在铝合金中加入陶瓷颗粒可提高铝合金的承载能力,从而提高干滑动磨损轻微的载荷和滑动速度范围。许多研究人员对此进行了详细研究,为铝基金属基复合材料(Al-MMC)在滑动阻力方面的应用提供了新的机遇。一些研究还分析了Al-MMC在外部加热(温度范围高达200C◦或500C◦)情况下的磨损行为。
研究发现,由于复合材料的热软化,磨损会随着温度的升高而加剧,并在临界温度下变得严重。摩擦系数也明显增大,这归因于粘附力的增加。大多数实验研究都是以硬钢为基准面进行的。对Al-MMC与摩擦材料的摩擦和磨损行为的研究受到特别关注,因为这些材料可用于汽车盘式制动器。与传统的铸铁相比,Al-MMCs盘具有密度低、热导率高等优点。
通过研究了两种Al-MMC与有机和半金属摩擦材料的摩擦和磨损情况。结果发现,与有机摩擦材料的磨损率较低,原因是形成了富含石墨的转移层,而与半金属摩擦材料的磨损率较高,原因是摩擦材料中的金属碎片或纤维产生了磨蚀作用。
正如最近的研究所示,了解摩擦接触的性质对于解释盘/垫联轴器中观察到的摩擦和磨损行为非常重要。在实际制动系统中,标称接触压力p0通常在0.3至2兆帕之间,滑动速度v在1至大于10米/秒之间。
因此,p0v值通常在0.3至20MPam/s之间。有关制动应用材料的摩擦和磨损行为的大多数实验室研究都是通过盘上销和盘上块磨损钻机进行的,在大多数情况下采用的p0v值低于10MPam/s。
在先前的研究中,优化了负载递增程序下的挡圈磨损试验,以研究Al-MMC与铸铁和摩擦材料的摩擦和磨损行为。p0v值高达8.5MPam/s,足以说明所研究材料的性能。
在本次研究中,采用了增加载荷的方法来研究载荷和温度对两种Al-MMC与一种商用摩擦材料的摩擦和磨损行为的影响。通过外部加热来提高接触温度,从而评估温度对所研究材料摩擦学行为的影响。在实践中,温度峰值很常见,因此了解系统对这种峰值的反应非常重要,特别是在摩擦系数方面。
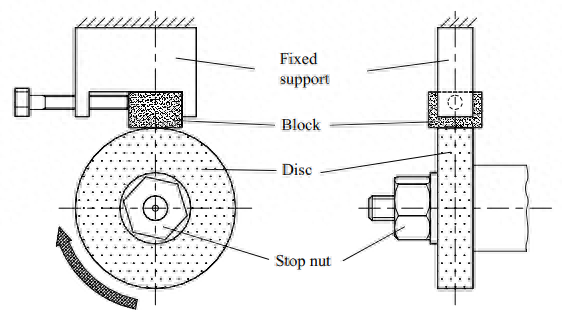
干式滑动测试采用块对盘结构进行,如图所示。圆盘由Al-MMC制成,滑块由摩擦材料制成。圆盘直径为45毫米,厚度(即接触长度)为10毫米。它们是从美国Duralcan公司提供的棒材上切割下来的。铝合金的名义成分如下::Al-8.5-9.5%Si-0.45-0.65%Mg-0.2%Fe(最大值)-0.2%Cu(最大值)-0.2%Ti(最大值),强化颗粒为平均直径为8微米的碳化硅颗粒。测试了两种材料。
第一种是SiC10,含有10Vol%的增强材料,其密度为2.71g/cm3。第二种是SiC20,含有20Vol.%的强化剂,密度为2.77g/cm3。Al-MMC经过T6热处理后,硬度达到,分别为68HV30和81HV30。
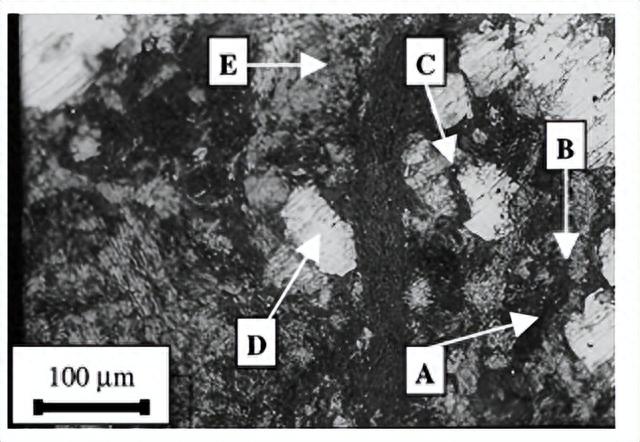
摩擦块是从商用刹车片上切割下来的,尺寸为15毫米×15毫米×10毫米。使用的摩擦材料为半金属。如图所示,可以看出以下成分:(A)石墨;(B)硅酸镁;(C)硅酸锆;(D)钢粉;(E)黄铜粉。粘合剂由苯酚甲醛树脂制成,还含有其他电荷,如玻璃纤维和CaCO3颗粒,但在图中没有标出。
干式滑动试验的滑动速度为0.94米/秒。在环境温度下进行了从100牛顿到750牛顿的七级增载试验。给定载荷下的每个试验周期为30分钟,每次试验前后都对试样进行称重,以测量磨损情况。
在每个测试期间,摩擦系数被持续测量,接触温度的变化也被记录下来。为此,在距离表面4毫米和10毫米处的摩擦材料块中插入了两个热电偶,并通过考虑线性热梯度来估算接触温度。
高温试验是在500、650和800N三个载荷水平下进行的。加热是通过两个热阻进行的,热功率的设定目的是在相同的摩擦学条件下,在没有外部加热的情况下,获得比测量值高110◦C的接触温度。
为了获得磨损机制的运行信息和转移层的特征,对磨损的碎片和轨迹进行了分析。用扫描电子显微镜(SEM)观察了磨损的碎片。磨损表面通过光学显微镜和扫描电子显微镜进行观察。此外,为了进一步了解转移层和表面下损伤的情况,还对平行于滑动方向的横截面进行了分析。
经过短暂的磨合阶段后,摩擦系数逐渐增大,在所有情况下,经过5-7分钟的测试后,摩擦系数达到稳态值。
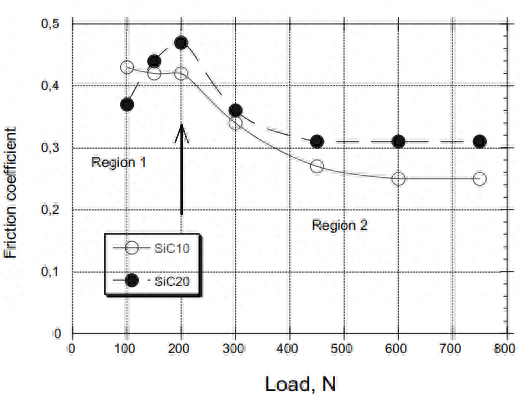
稳态摩擦系数与外加载荷的关系如图所示。磨损机理的连续分析证实,可以确定两个区域。在区域1中,当载荷低于200N时,两种材料的摩擦系数都很高。对于SiC10来说,摩擦系数是恒定的,而对于SiC20来说,摩擦系数会随着载荷的增加而增大。
在区域2,即载荷高于200N时,两种联轴器的摩擦系数都会随载荷的增加而减小,直至约500N,然后趋于稳定。在这一区域,SiC20的摩擦系数在每个施加载荷下都高于SiC10的摩擦系数。第2区的摩擦趋势是这类摩擦学的典型特征。其他研究也观察到了这一现象。
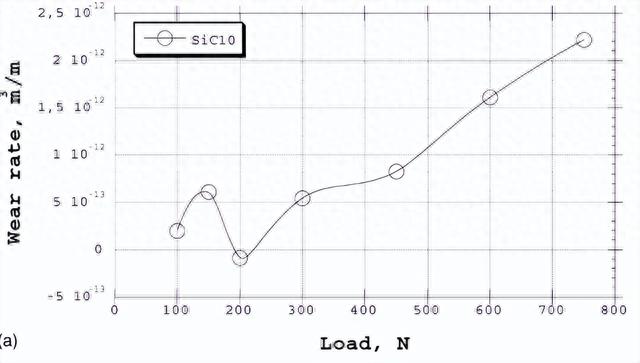
上图显示了磨损率随施加载荷的变化情况。对于SiC20,磨损率随着施加载荷的增加而持续降低。磨损率很快变为负值,这表明摩擦材料在滑动过程中向圆盘转移,而且这种转移的强度随着施加载荷的增加而增加。
另一方面,SiC10的磨损率在通过100至150牛顿时增加,在通过150至200牛顿时减少,而在通过此负载后,磨损率持续增加。
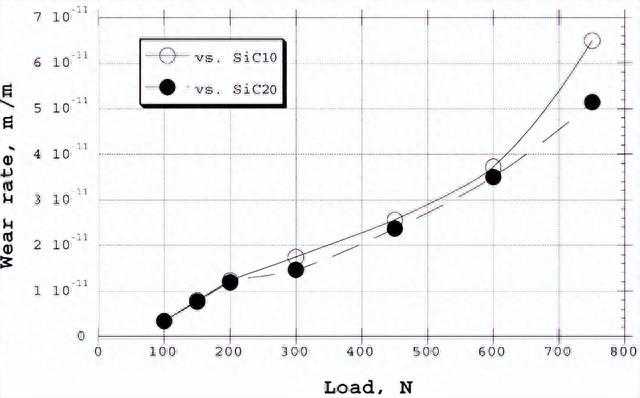
上图显示了与SiC10和SiC20相滑动的摩擦材料的磨损率。磨损率并不取决于与之滑动的材料,而是随着施加载荷的增加而增加。通过测量磨损痕迹的厚度发现,每次试验期间的工作压力从300N时的约3.5MPa增至800N时的9MPa。
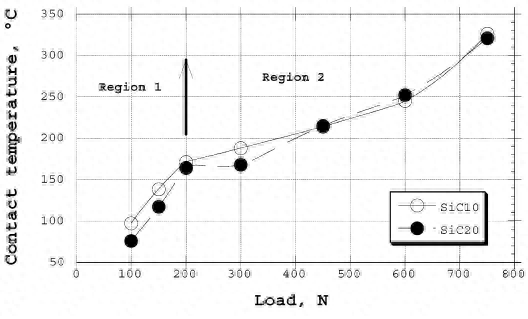
这意味着实验p0v值介于3和4之间,这个范围与实际观察到的通常范围相当。上图显示了每次测试期间记录的稳态接触温度。从图中可以看出,正如预期的那样,接触温度会随着载荷的增加而升高,两个联轴器之间几乎没有差别。还可以看出,在区域2中,接触温度低于根据区域1的相关数据线性推断的温度。
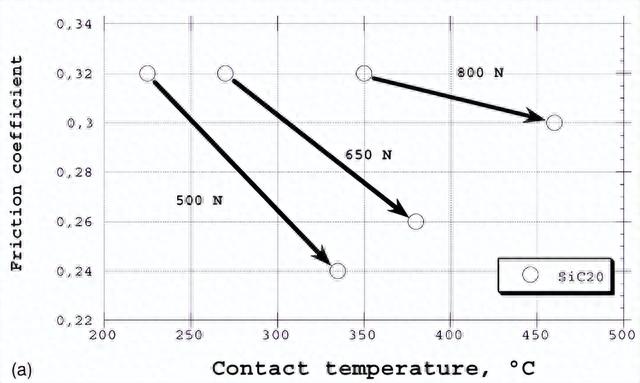
高温试验是在500、650和800牛顿时进行的,即在第2区域内。因此,这种试验的目的是检查在最关键的加载条件下过热对摩擦系数的影响。上图显示了温度对摩擦系数的影响。可以看出,当温度升高到110◦C时(通过外部加热获得),摩擦系数会增加。
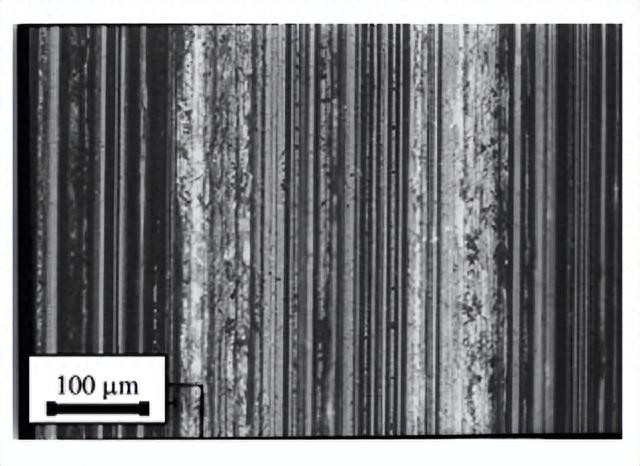
上图分别显示了SiC10和SiC20样品磨损表面的俯视图。在SiC10的情况下,可以清楚地看到磨蚀沟槽的存在。而在SiC20的情况下,只有少数沟槽存在,图中显示的粗糙度轮廓证实了这一点。
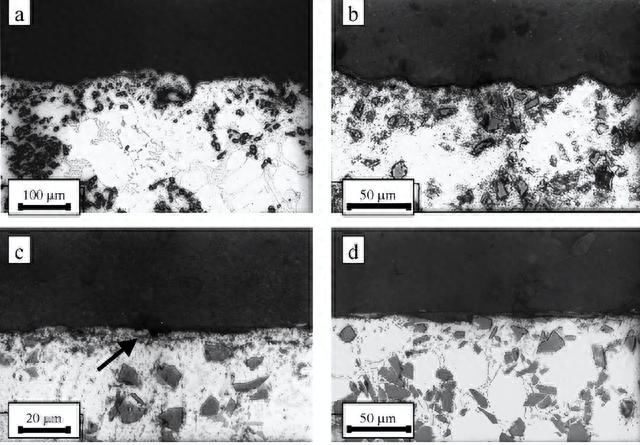
上图显示了受损的圆盘垂直和平行于滑动方向。可以看出,SiC10的磨损表面具有强烈的塑性变形特征。SiC20的磨损表面看起来很平整,因为上面覆盖了一层厚厚的转移层。
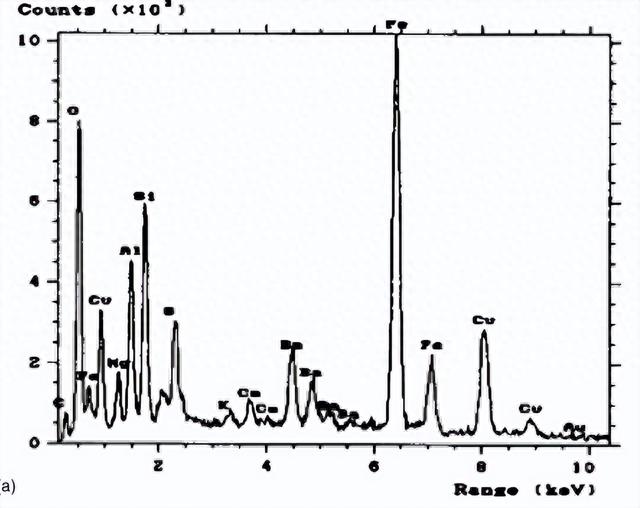
上图显示了这一点,它是SiC20横截面垂直于滑动方向的SEM显微图。现在,转移层的存在显而易见,图中的EDXS分析表明,转移层是由摩擦材料构成的。
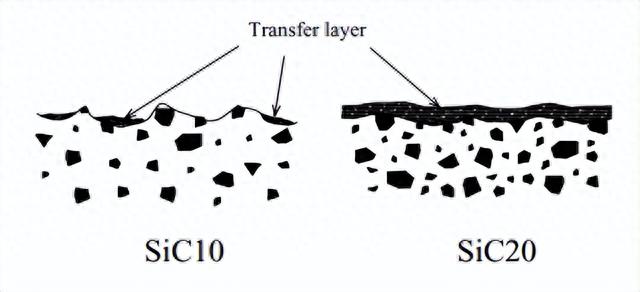
上图显示了转移层的特征。在SiC20中,转移层相当厚(约10微米),而在SiC10中,转移层很薄(不到4微米),且位于凹槽内。
在150N条件下还进行了其他试验,并观察了磨损表面和收集到的磨损碎片,以获得有关第1工作区磨损机制的信息。两种材料磨损表面的特征都是存在类似所示的磨蚀沟槽。
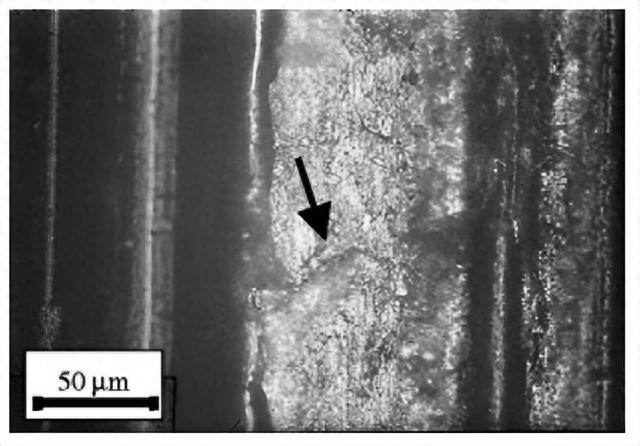
由于SiC10的硬度较低,因此其磨损尤为严重。如图所示,在所有情况下,凹槽内都有粘合剂损坏的迹象。
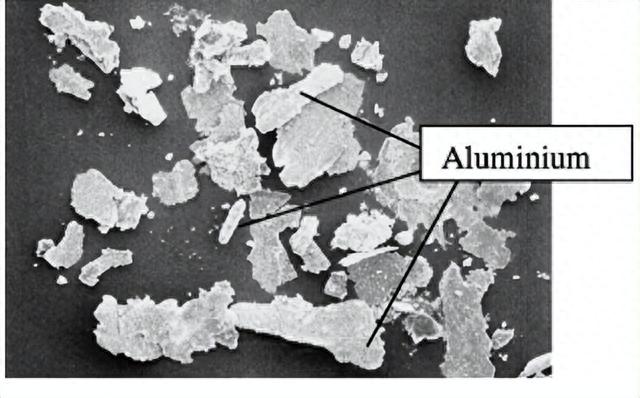
上图显示了在SiC10材料测试结束时收集到的磨损碎片的形态。在大块树脂碎片附近,可以看到一些富含铝的碎片,这些碎片是通过粘附去除的。
在200N下对SiC10进行的其他测试表明,存在类似的厚转移层。在高温条件下测试的两种配磨损表面的特征非常相似,几乎都是与施加的载荷无关。在这种情况下,始终可以观察到磨损表面上存在较厚的转移层。表1概述了在区域1和区域2以及高温试验中观察到的磨损特征。
在区域1中,SiC20的摩擦系数随载荷增加而增大,而SiC10的摩擦系数几乎与载荷无关。这种行为可以通过考虑所服务的接触过程来解释。事实上,摩擦系数一般由两个因素决定,首先是接触表面之间的粘合作用,其次是磨损导致的犁沟作用。
这两种贡献都存在,但在SiC10的情况中,主要贡献是磨损,因此摩擦系数与施加的载荷无关,因为它只取决于摩擦材料中存在的磨损硬颗粒的攻击角,可以合理地认为它不会随施加的载荷而改变。
另一方面,在SiC20的情况下,粘附力的贡献变得更加重要,因为其较高的硬度减少了磨损的贡献,而摩擦系数会随着载荷的增加而增加,因为实际接触面积增加了。就磨损率而言,在区域1中,磨损率随载荷增加而增加,SiC10的磨损率更高,因为其硬度较低。最大磨损系数为2.76×10−15m2/N(SiC10在150N条件下),因此与铸铁的典型值(介于3和8×10−15m2/N之间)相比相当低。
在区域2中,两种材料的摩擦系数都会随着载荷的增加而减小,因此也会随着接触温度的升高而减小。这是一个重要的效应,称为"衰减"。值得注意的是,在Al-MMC与钢材滑动的情况下,摩擦系数随温度升高而减小。衰减效应与摩擦面材料的退化有关。当载荷为200N时,两个联轴器的接触温度均达到150◦C,在此温度下,摩擦材料的粘合剂酚醛树脂会发生强烈的热软化。
在区域2中,摩擦力主要由粘合剂产生,因此与分离接触体所需的平均剪应力τm成正比。因此,随着温度的升高,摩擦材料的密实度会因衰减而降低,τm也会随之降低,因为摩擦材料表现得像固体润滑剂。在这一区域,SiC10的摩擦系数始终低于SiC20。
在区域2中,所研究的两种材料具有截然不同的磨损特性:SiC10因磨损而磨损;SiC20则因摩擦材料的转移而增加重量。对于SiC10来说,磨损率随施加载荷的增加而增加,这显然是由于复合材料的软化,这有利于磨损。
对于SiC20,由于转移层保护了材料,因此没有磨损。转移强度随载荷增加而增加。事实上,随着载荷的增加,热软化涉及到接触面以下更深的区域,因此有更多的材料可用于转移。
为了理解为什么SiC20材料能完全受到转移层的保护,而SiC10却不能,我们必须考虑到Al-MMCs盘的表面损伤是两种动态现象的结果:摩擦材料中的硬质颗粒产生的磨蚀沟槽和摩擦材料的转移。
在SiC10中,由于硬度较低,磨料沟纹占主导地位,而且转移速度不足以形成较厚的转移层。另一方面,SiC20具有更强的抗切槽能力,因此转移率高,足以形成厚的转移层,从而保护底层材料。根据这一推理,我们可以解释高温试验中出现的过程。在这些试验中,SiC20和SiC10都出现了转移现象。
事实上,外部加热导致的热软化增加了摩擦材料向对磨盘的转移率。这压倒了磨料沟槽效应,并允许形成厚的转移层。就Al-MMC磨盘的耐磨性而言,外部加热是有益的,因为它可以形成保护性转移层。
然而,外部加热对盘面磨损和摩擦系数的影响是负面的。事实上,由于热软化的增加,摩擦材料的磨损率也会增加,达到10−13m2/N的数量级,这被认为是摩擦材料磨损率的上限。
两种Al-MMC与半金属摩擦材料的干滑动摩擦和磨损行为在很大程度上取决于载荷和外部加热。当施加的载荷小于200N时,磨损是通过磨损和粘附实现的,摩擦系数相当高,约为0.45.当施加的载荷大于200N时,接触温度会高于约150◦C,从而导致摩擦材料中的有机粘合剂降解。