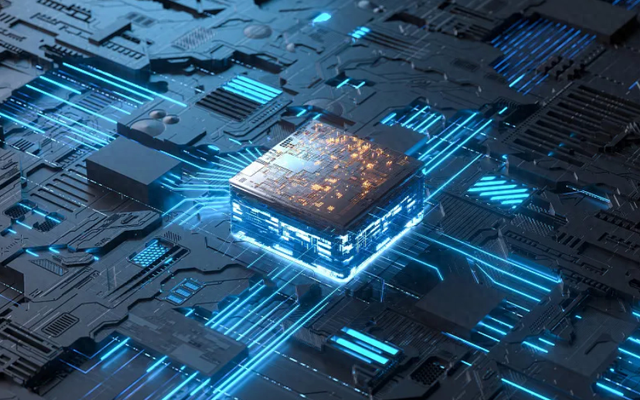
01晶圆键合发展背景
在摩尔定律的引导下,集成电路行业一直高速发展,晶体管特征尺寸已经从90nm向7nm迈进。然而,由于随着晶体管特征尺寸已日益接近物理极限,量子效应和短沟道效应越来越严重,内部电子自发地通过源极和漏极,导致漏电流增加,进而限制了晶体管的进一步缩小。因此,按照摩尔定律的方式,通过缩小晶体管特征尺寸来提升集成电路性能、降低功耗变得越发困难。晶体管将会快速地接近约5nm的极限栅极长度,因此探索新的沟道材料和器件结构是推动IC产业继续发展的两条极为重要的路线。
3D、晶圆级等先进封装是超越摩尔一个至关重要的研究应用方向。以3D集成封装为例,垂直于晶圆或芯片平面方向上进行堆叠,集成电路技术由二维平面向三维方向发展,该技术分段实现,首先实现几层的3D堆叠,随着时间的推移,堆叠芯片层数将会不断增加。采用全新结构的3D集成是推动半导体行业发展的重要技术,诸如存储器、逻辑器件、传感器和处理器等不同类型的器件和软件的复杂集成,以及新材料和先进的芯片堆叠技术,都要基于3D集成技术。另外,由于最新一代的光刻机的延迟交货和功率限制的综合影响,制造商无法进一步缩小器件尺寸,垂直堆叠芯片设备(含三维集成技术)正成为大势所趋。芯片堆叠封装存在着4项挑战,分别为晶圆级对准精度、键合完整性、晶圆减薄与均匀性控制以及层内(层间)互联。随着摩尔定律逼近材料与器件的物理极限,源于微机电系统(Micro Electro Mechanical Systems,MEMS)制造技术的晶圆级封装键合技术逐渐进入集成电路制造领域,成为实现存储器、逻辑器件、射频器件等部件的三维堆叠同质/异质集成,进而提升器件性能和功能,降低系统功耗、尺寸与制造成本的重要技术途径,对满足集成电路高集密度、高功能密度和高性能集成的迫切需求,突破国内自主可控平面集成能力不足的瓶颈,实现集成电路由平面集成向三维立体集成的跨越式发展有重要的战略价值。因此,英特尔、三星、华为、高通、罗姆、台积电等知名企业及众多高校、科研院所均围绕晶圆级封装键合开展了设备、器件、工艺的研究。键合(Bonding)属于后道封装过程,分为晶圆-晶圆键合(Wafer-to-Wafer,W2W)和芯片-晶圆键合(Die-to-Wafer,D2W)。键合主要指将两片表面清洁、原子级平整的同质或异质半导体材料经表面清洗和活化处理,在一定条件下直接结合,通过范德华力、分子力甚至原子力使两片半导体材料成为一体的技术。W2W 是指通过化学或物理反应将晶圆与晶圆、晶圆与玻璃基板或其他材料圆片永久结合起来的工艺。键合过程为,在外能量的作用下,两个晶圆接合界面上的原子相互反应形成共价键,从而使晶圆接合并达到一定的界面键合强度;D2W 指在划片工艺之后,将从晶圆上切割的芯片黏贴在封装基板(引线框架或印刷电路板)上。芯片键合工艺可分为传统和先进方法,传统方法采用芯片键合(Die Bonding)和引线键合(Wire Bonding),先进方法采用倒装芯片键合(Flip Chip Bonding)、混合键合(Hybrid Bonding)等技术。键合、解键合市场发展较晚,是从第二代半导体磷化铟、砷化镓开始发展的,最先开始使用键合/解键合的厂商是台湾稳懋,主要是做射频器件、光通器件及激光器件时,会用到薄化工艺,后来逐渐发展到先进封装层面,目前重点是台积电的应用为主。键合广泛应用在芯片的减薄工艺,追求芯片越来越小、效率越来越高、成本越来越低是各个芯片厂商追求的趋势。随着碳化硅产业的起步和发展,目前键合/解键合工艺涵盖了第一代、第二代、第三代半导体。晶圆键合(wafer bonding),从名字上就可以同传统封装中应用到的引线键合wire bonding和贴片键合die bonding所区分。bonding可以被翻译为接合,从直观印象上更方便于理解这一工艺和过程。从键合方式上来分类,晶圆键合可以分为永久键合和临时键合。区别也顾名思义,永久键合后无需再解键合(debonding),而临时键合还需要解键合,将接合在一起的晶圆重新打开。从界面材料来讲,分为带中间层的胶键合,共晶键合,金属热压键,无中间层的熔融键合(fusion bonding)和阳极键合等。以前晶圆键合业务主要面向封装领域的客户。如果一颗一颗晶圆去做封装,效率会很低,如果用整一个晶圆片去做封装,效率就会高很多。如今越来越多其他领域的公司也开始用键合技术。当芯片的集成度越来越高,成本也会越来越高。半导体产业的研发生产要同时兼顾技术和成本。如今各芯片企业不再追求更小的制程,而是将各种功能的芯片叠层起来,进行3D封装。实现3D封装的首要因素是晶圆片要薄,薄的晶圆可以更容易实现TSV穿孔工艺,而且如果芯片叠起来过厚就不利于用在终端设备中。因此目前行业内都在往50微米到100微米的级别靠拢,甚至有一些客户在往更薄的级别努力。一个50微米厚度的12吋晶圆片像纸一样薄,很难进行后续的光刻、湿制程等工艺,为了节省成本,各企业都希望不要更换现有的设备。这样就产生了临时键合的需求。我们用一个载片托住这片晶圆,做完减薄后仍然在这片晶圆上进行后续的所有工艺,最后再完整无损地将晶圆片和载片打开,清洗后就可以进行切片作业了。
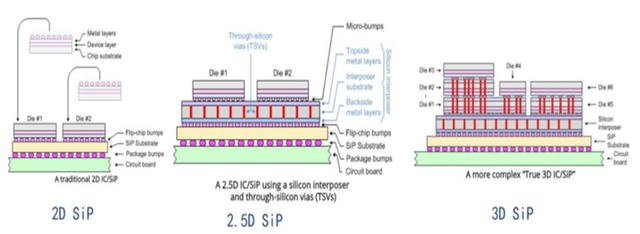
图1:2D、2.5D及3D封装之间的差距(来源日月光公开材料)
02晶圆键工艺过程(一)晶圆键合工艺过程及键合分类
如图2所示,晶圆键合工艺过程为:首先将待键合的一组晶圆进行预处理、清洗、视觉对准,进而通过不同方法实现晶圆对的键合。晶片接合后,界面的原子受到外力的作用而产生反应形成共价键结合成一体,并使接合界面达到特定的键合强度,称之为永久性键合。若借助粘结剂将晶片接合,也可作为临时键合,通过将器件晶圆固定在承载晶圆上,可为超薄器件晶圆提供足够的机械支撑,保证器件晶圆能够顺利安全地完成后续工艺制程,如光刻、刻蚀、钝化、溅射、电镀和回流焊。

图2:晶圆键合及后续工艺流程具体的晶圆键合工艺可按照键合材料、键合手段、应用场景分类,方法不尽相同,按照键合工艺对晶圆键合分类(见表1)。晶圆级键合是半导体器件物理、材料物理化学、精密机械设计、高精度自动控制等多学科交叉的科学技术领域。晶圆键合工艺中晶圆尺寸的扩大、芯片特征尺寸的缩小、异质材料之间的热失配及晶格失配等重要技术问题还有待解决。国外利用超高真空Ar快速原子束表面活化键合工艺实现了大面积、高强度的晶圆级键合,但我国在大面积、高强度晶圆级键合理论与工艺领域能力仍有待提高。晶圆键合及烘烤激活对晶圆表面温度均匀性及翘曲变形有十分严格的要求。温度均匀性取决于设备结构、加热工艺以及晶圆自身的热物理性能,翘曲变形则受温度均匀性、外加机械力以及晶圆自身力学性能的影响。传统的研究多采用实验试错的方法,没有将上述因素协同考虑,难以获得优化的结构工艺参数,导致键合可靠性及器件良率大大下降。国际上的高水平研究团队通常结合先进的数值仿真手段及多变量多目标优化方法,综合考虑包含热辐射、热传导在内的热场以及包含热应力、机械应力在内的应力场等多物理场之间的复杂耦合作用机理,开展对晶圆键合和烘烤激活工艺参数的协同优化,从而大大提高键合品质及器件良率。
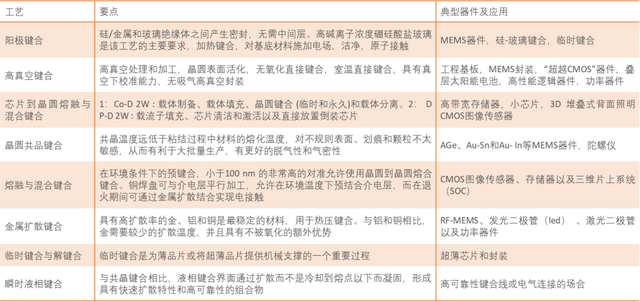
表1晶圆键合工艺分类及典型器件从界面材料来讲,晶圆键合又分为:(1)没有中间层的晶圆键合,包括融熔键合、铜-铜混合键合和阳极键合;(2)使用中间层的晶圆键合,中间层诸如玻璃浆料的绝缘体,或是在共晶键合和热压键合中采用的金属,包括胶键合、共晶键合、金属热压键合。如图3:
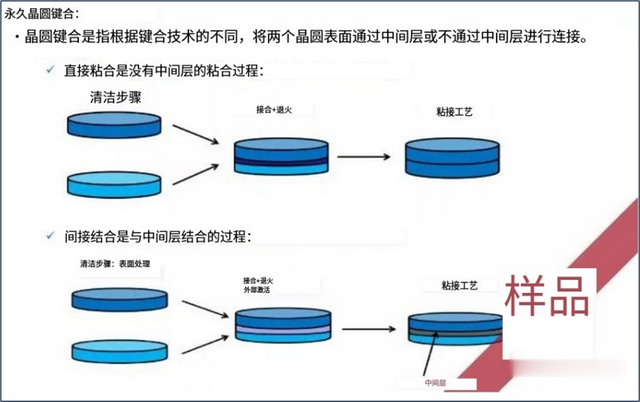
图3:根据界面材料的分类
1、键合条件
影响键合质量的内在因素是晶片表面的化学吸附状态、平整度及粗糙度;外在因素主要是键合的温度和时间。通常还需要加压来克服表面起伏与增加表面原子间的成键密度,来达到提高键合强度的目的。决定键合成功与否的基本条件:
(1)几何条件:利用键合技术可以有效解诀晶格失配的问题,要保证两个键合晶片的表面平整度与弹性模量的差异要小。(2)机械条件:键合所需的表面需要非常平滑,表面的粗糙度要求达到2nm以上,配合化学机械研磨(C雔}任)实现。(3)物理条件:由于磊晶或长晶的过程往往会有一些缺陷,如:晶界(grainboundaries) 大、晶格错位(dislocation)双尖峰(spikes)等,这些也需使用CMP的方式去除。(4)化学条件:两个欲键合表面的洁净度非常重要,键合时需注意去除表面金属、有机物等杂质。(5)能量条件:在热处理的过程中,温度可能会造成表面残余物质的化学反应,键合过程中引入热应力导致形变等对器件不利的结果。为了达到良好的键合质量,通常需要对欲键合的晶片进行前期准备,主要通过表面处理、预键合及热处理三个过程。2、键合界面的性质
(1)键合界面的位错和空洞。
除了硅硅直接键合这种同质材料键合之外,大部分都是通过异质材料进行键合。而由于两个键合的材料不同,晶片之间必然存在着热失配及晶格失配等问题。键合界面将会产生应力,为了应力弛豫,界面处会形成一定的位错,会严重影响器件的性能。此外,晶片表面会有一定的杂质、多孔层结构和空洞。这些杂质和多孔层结构的产生可能是由于表面未清洗洁净及界面附近的原子重组造成的,空洞是晶片在退火时产生的气泡引起的。(2)键合界面的电学和光学特性。键合晶片的界面状态会影响晶片的电学和光学性质,通过I-籚特性及PL谱等测试手段来分析界面处的键合情况,有助于更好的了解界面的性质变化,从而改进方法来提高界面的电学和光学性能。(3)键合界面的表面悬挂键和键合能。对于晶片来说,晶片内部与晶片表面的原子有不同的排列方式。当表面某处的原子排列出现中断时,表面处就会产生额外的能量此时中断处附近的原子如果仍以内部结构的形式排列,系统的自由能会明显增加。为了恢复稳定的排列方式,表面处的原子会进行一定的调整来降低附加的自由能。实现调整的方式主要有两种:通过晶片表面自行调整和借由外界条件调整。对于自行调整方式,由于晶片内部受力与晶片表面受力的情况显著不同,表面的晶格常数会随之发生改变。改变后晶片表面的原子与内部原子的排列形成不同的排列方式。如重构、台阶化等。以这种方式排列之后表面会形成本征表面态。通过外界条件的调整方式,晶片表面原子之间存在不饱和键,易吸附外来的杂质。吸附杂质的同时还进行电子交换,原有的表面太发生变化形成非本征表面态。通过以上两种调整方式都可以达到减低表面能的目的,从而使晶片内外系统达到稳定。晶片的表面悬挂键越多,表面能越大,键合时两个晶片之间的原子越容易相互作用。而键合界面处随着原子的不断相互作用形成越来越多的共价键,键合晶片的界面越牢固,键合强度越大。3、晶圆键合的难度
3D堆叠、晶圆级等先进封装方案可以采用多种形式,具体取决于所需的互连密度。图像传感器和高密度存储器可能需要将一个芯片直接堆叠在另一个芯片上,并通过硅通孔连接,而系统级封装设计可能会将多个传感器及其控制逻辑放在一个重新分配的层上。对于设计师来说,关键问题不是如何物理地包含单个模块,而是如何集成一个复杂的系统。尽管如此,从相对低密度的扇出型晶圆级封装到高密度芯片堆叠的所有形式的三维集成都存在一些具有挑战性的组装问题。
首先,为了确保一致的机械和电气连接,并方便进行任何进一步的光刻步骤,应将复杂堆叠中的每个晶片和每个重新分布层或其他元素平面化。这可以通过抛光、在现有形貌的顶部沉积电介质或键合胶或同时在两者之上实现。其次,硅、金属互连以及诸如键合胶之类的辅助材料可能具有非常不同的热膨胀系数。组装过程必须控制应力和翘曲,以确保最终封装中的可靠连接。例如,封装设计可能包含可适应工艺引起的应力的顺应性材料。或者,它可以通过限制高温处理来减少应力。例如,与需要高温的键合胶相比,可以在室温下施加和固化的键合胶对系统的应力较小。最后,组装涉及单个晶片、由单个晶片重构的晶片以及带有暴露的硅通孔的薄晶片的精确处理和对准。处理步骤可能涉及晶片的正面和背面。例如,在完整的封装中,芯片可能会停留在TSV的顶部并通过TSV连接到再分布层,而有源层会面对面或面对面地结合到另一个芯片。确切的工艺步骤各不相同,但是通常必须将晶圆临时键合到一个或多个临时载体衬底上,后面再解离,晶圆的翻转很常见。在将晶片转移到背面接触的载体上以进行进一步的正面处理之前,正面接触载体的晶圆允许减薄和其他背面处理。(二)临时键合与键合工艺晶圆键合是指通过一系列物理过程将两个或多个基板或晶片相互连接和化学过程。晶片键合用于各种技术,包括MEMS器件制造、三维集成封装等先进的封装技术,以及IC制造环节,在晶圆键合中有两种主要的键合,临时键合和永久键合,两者都是在促进三维集成的技术中发挥着关键作用。随着半导体晶圆制程对缩小特征尺寸和引入全尺寸三维集成需求的高涨,晶圆正朝着大尺寸、多芯片堆叠和超薄化方向发展,以实现高端芯片的高性能系统集成、多功能化和成本效益。晶圆减薄(低于100 μm)的目的主要是为了满足TSV制造和多片晶圆堆叠键合总厚度受限的需求。采用大尺寸晶圆能够有效提高芯片制造的效率和成本效益。然而,大尺寸薄化晶圆的柔性和易脆性使其很容易发生翘曲和破损。为降低减薄工艺中的碎片率,提高芯片制造的良率、加工精度和封装精度,通常采用临时键合及解键合(Temporary Bonding and De-bonding)技术,在背面减薄前,采用临时键合的方式将晶圆转移到载片上为其提供强度支撑,完成背面减薄及其他双面工艺后进行解键合。该技术在硅基TSV 互连工艺和3D 堆叠集成封装领域应用广泛。1、临时键合及解键合原理
晶圆与键合载片键合后,键合载片可以为晶圆提供机械支撑;在减薄抛光工艺完成后,通过解键合将晶圆与键合载片分离,该过程称为临时键合及解键合技术。采用热压临时键合,首先要使得键合介质(液态蜡或者液态胶)通过旋涂或喷涂方式在晶圆和载片表面均匀涂覆,然后在高温、真空、外力的键合腔室内叠放完成键合。键合层要牢固可靠,不允许有分离、松动、气泡、镂空等现象存在。
解键合技术根据不同的键合介质,划分为UV光照射(适配UV 干膜)、机械剥离(适配垂直剥离胶)、激光剥离(适配光敏胶)和热解滑移(适配热熔胶)4 种类型。UV 光照射解键合、机械剥离解键合、激光剥离解键合会产生较大的作用力和污染,不适用于软脆易碎的InP 晶圆。而热解滑移解键合原理是将晶圆吸附在解键合载片上,使用可加热真空工作台加热并吸附载片与晶圆,通过温度调节键合介质黏稠度的同时将键合载片延水平方向滑移出晶圆。较适用于脆性的InP 晶圆。2、临时键合工艺技术
临时键合主要包括3 个步骤:键合介质涂覆、前烘固化、晶圆与键合载片对准,以及真空热压。
如图4(a)、(b)所示,在临时键合工艺过程中,常见的技术要点是排除键合层的中心及边缘产生气泡。该气泡引起的键合层厚度不均匀或镂空现象直接导致该区域在减薄时因局部失去支撑而碎裂;或因边缘键合层密封不足,使减薄废料渗入,导致晶圆表面沾污无法祛除。所以如何优化键合工艺,避免气泡的出现是该步骤最大的难点所在。首先,涂覆键合介质时,先低转速匀开静置,目的是让肉眼可见的气泡自然破裂,然后再高速旋开,从而制备满足一定厚度且均匀的键合介质层;其次,在前烘固化时应提供一定负压的真空,目的是让肉眼不可见的气泡通过真空利用气压差使其破裂避免在烘烤时鼓包,特别注意的是,该负压不能过强,否则键合介质中大量的挥发性稀释剂会剧烈挥发产生更多更大的泡沫组织,如图4 (c)所示;最后,在真空热压过程中,需要通过调节工艺过程中“温度—真空—压力”3 个共同作用,诱导空隙气泡移动到晶圆边缘排除。温度过低,蜡层黏稠度大流动性差,气泡空隙无法移动到晶圆边缘顺利排除;温度过高,蜡层黏稠度低流动性佳,蜡层在压力作用下挤压溢出,导致厚度偏薄,甚至载片会因为蜡层过薄压坏晶圆表面仅仅几微米的芯片。如图4(d)所示,通过工艺参数的优化,以某型号带铟凸点的InGaAs 焦平面探测器为例,成功实现了100 mm InP 晶圆的临时键合,并且键合层组织致密,无气泡。
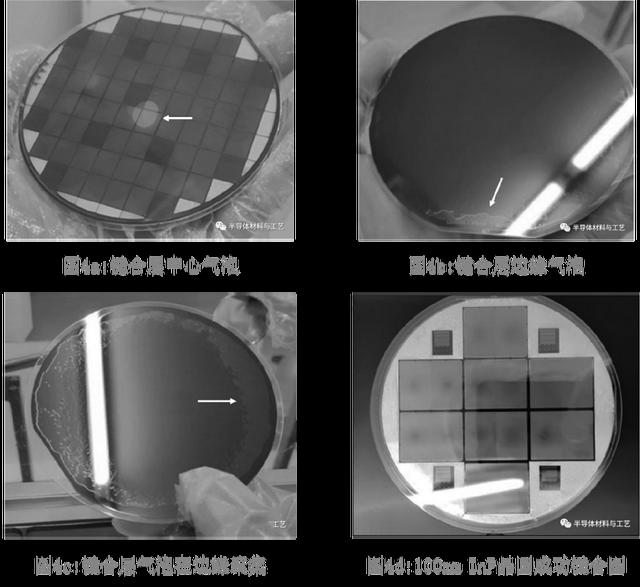
图4:键合层中心和边缘出现气泡其另一技术要点是控制键合片的翘曲度(WARP)。翘曲度过大会严重影响减薄过程中的全局平坦化工艺效果,也会导致解键合过程因受力不均产生更大的碎裂风险。影响翘曲度WARP的主要因素有3 点:(1)晶圆与键合载片各自的热膨胀系数及相互匹配;(2)晶圆及键合载片本身的厚度和形貌等输入状态;(3) 键合工艺技术调节3、解键合工艺技术
解键合是在减薄抛光完成后,将晶圆与载片分开的技术。解键合是按照翘曲矫正、热解滑移和晶圆清洗3 个过程进行的。在临时键合后,键合片往往会经过背面减薄抛光或者镀膜等工艺。这些工艺不仅使得晶圆厚度降低至100 μm 左右,还会引入机械应力和热应力,使得晶圆发生严重翘曲。所以,在解键合前,必须对薄片晶圆进行翘曲矫正,否则在后续升温和滑移解键合时,都会因为形变过大、受力不均导致晶圆损伤、碎裂。
根据解键合方式的不同,解键合方式主要分为机械剥离、湿化学浸泡、热滑移和激光解键合4种方法,这几种方法均有各自的优缺点,图表2。随着键合技术的不断进步,其将成为推动晶圆级先进封装技术不断发展的重要组成部分。
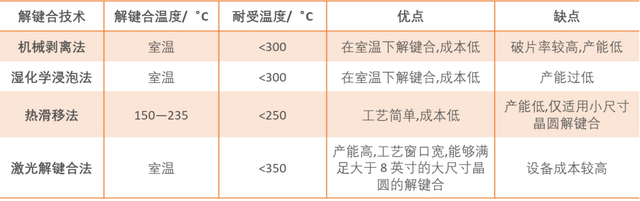
(1)机械剥离法对于不能承受高温和高热应力的器件晶圆,在室温下即可实现键合对的机械剥离方法是一种低成本的解决方案。机械剥离法的基本流程如图1所示。机械剥离法相对简单粗暴,将薄片插入载板与器件晶圆中间,通过向上的拉力和旋转的剪切力剥离载板。超薄器件晶圆采用该方法会因为过大的机械应力而出现较高的破片率。道康宁公司开发了一种耐腐蚀的硅基临时键合材料,用于机械解键合工艺。由于键合对分离之后还需要大量清洗剂去除器件表面残胶,这会产生额外的成本。为了实现无溶剂分离,比利时微电子研究中心(IMEC)开发了一种可以从薄晶圆上直接揭除键合胶的纯机械剥离方法,从而极大地减少了清洗剂的使用。此外,在机械剥离之前通常先将键合对转移到切割胶带上以降低薄晶圆破损的风险。通过配套的专用机械解键合设备甚至能够实现12英寸极薄(厚度为5.6 μm)晶圆的剥离。然而,这种专用机械解键合设备的高成本限制了其应用。
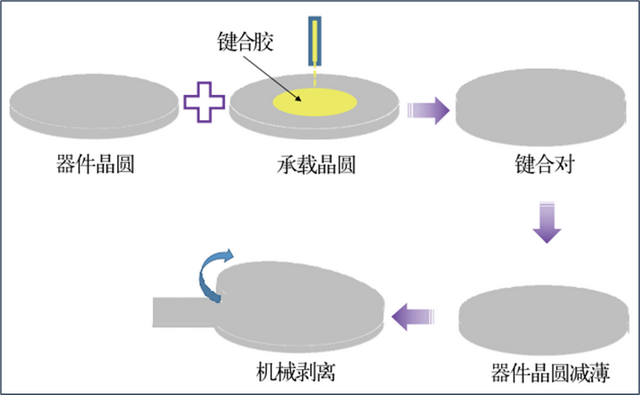
图5:机械剥离法流程(2)湿化学浸泡法根据临时键合胶在特定溶剂中的溶解特性,可以通过溶剂浸没去除键合胶层,直接分离器件晶圆,这种方法被称为湿化学浸泡法。湿化学浸泡法的基本流程如图6所示,主要包括以下3个步骤:(1)通过临时键合胶将带有通孔的承载晶圆与器件晶圆进行键合;(2)对器件晶圆进行减薄、研磨、重布线层(RDL)和球化等半导体制程工艺;(3)将键合对放置在装有溶剂的容器内,放置一段时间后键合胶逐渐溶解,从而实现器件晶圆的剥离。值得注意的是,需在承载晶圆上制造分布均匀的群孔以加快键合胶的溶解,同时尽量避免因溶解不均而导致的机械应力集中。
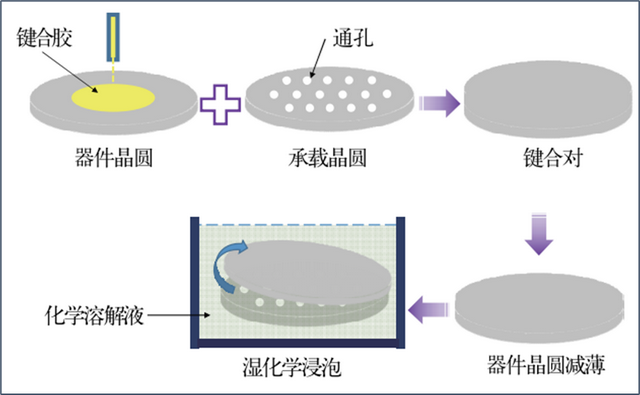
图6:湿化学浸泡法的基本流程(3)热滑移法热塑性材料在溶剂清洗过程中易于从器件晶圆上去除,其被认为是最适合用于临时键合胶的材料,且对器件晶圆表面的结构损伤较小。热滑移解键合的工艺流程如图7所示。热滑移法是将器件晶圆放置在真空吸附工作台上,采用可加热吸盘吸附载板,通过加热使键合胶材料软化,再施加剪切力使器件晶圆侧向滑移出载板。这种方法通常采用的临时键合材料的热稳定性较差,在晶圆级封装的高温制程中容易软化,会影响器件的加工精度和封装精度。此外,器件晶圆在滑移完成后很容易在设备平台上残留键合胶,影响后续的产品工艺。早在20世纪初,美国Brewer Science公司就开始研发适用于热滑移法的临时键合材料产品,其早期开发的WaferBond HT-10.10以及紫外激光解键合材料WaferBond 305与WaferBond 701长期占据国内主要市场,但这些材料仍然存在着耐化学腐蚀和耐高温性能较差等问题
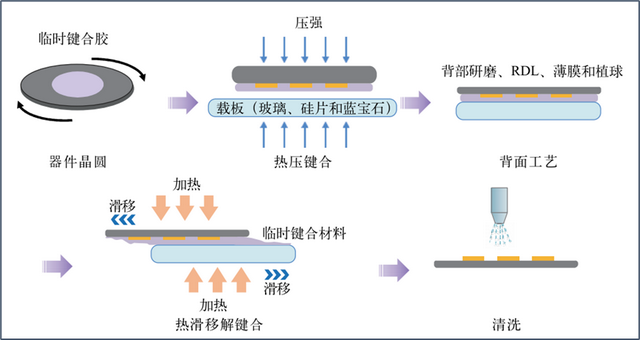
图7:热滑移解键合的工艺流程(4)激光解键合法激光解键合法是一种在室温下不使用化学物质的低应力剥离工艺。激光解键合法具有可在室温下解键合、高通量、低机械应力和环境友好等优点,在大尺寸超薄晶圆的制造方面逐渐得到了广泛的关注和应用,有望为高端超薄芯片制造过程中的易破损和吞吐量低等困境提供可行性解决方案。此外,激光在能量、时间、空间方面的可选择范围很宽,可形成超快、超强、超短等极端物理条件。鉴于激光解键合在高应力晶圆处理方面具有高度的灵活性,能够在传统的后端设备上进行先进的封装流程。例如,激光解键合的宽工艺窗口更适合应用于扇出型晶圆级封装(FOWLP)。另外,激光解键合工艺能够避免表面能、温度行为和溶剂渗透的依赖性,并与后续半导体制程工艺相兼容。目前,激光解键合法主要分为红外激光解键合法和紫外激光解键合法。激光解键合法的剥离机制主要依赖于激光种类以及响应材料的类型。激光解键合工艺主要是利用激光穿过透明载板,光子能量沉积在光敏响应材料层,进而诱发材料的快速分解、汽化甚至等离子化而失去粘性。同时,快速释放的分解气体还会增大响应层界面的分离压力,从而进一步促进器件晶圆的自动分离。激光解键合工艺的工作流程主要包括(图8 所示):(1)在透明刚性载板(如玻璃、蓝宝石等)和器件晶圆表面分别涂上粘结材料和响应材料;(2)将透明刚性载板和器件晶圆通过光或热等方式键合在一起;(3)利用激光透过刚性载板辐照在响应材料层引发烧蚀,从而使得器件晶圆分离;(4)清洗器件晶圆和透明刚性载板,其中的载板可以多次重复使用。
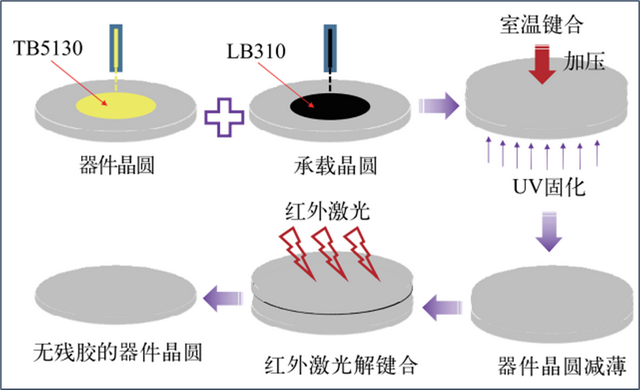
图8:红外激光解键合的工艺流程4、晶圆清洗工艺技术
在晶圆完成解键合后,均需要在超薄片状态下进行清洗,从而移除残余的键合介质。在该过程中,需要首先注意的是晶圆薄片的碎片率。由于超薄晶圆会在溶液冲洗和片盒上下过程中碎裂,无法使用常规的片盒式槽式清洗机。同时,也无法使用单片式晶圆清洗机,因为不论是机械手臂上下料还是清洗过程中的溶剂冲力都会造成晶圆碎裂。
03晶圆键合设备市场情况(一)晶圆键合设备市场现状及预测
晶圆键合设备领域目前正朝着多元化的方向发展。例如,随着技术的提高与更新,并且受益于地方政府的大力补贴,亚洲设备供应商对整个市场造成了巨大的价格压力,将来会进一步开拓市场并开始与顶级企业竞争,并可能重新洗牌晶圆键合设备设备市场。
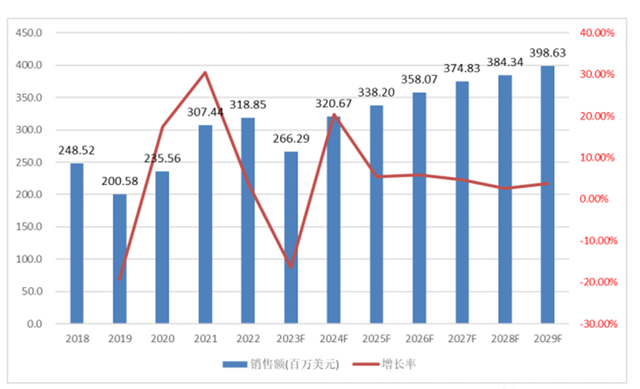
图9:全球晶圆键合设备消费额及发展趋势(2018-2029)(百万美金)资料来源:Yole Developpemen、第三方资料、新闻报道、业内专家采访及QYResearch 整理研究
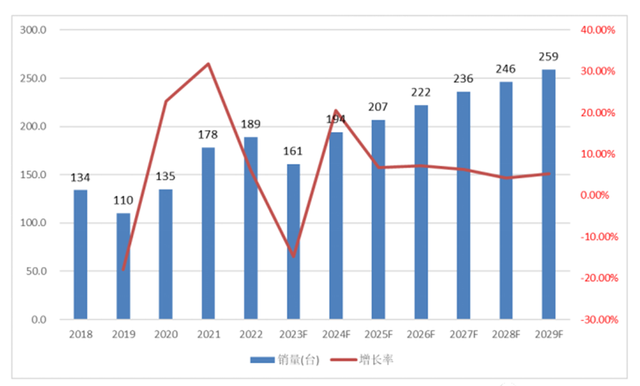
图10:全球晶圆键合设备销量及发展趋势(2018-2029)(台)
资料来源:Yole Developpemen、第三方资料、新闻报道、业内专家采访及QYResearch 整理研究根据上图数据显示,2022年全球晶圆键合设备行业市场总收入大约达到318.85百万美元,预测2029年有望达到398.63百万美元,2023到2029年的年均增长率为6.96%。全球晶圆键合设备消费市场主要集中在中国,日本,欧洲和美国等地区。其中中国半导体行业发展较快,晶圆键合设备销量份额最大,2022年占据全球的40%。日本占据5%,而欧洲和美国分别占有19%和11%。在下游消费市场中,晶圆键合设备可以广泛地应用于MEMS,先进封装,CIS和其他,其中MEMS市场是最大的消费市场,占有35%的市场。先进封装为第二大市场32%,CIS及其他应用则占有更小的市场。全球晶圆键合设备市场相对集中,国际市场上的主要生产商包括EV Group, SUSS MicroTec, Tokyo Electron, AML, Mitsubishi, AyumiIndustry, SMEE等,奥地利EV Group为全球龙头企业,2022年收入占据全球份额的59%。德国SUSSMicroTec为全球第二大企业,占据全球市场的12%。TokyoElectron, AML, Mitsubishi, Ayumi Industry, SMEE等一共占有将近29%的市场份额。(二)晶圆键合设备主要厂商情况以公开的2020年数据为例,全球晶圆键合设备主要厂商列表

图11:2020年公开数据,全球晶圆键合设备厂商经营情况奥地利EVG公司的主流产品,适合阳极键合、共晶键合、金属扩散键合、直接键合、聚合物键合、熔融与混合键合和瞬时液相键合的小批量、半自动晶圆键合解决方案,如EVG510、EVG520、E V G 5 4 0 晶圆键合系统;也可以提供全自动、大批量、满足3D异构集成高对准精度生产的晶圆键合解决方案,如EVG560、EVG GEMINI、EVGCombond、EVG Bondscale等晶圆键合系统;还有用于扇出封装、晶圆减薄、3D堆叠、晶圆键合的临时键合和晶圆解键合解决方案,如E V G 8 5 0 、EVG850TB、EVG850LT等晶圆临时键合与解键合系统;晶圆对准设备由Smartview发展到Smartview3,对准精度提高到50 nm。晶圆键合设备总体技术发展方向是高精度、高集成化、高可靠性、高动态、高效化的趋势,关键技术指标为:对准精度≤50 nm;键合温度均匀性≤±1%;最大晶圆尺寸304.8 mm(12英寸);最大键合压力100 kN;最高键合温度550 ℃。德国SUSS MicroTec拥有六十多年的历史,是半导体行业领先的微结构工艺设备制造商,产品涵盖光刻、涂胶/显影、晶圆键合、光刻掩膜版清洗等诸多半导体、微加工相关领域。SUSS晶圆键合系统主要包括XB8、SB6/8Gen2、XBS200、XBS300、XBC300Gen2等系统,最大晶圆尺寸304.8 mm(12英寸),对准精度≤500 nm,能够满足包括共晶、直接键合等各种晶圆键合工艺需求。国内设备起步晚,国内键合设备技术发展方向由手动向半自动转换,国内没有多模块集成的晶圆键合设备,与国外设备代差距较大。上海微电子装备(SMEE)有独立对准、键合、解键合等设备,SWB系列晶圆键合设备用于有机胶键合、玻璃浆料键合、共晶键合、阳极键合等工艺。SWA系列晶圆对准设备对准精度≤±2 μm。苏州美图开发的阳极晶圆键合设备,最大键合压力10~30 kN,最高温度450 ℃。中国电科2所研制真空晶圆键合系统对准精度≤1 μm,键合温度均匀性≤±1%(FS),设备达到国内先进水平(如图12所示)
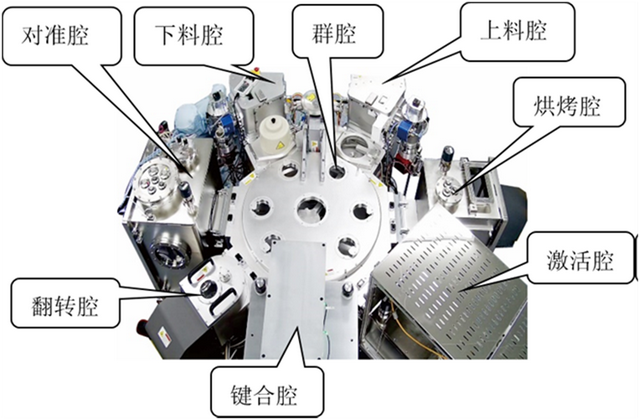
图12:全自动真空晶圆键合系统(三)国内晶圆键合设备研发进展情况
晶圆键合设备是进入壁垒很高的产业,对于光学系统、图像处理与识别、高精度晶圆平行移动等技术的要求极高。国内的众多设备厂家因自身的人才、技术、设备、材料和资金等各方面因素的制约,无力进行设备持续的研究和改进,与国外同行之间的技术和实力的差距有扩大的趋势,晶圆键合产品在技术性能、质量可靠性、稳定性等方面存在很大的不足。目前,国内晶圆级键合技术主要受限于国内器件设计与工艺、设备稳定性与精确度等领域的基础理论与关键技术的发展水平。
1、技术性能方面发展
目前国内生产的最好的设备对准精度为±2 μm,与国外设备差距较大,EVG对准精度≤50 nm。键合温度均匀性规格书≤±1%(FS),实际能达到≤±0.6%。目前在晶圆级封装行业内,临时键合技术的使用已经比较成熟,但都是厚度都在100μm以上的单层硅通孔(TSV)结构,受限于临时键合材料,暂不能做到更薄。临时键合稳定的另一面是解键合和清除残胶更加麻烦,需要更长时间去除残胶,键合的稳定和解键合残胶的易清洁之间的平衡,还需要更长时间去解决。国外设备自动化程度可满足大生产线需求,国内设备差距很大。
2、质量可靠性方面发展
国外设备键合热台使用寿命长、密封可靠性高,加压气液缸、检测传感器、卡盘等关键件可靠、耐用,设备一致性、长期使用稳定性好,加热台互换性良好。国内设备、键合加热台等部件一致性差,稳定性不好,缺乏关键零部件持续攻关及工艺深度结合。
3、研发模式及投入方面
我国设备行业与国外行业领军企业的研发模式有很大不同。以半导体装备龙头企业AMSL为例,在全球范围内与优势单位、头部企业合作,实现优势互补、强强联合,分布在全球的700多家供应商提供的功能模块和单元组件贡献了AMSL光刻设备约85%的外购成本。AMSL能专注于自身独特的能力优势,集成世界范围内最专业的制造商来设计、研发与制造光刻机,与比利时的IMEC光刻研究中心保持着长期合作关系,依靠强大的研发实力引领市场、开拓创新,拥有庞大且涉及多学科多领域的高科技研发团队,每年用于研发的费用数以亿计。自2015年以来,AMSL的研发人数占员工总数的比例一直维持在35%左右,研发人员逐年递增,2018年达8500多人。国内装备研制企业与零部件生产商配合不紧密,产学研合作脱节,研究方向不专注,高端人才缺乏,研发投入不够,缺乏长期战略投入,造成与国外高端核心装备的技术差距较大。
4、国内的相关厂商
(1)芯睿科技
苏州芯睿科技有限公司官网介绍:公司是一家专注于半导体晶圆键合设备研发、生产及销售的企业。通过十多年的研发,公司产品应用覆盖半导体各领域(包括射频器件、功率器件、先进封装、光通讯等),工艺能力覆盖2至12英寸,是临时键合、永久键合整体方案提供商。公司核心技术团队均有20年以上的半导体设备开发经验。根据公开信息显示,芯睿科技最新自主研发生产的12英寸临时键合设备可应用于Fan-out、2.5D、3D interposer等先进封装相关工艺。键合腔体采用高真空、高温和高压设计,及具有专利的腔内置中机构,使得置中精度能够达到≤50um。此外,该设备可以适应市场上各种临时键合材料,为客户提供多样性的选择。公司的12英寸激光解键合设备则搭载主流波段355nm固态激光源,并采用平顶光设计,避免单点能量过高对芯片造成损伤;光路的实时能量监控功能,确保工艺流程中激光能量的稳定性。此外,该设备腔体还配备载片分离模组,可以实现解键合后载片的自动分离。目前芯睿科技的永久键合设备有少量的订单,临时键合设备处于研发验证阶段。(2)华卓精科华卓精科以超精密测控技术为基础,研究、开发以及生产超精密测控设备部件、超精密测控设备整机并提供相关技术开发服务,其中报告期内的超精密测控设备部件产品包括精密运动系统、静电卡盘和隔振器等,整机产品包括晶圆级键合设备、激光退火设备等。上述产品的应用领域覆盖集成电路制造、超精密制造、光学、医疗、3C制造等行业。主要产品包括精密运动系统、静电卡盘和隔振器等超精密测控设备部件及晶圆级键合设备、激光退火设备等超精密测控设备整机,以及上述部分主要产品和纳米精度运动及测控系统的技术开发服务。其中,晶圆级键合设备、激光退火设备等产品均为国内前沿技术产品,技术构造复杂。根据华卓精科公开信息显示,目前键合设备方面主要有全自动化临时键合设备、混合键合设备,都以先进封装应用为主,但没有查到产品的具体导入应用信息。(3)拓荆科技拓荆科技主要从事高端半导体专用设备的研发、生产、销售和技术服务。公司主要产品为半导体薄膜沉积设备包括PECVD设备、ALD设备及SACVD设备三个系列。公司是国内唯一一家产业化应用的集成电路PECVD、SACVD设备厂商。先进封装方面,公司积极进军高端半导体设备的前沿技术领域,研制了应用于晶圆级三维集成领域的混合键合(Hybrid Bonding)设备产品系列,同时,该设备还能兼容熔融键合(Fusion Bonding)。公司混合键合系列产品包括晶圆对晶圆键合(Wafer to Wafer Bonding)产品和芯片对晶圆键合表面预处理(Die to Wafer Bonding Preparation and Activation)产品,可以实现直接或基于层间的键合工艺、复杂的常温共价键合工艺。根据公开信息,拓荆目前在研晶圆键合设备主要以混合键合设备为主,其首台Dione 300机型目前正在客户方验证。
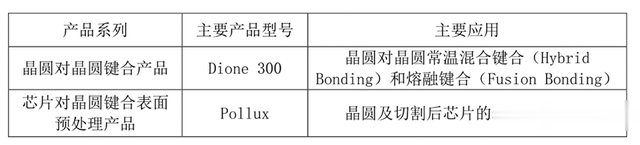
图13:拓荆公开信息相关在研晶圆键合设备型号(4)三河建华高科三河建华高科有限责任公司创建于2003年,公司位于河北省廊坊市,为中电45所旗下控股子公司。根据三河建华高科公开信息,其已成功研发了WB-1200自动晶圆键合机,该设备主要适用于 8″、12″基片的自动对准、晶圆级临时键合工艺。该设备采用全自动Robot上下基片,工艺过程连续处理,自动运行;设备操作方便、稳定性高、重复定位,并具有较高的性价比,可广泛应用于科研和生产。2023年11月公开成功签订一台设备订单,但并未查到具体订单信息,是否作为实验用,还是量产线用。(5)博纳半导体博纳半导体是2018年在上海成立,专注于晶圆键合设备的研发和生产。早期由头部封测企业发出设备需求,开始启动键合设备的研发。目前博纳半导体的晶圆键合设备主要包括:临时键合、临时解键合设备、临时解键合清洗一体机三款产品。临时解键合清洗一体机也是国内首创的解键合、清洗工艺融合一起的设备。根据公开信息,博纳半导体的临时键合设备以正式订单形式,已交付长电科技量产线,也是国内首台正式交付量产线的临时键合设备。(6)根据相关信息,除以上企业外,目前国内正在准备启动和在研发晶圆键合设备的企业方还有上海微电子、新汇联、晶盛半导体、江丰电子等企业,但到目前为止,还没有公开的渠道查到相关产品信息。