
文|万象硬核
编辑|万象硬核
«——【·前言·】——»
锂电池具有高能量密度比、输出功率高、循环使用寿命长和无污染等优点,其广泛应用于电子设备和新能源汽车等领域,由于锂电池具有高能量密度的电极材料,导致其容易发生安全问题。
近年来,国内外报道了多起新能源汽车起火/爆炸等严重的热失控事件,电池安全性已经成为制约新能源汽车发展的一个重要因素,据统计,碰撞是导致新能源汽车发生热失控的主要原因。
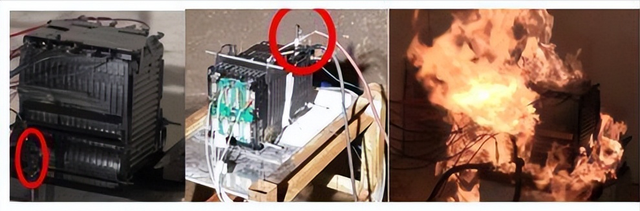
新能源汽车发生碰撞时,电池单体之间、电池与电池箱框架之间会发生冲击,导致电池受到结构损伤发生内短路,从而引发热失控等严重的安全事故。
锂电池受到局部挤压是汽车碰撞引发的主要损伤形式,也是造成电池失效而发生热失控的原因,局部压痕实验可以研究电池侧面受到局部损伤的规律,那么该如何解决这一难题呢?
研究现状
目前,国内外对于圆柱形锂离子电池在局部压痕下的安全性研究已有一些重要成果。研究人员结合实验与仿真的方法研究了圆柱形锂电池在径向局部压痕下的热失控规律,开发了电池高保真的力-电-热耦合模型,并建立了典型的内短路标准。
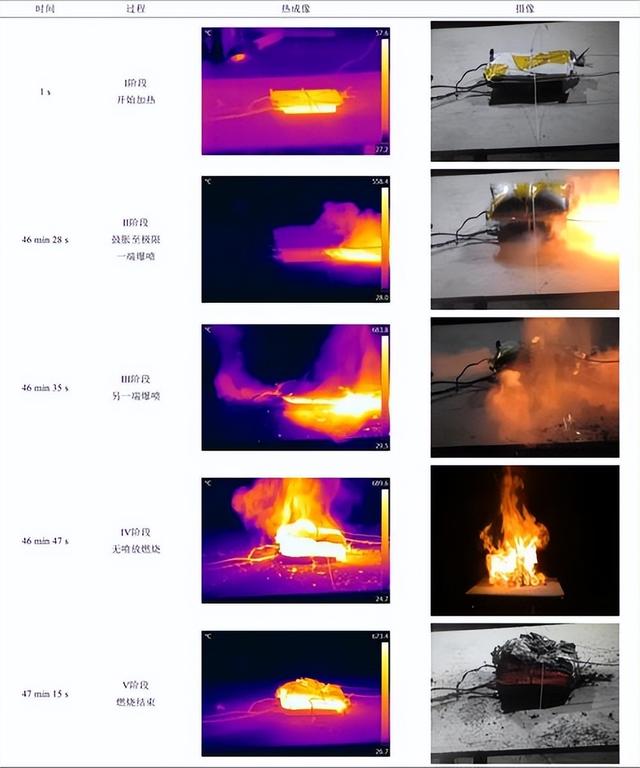
研究人员利用仿真模型研究了圆柱形电池在径向局部压痕下的失效机理,并分析了压头尺寸和压痕位置对电池安全性能的影响,并利用X射线计算机断层扫描技术(XCT),并采用渐进侵入的方式对锂电池进行局部压痕试验,从微观和宏观尺度上对锂离子电池单元中的内部短路进行了研究。
相关学者选用了三种不同容量的18650锂电池,并分别在径向挤压和局部压痕工况下进行实验,分析了加载形式和不同容量对电池失效过程的影响。
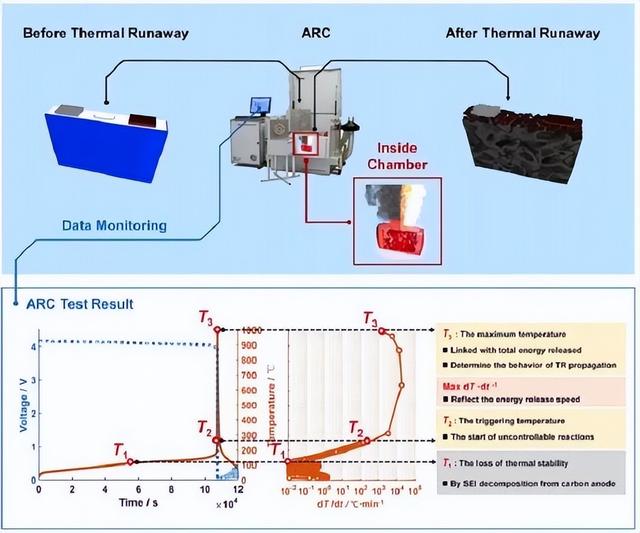
研究人员研究了锂电池在局部压痕下的失效特征,提出了一种新的现象学分析模型来得到压头与电池的接触面积,并利用有限元模型进行了验证。
结合了实验和仿真研究锂电池在压痕下的热失控行为,并揭示了热失控触发机制,解释了电池内部短路引起的电化学行为。
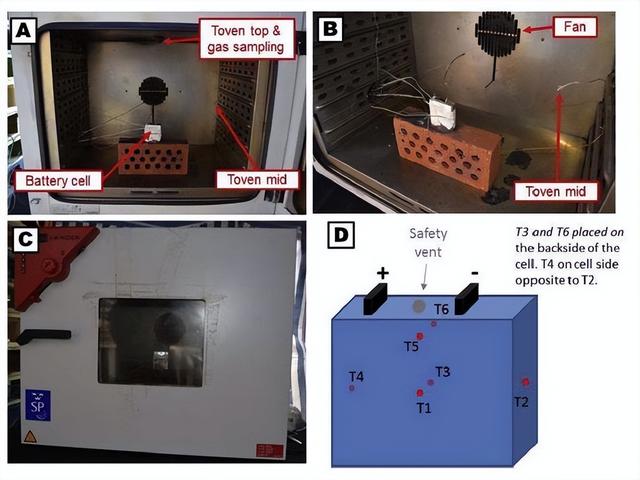
上述研究在局部压痕的安全性方面做出了较好的探索,但尚待进一步完善。尤其是缺少锂电池在局部压痕实验下相关控制参数(如荷电状态、加载速度、压痕位置和压头尺寸)对其安全性能的影响规律。
针对上述问题,我们今天以18650锂电池作为研究对象,通过搭建的机械滥用实验平台,研究锂电池在径向局部压痕下的力-电-热表征参数的变化关系,以渐进压缩的方式分析其失效过程,并且设计实验详细分析电池在受到不同加载工况下的安全性能,建立电池荷电状态、压头速度、压痕位置和压头尺寸与电池安全性能的表征关系,并根据实验结果提出锂电池安全性设计的具体建议。
实验方法
我们选用18650锂电池作为研究样本(图1(a)),主要由内芯(图1(b))和钢外壳(图1(c))组成,内芯由正极、负极和隔膜多层卷绕而成。
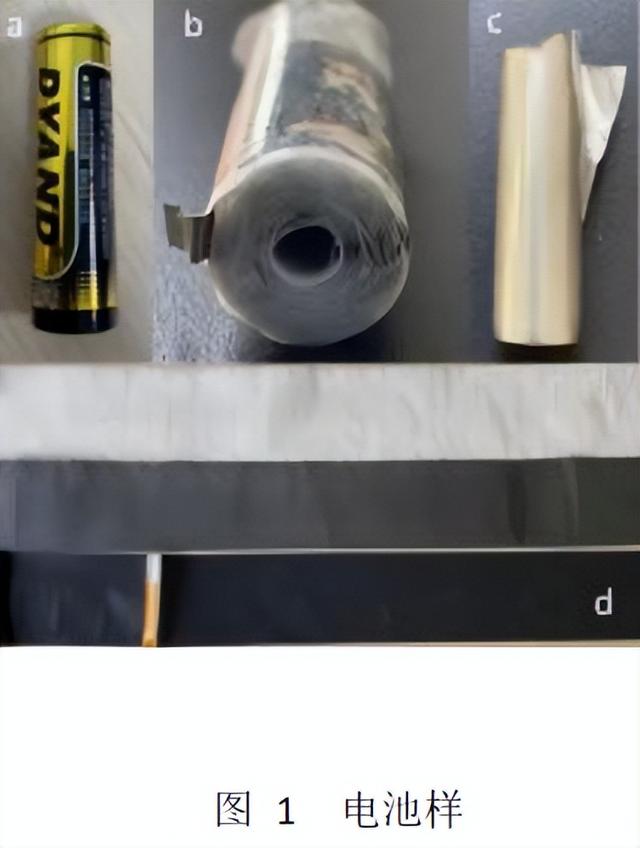
正极由活性材料钴酸锂和集流体铝箔组成,负极由石墨涂层和集流体铜箔组成,隔膜为聚乙烯材料,图1(d)为内芯拆解后的正极、负极和隔膜组件,本文研究电池样本的参数如表1所示。
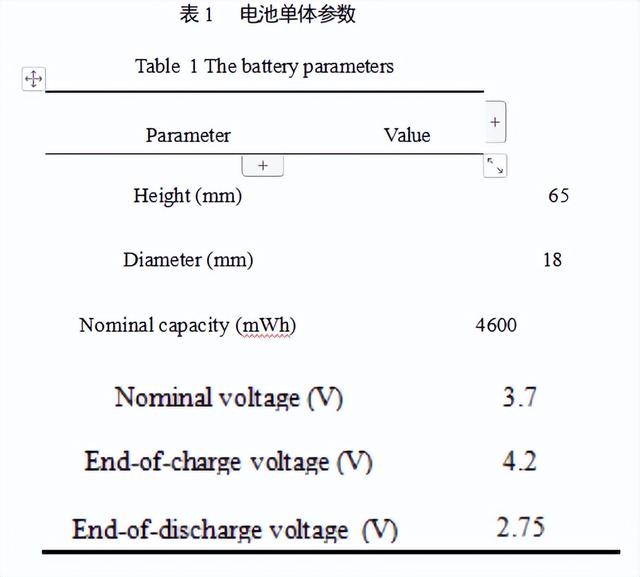
如图2(a)所示,为压痕测试实验平台,利用万能拉伸试验机对电池施加载荷并记录时间-位移力的数据,量程为100kN;
电压使用TBS2204B示波器测量,将导线连接电池正负极两端,测量电池的电压变化;
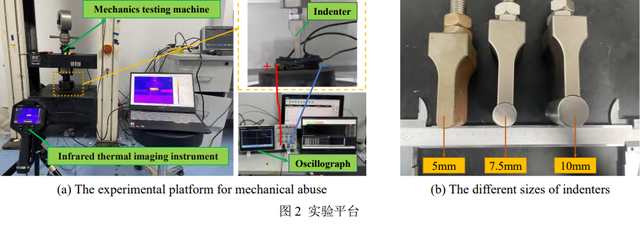
使用FOTRIC红外热成像仪测量电池表面的温度分布以及最高温度变化曲线,使用热电偶放置在电池侧面的几何中心来校验发射率,经过校验,发射率设定为95%,热成像仪放置在距离电池1m处,采样时间设置为1s;
使用300mm×250mm×150mm的透明保护壳,容纳电池爆炸碎片和烟雾,以保证实验的安全性。
本文针对径向局部压痕的特点,设计了四组实验,其参数信息列于表2中。首先设置第一组实验,在电池SOC=100%状态下做压痕滥用实验,分析电池的失效过程和温度演变规律,其中SOC(StateofCharge)表示电池的荷电状态,通常用百分比表示。
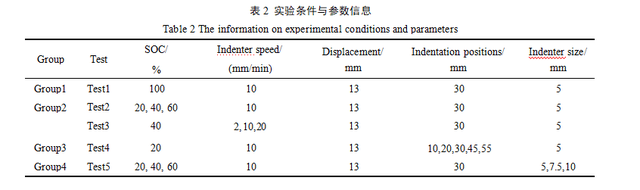
假设Q1为当前电池剩余电量,Qt为电池的总电量,则SOC=(Q1/Qt)×100%。
设置第二组实验,分别测量不同SOC和不同压头加载速度时电池的力-电-热响应,为本次实验的基准数据,用于探究不同实验条件;
设置第三组实验,测量不同压痕位置时电池的力-电-热响应,并结合本文电池尺寸特点,压痕位置设5种不同情况,分别为距离负极10mm、20mm和30mm处,距离正极10mm和20mm处;
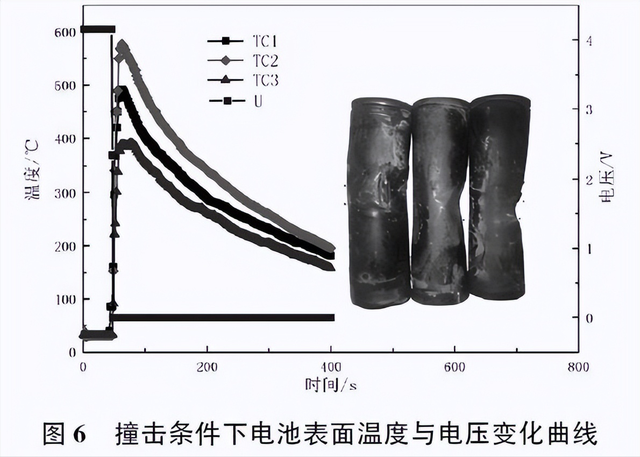
设置第四组实验,测量不同压头尺寸下电池的力-电-热响应,压头尺寸如图2(b)所示,半径分别为5mm、7.5mm和10mm。此外,当压头达到加载位移时停止,压头返回至初始位置,每组测试至少重复三选次,以保证数据的重复性。
实验结果与讨论
图3为电池在Group1-Test1组的实验结果。图3(a)为电池的力-电-热响应曲线,结合曲线分析发现,其载荷变化可分为四个阶段,采用渐进压痕方法,分析其特征。
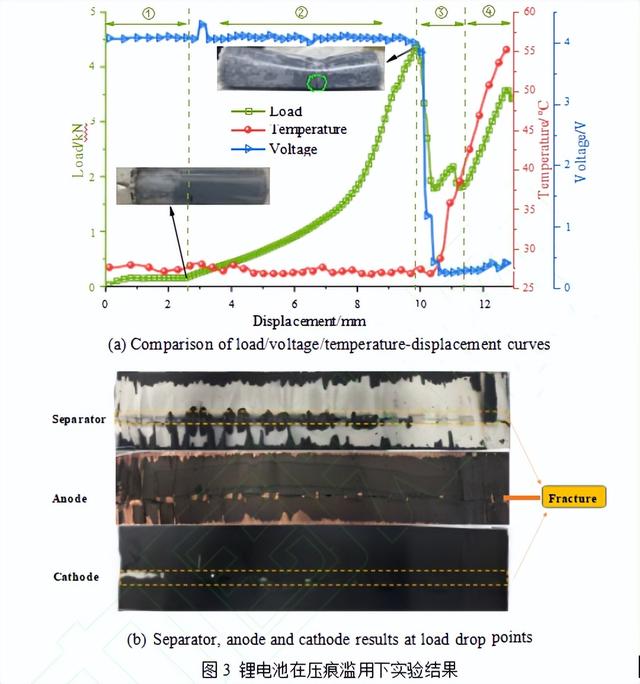
第一阶段是密实化阶段,该阶段在侵入量为2.6mm以内,其特征是载荷缓慢上升,因为电池外壳与内芯及内芯层与层之间存在间隙,在压缩过程中发生了密实化过程。
第一阶段结束时,对电池拆解发现内芯没有发生明显形变。
第二阶段是指数上升阶段,该阶段在侵入量为2.6mm至9.9mm之间,电池各组件间隙被压实,载荷以指数形式快速上升至电池极限载荷4.34kN。第三阶段是载荷下降阶段,侵入量为9.9mm时载荷迅速下降至1.82kN,当极限载荷出现时,对电池拆解发现载荷下降的主要原因是内芯各层发生断裂,电池完全失效。
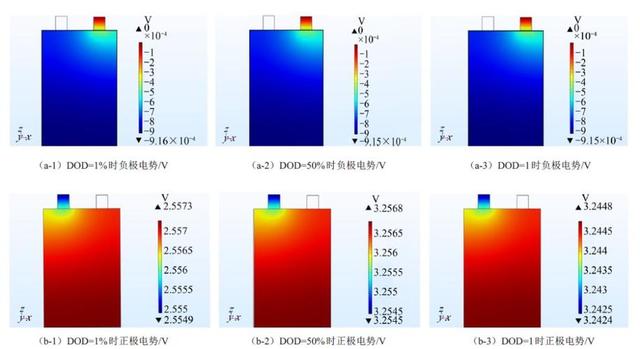
图3(b)为电池失效时的拆解图,从图中可以看出,隔膜、正极和负极均断裂,且裂痕是沿着内芯卷绕方向的一条直线。第四阶段为载荷上升阶段,此阶段电池内芯断裂部分已压实,内芯和钢外壳共同承受挤压载荷并快速上升。
此外,对比图3(a)中力-电-热曲线可以看出,载荷下降、电压下降和温度上升几乎同时发生,电压下降主要是由于内芯各层发生断裂而导致正负极接触发生内短路,温度上升主要由于电池发生内短路产生的焦耳热。
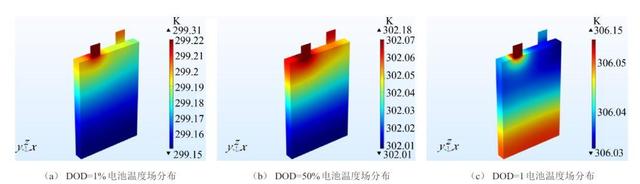
电池在局部压痕下,载荷下降、电压下降和温度升高有高度相关性,表明其机械和电化学性能存在密切联系。值得注意的是,图3(a)中温度仅上升至55.6℃,主要是因为电池发生内短路后,不会立即发生热失控反应,其热失控反应过程会随着时间而变化,在压头压缩至13mm时,内短路仅发生了13s,此时未发生明显热失控现象。
针对这一现象,本文详细分析电池内短路后温度的变化规律,图4(a)为Group1-Test1组电池表面最高温度随着时间的变化曲线;图4(b)为压痕后的结果,可以看出电池发生了剧烈热失控现象,且压痕附近出现了大量灼烧痕迹。
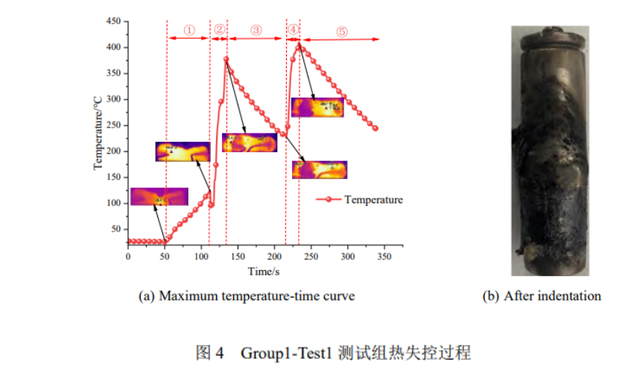
本文根据电池失效后温度变化的特征,并结合图4(a)中电池表面最高温度-时间变化曲线与图5所示电池表面热成像图,将其分为5个阶段。
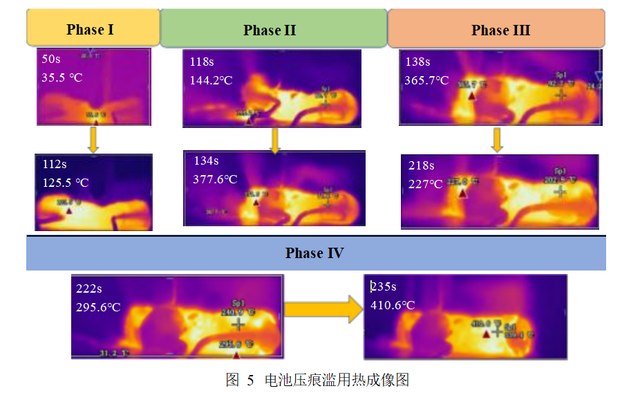
第一阶段是温度缓慢上升阶段,根据图5可知,在50s时压痕位置所对应的电池底部一侧最先短路,由内短路产生的焦耳热提供热量,热量从短路处向整个电池单体扩散,此阶段电池最高温度上升了100℃左右,且最高温度出现在压痕附近并达到了125.5℃,没有发生明显的热失控现象;
第二阶段是电池热失控发生阶段,此阶段在短路后65s左右发生且会持续20s,热量主要由热失控副反应所产生,电池表面最高温度上升了252.1℃,从图5可以看出,电池最高温度达到377.6℃,且最高温度出现在电池正极一侧,热量逐渐积累,从电池的正极安全阀会持续喷出大量刺鼻性白烟,并伴随剧烈的爆炸声;
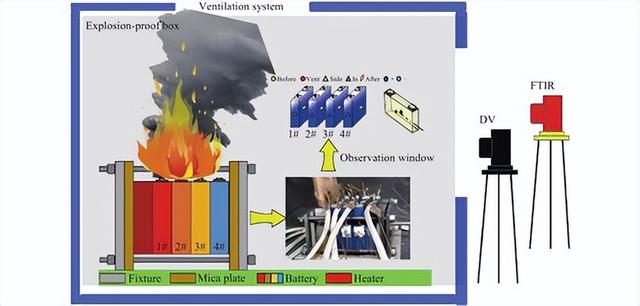
第三阶段是电池散热阶段,电池安全阀打开后释放热量,从图5可以看出,第三阶段时正极一端温度从365.7℃下降至227℃;
第四阶段,经第三阶段散热后电池内部的热失控副反应并未完全结束,电池表面温度再次急剧升高,由图5可以发现,阶段三正极端散热的同时,此时由于热失控反应并没有结束,负极端的温度在持续上升,当负极端温度高于正极端温度时,电池表面最高温度出现在了负极端,并且由于热失控反应,温度持续上升;
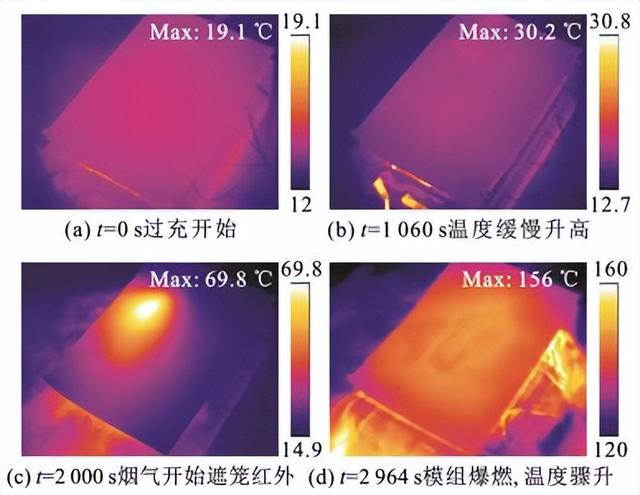
第五阶段为热失控反应结束阶段,此阶段电池的热失控反应已经完全结束,电池温度会随着时间呈下降趋势。
压头加载速度和SOC对锂电池安全性能的影响
图6为电池在Group2-Test2组下的实验结果。结合曲线分析发现,电池所承受的极限载荷和最高温度等参数与SOC有密切的联系,下面将分析SOC对电池安全性能的影响。
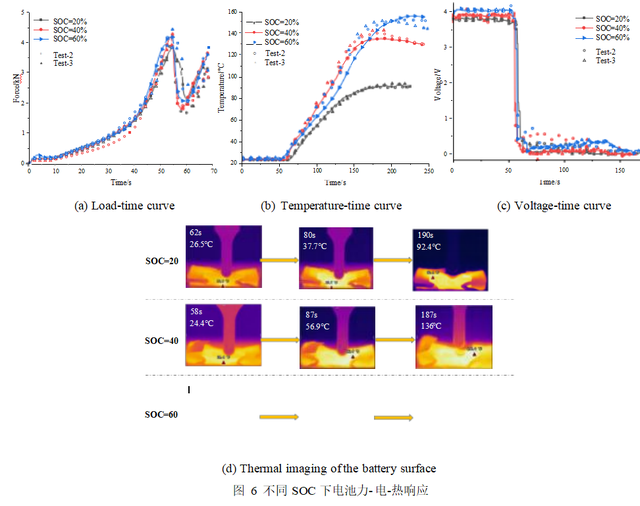
图6(a)为不同SOC下电池时间-载荷曲线。结果表明,在局部压痕下SOC对于电池的机械性能有一定影响,电池的极限承载力会随着SOC的增加而增大,SOC=60%比SOC=20%时的极限载荷大7.3%,而SOC对载荷下降点的影响并不明显。上述行为的主要原因是由于锂离子嵌入,在较高SOC中负极颗粒层更加致密,导致电池承受载荷的能力增强。
图6(c)为不同SOC下电池的时间-电压曲线。压降点能够直观的反应电池的内短路失效,在本文中压降点定义为电池的端电压发生骤降时的时间点。
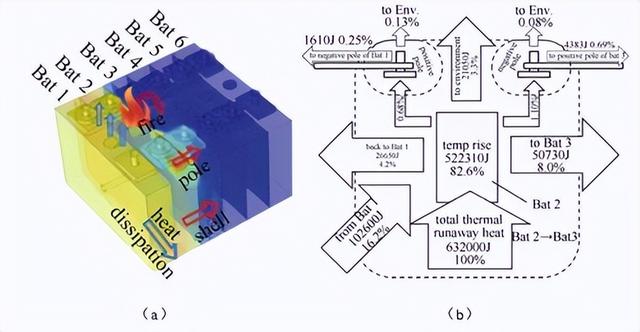
在压痕滥用下,电池SOC对其失效点有一定影响,随着SOC的增大,电压的下降点会提前,电池更容易失效,但在本实验中,SOC对电压下降点的影响不大。
图6(b)为不同SOC下电池的时间-温度曲线。结果表明电池SOC对温度有较大影响,电池的最高温度随着SOC的增大而增大,当SOC=60%时最高温度达到157℃,SOC=20%时最高温度为92℃。
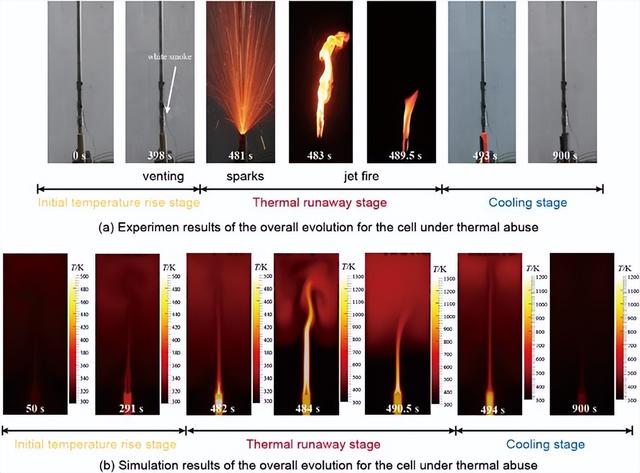
图6(d)为电池在不同SOC下温度热成像演变图,在SOC=20%和40%时并未有明显热失控现象发生(爆炸,白烟等),而SOC=60%时发生了明显的热失控现象,电池发出爆鸣声,并伴随从正极安全阀喷出白色浓烟,温度急剧上升。
图7为电池在Group2-Test3组下的实验结果。分别采用2mm/min、10mm/min和20mm/min的加载速度进行压痕实验,研究压头加载速度对电池安全性能的影响,实验参数信息列于表2。
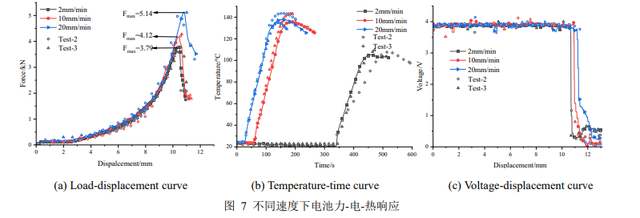
图7(a)为电池在不同加载速度下的载荷-位移曲线。观察实验曲线可以发现,变形量达到9.6mm之前,载荷-位移曲线重合度高,但电池所承受的极限载荷会随着速度的增加而增加。加载速度从2mm/min提升到20mm/min时,极限载荷提升了35.6%。
图7(c)为电池在不同加载速度下的电压-位移曲线,对比图中曲线可以看出,加载速度越高,电池发生短路时对应的变形量越大。由于电池的结构刚度会随着应变率的增加而增加,当电池受到较大的加载速度时,电池所承受到的极限载荷会增加,而在短路之前电池所受的载荷曲线有较高的重合度,所以电池失效时对应的变形量会变大。
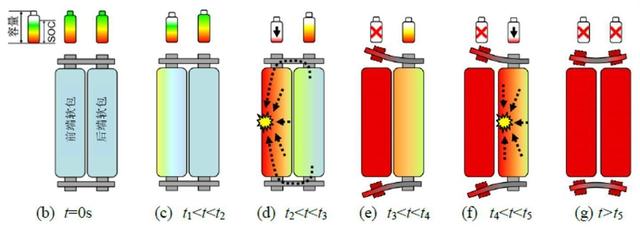
图7(b)为电池在不同加载速度下的温度-时间曲线,结果表明速度和电池温度也有一定联系,速度越大电池失效后达到的温度越高,电池内部反应更加剧烈。
综上分析,SOC和加载速度对锂电池力-电-热响应有一定的影响,但SOC与加载速度对其影响程度有所差异。其中SOC主要对电池的温度以及热失控反应的剧烈程度有较大影响,而对其力学响应的影响不大;速度对电池的极限载荷和压降点的大小有较大影响,和SOC相比,速度对热失控反应的影响有限。
压痕位置对锂电池安全性能的影响
为了探究不同压痕位置对锂电池安全性能的影响,本文设计了Group3-Test4测试实验。如图8(a)所示,压痕位置选取为距离负极10mm、20mm、30mm、45mm和55mm,其他实验参数列于表2,每组实验至少重复三次,图9为锂电池在不同压痕位置下的力-电-热响应。
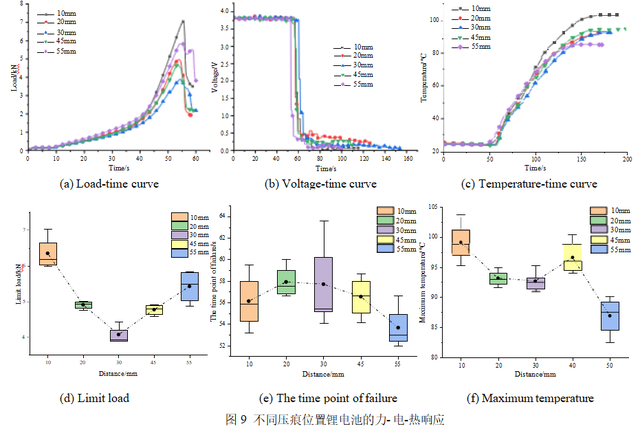
图9(a)为锂电池在不同压痕位置下的力学响应,结果表明在加载前期,电池的载荷曲线重合度较高;加载时间在45s(变形量7.5mm)之后,压痕位置会对力学响应产生较大的影响,压痕位置在10mm和55mm时的极限载荷远大于30mm、20mm和45mm处的极限载荷,20mm和45mm处的极限载荷大于30mm处,且压痕位置靠近电池两端时,载荷的上升斜率也较大。
图9(d)为多组实验在不同压痕位置下的电池极限载荷箱线图,从图中数据分布可以看出压痕位置对电池极限载荷的影响有明显的规律性,压痕位置越接近电池轴向中心,其极限载荷越小,反之,则极限载荷越大。
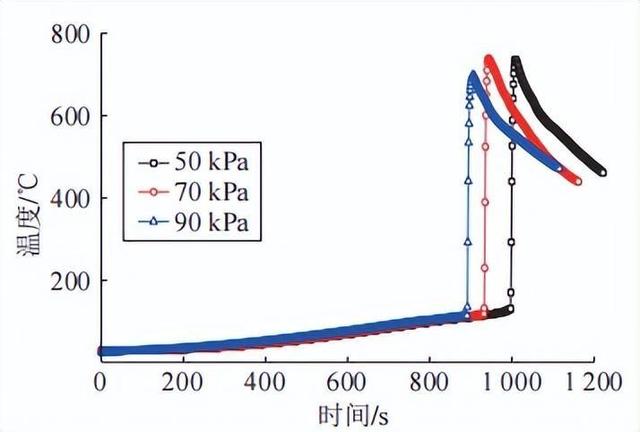
图9(b)为锂电池在不同压痕位置下的电学响应,从图中可以看出电池在压痕位置为55mm(距离正极10mm)时最先短路失效,而压痕位置在30mm时最晚发生短路失效。这主要由电池的内部结构决定,如图8(b)所示,电池长度为65mm,内芯长度为60mm,由于内芯与电池负极端紧贴,所以内芯与正极端存在5mm左右的间隙,压头半径为5mm,压头位置正好在内芯的顶端,而内芯顶端和正极一端存在间隙,这导致在加载过程中会产生有限的滑移和应力集中,在相同的变形量下,局部应变会更大,更容易导致隔膜失效,内短路的发生也会提前。
同理,在相同的变形量下,压痕位置在电池正中间时局部应变会更小,所以内短路会较晚发生。
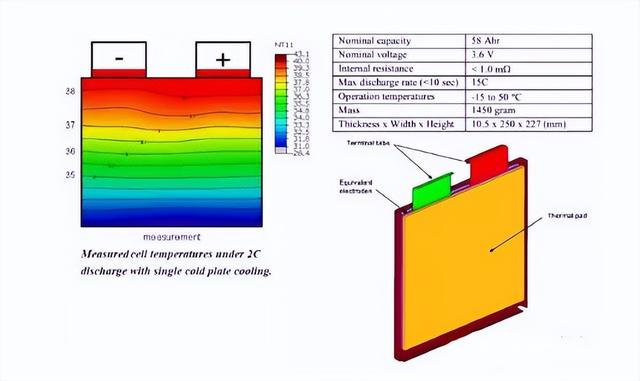
图9(e)为多组实验在不同压痕位置下电池失效时间点的分布箱线图,实验结果表明,压痕位置在接近电池正极一端时更容易发生短路。
图9(c)为不同压痕位置下锂电池的温度特征,可以看出压痕位置对电池的温度会产生一定影响,在压痕位置为10mm时电池的最高温度可以达到104℃,而压痕位置在55mm时最高温度仅为86℃,主要由于压痕位置为55mm时,内芯可能会发生滑移,导致内部断裂程度较小,所以由内短路产生的热量最小。
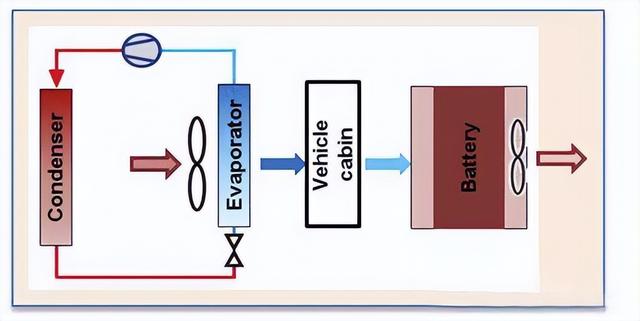
图9(f)所示为多组实验在不同压痕位置的电池最高温度箱线图,可以验证上述规律的正确性,压痕位置距离电池正极端10mm时,温度较低;而压痕位置接近负极端时,温度较高,容易引起热失控现象的发生。
图10是不同压痕位置下锂电池的热成像图,在SOC=20%时,压痕位置靠近负极时电池表面温度最高,而在压痕位置接近正极时温度最低,且未发生热失控现象;
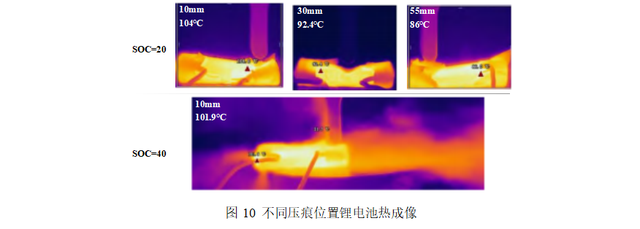
在SOC=40%时,压痕位置距离负极10mm时,引发了热失控现象,从正极安全阀喷出白烟,而在图6(d)中可以看出压痕位置距离负极端30mm时并未发生明显的热失控。
压头尺寸对锂电池安全性能的影响
为了探究压头尺寸对锂电池安全性能的影响,设计了Group4-Test5组实验。
图2(b)为三种不同尺寸压头,半径分别为5mm、7.5mm和10mm。Group4-Test5组分别在SOC=20%、40%和60%时,做三种尺寸下的压痕实验,压痕位置始终距离负极30mm,且加载速度设置为10mm/min。
图11为Group4-Test5实验测试组在SOC=20%下的力-电-热响应结果,不同压头的尺寸对锂电池的力-电-热响应有一定的影响,下面将详细分析压头尺寸对锂电池安全性能的影响。
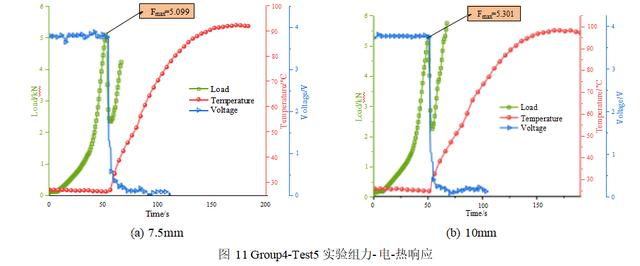
图12(a)所示为锂电池在SOC=20%、40%和60%下不同尺寸压头的极限载荷箱线图。
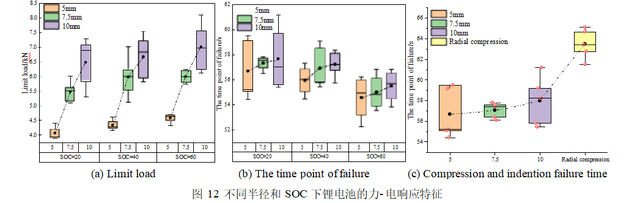
实验结果表明,电池极限载荷会随着压头尺寸的增加而增大,且在不同SOC下都表现出了一致性。在电池SOC=20%情况下,压头半径为5mm时电池平均极限载荷F1=4.069kN,半径为10mm时电池平均极限载荷F2=6.4822kN,从5mm增加到10mm,电池的平均极限载荷提升了59.3%;类似的,在SOC=40%下,电池平均极限载荷提升了53.4%;在SOC=60%下,电池平均极限载荷提升了52.9%。
其中SOC和压头半径对电池极限载荷的耦合影响中,压头尺寸占主导地位。从机理分析来看,SOC导致极限载荷升高的原因是较高SOC中负极颗粒层更加致密,导致电池承受载荷的能力增强;而压头尺寸导致极限载荷升高的原因是直接改变压头和电池的接触面积,和面积相比载荷受负极颗粒层的致密性影响较小。
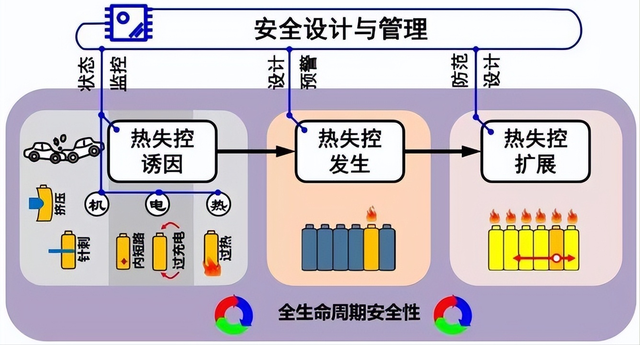
图12(b)所示为锂电池在SOC=20%、40%和60%下不同尺寸压头的失效时间点。实验结果表明,压头尺寸对于电池的压降点/失效时间点的影响有限。
在多次重复实验中,电池的平均压降点会随着压头尺寸的增加而增大。电池的压降点随着压头尺寸大小呈规律性变化,其主要原因是在相同的变形下,尺寸较小的压头与电池接触的面积小,更容易发生应力集中,导致隔膜容易失效,进而引起电池内短路。
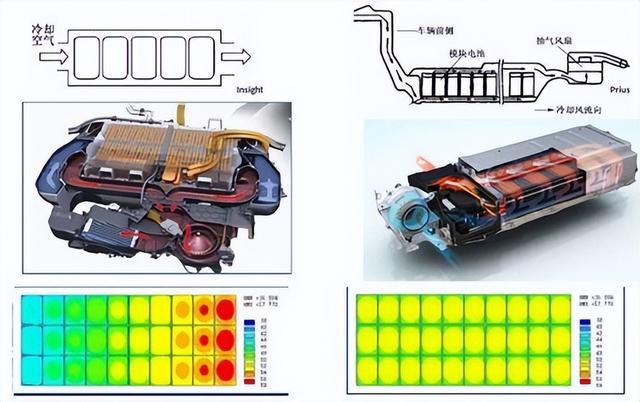
本实验中由于实验中压头尺寸较为接近,压头与电池接触的面积相差不大,导致在三种压头下电池的失效时间较为接近,实验数据呈现的规律性并不明显。
为了进一步证明上述分析,我们设置了5组径向平面压缩实验,设置电池SOC=20%,压头加载速度为10mm/min。
图12(c)为局部压痕和径向平面压缩短路失效点对比,平面压缩时的平均压降点比半径5mm压头时增加了7.8s。从平面压缩的失效机理来看,由于电池被整体挤压,电池内部的正负极材料扭曲变形,在整体挤压时由于整体受力均匀以及隔膜的延展性,隔膜被挤压后不容易断裂,最终电池失效是内部材料由于损伤不断累积,内部发生了短路失效。
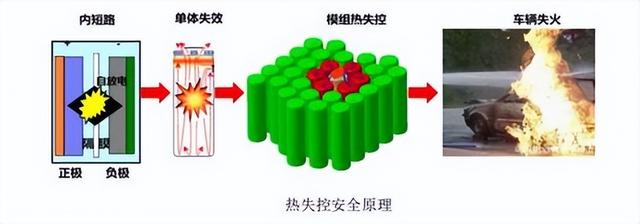
而局部压痕下压头和电池表面接触的面积小,内部的电极材料和隔膜更容易发生应力集中被破坏断裂,电压也更早的下降到0,这进一步印证了影响电池失效时间点的主要原因是压头和电池接触的面积不同。
图13为电池在不同半径和SOC下的温度特征,图13(a)为SOC=20%和40%下不同半径的时间温度曲线,从图中可以看出在相同SOC下,温度随着压头半径的增加而增大。
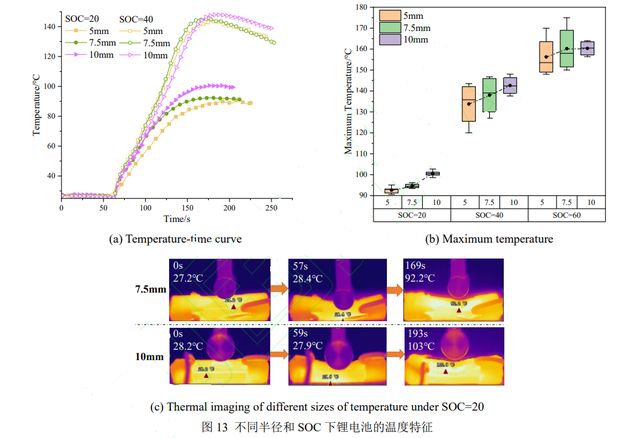
在SOC=20%时,压头半径在5mm下,电池最高温度达到92℃,压头半径为10mm时,电池的最高温度达到了103℃,主要由于压头和电池的接触面积变大,内短路的区域变大,最终导致电池的温度也较高。
图13(b)为多组实验在不同压头半径下的电池最高温度箱线图,在相同SOC下电池的平均最高温度会随着半径的增加而增加。
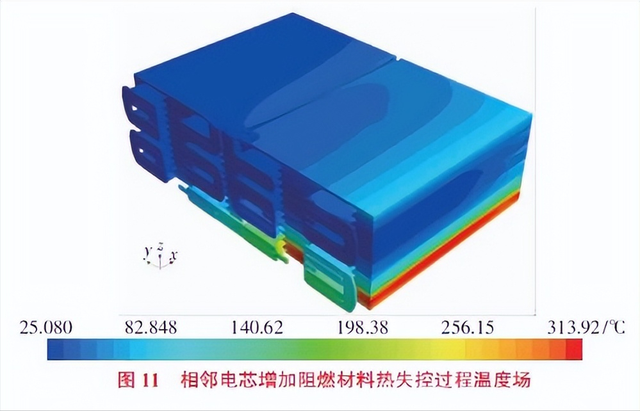
图13(c)为SOC=20%时,不同压头尺寸的电池热成像图。从图中可以看到,压头半径在7.5mm下,57s时电池局部温度升高,此时发生内短路,在169s达到最高温度;压头半径在10mm下,59s时电池内短路,193s达到最高温度,电池达到最高温度的时间也会随着压头半径的增加而增加。
其中,在SOC和压头半径对电池温度的耦合影响中,SOC对电池温度影响占主导作用,而压头尺寸对温度的影响则非常有限。从机理分析来看,SOC越高会导致正负极材料的反应活性变高,会引发更剧烈的热失控副反应,导致温度升高;压头尺寸越高则是导致压头和电池的接触面积变大,导致短路区域增大,进而使得温度升高,和正负极材料的活性相比短路区域的面积对温度的影响较小。
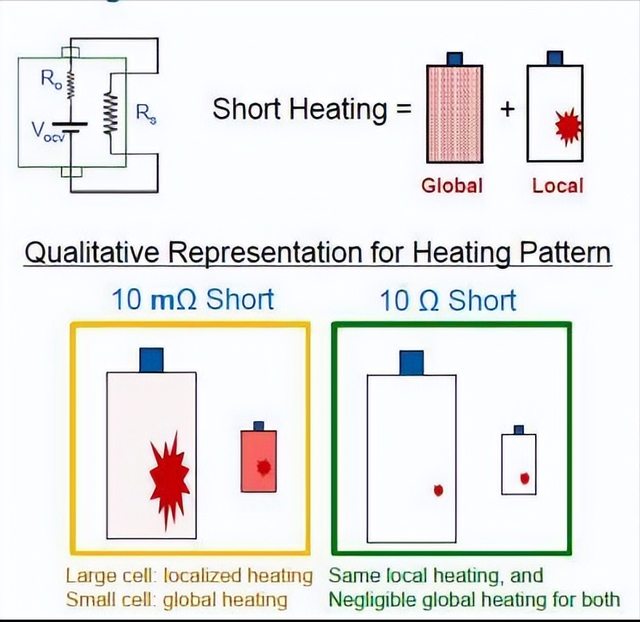
综合上述分析,压头尺寸对电池力-电-热响应影响的主要原因是压头和电池之间接触面积的变化。
压头尺寸对电池的力学响应有较大影响,压头半径增加5mm,电池的平均极限载荷会增加50%~60%;而压头尺寸对电池的电-热响应影响不大,压头半径增加5mm,电池的平均失效时间仅增加了1~2s,平均最高温度增加了6~10℃。
在SOC和压头尺寸对电池力-热-电响应的耦合作用中,电池的力学响应主要取决于压头尺寸,而SOC的影响较小;电池的温度响应主要取决于SOC,压头半径对温度的影响非常有限。
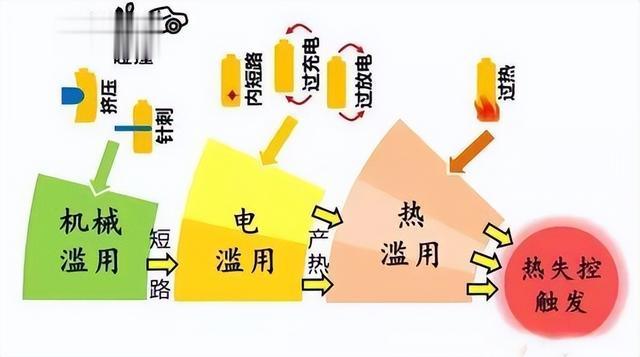
结语
通过实验发现,电池承受载荷下降、电压下降和温度上升的同时发生可作为判断局部压痕下电池是否失效的依据;在电池失效后,并不会立即发生热失控,存在一定的反应时间,短路失效后表现出明显的热失控演变规律,可为电池热失控预警系统的设计提供重要的参考价值。
在压痕工况下,电池热失控反应的剧烈程度主要随着SOC的增加而增加,而加载速度主要决定电池的失效时间与极限载荷,加载速度越快电池越快短路失效,并且SOC和其他参数相比,SOC是决定热失控反应剧烈程度的关键因素,SOC和加载速度可作为热失控预警算法设计的重要特征。
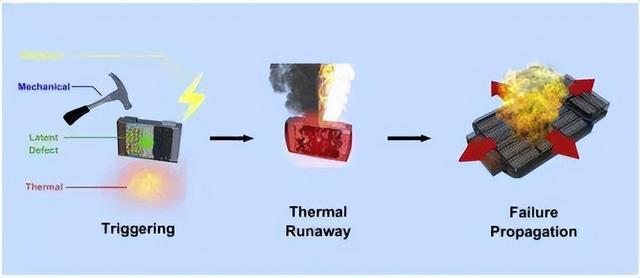
圆柱形锂电池靠近负极一端受到机械损伤时更易发生热失控等安全事故,并且电池受到机械损伤的面积较大时温度会更高,在实际电池包的防碰撞设计中应避免电池受到大面积机械损伤和负极一端的碰撞,这些实验数据为解决新能源汽车碰撞引发的热失控问题提供了新的思路和方法。