在芯层发泡型材的生产过程中,一个令人头疼的问题常常出现 —— 共挤出层与发泡层发生分离。这不仅影响产品外观,更严重威胁到产品质量与性能。今天,咱们就来深挖一下,究竟是什么导致了这种 “脱层” 现象,又该如何巧妙化解。
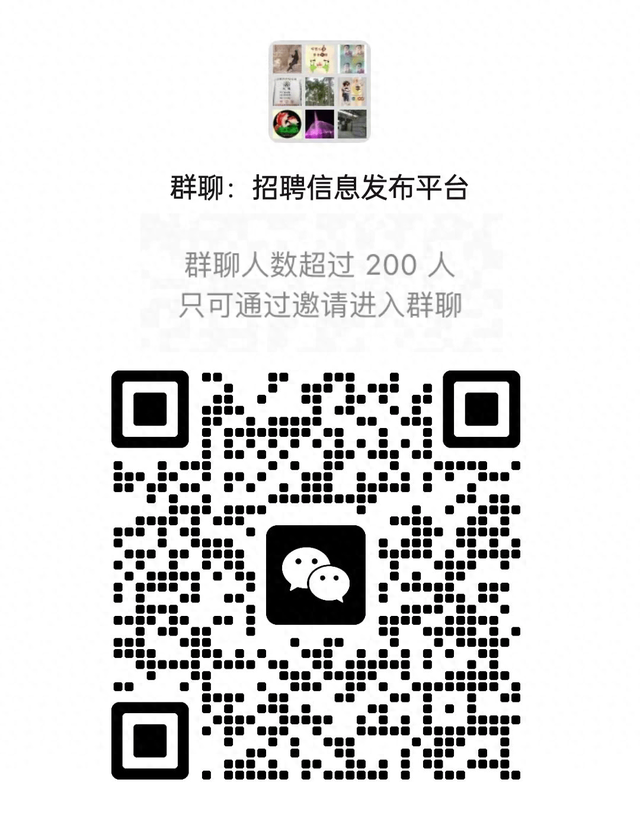
(欢迎更多行业朋友加入我们~添加请备注信息)
从工艺角度来看,多个因素可能成为这场 “分离危机” 的导火索。首当其冲的是共挤出层原料选择不当。共挤出层原料与芯部发泡物料就像一对 “搭档”,若二者相熔性不佳,熔体熔接强度差,就如同搭档间缺乏默契,共挤出层与发泡层便极易 “分道扬镳”,严重时甚至用手轻轻一撕就能轻易剥离。这就好比两种性格迥异的物质,难以真正融合在一起。
其次,共挤出口模汇流段过短也是一大 “元凶”。当汇流段太短,汇流点靠后,发泡物料已完成发泡并开始表面冷却收缩,此时共挤料的熔体压力却突然下降,这就像拔河比赛,一方突然松懈,导致共挤料与发泡料的复合强度大打折扣,进而引发分离。想象一下,原本紧密相连的两个部分,因为这样的 “压力突变” 而产生间隙,最终走向分离。
冷却系统设计与原料冷却机理不匹配同样不可小觑。尤其是当表面共挤料与芯部发泡料收缩率差异显著,特别是表面共挤原料选用结晶性聚合物时,如果冷却系统入口温度过低,共挤出层物料迅速达到结晶点,而芯部发泡料还未开始冷却,这种 “冷热不均” 就如同在两者之间硬生生地插入了一道 “裂缝”,导致共挤出层与发泡层出现分离缺陷。
另外,共挤出层与发泡层的大泡缺陷也会引发分离。大泡的存在破坏了两层之间的紧密结合,就像在原本平整的界面上制造了 “空洞”,削弱了它们之间的连接力。
面对这些问题,我们该如何 “对症下药” 呢?针对共挤出层原料选择不当,我们可以改变共挤出层原料或调整共挤材料的配方,就像为这对 “搭档” 找到更合适的相处模式,增加其与芯部发泡原料的相熔性,让它们能更好地融合在一起。
对于共挤出口模汇流段过短的情况,增加共挤物料与发泡物料的汇流长度,适当提前汇流,就像让拔河双方提前做好准备,增强彼此的协作,从而提升复合强度,避免分离。
而针对冷却温度控制不合理,我们要调整冷却水温度,确保冷却速度与材料特性相匹配,就像给两种材料找到最适合它们的 “冷却节奏”,避免因 “冷热不均” 而产生分离。
在芯层发泡型材的生产中,共挤出层与发泡层的分离问题虽棘手,但只要我们找准原因,精准施策,就能有效解决,确保产品质量稳定,让生产过程顺利进行。希望今天的分享能为各位在生产一线的朋友们提供帮助,让我们共同攻克这些难题,提升产品品质!