
在工业 4.0 浪潮中,中国制造业正经历着前所未有的数字化转型阵痛。工信部最新数据显示,我国规模以上工业企业数字化设备联网率已达 47.5%,但产能利用率却长期徘徊在 75% 左右。这种看似矛盾的现状揭示了智能工厂建设中一个关键痛点:孤立的信息系统正在制造新的数字鸿沟。当设备管理系统(EAM)与制造执行系统(MES)各自为政时,智能工厂就陷入了 "看得见的设备,看不见的流程" 的困局。
1.1 生产瓶颈的数字化溯源
某汽车零部件企业的案例极具代表性:其 EAM 系统记录的设备完好率高达 92%,但 MES 系统却显示实际产能仅达理论值的 68%。深入分析发现,设备维修记录与生产排程数据完全割裂,导致预防性维护计划与生产计划频繁冲突。这种信息断层造成的隐性损失,每年吞噬企业近 15% 的利润。
在电子制造车间,EAM 采集的设备振动数据与 MES 记录的产品良率看似毫无关联。但当工程师将两者时间轴对齐后,发现特定频率的设备异常会导致后续 3 小时生产的产品不良率陡增 12%。这种跨系统数据价值的流失,正是传统工厂数字化转型的最大黑洞。
某食品加工厂的实践表明:当包装设备故障信息在 EAM 系统停留 2 小时后才传递到 MES 系统,造成的连锁反应包括:7 条产线被迫调整、3 批次原料过期报废、2 笔紧急订单违约。这种系统间协同的延迟,正在指数级放大生产风险。

2.1 数字孪生:打破虚实界限的融合基座
基于工业物联网的融合架构正在重构系统边界。某工程机械龙头企业构建的 EAM-MES 联合数字孪生体,实现了设备状态与生产流程的毫秒级映射。通过将 EAM 的设备健康指数(PHM)与 MES 的工序节拍(Takt Time)动态耦合,成功将设备综合效率(OEE)提升 19%。
2.2 智能算法的协同进化
深度学习算法正在突破传统系统的功能边界。某光伏企业的实践显示:将 EAM 的设备预测性维护模型与 MES 的生产排程优化算法进行联合训练后,非计划停机时间减少 40%,同时设备利用率提高 22%。这种算法层面的深度交融,正在创造 1+1>3 的价值裂变。
2.3 区块链构建的信任链条
在制药行业,基于区块链的 EAM-MES 融合系统实现了全生命周期数据可信追溯。从设备维护记录到生产批次数据的不可篡改存证,使质量追溯时间从 72 小时压缩至 15 分钟,同时降低合规审计成本 60% 以上。
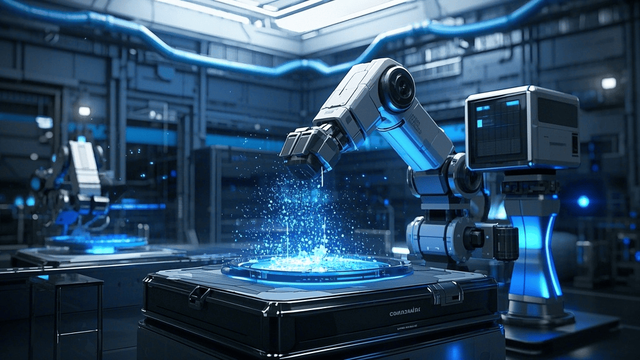
3.1 流程再造型融合(某白色家电集团案例)
通过重构价值流将设备维护窗口嵌入生产节拍:在 MES 排程中动态插入预防性维护时段,同时根据 EAM 预测调整生产批次。实施后设备可用率提升至 98.7%,换型时间缩短 33%。
3.2 数据驱动型融合(某半导体代工厂方案)
建立跨系统的数据湖架构,通过特征工程提取设备振动频谱与晶圆良率的关联规则。基于实时数据流构建的预警模型,使缺陷检测前移三个工序段,每年避免损失超 2 亿元。
3.3 组织变革型融合(某新能源电池企业实践)
打破传统设备部与生产部的职能壁垒,建立由 EAM 和 MES 数据共同驱动的联合决策中心。通过 KPI 体系的重新设计,将设备生命周期成本与生产运营效率纳入统一考核,推动跨部门协同效率提升 40%。
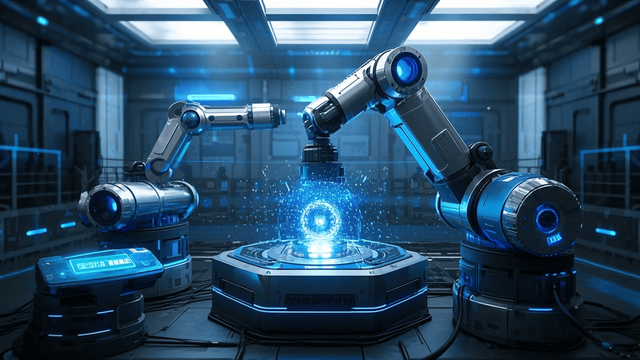
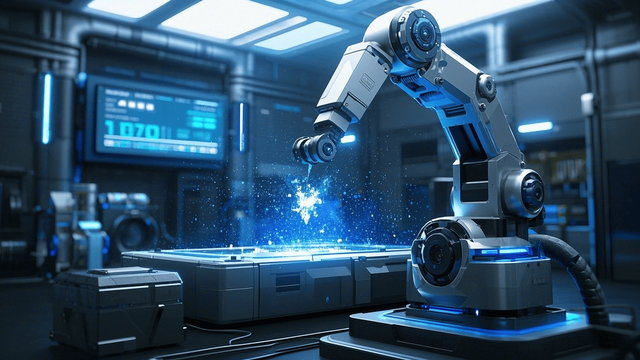
当 5G+MEC 边缘计算遇上工业元宇宙,EAM 与 MES 的融合正在进入新维度。某航天制造企业打造的 "维护 - 生产" 共生系统,通过 AR 眼镜实现设备状态可视化与生产指导的实时叠加,使复杂装配作业效率提升 3 倍。这种虚实交融的实践,预示着工业系统将从工具理性走向生态智慧。
站在智能制造的新起点,EAM 与 MES 的深度融合已不是选择题,而是生存题。那些率先打破系统边界、构建数字协同生态的企业,正在智能制造竞赛中赢得关键赛点。当设备心跳与生产脉搏真正同频共振时,智能工厂将突破物理世界的局限,奏响工业进化的新乐章。

在智能制造的浪潮中,EAM 与 MES 的深度融合不仅是技术命题,更是管理命题。通过数字孪生重构系统边界,借助智能算法突破功能局限,依托区块链建立信任机制,企业正在探索出一条从数据孤岛到价值共生的转型路径。这场融合革命不仅关乎效率提升,更将催生全新的工业生态 —— 当设备健康与生产节拍实现动态平衡,当维护决策与排程优化形成智能闭环,中国制造业的智能工厂将真正驶入 "双引擎" 驱动的快车道。