
2025年,全球锂电池用PVP年需求量预计将达到3.31万吨。预计2025年全球动力电池出货量将达到1550GWh,储能电池出货量将达到476GWh。基于新型消费电子市场的高增速以及传统3C消费电子单位产能的提升,假设全球消费电子锂离子电池出货量年均复合增长率为10%,出货量将达到2025年183.2GWh。如果您对消费类电池感兴趣,这里有相关3C消费类锂电池厂家供参考。
根据上述分析,假设锂离子电池领域PVP用量为1GWh约15吨,则2022年锂电池PVP年需求量将达到1.16万吨,2025年将达到3.31万吨。
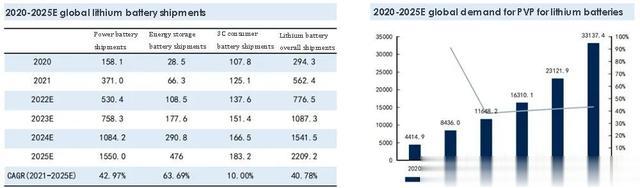
电解质有机溶剂 锂离子电池电解质是锂离子电池电解质的重要组成部分,对锂盐的溶解度、电解质的电导率、电池的循环效率、可逆容量和安全性都有重要影响。优化有机电解质的组成,提高有机电解质的导电性,降低极化度是提高电池性能的重要途径之一。
电解质有机溶剂的介电常数直接影响锂盐的溶解和分解过程。介电常数越大,就越容易溶解和分解锂盐。电解质有机溶剂的粘度对离子的移动速度有重要影响,其粘度越小,离子的移动速度越快。
因此,锂离子电池的电解质倾向于选择高介电常数、低粘度的电解质有机溶剂。在实际情况下,具有较高介电常数的电解质有机溶剂的粘度必须相对较大,低粘度的电解质有机溶剂的介电常数也必须较小。
在实际应用中,它通常与介质常数大的电解质有机溶剂和低粘度的电解质有机溶剂混合,使介质常数相对较大,而粘度较小的混合溶剂被用作锂离子电池的电解质。因此,通过优化电解质有机溶剂的组成,电解质可以获得最高的电导率。
作为最好的锂离子电池电解质溶剂,应尽可能满足以下要求:
*熔点低、沸点高、蒸汽压低,工作温度范围宽;
*高介电常数和低粘度,导致高电导率;
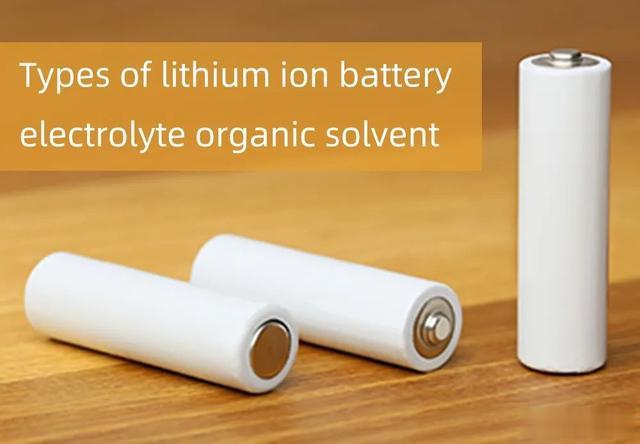
碳酸盐是锂电池工业中使用最早的电解质有机溶剂,在锂电池工业中具有不可替代的地位。锂电池中常用碳酸盐溶剂可分为两种类型:循环碳酸盐和线性碳酸盐。
环碳酸酯、碳酸乙烯和碳酸丙烯是锂离子电池电解质中最重要的两种循环碳酸电解质。PC是一种无色、透明、在常温和常压下略有芳香的液体,闪点为128℃,火点为133℃。PC的熔点较低(-49℃),含有它的电解质即使在低温下也仍然具有较高的电导率。
在基于PC的电解质中,锂离子插入石墨的过程伴随着PC的共插入现象。添加剂或共溶剂常被加入到石墨电极表面形成稳定的SEI薄膜,从而抑制PC共混物对电极的破坏。人们普遍认为碳酸丙乙烯能有效地抑制碳酸乙烯的低温结晶,并能有效地提高锂离子的低温性能。
电池的高温和低温性能试验结果表明,在70℃的高温和-10℃的低温下,含有PC的电池的放电能力要比没有PC元件电解质的电池高得多。EC的结构与PC非常相似,有一个比PC少的甲基基团,这是PC的同系物。
EC是室温无色晶体,闪点为160℃,热安全性高于PC,粘度略低于PC,介质常数高于PC,甚至高于水。它可以完全溶解或电离锂盐,这是非常有利于提高电解质的导电性。
EC的热稳定性相对较高,加热到200℃时只有少量的分解,但在碱性条件下容易分解,可与甲醇进行酯化反应生成碳酸二酯或乙二醇。EC的混溶性高于PC的混溶性,且可与水混溶。

第二种是线性碳酸盐。常用的线性碳酸盐包括碳酸二甲基、碳酸二乙酯、碳酸乙酯和碳酸丙酯。线性碳酸盐通常具有低粘度和低介电常数,不能单独作为锂离子电池电解质的好溶剂,必须与循环碳酸盐联合使用。DMC是室温无色液体,闪光点为18℃。它是一种无毒或轻微毒性的产品,可以形成含水或酒精的共沸物。
DMC具有独特的分子结构,其分子结构含有羧基、甲基和甲氧基等官能团,因此具有多种反应性。其结构与DMC相似,在室温下为无色液体,闪点为33℃,略高于DMC,但毒性高于DMC。DEC溶于酮、醇、醚、酯类等。,但几乎不溶于水,有一种类似乙醚的气味。
EMC和MPC是不对称的线性碳酸盐,其熔点、沸点和闪点接近DMC和DEC。但其热稳定性较差,在碱性条件下易于加热或通过酯化生成DMC和DEC。与循环碳酸盐相比,线性碳酸盐的熔点低,粘度低,介电常数低,且与EC在任意比例下均可混溶。
由EC和DMC混合溶剂制备的电解质在弥补另一种溶剂的缺点的同时,又具有良好的电化学稳定性。目前,商用锂离子电池的电解质溶剂是由EC和一两种直线碳酸盐混合而成的。

其中最重要的循环羧酸酯溶剂是Y-丁基内酯,它已被用于初级锂电池,液体温度范围相对较宽,形成的电解质电导率与EC+PC电解质电导率相似,也可形成碳酸盐等钝化膜。
但在水环境下,BL易分解,毒性高,循环效率比碳酸盐电解质有机溶剂低得多,很少用于锂离子电池。
线性羧酸酯主要包括甲酸甲酯、醋酸甲酯、丁酸甲酯和丙酸乙酯。这些酯的冰点比碳酸盐的冰点平均低20-30℃,粘度也较低,因此可以提高电解质的低温性能。
电解质有机溶剂醚电解质有机溶剂分为循环醚、链醚、冠醚及其衍生物。环醚主要包括四氢呋喃、2-甲基四氢呋喃、1,3-二氧烷和4-甲基1,3-二氧烷等。
链醚主要包括二甲氧基甲烷(DMM)、1,2-二甲氧基甲烷(DME)、1,2-二甲氧基丙烷(DMP)和二苯氧基甲烷(DH)。冠醚和隐酯可以形成与锂离子的铜化型集成,大大提高了锂盐的溶解性,实现了阴离子和阳离子对的有效分离,锂离子和溶剂分子的分离。
这不仅可以提高电解质的导电性,而且可以减少充电过程中溶剂共插和分解的可能性,而且昂贵的有毒冠醚化合物限制了它们的应用。
新型电解质有机溶剂为了提高锂离子电池的整体性能,人们开始开发新型电解质有机溶剂。目前,新型溶剂的研究工作主要集中在两个方面:非易燃电解质有机溶剂和阻燃电解质有机溶剂。通过将卤素原子引入常用电解质有机溶剂分子,可以降低电解质有机溶剂的易燃性,甚至完全易燃。
用卤素原子代替PC分子中甲基的氢原子,使其具有很好的物理和化学稳定性,而且具有很高的介电常数,不易燃烧,可用作锂离子电池中的非易燃溶剂。
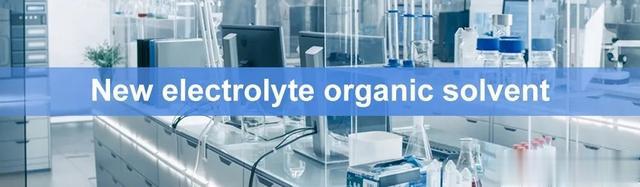
阻燃剂不仅不会自燃,而且可以通过气相阻燃机理和浓缩型阻燃机理防止其他常规电解质有机溶剂的燃烧。例如,磷酸三甲基(TMP)本身就是一种优良的阻燃剂,将其作为锂离子电池的电解质有机溶剂,无疑可以显著提高电池的安全性。
TMP具有良好的氧化稳定性,但还原稳定性较差,在石墨电极上,当负电位为1.2V时,TMP不受限制地减小并大量分解产生甲烷、C2H4等气体产物。添加诸如EC和PC等共溶物可以抑制其还原和分解。然而,随着共溶剂含量的增加,电解质的非易燃性降低。