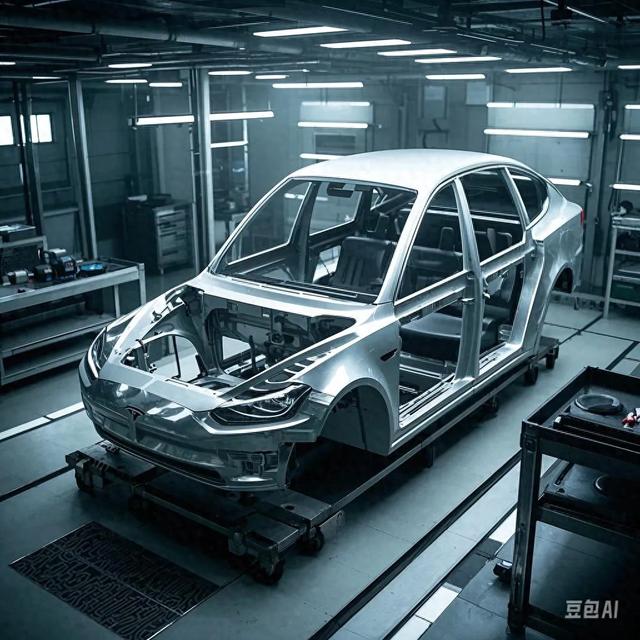
在汽车制造领域,特斯拉一直是备受瞩目的创新者。然而,据路透社等报道,特斯拉已放弃一体成型车架技术,这一重磅消息引发了广泛的关注与讨论。
特斯拉放弃一体成型车架技术,背后有着诸多原因。首先是成本投入问题。一体化压铸虽然从长远来看有助于降低成本,可前期却需要巨额投资。就像丰田安装的大型一体式铝制压铸车架专用压铸机,售价高达数百万美金,这还不算额外的模具开销。如此高昂的初期生产成本,让特斯拉在当前面临较大资金压力的情况下,无力承担进一步扩大一体化压铸工艺所需的费用。其次,生产效率和品控方面也存在挑战。一体化压铸生产线打造极为复杂,涉及众多环节流程,实际进度往往不尽如人意,其生产效率难以满足大规模量产的需求。而且,压铸件的精度低于冲压件,容易出现表面粗糙、气泡等质量问题,这不仅影响铸件强度,还会增加检测成本和工作量,对于追求高品质与高效率的特斯拉来说,无疑是个棘手的难题。再者,特斯拉正处于重大战略调整和成本削减阶段,其将更多精力放在了自动驾驶和新车型开发上,例如优先开发基于下一代平台的 Robotaxi,而其底盘将采用三段式组装方法,而非一体成型车架。
在放弃一体成型车架技术后,特斯拉有着一系列替代方案可供选择。回归传统三段式铸造方法是其中之一。这种方法将车架分为三个部分分别铸造然后组装,相对成熟可靠。它能够降低生产的复杂性,前期设备投资无需像一体成型车架技术那般巨大,主要依靠冲压、焊接等常规工艺设备即可。在生产过程中,能够在一定程度上提高生产效率,使量产需求得到更好的满足。同时,后期维护成本也相对较低,若某个部分出现损坏,可针对性地进行修复或更换,无需像一体成型车架那样在严重碰撞时可能面临整体更换的困境。
“拆箱式”生产工艺则是另一种创新尝试。它改变了以往从外到内的汽车制造模式,在最终组装之前同时组装关键部件,由内到外进行汽车的制造。这一工艺可显著提高自动化程度,减少员工数量,从而降低人力成本。并且,它还能加快汽车制造速度,使特斯拉在市场竞争中更具时间优势,能够更快地将产品推向市场,满足消费者日益增长的需求。
Cell-to-chassis 电池车身一体化技术也备受关注。该技术将电池 cells 直接集成到底盘 chassis 中,打造出一个融合的整体结构。这样做的好处颇多,一方面能够增加车内空间,为消费者提供更为宽敞舒适的驾乘环境;另一方面,它能提高车身扭转刚度,使车辆在行驶过程中更加稳定和安全。同时,还能降低车辆重量,减少零部件数量,进而降低成本,在提升车辆性能的同时实现了成本的有效控制。
此外,高强度钢及铝合金组合车身结构也是特斯拉可能采用的方案。这种结构根据车辆不同部位的功能和受力特点,巧妙地运用不同强度和材质的材料。比如在车头易碰撞部位使用高强度钢制作吸能盒,能够有效吸收碰撞能量,保护车内乘客安全;在车身 A 柱到 C 柱采用超高强度钢搭建笼式车身结构,为车身提供坚实的骨架支撑;在车尾底部等部位使用铝合金材质,在保证车身强度和安全性的前提下,实现车辆的轻量化目标。与一体成型车架技术相比,其前期设备投资成本相对较低,无需购入昂贵的大型压铸机及配套设备。在原材料成本方面,虽然铝合金单价高于高强度钢,但通过合理布局材料使用,可在保证强度和性能的同时控制成本。制造成本方面,尽管制造工艺成熟但因多零件冲压、焊接等会增加制造时间和人力成本,不过总体制造成本相对较易控制。后期维修成本也较低,局部损坏可单独更换受损部件。
特斯拉在车架技术上的这一变革,无论是对于汽车行业的技术发展走向,还是对于特斯拉自身的未来布局,都有着深远的意义。它将在成本控制、生产效率提升、产品质量保障以及战略推进等多方面产生连锁反应,而我们也将拭目以待,看特斯拉在新的车架技术路线上能创造出怎样的辉煌成就。