
文 |史记新说
编辑 | 史记新说
在1773 K到1873 K的不同时间(60到600秒)实验研究了不同还原度的氢直接还原铁球团(H-DRI)熔化过程中的反应机理,重点研究了自生渣的形成。
已经发现,在金属相熔化之前,自生炉渣在球团内部形成。自生熔渣的形成始于最初位于铁颗粒中心的FeO的熔化。液态FeO流入颗粒的孔隙网络中。流动时,液态FeO溶解了部分残余氧化物,形成自生熔渣。
炉渣留在孔隙网络中,直到铁熔化。铁熔化后,熔渣聚结成球形熔滴。当通过浮选分离金属和炉渣相时,达到最终状态,因为在液态铁的表面上形成了大量炉渣。
此外,由于本研究中使用的铁矿石中含有钒,因此在实验观察的基础上单独讨论了钒的行为,为今后提取钒的研究奠定了基础。
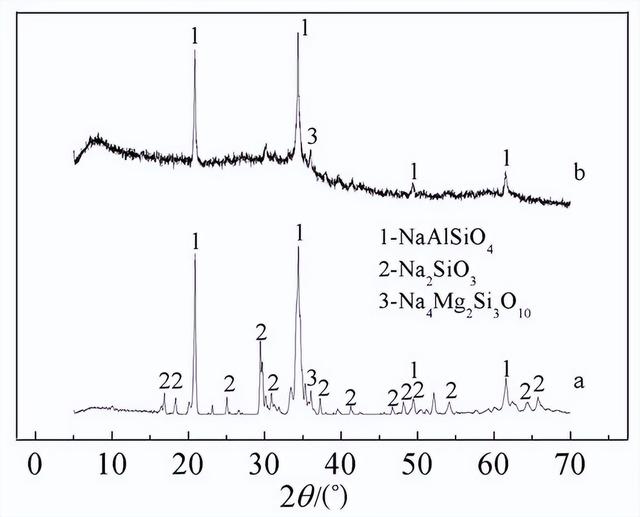
许多钢铁生产商依赖以铁矿石为基础的纯铁来满足他们对高等级钢铁的需求。铁矿石主要通过鼓风炉-氧气顶吹转炉路线炼钢,这是主要的炼钢路线。
大量的一氧化碳2排放与这种生产路线有关,主要是由于在高炉中使用焦炭作为还原剂。
随着环境因素在社会中变得越来越重要,世界各国政府都制定了减少工业环境影响的目标,例如巴黎协议和联合国可持续发展目标。因此,许多钢铁生产商开始了无化石炼钢之旅,减少了他们的碳足迹。
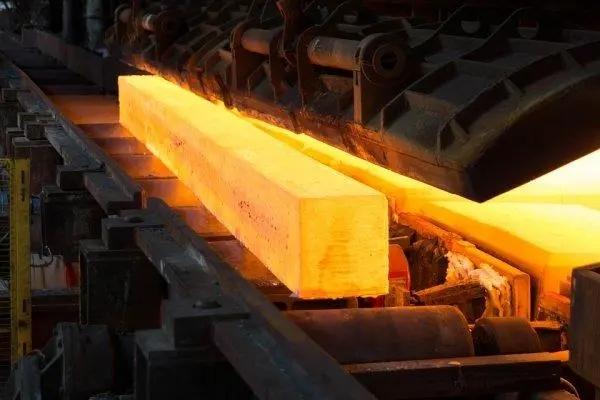
已经发现鼓风炉路线的一个有希望的替代方案是调整现有的使用天然气还原铁矿石的直接还原竖炉,改为使用更高比例的或者甚至纯的氢气作为还原剂。
使用H的直接还原竖炉2随着还原剂产生H2o作为副产品代替了CO2。这一过程的可持续性取决于能否获得可再生能源生产的氢气。
铁产品,氢直接还原铁(H-DRI),是一种可以在电弧炉(EAF)中熔化的固体产品。
H-DRI的使用影响了EAF工艺路线,使得与H-DRI的熔化和精炼相关的基本理解变得越来越重要。最重要的原因是优化炼钢成本以弥补与绿色氢电解相关的高成本。

氢DRI最有可能被连续地而不是分批地送入电弧炉。H-DRI的熔化将受到炉渣成分、局部温度以及球团与炉渣和/或钢浴的接触的影响。
DRI含有铁和几种来源于脉石、熔剂和氧化铁不完全还原的氧化物。与来自高炉的生铁不同,Si、Mn、V和P(当存在于磷灰石中时)等成分在H-DRI中保持氧化状态。
当H-DRI熔化时,未还原的氧化物形成所谓的自生渣。本研究组之前的两项研究已经研究了熔融过程中未还原氧化物的行为。
发现氧化物的精细混合以及球团中增加的CaO添加量在球团的分批熔化过程中提供了有效的磷精炼。
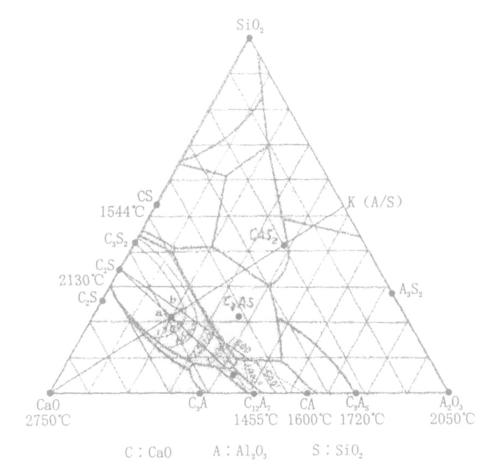
这些研究表明,球团中形成的自生渣在熔化过程中起着重要作用。因此,H-DRI熔化过程中的反应机制是重要的,需要更彻底地研究。
此外,这项研究是基于含有0.1至0.2重量%钒的铁矿石球团。钒渣对钢铁生产商来说是一种有价值的副产品,因此值得进一步研究。
经济上可行的钒提取的关键特性之一是炉渣中钒的浓度。因此,关于钒在熔化过程中从氢DRI转移到自生炉渣的信息对于开发从氢DRI炉渣中提取钒的途径是有价值的。
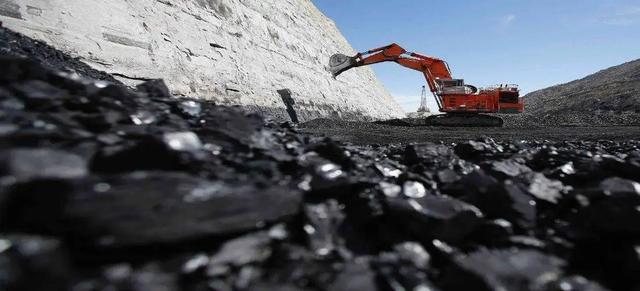
因此,这项研究的目的是双重的。首先,旨在增加对DRI熔化过程中反应机理的理解。
第二,该研究旨在增加对钒在熔化过程中行为的了解,这将有助于未来与钒提取相关的研究。
针对这些目标,进行了一项实验研究,其中还原度为90%和99%的单个H-DRI芯块在1773 K和1873 K下加热不同的时间(60至600秒),对应于不同的熔化阶段。
作为开始条件,热量仅通过传导提供,这对应于与炉渣和钢接触不良的情况。在快速冷却之后,在扫描电子显微镜(SEM)中使用背散射电子(BSE)显微镜和电子色散谱(EDS)来研究H-DRI芯块的截面。
为了获得具有不同还原度的H-DRI球团,来自瑞典北部的基于磷灰石铁矿的工业赤铁矿球团在1173 K下被纯氢气(2 L min)还原-1)在密封的垂直管式炉中。
赤铁矿球团(∅ = 10至12.5毫米)含有67.8重量%的铁和3重量%的非铁氧化物。非铁氧化物来源于制粒过程中添加的脉石、膨润土和白云石,通过以下等式计算减少程度:


还原后,将一个球团放入小MgO坩埚中。使用一个小筐钼丝作为装有丸粒的坩埚的悬挂装置。
在所有实验中,丸粒、坩埚和篮子的质量保持不变,即。2、12和0.4 g,以不改变熔化样品所需的热量。如图所示,使用40厘米钼丝将样品篮连接到钢棒的下端1.
样品最初放置在熔炉的冷却室中。关闭炉子,并通过引入真空确保气密性。然后向熔炉中重新充入氩气。为了确保气氛已经充分转变为氩气,将炉子抽空并再充入氩气两次。
最后一次再填充后,氩气流量为0.1升/分钟−1得到了维护。然后将炉子加热到1773 K或1873 K的温度。当达到实验温度时,将样品降低到高温区,在那里保持预定的时间,如表中所示二,其中也说明了每个样品的还原程度。
通过将样品快速提升至冷却室,同时将氩气吹入冷却室以增强对流和冷却速率,从而终止实验。冲洗保持30分钟。
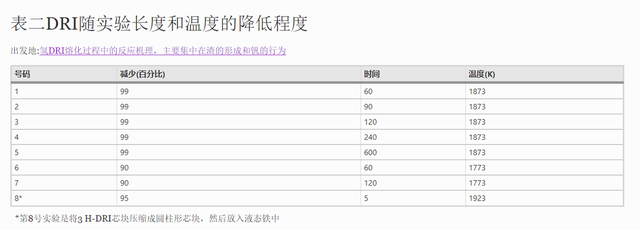
进行了一个补充实验,其中将三个压缩的H-DRI的圆柱形丸粒滴入装有液态铁的坩埚中,表中的实验8。液态铁在氩气氛下保持在1923 K。5秒钟后,样品(液态铁+圆柱形小球)在冷却室中冷却。
然后制备样品用于SEM。此外,还制备了一个未还原的赤铁矿球团以及两个还原度分别为90%和99%的未加热H-DRI球团。
检查样品的微观结构,并使用EDS在样品中发现的每个相中的至少三个不同位置确定相组成。鉴于EDS的局限性,成分数据仅用于相表征。
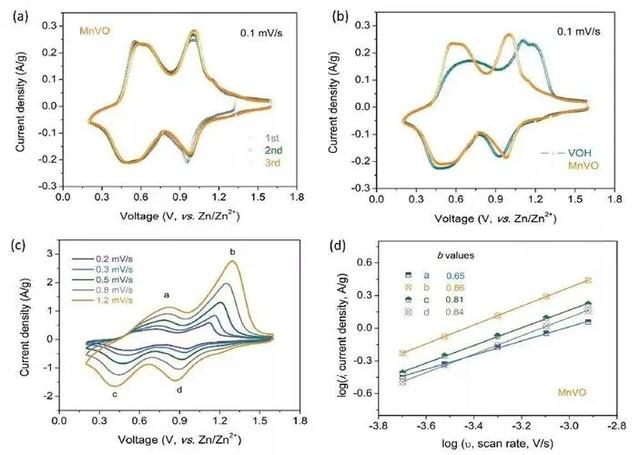
为了理解H-DRI的熔化过程,在熔化之前了解芯块的微观结构是必要的。
因此,为了有助于讨论,在加热之前,检查了一个未还原的赤铁矿球团和两个还原度分别为90%和99%的H-DRI球团。
如图所示,未还原的球团含有赤铁矿、镁铁矿和富含CaO的硅酸盐2。未还原的球团也含有磷灰石,尽管图中未显示2。
除了富含CaO的硅酸盐之外,所研究的球团矿还含有少量未在此研究的其他硅酸盐。这些相是根据它们的组成来识别的。
它们是通过EDS分析测定的,并在表中给出罗马数字3。尝试使用X射线衍射(XRD)进行物相鉴定,但由于少量的非铁氧化物,仅检测到赤铁矿。
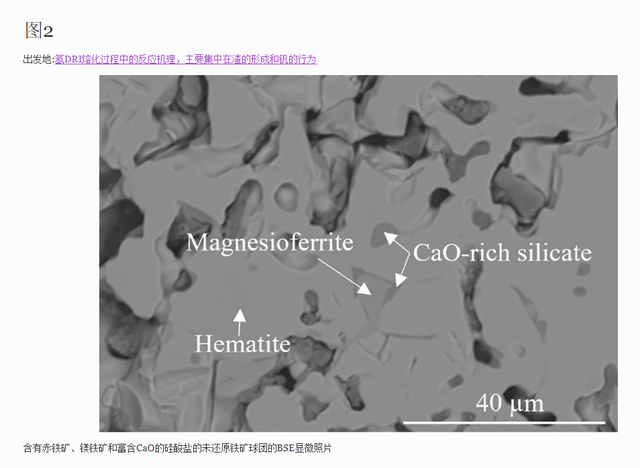
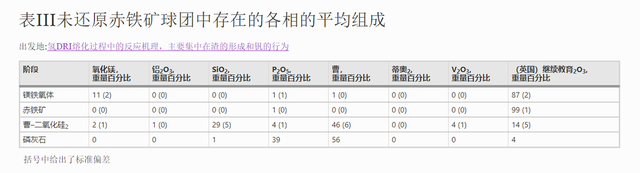
加热前的H-DRI颗粒的微观结构如图所示3(减少90 %)和图4(a)(减少99%)。正如未还原的球团一样,这些球团含有富含磷灰石和CaO的硅酸盐。它们还包含wüstite和CaTiO3。
此外,99%还原球团在1µm码。注入静脉的显示了99%还原颗粒中不同相的成分。在90%还原颗粒中发现的相组成是相似的。
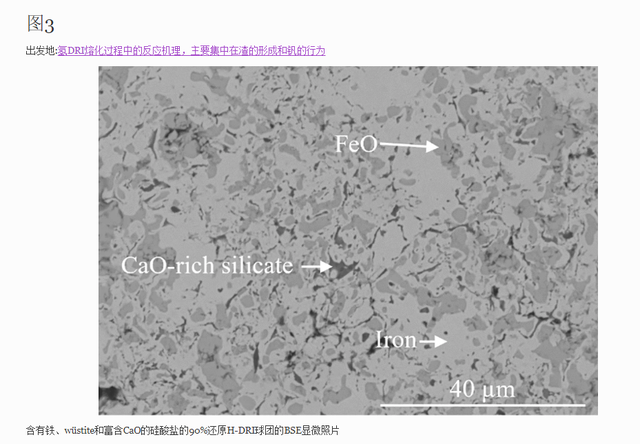
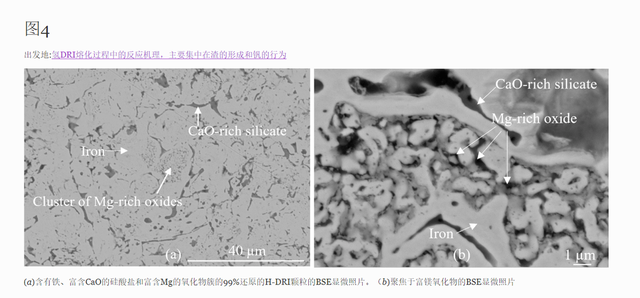

wüstite相包含FeO、一些MgO和少量的MnO和V2O3,在表中给出注入静脉的。自然地,99%还原度的球团中的wüstite的量比90%还原度的球团中的低得多。这解释了为什么图中没有捕获到未还原的wüstite4(一)。
1 m量级的富镁氧化物通常含有少量的其他氧化物,例如钒2O3,根据表注入静脉的。如图所示,它们成簇分布4(一)。数字4(b)显示了高放大倍数下的富镁氧化物。
富含CaO的硅酸盐在两个图中都有发现3和4。CaO/SiO2富含CaO的硅酸盐的摩尔比在0.6至2.5的范围内,平均值为1.3。桌子注入静脉的呈现平均构成。富含CaO的硅酸盐还含有少量其它氧化物,例如MgO、P2O5、和V2O3.
富含CaO的硅酸盐和富含Mg的氧化物的FeO含量变化范围很大,可能是由于样品背景的干扰。注意表中使用的铁和钒的氧化态注入静脉的在这项工作中没有被确定。
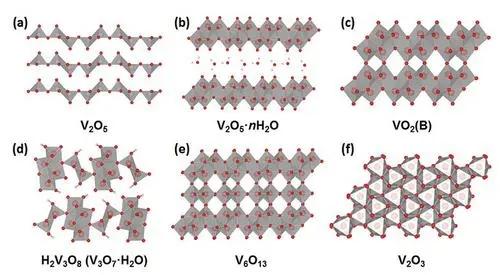
将还原度为90%的球团加热到1773 K,以研究炉渣的形成。图中显示了加热60秒和120秒后的微观结构5(a)和(b)。两种微结构都是多孔的。
根据数字5(a)和(b)中,孔构成颗粒中的孔网络。数字5(a)显示在加热60秒后,wüstite和富含CaO的硅酸盐仍然分离。数字5(b)显示在120秒后,富含wüstite和CaO的硅酸盐已经反应并形成炉渣。
矿渣存在于孔隙网络中。炉渣由两相组成,在图中标记为相1和相25(二)。第一阶段主要包含氧化钙、二氧化硅2和FeO,而相2包含FeO和MgO。根据EDS测量,这些相的平均组成示于表中V.
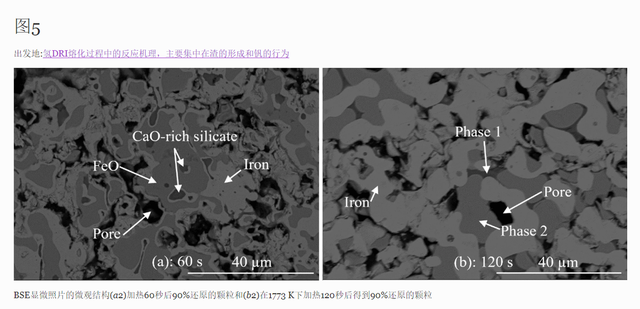
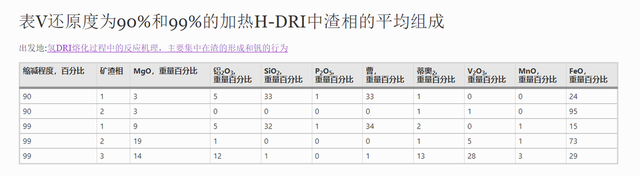
数字6(a)显示了已经加热60秒的颗粒的多孔微结构。铁还没有熔化,而复杂的渣相已经在球团的孔隙网络中形成。
数字6(b)显示了炉渣中存在的相,表示为相1至3。表中给出了各相的平均组成V。
根据相组成,很明显,图中的相1和相26(b)与图中的阶段1和阶段2相同5(b)相,而相3包含MgO,V2O3,铝2O3,还有FeO。此外,磷灰石和CaTiO3存在,作为数字6(c)和(d)显示。
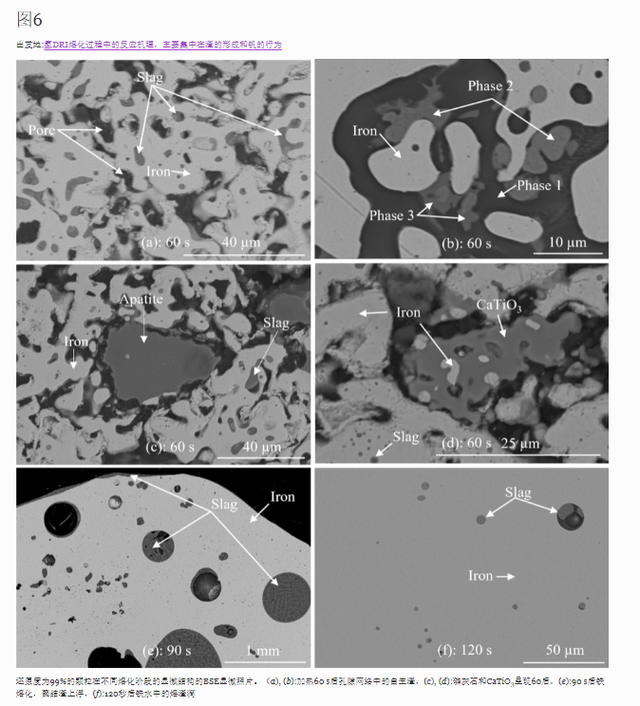
90秒后,铁熔化了。如图所示,液态金属相中存在最大1毫米的熔渣滴6(e)。此外,数量级为10的更大数量的更小熔渣液滴μm存在于液态金属相中。如图所示,渣层覆盖在铁的表面6(e)。与前述相同的相,相1-3,存在于渣层中。
120秒后,大的熔渣滴已经加入熔渣层,形成大块熔渣相。然而,一些最大尺寸约为30µ直径为100米的粒子保持在液态金属相中,见图6(f)。
240秒和600秒后,残留在铁中的氧化液滴不大于5μ米(meter的缩写)

将三个压缩的H-DRI芯块的圆柱形芯块丢入液态铁中。需要压缩三个H-DRI芯块,以增加H-DRI的热质量,并允许观察熔化过程,因为一个芯块在尽可能快的冷却后完全熔化。
在H-DRI被投入到液态铁中5秒钟后,它还没有完全熔化。数字7显示在这一点上,自生熔渣已经在整个圆柱形球粒中形成。在球团和液态铁之间的界面上,释放出自生熔渣液滴。
