引言:
世人皆知,柴油发动机是工业发展的"心脏"。然而鲜为人知的是,在上世纪70年代,中国的柴油发动机还处在"拖拉机冒黑烟"的尴尬境地。那时的中国工程师们,只能眼睁睁看着国外的先进技术却无法突破。可就在1978年,一个偶然的机会,让中国的柴油发动机研发迎来了转机。在一次普通的技术交流会上,一位年过古稀的老工程师站了起来,他的一番话惊呆了在场所有人。就是这位老人的建议,为中国柴油发动机打开了突破的大门。40多年后的今天,当年那个让国人抬不起头的"心病",如今却成为了中国制造业的一张闪亮名片。这位老工程师到底说了什么?中国的柴油发动机又是如何从"冒黑烟"走向"技术领先"的呢?
一、蹒跚学步:国产柴油机的艰难起步
1973年的一个寒冷冬日,上海柴油机厂的车间里,工人们正围着一台刚从国外进口的柴油发动机发愁。这台发动机虽然个头不大,却价值不菲,折合人民币要20多万元。要知道,那时候一个普通工人的月工资也就四五十元。
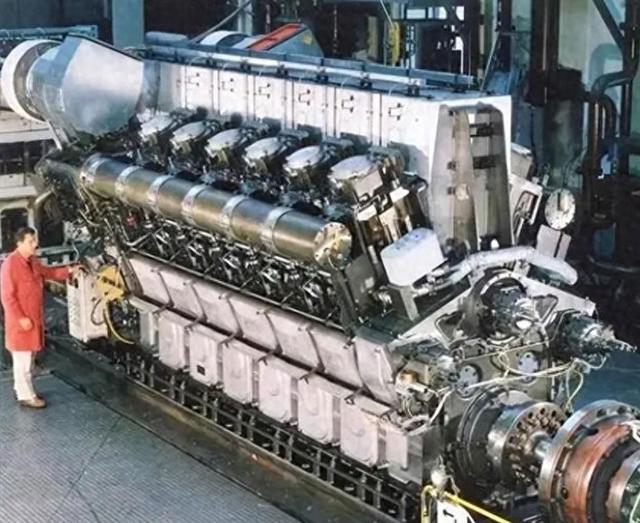
"这么贵的东西,我们就不能自己造吗?"车间主任李国强叹了口气说道。可话是这么说,当时的中国柴油机制造业,连最基本的精密加工设备都没有。
那时的国产柴油机,质量确实令人担忧。拖拉机一启动,黑烟就滚滚而出,噪音震天响,农民们戏称这是"会喘气的铁牛"。更让人头疼的是,这些柴油机经常会出现故障,一到收获季节就让农民们捏着一把汗。
1975年,全国重点工程项目需要大量工程机械,可国产柴油机的质量实在无法满足要求。没办法,只能花大价钱从国外进口。一年下来,光是柴油发动机的进口费用就高达3亿美元,这可是当时国家一笔不小的外汇支出。
有人说,不就是个发动机吗?看着照着造不就行了?可实际上哪有那么简单。就拿最关键的喷油器来说,它的精度要求达到头发丝直径的千分之一,这样的加工精度,在当时的中国简直是天方夜谭。

1976年,国家组织了一次柴油机攻关会议。会上,来自全国各地的专家们都提出了自己的想法。有人提议从国外购买技术,有人建议先从简单的零件做起。但最终因为种种原因,这些建议都没能落实。
就在大家一筹莫展的时候,天津内燃机研究所送来了一份调查报告:他们发现国产柴油机之所以效率低下,关键problem出在燃油系统上。这个发现为后来的技术突破指明了方向。
1977年深秋,第一台采用改良型燃油系统的样机在上海柴油机厂试制成功。虽然这台发动机的性能还比不上进口产品,但黑烟明显减少了,油耗也降低了不少。这个小小的进步,让工程师们看到了希望。
可是好景不长,在进行第二批样机试制时,又遇到了新的难题。由于缺乏精密的检测设备,许多关键参数无法准确测量,样机的性能始终无法达到预期效果。
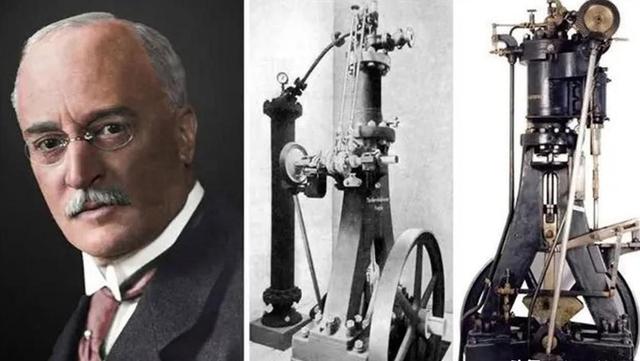
这种困境一直持续到1978年初。那时的中国柴油机行业,就像一个正在学走路的孩子,每迈出一步都充满了艰辛。但正是这些艰难的尝试,为后来的技术突破积累了宝贵的经验。
二、转机初现:老工程师的关键建议
1978年3月15日,北京机械研究所的会议室里座无虚席。这是一场全国性的柴油机技术交流会,来自全国各地的工程师们齐聚一堂,讨论如何突破柴油机制造的技术瓶颈。
就在大家争论不休之际,坐在角落里的张德昌老工程师举起了手。张德昌已经75岁高龄,他是新中国第一代内燃机专家,曾在1950年代参与过第一台国产柴油机的研制工作。
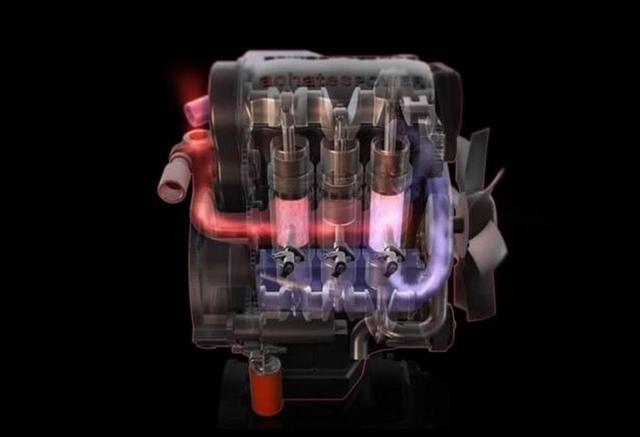
"诸位同志,我们现在走的是一条错误的道路。"张德昌的开场白让会场一片哗然。他指出,当时国内普遍采用的是照搬国外图纸的方式,这种方式根本无法掌握核心技术。
张德昌拿出了一份手绘的设计图纸,这是他花了三年时间研究出来的新型柴油机燃烧系统方案。他建议,与其盲目模仿国外技术,不如从基础研究做起,先解决燃烧效率的问题。
会议结束后,张德昌的建议引起了有关部门的重视。当年4月,国家计委批准成立了"柴油机基础研究专项小组",张德昌被任命为技术顾问。
专项小组成立后的第一个任务,就是验证张德昌提出的新型燃烧系统方案。在天津内燃机研究所的实验室里,工程师们按照张德昌的图纸制作了试验装置。
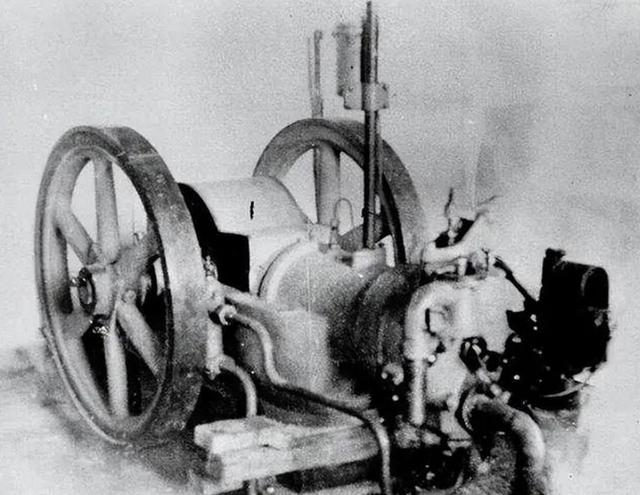
实验结果令人振奋。新型燃烧系统在相同工况下,燃油效率提高了15%,而且黑烟排放明显减少。这个成果立即引起了业内轰动。
1978年底,专项小组又有了新发现。他们发现国外先进的柴油机并非依靠单一技术取胜,而是将多项技术有机结合。这个认识促使他们改变了研究思路。
1979年初,在张德昌的指导下,专项小组提出了"三步走"发展战略:第一步解决燃烧效率,第二步提高制造精度,第三步开发电控系统。这个战略为后来的技术突破指明了方向。
同年5月,第一台采用新型燃烧系统的样机在上海柴油机厂试制成功。这台发动机虽然还不够完善,但它的诞生标志着中国开始走上了自主创新的道路。
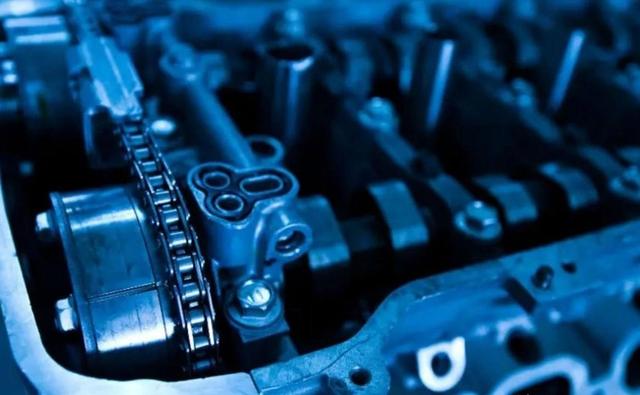
张德昌的建议不仅带来了技术上的突破,更重要的是改变了整个行业的发展思路。从此,中国的柴油机制造业不再一味追求"拿来主义",而是开始重视基础研究和自主创新。
到了1980年,这个新思路带来的成果开始显现。全国已有十几家工厂开始采用新型燃烧系统,产品性能有了明显提升。柴油机行业的"冒黑烟"现象也开始逐渐改善。
三、突破瓶颈:三大技术难关的攻克
1980年代初期,虽然新型燃烧系统取得了初步成功,但中国柴油机行业依然面临着三大技术难关:高压共轨系统、精密喷油器和智能控制系统。这些技术被国外垄断多年,要攻克谈何容易?
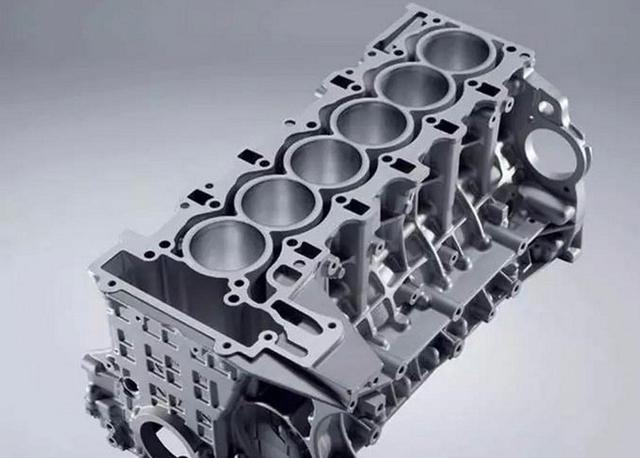
1982年春天,武汉理工大学的实验室里,一群年轻工程师正在进行高压共轨系统的测试。这个系统要求燃油压力必须稳定在1600bar以上,而当时国产设备最高只能达到800bar。经过反复试验,他们发现问题出在高压泵的材料上。
为了解决这个难题,冶金研究所专门成立了攻关小组。他们尝试了上百种不同的材料配方,终于在1984年研制出了能承受2000bar压力的特种钢材。这项突破为高压共轨系统的研发打下了基础。
第二个难关是喷油器。1985年,上海柴油机研究所的工程师们正在挑战一个看似不可能的任务:将喷油器的加工精度提高到0.002毫米。要知道,这相当于将一根头发丝劈成五十份那么细。
攻关小组从日本进口了一台精密加工中心,但仅有设备还不够。工程师们发现,即使用同样的设备,国外的喷油器质量依然更好。原来,关键在于加工工艺。
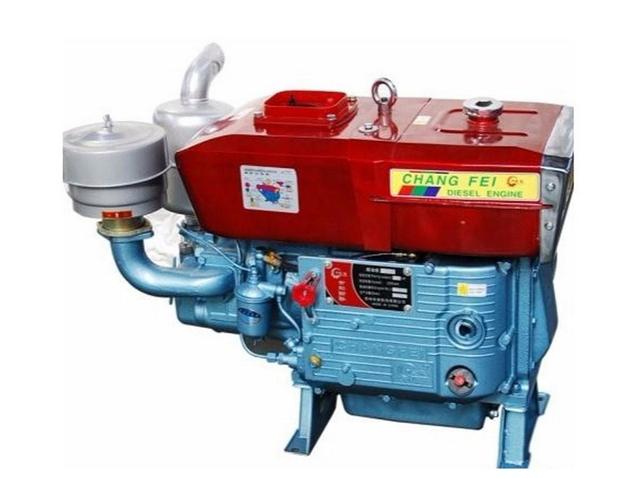
1986年底,一个偶然的发现为他们指明了方向。一位工人发现,在深夜车间温度稳定时,加工精度会明显提高。这启发工程师们开发了恒温加工工艺,终于实现了超高精度加工。
第三个难关是智能控制系统。1987年,清华大学的专家们开始研发柴油机电控单元。当时国内还没有相关的技术积累,他们只能从最基础的程序开始写起。

一年后,第一个国产电控单元问世了。虽然功能还很简单,但已经能够实现基本的喷油控制。这个突破证明了中国完全有能力开发自己的控制系统。
1989年初,这三项技术首次在同一台发动机上进行集成测试。测试结果显示,发动机的性能已经接近国际水平,而成本却只有进口产品的三分之一。
到了1990年,更大的惊喜出现了。工程师们发现,通过优化三项技术的协同工作,发动机的效率居然比单独使用每项技术时都要高。这个发现为后续的技术改进指明了新方向。
1991年,第一批采用全套新技术的柴油机投入市场。这些发动机不仅性能优异,而且价格适中,很快就受到用户欢迎。一些外国专家参观后也对中国的技术进步表示惊讶。
经过十多年的努力,中国终于攻克了这三大技术难关。但更重要的是,通过这个过程,中国积累了宝贵的技术经验,培养了一支优秀的研发队伍,为后续的创新发展奠定了坚实基础。
当这些发动机陆续装配到工程机械上时,施工现场再也看不到往日浓烟滚滚的景象。取而代之的是动力强劲、节能环保的新型机械。这不仅改变了中国工程机械的面貌,也为后来的技术创新打开了新的篇章。
四、再创新高:走向世界一流水平
1992年,一个令人振奋的消息传遍了中国柴油机行业:天津内燃机研究所研制出了一款全新的重型柴油发动机,其燃油经济性首次超过了德国同类产品。这标志着中国柴油机制造业开始向世界一流水平迈进。
这款发动机的成功并非偶然。1991年底,天津内燃机研究所组建了一支由年轻工程师主导的创新团队。他们打破常规,采用了全新的设计理念,将传统的机械控制改为全电子控制系统。
1993年,上海柴油机厂也传来好消息。他们开发出了一种新型缸内直喷技术,这项技术不仅提高了发动机效率,还大幅降低了污染物排放。该技术很快获得了国家专利,并引起了国际同行的关注。
1994年的广州国际工程机械展览会上,一场特殊的性能测试引来众多观众。测试场地上,一台国产柴油机与一台进口发动机同时运行。测试结果显示,国产发动机在功率输出和燃油经济性方面已经与国际品牌不相上下。
技术进步带来的不仅是性能提升。1995年,中国首次向东南亚出口大批量柴油发动机。这些发动机的价格只有同类进口产品的一半,却能提供相近的性能,很快在国际市场上站稳了脚跟。
1996年,一个重要的国际合作项目启动了。德国一家著名发动机制造商主动寻求与中国合作,共同开发新一代柴油机。这在此前是难以想象的,因为中国一直被视为技术引进方。
1997年的一个细节特别值得一提。当时一家日本公司准备在中国建厂,他们惊讶地发现中国的某些加工工艺比他们还要先进。特别是在气缸套的制造方面,中国开发的新工艺可以将生产成本降低30%。
进入1998年,中国柴油机行业又有重大突破。西安交通大学的研究团队开发出了具有自主知识产权的可变几何涡轮增压器,这项技术随后被多个国家的制造商采用。
1999年,一个国际性的技术评估会在北京举行。来自各国的专家对中国柴油机的发展给予了高度评价,特别是在节能环保方面的创新成果。有专家指出,中国已经从技术追随者转变为创新者。
2000年,中国柴油机产业迎来了一个具有里程碑意义的时刻。一款完全自主研发的高端柴油发动机通过了欧盟最严格的排放标准认证。这标志着中国柴油机制造技术已经达到了世界领先水平。
这期间,国产柴油机的应用范围也在不断扩大。从工程机械到发电设备,从农用机械到船用动力,中国制造的柴油机开始在各个领域崭露头角。特别是在工程机械领域,国产柴油机的市场份额已经超过了70%。
到了2001年,中国已经成为全球重要的柴油机制造国。不仅产量位居世界前列,技术水平也获得国际认可。当年,有三项中国发明的柴油机核心技术被写入国际标准,这在中国工业史上还是首次。
五、持续创新:引领行业发展方向
2002年初,一场别开生面的技术交流会在重庆召开。会议的主题是柴油机的未来发展方向,与会专家一致认为,新能源与智能化将成为行业发展的两大趋势。
这个判断很快得到了验证。2003年,上海柴油机厂推出了首款混合动力柴油发动机系统。这套系统采用了电机辅助技术,在低速工况下可以实现纯电动运行,显著降低了燃油消耗和排放。
2004年,一个重要的研究项目在大连理工大学启动。研究团队开始探索生物柴油在传统发动机上的应用可能。他们改进了喷油系统,成功解决了生物柴油黏度过高的问题。
2005年的一次偶然发现引发了新的技术革命。天津一家研究所在测试中发现,采用纳米涂层技术处理的气缸壁,可以大幅减少机械损耗。这项技术随后被推广到全行业。
2006年,智能化领域取得重大突破。中国自主研发的柴油机智能诊断系统首次投入使用。这套系统能够实时监测发动机的工作状态,提前预警可能出现的故障。
2007年,一项创新性的合作模式开始推行。全国多家科研院所联合成立了"柴油机创新联盟",共享研发资源,协同攻关重大技术难题。这种模式极大地提高了研发效率。
2008年,中国首次主导制定了一项国际柴油机标准。这项标准涉及柴油机的智能化测试方法,得到了国际同行的广泛认可。这标志着中国在行业标准制定方面开始发挥主导作用。
2009年,一个重要的技术突破引起了全球关注。西安交通大学开发出了新型可变压缩比技术,这项技术可以根据不同工况自动调整压缩比,实现最优化运行。
2010年,智能制造开始在柴油机行业推广。武汉一家工厂建成了全国首条柴油机智能化生产线,实现了全过程数字化控制,生产效率提高了40%。
2011年,新能源领域又有重大进展。一种利用氢气辅助燃烧的技术在长沙试验成功,这项技术可以让传统柴油机实现超低排放。
2012年见证了另一个重要突破。南京一家研究所开发出了基于人工智能的发动机优化控制系统,这套系统能够自主学习和优化运行参数。
2013年,中国柴油机制造业实现了一项历史性跨越。全行业的技术创新专利申请数量首次超过德国,跃居世界第二位。其中,有多项专利技术已经在国际市场上广泛应用。
这些年来,中国柴油机行业的创新成果不断涌现。从新材料应用到智能控制,从节能减排到可靠性提升,中国的技术创新正在引领全球行业发展。特别是在智能化和新能源应用方面,中国的许多创新做法已经成为国际同行借鉴的对象。
当第一批搭载新一代智能柴油机的工程机械开进施工现场时,现场的工人们再也不用担心噪音和尾气的困扰。这些机器不仅工作效率更高,而且更加节能环保。在城市建设的工地上,这些新型柴油机正在默默见证着中国工业技术的进步。