随着电气产品向密集化、小型化方向快速发展,表面贴装技术已成为印制电路板(PCB)组装的主流技术,因此通孔回流焊工艺的应用越来越广泛。南京南瑞继保电气有限公司鲍军云、王高垒、彭学军、李磊在2024年第4期《电气技术》上撰文,重点从锡膏选型、钢网开孔工艺优化、元器件性能、PCB焊盘设计优化等角度展开研究,并通过实际生产验证了通孔回流焊工艺能够拓展高密度、细间距产品的生产窗口,并解决了锡珠、空洞等焊接问题。该工艺能从多方面替代传统波峰焊工艺,可提升元器件的焊接质量,使焊接可靠性大大提高,为有效推进表贴化工艺、降低生产成本、提高生产效率提供支撑。
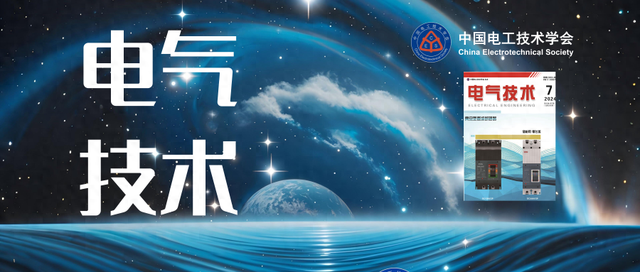
随着智能电网继电保护技术的快速推广,保护装置相关的电气产品朝着密集化、小型化方向快速发展,装置内部的电路板使用表贴元器件已成为主流趋势。大部分板卡特别是中央处理器(central processing unit, CPU)板卡实现了采用表面贴装技术(surface mount technology, SMT),但还有一些大功率元器件、连接端子等需要采用传统波峰焊工艺。
传统波峰焊工艺窗口受限多,如该工艺不适合高密度、细间距元器件焊装,焊接过程容易产生桥接、虚焊等质量问题,存在插装、焊接、修焊等复杂工序,导致产品加工周期长、生产效率低,因此传统波峰焊工艺对生产效率和产品质量的影响较大。
一方面通孔插装(through-hole technology, THT)元器件使用波峰焊工艺导致焊接质量一致性差,降低了焊接可靠性;另一方面使用波峰焊工艺焊接的通孔插装元器件数量少,却需要多道工序生产、多个设备和人员参与,大幅增加了生产成本,拉长了生产周期,降低了生产效率。
通孔回流焊(through-hole reflow solder, THR)工艺采用丝网印刷方式将锡膏印刷在通孔焊盘上,将插装元器件插入通孔内,再通过回流焊完成与表贴元器件的焊接。该工艺可减少波峰焊工序,缩短工艺流程,降低生产成本,从而解决焊接质量一致性差、生产效率低等问题。通孔回流焊工艺示意图如图1所示。
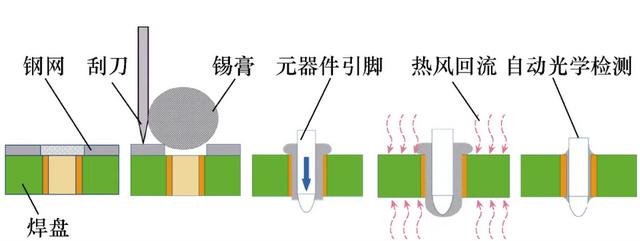
图1 通孔回流焊工艺示意图
1 通孔回流焊工艺与传统焊接工艺对比
1.1 通孔回流焊原理及特点
THR工艺的基本原理:提前通过钢网和印刷机将锡膏印刷在通孔焊盘上,通过表面贴装机将通孔元器件和表贴元器件一起表贴到相应位置,在回流炉加热区将锡膏熔化,使锡膏在表面张力的作用下流向通孔元器件引脚、焊盘和印制板通孔,最终完成良好的焊接。
该工艺减少了一道波峰焊接工序,简化了生产流程,缩短了加工周期,可有效避免印制电路板(printed circuit board, PCB)和元器件受到波峰焊接的二次热冲击,使其不易变形。该过程无需使用锡条和助焊剂,不存在锡渣和助焊剂残留等污染问题。此外,对该过程中的锡膏印刷参数、贴片机表贴参数等工艺数据进行统一设置与管控,因而焊接质量一致性较好,保证了PCB与元器件的高接合强度与高焊接可靠性。
1.2 工艺流程对比
常规电气产品的PCB焊装工艺流程为SMT贴装和THT焊装,主要设备包括丝网印刷机、锡膏检测(solder paste inspection, SPI)机、表面贴装机、回流焊设备、自动光学检测(automated optical inspection, AOI)机、波峰焊机/选择焊机,工艺流程为:PCB上料→锡膏印刷→SPI→元器件贴装→回流焊接→AOI→THT元器件插装→波峰焊焊接→焊后处理→焊装检验。
通孔回流焊工艺流程将波峰焊焊装工序集成到SMT焊装工序,去掉波峰焊工序,省去了多个复杂工步,大幅度简化了工艺流程,具体流程为:PCB上料→锡膏印刷→SPI→元器件贴装→回流焊接→AOI。
1.3 生产质量与效率对比
与传统焊接工艺相比,通孔回流焊工艺的技术先进性、生产经济性明显。传统焊接工艺与通孔回流焊工艺对比见表1。
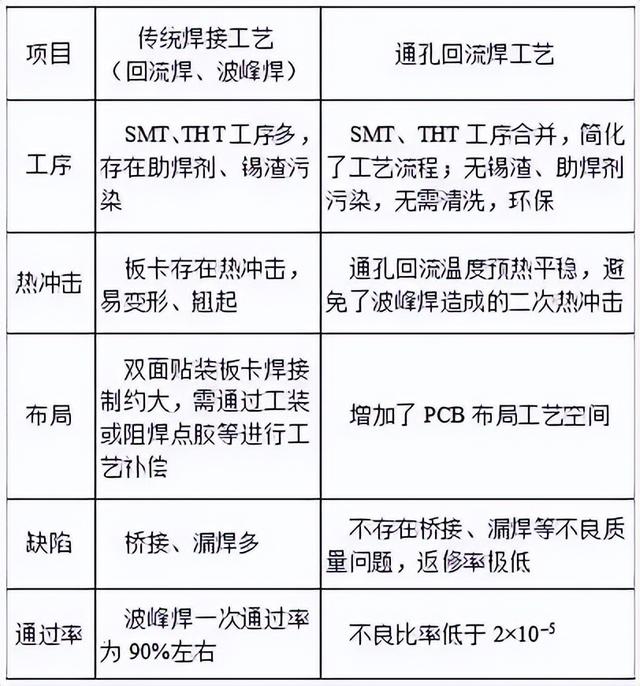
表1 传统焊接工艺与通孔回流焊工艺对比
2 通孔回流焊工艺制程影响因素
2.1 锡膏
为保证元器件在通孔回流焊过程中具备优良的焊接力,焊膏需要具有良好的湿润性和流动性。目前,锡膏分为低温锡膏、中温锡膏和高温锡膏,其主要成分及熔点见表2。中、低温锡膏成分主要为锡(Sn)、铋(Bi),成分Bi用于降低锡膏熔点,但容易造成焊点脆裂;高温锡膏成分主要为Sn、铅(Pb)、银(Ag),爬锡效果好,具有良好的焊接性能。因此,锡膏成分直接影响回流焊的焊接温度、焊接时间和焊接质量。
为保证良好的焊接可靠性,电气产品所使用的锡膏优先采用高温锡膏,此外在锡膏使用说明书中,炉温曲线规定了回流焊升温温度、焊接温度等关键参数,常见的炉温曲线示意图如图2所示。
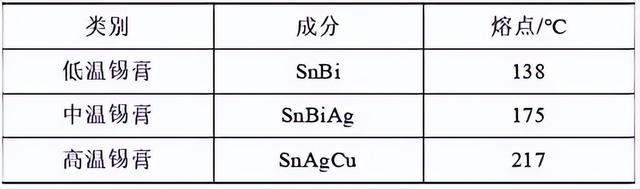
表2 不同锡膏的主要成分及熔点
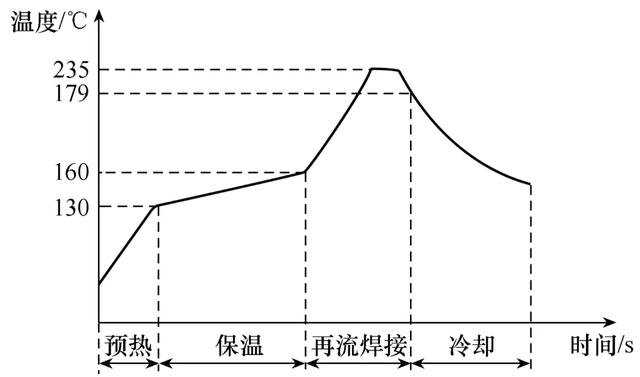
图2 常见炉温曲线示意图
2.2 钢网开孔
钢网选用不锈钢薄板材质,开孔孔壁一般为梯形,因为梯形开口有利于提高锡膏流动性。为保证充足锡膏量,并兼顾细间距元器件的特殊性,一般采用阶梯钢网印刷锡膏。
阶梯钢网是指在普通钢网基础上局部加厚或局部减薄,以满足不同元器件所需的不同锡膏量。通孔回流焊元器件所需的锡膏量应在PCB通孔填充并形成良好的焊点,因此其远大于SMT元器件所需的锡膏量。钢网开孔超出PCB焊盘的区域需要结合锡膏属性及PCB封装的实际情况进行合理调整,要注意避开元器件本体部位,防止贴装过程中锡膏被元器件本体压塌而飞溅出去,而飞溅出去的锡膏会在回流焊过程中形成锡珠。
通孔回流焊标准焊点填充效果如图3所示,元器件引脚所需的锡膏量必须根据元器件引脚形状、焊盘的通孔直径和PCB厚度来确定。因锡膏中50%为助焊剂类的挥发物体,所以锡膏体积是焊点体积的两倍,即锡膏体积V=2×(Vsolder+Vfillet),其中Vsolder为焊盘孔内焊锡体积,Vfillet为焊盘焊点润湿角体积。
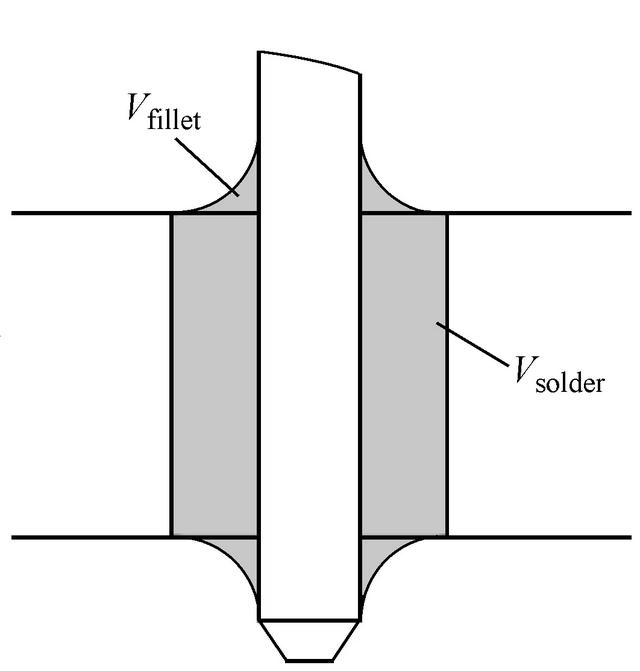
图3 通孔回流焊标准焊点填充效果
2.3 元器件
通孔回流焊元器件材质需满足防静电标准,当使用高温焊膏焊接时,元器件本体材质必须为耐高温材料,其能够承受的焊接炉温为260℃及以上。为便于表面贴装机自动吸取通孔元器件,通孔元器件来料包装方式采用编带包装或Tray盘包装,保证元器件本体平整且不得有分模线等凸起现象。因锥角不易挡住锡膏,元器件引脚脚端的形状优先选用锥形。此外,元器件引脚不宜太长,伸出PCB距离为0.8~1.2mm。元器件引脚要求示意图如图4所示。
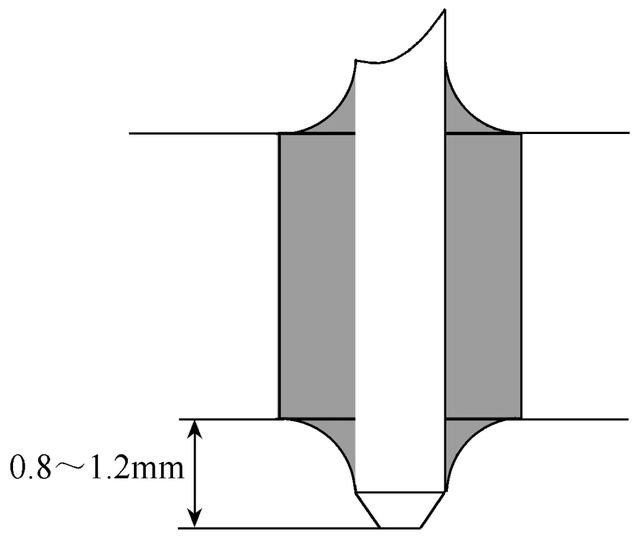
图4 元器件引脚要求示意图
通孔回流焊采用热风对流方式,便于锡膏从PCB正面流向焊盘孔内,在PCB的正反面形成良好的润湿角。当元器件与PCB贴底插装时,在元器件引脚与焊盘位置需有一定对外空间,便于热风进入焊盘孔内将锡膏熔化后形成良好的焊点。因此,为了保证整个PCB受热均匀,类似RJ45连接座类型的贴底元器件一般在底部有间隙保持器(standoff),如图5所示。
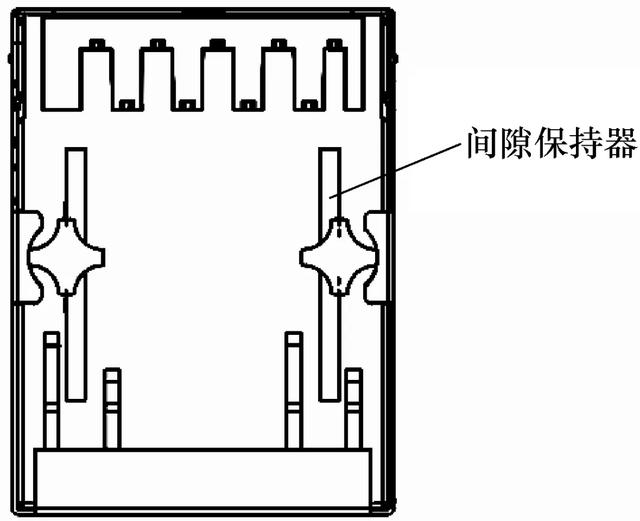
图5 间隙保持器
2.4 PCB的焊盘设计
运用通孔回流焊工艺时,PCB焊盘设计的主要要求如下:
1)合理设计元器件引脚直径d与PCB焊盘通孔径di的间距。间距太大容易造成锡膏掉落而产生空洞、少锡等不良现象,间距太小容易造成锡膏熔化后流动空间不足而产生虚焊现象。通常情况下,元器件引脚直径d与PCB焊盘通孔径di的间距设计为0.3~0.5mm,元器件引脚与焊盘通孔间隙示意图如图6所示。
2)通孔回流焊的元器件引脚间距一般要求设计为大于等于2.54mm,若引脚间距过小容易造成引脚连焊并导致相邻的孔内少锡。
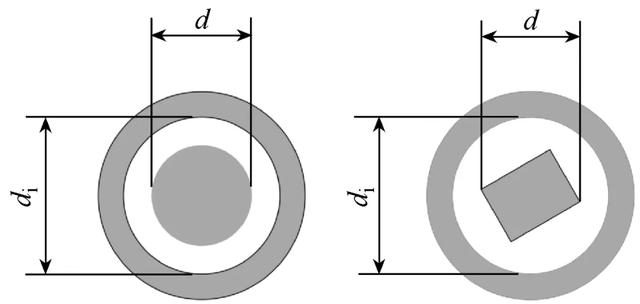
图6 元器件引脚与焊盘通孔间隙示意图
3)PCB正面贴片元器件与通孔回流焊元器件引脚的距离设计在3mm以上,防止因阶梯钢网加工工艺导致丝网印刷过程中周边元器件锡膏量过大而发生桥接现象。
3 通孔回流焊工艺应用
以某公司产品NRXX插件生产为例,验证通孔回流焊工艺的优越性。目前,NRXX插件的生产工艺为SMT表面贴装工艺和波峰焊焊接工艺,其中SMT表面贴装生产节拍为20s,波峰焊焊接生产节拍为60s。NRXX插件生产节拍与工序见表3。
插装元器件只有法拉电容、排针、端子等6种元器件,其总数量仅为6个却需要投入一条占地空间大的波峰焊生产线,还需配备4个工作人员参与生产,投入产出比特别低且无法保证焊接可靠性。为提高生产效率和焊接质量,应用通孔回流焊工艺进行改进。
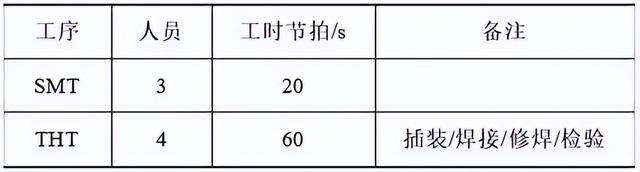
表3 NRXX插件生产节拍与工序
3.1 元器件
基于高温锡膏260℃的耐高温要求,核对NRXX 插件上所有元器件的耐高温特性。经确认,所有表贴元器件均满足回流焊炉温260℃的要求,而THT元器件不满足回流焊炉温条件,根据通孔回流焊工艺要求,对THT元器件进行改进。THT元器件分析与改进见表4。
3.2 PCB升级与钢网加工
EECRF0H法拉电容、排针等元器件改用表贴物料,并将对应的PCB板卡升级,钢网按照新工艺要求重新加工。RJ45插座、端子等改为通孔回流焊元器件,为保证充足的锡膏量,采用阶梯钢网印刷锡膏,新设计的局部加厚阶梯钢网如图7所示。
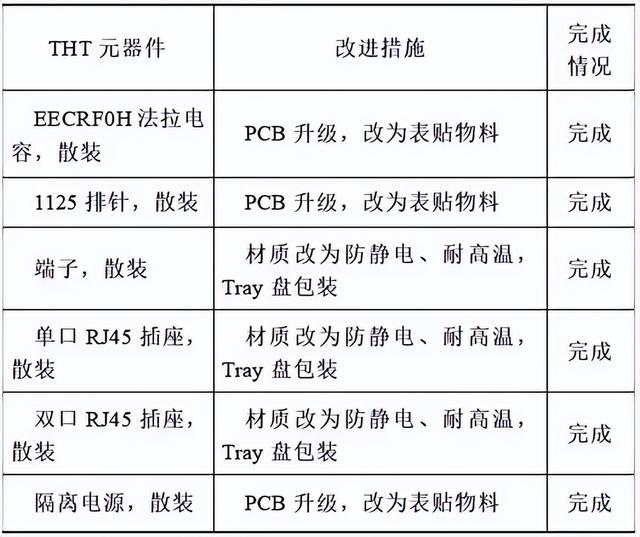
表4 THT元器件分析与改进
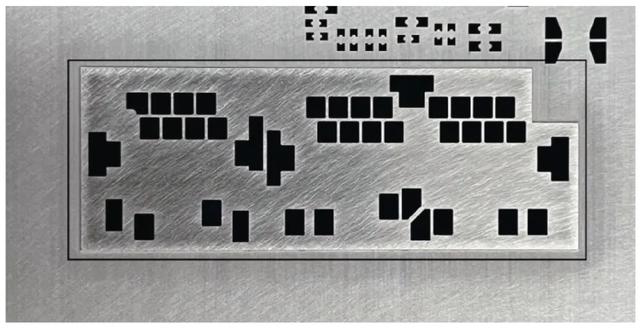
图7 局部加厚阶梯钢网示意图
3.3 试制加工
首先在表贴工序对通孔回流焊元器件的贴装工艺进行确认,包括供料方式是否合理、贴装吸嘴尺寸是否精准等。回流焊工序按照要求测试炉温曲线,回流焊峰值炉温在原有230℃的基础上提高到240℃,如图8所示。
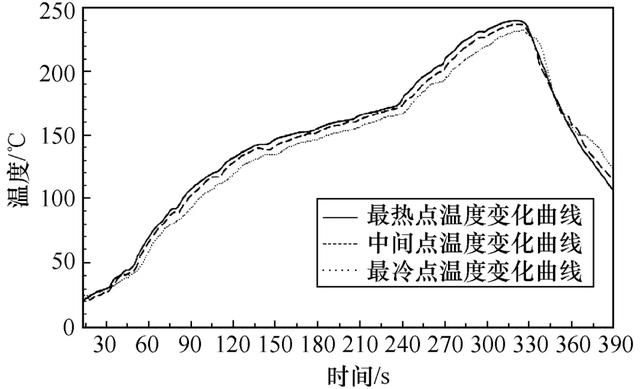
图8 炉温曲线
经打样验证,NRXX插件的 PCB焊点目视未发现异常,焊点目视化检查图如图9所示。
在X光检验环节,发现THR通孔元器件存在锡珠、空洞等焊接质量问题,针对这些问题进行分析并制定相应的解决方案,具体如下。
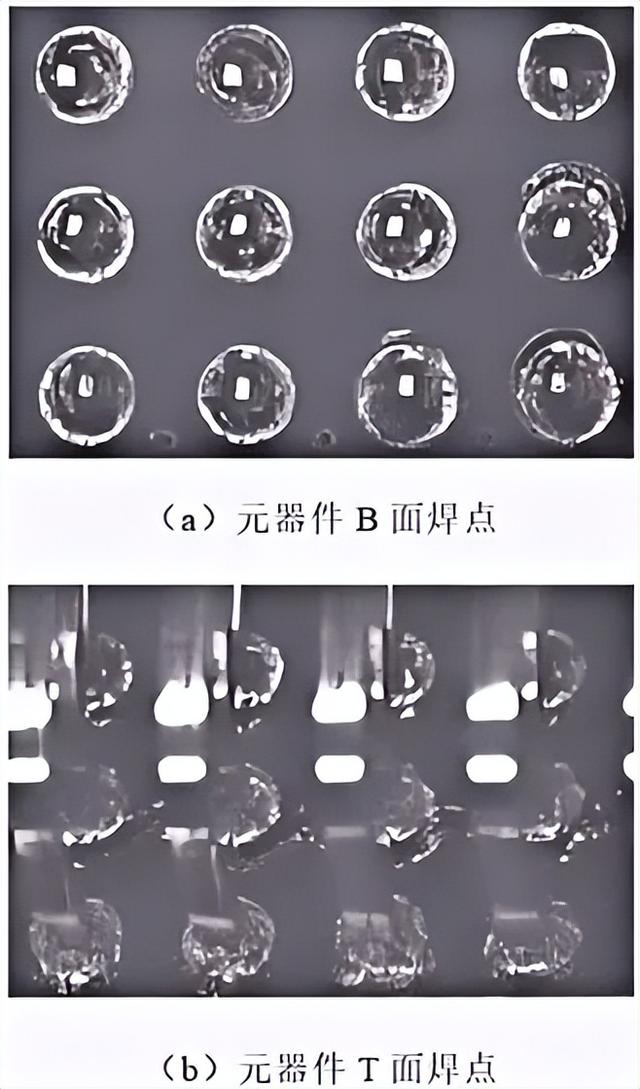
图9 焊点目视化检查图
1)锡珠:端子回流焊后,通过X光检验发现,焊点存在许多小锡珠,如图10(a)所示。调研发现,钢网开孔未避让端子本体,如图10(b)所示,绿色虚线区域为钢网开孔区域,PCB板卡经过锡膏印刷之后,锡膏填充在绿色虚线区域,在贴装过程中元器件端子将锡膏压塌,压塌的这部分锡膏在回流焊时形成锡珠。
因此,解决方案为优化钢网开孔,将钢网开孔区域纵向拉伸、横向收缩(3.05mm× 2.88mm改为4.4mm×2mm),以保证锡膏总体积不变,又能成功避免端子本体碰触锡膏,如图10(c)所示。再次生产焊接后,经X光检验未发现锡珠,如图10(d)所示。
2)空洞:经X光检验发现,端子焊点空洞率>25%,如图11(a)所示,不满足IPC 3级标准要求。
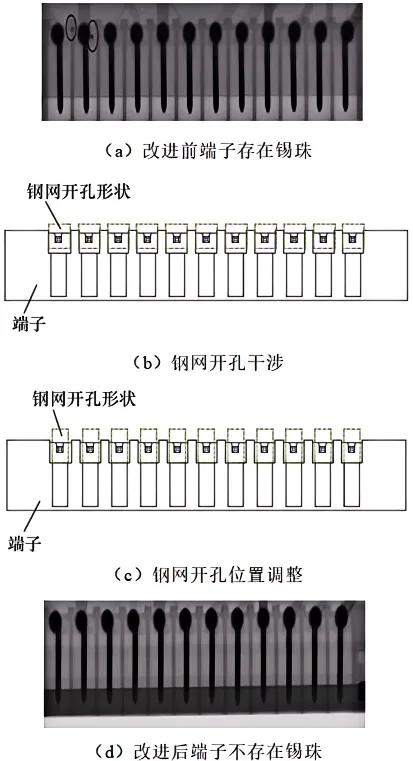
图10 锡珠问题分析与解决
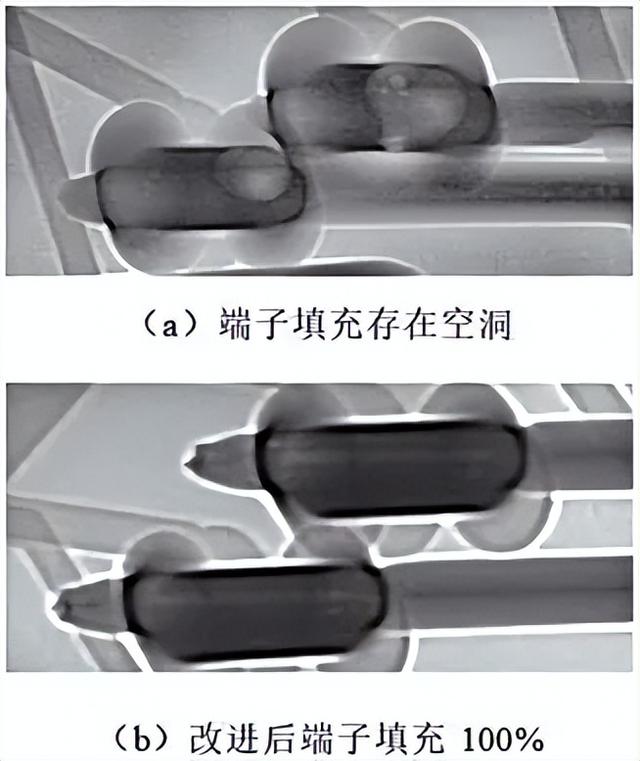
图11 空洞问题分析与解决
调研分析后认为,端子引脚电镀过程中电镀液杂质过多,导致引脚镀层可焊性差。将该问题反馈给端子厂家,厂家在端子加工过程中增加镀层可焊性测试,以保证引脚镀层可焊性良好。重新生产焊接后再进行X光检验,端子引脚焊点无空洞,其内部100%填充,如图11(b)所示。
3.4 第三方测试
对焊接后的焊点进行金相切片与扫描电子显微镜(scanning electron microscope, SEM)分析:根据IPC—TM—650标准,在金相显微镜下观察焊点微观结构,并利用SEM对焊点截面的金属间化合物(intermetallic compound, IMC)层进行测量,结果如图12所示。IMC层连续均衡,焊点填充满足IPC 3级要求,厚度在1~3mm之间,达到了理想的焊接强度。
3.5 不足之处
采用通孔回流焊工艺后发现,在通孔元器件插装过程中,部分锡膏被元器件引脚带出,掉落在回流焊设备内部,导致助焊剂挥发后沉淀增加,这对回流焊设备造成一定的污染,需设备人员定期清理保养。此外,回流焊峰值温度增加10℃,相应的热冲击也有小幅度增加,需要根据具体情况进行判断分析。
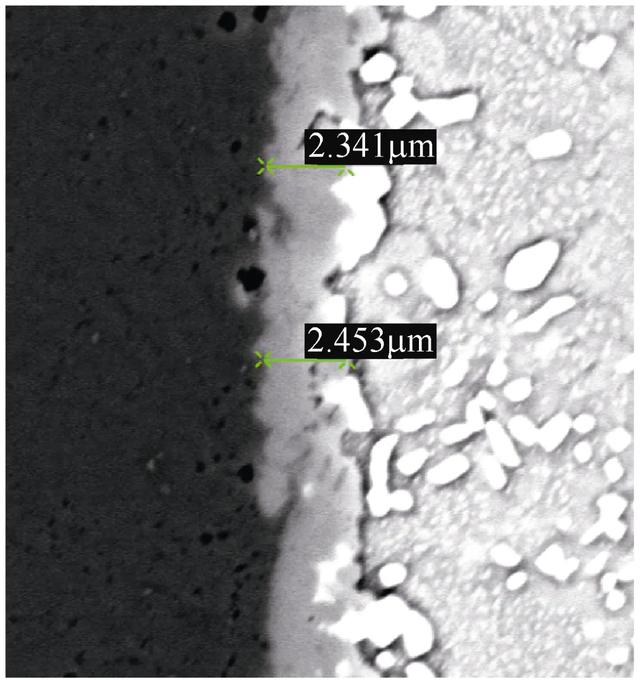
图12 通孔焊点的IMC层测量结果
3.6 小结
该公司NRXX插件经通孔回流焊工艺改进,减掉了波峰焊工序,省去了多个复杂工步,生产效率得到明显提高,生产周期缩短50%,人员减少50%,传统焊接与通孔回流焊生产模式对比见表5。过程中遇到锡珠、空洞等问题,从钢网开孔、元器件等角度进行分析解决,并将此类问题整理形成管控规范,保证后续生产不再出现。
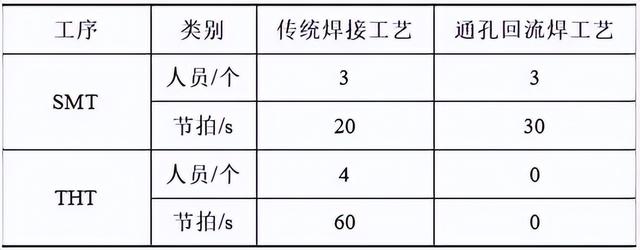
表5 传统焊接与通孔回流焊生产模式对比
4 结论
本文详细研究了通孔回流焊工艺的特点和影响因素,重点从锡膏选用、钢网开孔工艺、元器件性能、PCB焊盘设计等角度展开分析,并通过实际生产验证了通孔回流焊工艺能够拓展高密度、细间距产品的生产窗口,能从多方面替代传统波峰焊工艺,并解决锡珠、焊点空洞等焊接问题,提高了元器件在通孔回流焊中的焊接可靠性,降低了产品的生产成本,有效推进了元器件表贴化发展。
通孔回流焊工艺可根据产品的布局进行设计,在产品设计阶段提前规划相应生产工艺路线,明确PCB板卡、元器件等工艺要求,进一步提高产品焊接质量和生产效率,可以预见在未来电子组装中通孔回流焊会发挥更重要的作用。
本工作成果发表在2024年第4期《电气技术》,论文标题为“电气产品通孔回流焊工艺研究”,作者为鲍军云、王高垒、彭学军、李磊。