普渡大学机械工程系团队最新研发出一种可编程变形的柔性机器人表面(PARMS),通过创新性地结合离子驱动器阵列和机器学习算法,让机器人表面能够实现任意形状的动态变形。这项突破性成果已发表在近期的《Science Advances》封面上。
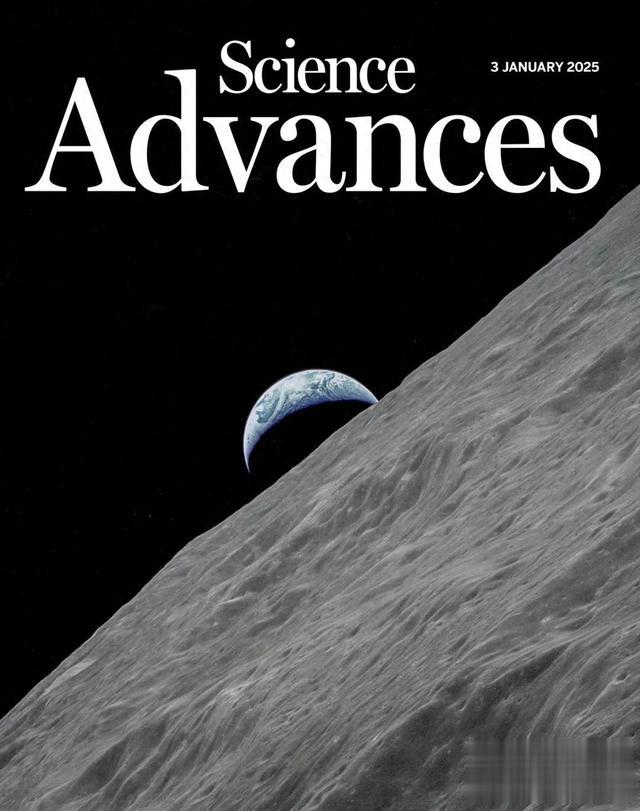
这种柔性表面不仅能实现精准的形状控制,更重要的是首次在大面积柔性驱动器阵列中实现了被动寻址技术!相比传统的直接寻址方式,被动寻址技术可以将N×N阵列的控制输入从N2减少到2N,大大简化了控制系统的复杂度。
▍创新的被动寻址架构
该系统采用了一种交叉排列的电极结构,通过在多孔PVDF膜两侧镀上铂/钯金属层,再电化学沉积聚吡咯(PPy)电极,形成了一个6×6的驱动器阵列。每个像素都位于行列电极的交叉点处,单个像素尺寸为7.5mm×7.5mm,像素间间隔1.5mm,整个作用区域达到54mm×54mm。
与传统的每个像素需要独立控制信号不同,这种被动寻址方式只需要控制行列电极即可。当给定行电极施加电压,同时将列电极接地时,交叉点处的像素就会发生形变。通过逐行扫描的方式,就可以实现对整个阵列的控制。
系统巧妙地利用了离子驱动器的电容特性 - 即使在断开电压后,驱动器仍能保持变形状态。实验表明,在0.8V驱动电压下,即使断开电源3分钟,驱动器的形变量仅下降4%。这一特性确保了在扫描过程中已激活的像素不会回弹,从而实现了稳定的形状控制。
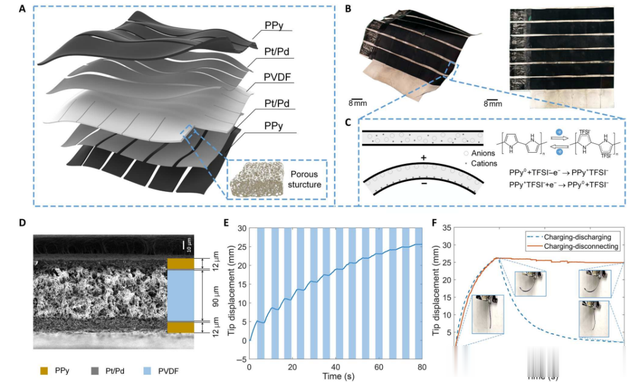
上图展示了PARMS的设计与工作原理。(A)显示了以聚吡咯(PPy)为活性电极、多孔聚偏二氟乙烯(PVDF)为离子导体的交叉电极阵列结构,通过显著减少控制输入实现高效像素独立控制。(B)展示了PARMS在初始平整状态与激励后的变形状态。(C)解析了离子电活性聚合物致动器的原理:PPy电极在阳极氧化结合阴离子TFSI⁻,在阴极还原释放TFSI⁻,引发电极体积差异膨胀,实现形变。(D)通过电子显微镜横截面图展示了各层结构,PVDF基底厚90微米,PPy电极层12微米,Pt/Pd导电层小于1微米。(E)通过间歇性电压应用,实现致动器在无电压状态下仍能维持形变,提升能效。(F)比较了“充电-放电”和“充电-断开”两种操作状态,后者表现出更好的形变保持性能。整体设计结合创新结构和控制技术,为动态形状重构提供了高效、灵活的解决方案。
▍突破物理限制的关键技术
为了解决像素间离子串扰的问题,研究团队在电极间隙处创新性地添加了聚合物阻挡层。测试结果显示,这种设计将电压误差从原来的15.6%降低到9.2%,特别是在多个像素同时激活的情况下效果更为显著。
团队还针对电极电阻损耗进行了补偿。实验发现,对于距离触点最远的像素,约有20.4%的电压损失在电极上。通过提前补偿这部分损耗,显著提高了控制精度。
▍机器学习助力实时精准控制
如何让这个包含36个耦合驱动器的复杂系统精确变形到目标形状?团队创新性地引入了机器学习方法。
他们首先通过有限元模拟(FEM)生成了大量训练数据。模拟中巧妙地利用热膨胀方程来近似描述离子迁移导致的形变:εV = βΔV(其中εV为应变,β为电膨胀系数,ΔV为电压变化)。这种方法不仅考虑了材料的非线性大变形,还包含了电阻损耗等非理想因素。
基于这些高质量的训练数据,他们构建了一个多层感知器(MLP)神经网络。正向预测模型采用了(73, 300, 580, 880, 1200)的隐藏层结构,而反向设计模型则使用了(901, 700, 550, 300, 180)的结构。
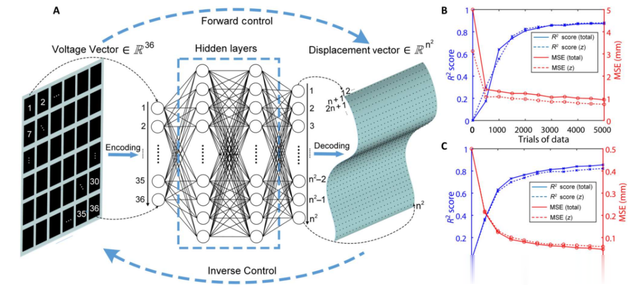
上图展示了多层感知机(MLP)模型的结构与训练性能。(A)为MLP模型的示意图,该模型用于被动矩阵软变形表面的形状控制,包括输入层、隐藏层和输出层,通过神经网络实现前向预测和逆向控制。(B)展示了逆向控制中R²分数和均方误差(MSE)随训练数据规模变化的关系,表明随着数据规模的增加,模型性能显著提升,R²趋于接近1,MSE逐步降低。(C)则展示了前向控制中类似的趋势,证明更大的训练数据规模对模型预测精度的提升同样重要。这些结果验证了MLP模型在软变形表面控制中的高效性,并强调了充分训练数据对优化性能的重要性。
研究发现,当训练数据量达到5000组时,模型的R2分数可达到0.88(正向预测)和0.82(反向设计)。更重要的是,模型能在0.01秒内完成预测,实现100Hz的控制频率,远超传统有限元分析30分钟的计算时间。
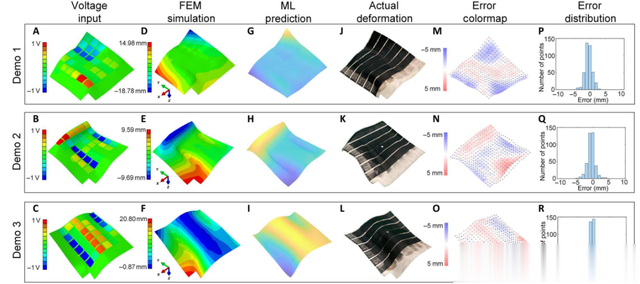
上图展示了基于机器学习对PARMS进行前向控制的效果。(A, C, E)分别为PARMS在不同输入电压下的实际形变。(B, D, F)为ML算法预测的对应形变结果,展示了较高的预测精度。(G-L)通过有限元方法(FEM)模拟PARMS的形变,其中(G, I, K)为输入电压分布,(H, J, L)为对应的z方向位移幅度。(M-R)则对实际形变与模拟结果的误差分布进行了分析,其中(M, O, Q)为数值误差分布,(N, P, R)为空间误差分布。这些结果表明,ML算法不仅能够准确预测PARMS的形变,还在空间分布上与FEM模拟结果具有较高一致性,为动态表面形变的精准控制提供了有力支持。
▍实验验证与性能突破
团队进行了一系列实验来验证系统性能。在形状重现测试中,系统能够准确复制预定义的各种曲面。对于单字母"P"的重现,与目标形状的平均误差仅为1.42mm,与仿真结果的误差更是只有1.08mm。
在动态变形序列测试中,系统展示了连续变形的能力。通过优化刷新策略,每个像素的充电时间为3s,完整的形状变换约需108-144s即可完成,变形完成度达到97.4%。
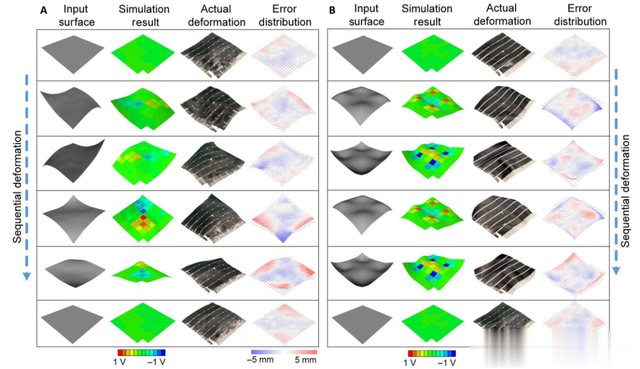
上图展示了动态形状变形系列的逆向控制效果。(A)和(B)分别为两个形变演示系列。在每一步中:最左侧图像为输入的目标表面形状;第二幅图像为通过模拟得到的形变结果;第三幅图像展示了物理设备的实际形变效果;最右侧图像为目标形状与实际形变之间的误差分布。图中黑色点为从物理设备采集并处理的点云数据,而表面形状由模拟结果推导而得。这些结果清晰展示了ML算法对目标表面的高效逆向控制能力,同时通过误差分布揭示了算法在实际形变控制中的准确性和潜在优化空间,为复杂表面动态形变的精准实现提供了技术支撑。
▍未来应用与发展方向
这项技术的成功为柔性机器人开辟了新的应用前景:
触觉显示:可以实时将3D模型、扫描的人脸或地形图等虚拟表面物理化呈现
远程协作:两个相同的变形表面可以实时同步,实现远程物理交互
可穿戴设备:低剖面设计使其适合集成到柔性可穿戴产品中
增强现实:为AR/VR提供真实的触觉反馈界面
未来的研究重点将包括:
1.提高分辨率:目前的6×6阵列还有很大的提升空间
2.优化响应速度:通过改进电极层设计,提高刷新率
3.增强控制精度:探索使用3D卷积神经网络等更先进的算法
4.扩展应用场景:结合其他智能材料,拓展功能边界
这项研究不仅展示了被动寻址、柔性驱动和机器学习的巧妙结合,更为大规模柔性机器人系统的控制提供了全新思路。相信随着技术的进一步完善,这种可编程变形表面有望在人机交互、远程协作等领域发挥重要作用。