针对传统管件电磁胀形存在管件壁厚减薄、轴向变形不均匀的问题,三峡大学邱立课题组提出一种基于双层凹型集磁器的管件电磁胀形方法。通过对集磁器结构的重新设计,调控管件成形区域的涡流与电磁力分布,实现提升管件轴向变形均匀性的同时也能够抑制管件壁厚减薄,为改善管件成形性能提供新思路。

研究背景
轻量化制造是航空航天,交通运输等领域实现节能减排的重要途径,采用镁铝为代表的轻质合金材料是实现轻量化的重要手段。然而,传统机械加工工艺处理镁铝等轻质合金材料时存在成形极限低,易起皱,易回弹等缺陷。电磁成形工艺是一种利用洛伦兹力驱动金属工件发生高速变形的先进制造技术。
与传统加工工艺相比,电磁成形因其极高的应变速率能够显著提升成形极限,且能抑制起皱及回弹现象。目前,传统管件电磁胀形工艺应用于金属管件材料时存在管件壁厚减薄严重及管件轴向变形不均匀等问题。
论文所解决的问题及意义
针对传统管件电磁成形存在的管件壁厚减薄严重及轴向变形不均匀的问题,在传统管件电磁胀形的基础上引入新型集磁器,提出基于双层凹型集磁器管件电磁胀形方法。通过调控管件成形区域涡流与电磁力分布,改善管件成形形貌,提升管件轴向变形均匀性;同时,通过轴径向电磁力同步加载的方式抑制管件壁厚减薄。
论文方法及创新点
图1(a), (b) 分别为传统管件电磁成形二维轴对称模型及成形管件形貌。由图1(a)可以看出传统管件电磁成形中径向电磁力呈现两端小中间大的凸型分布特征,因此图1(b)中成形管件形貌也呈现出相应的两端小中间大的凸型形貌特征;并且由于管件端部受到的轴向电磁力较小,管件端部材料难以流动,随着管件径向胀形的进行,管件壁厚不断减薄甚至破裂。
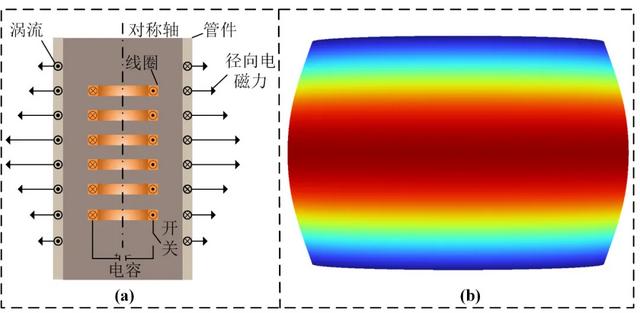
图1 传统管件电磁胀形 (a)二维轴对称模型 (b)成形管件形貌
三峡大学电气与新能源学院邱立课题组为了改善传统管件电磁胀形存在的成形缺陷,提出基于双层凹型集磁器管件电磁胀形方法,如图2所示。图2(a), (b)分别为其二维轴对称模型及成形管件形貌。
为了定量对比管件轴向变形均匀性,引入变量定义为管件轴向上能达到最大径向变形量90%的区域。由图2(a)可以看出,引入双层凹型集磁器之后,原本两端小中间大的电磁力分布特征被调控为两端大中间小的分布特征,通过削弱管件中部成形区域径向电磁力减小其胀形量,从而提升管件轴向变形均匀性,如图2(b)所示。
图3为两种成形模式下管件胀形过程对比。由图可以看出,传统管件电磁胀形过程中管件始终是凸型不均匀形貌,而引入双层凹型集磁器之后,管件胀形过程中成形形貌始终是均匀的;
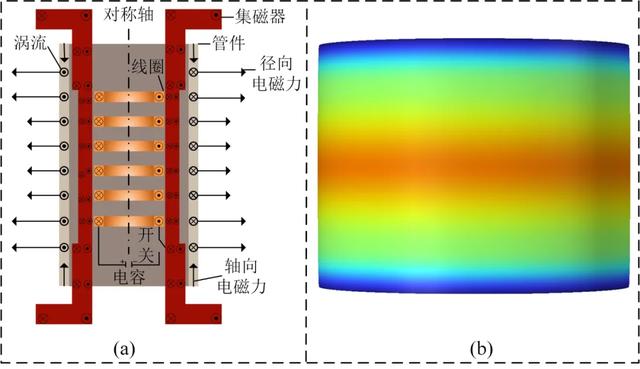
图2 基于双层凹型集磁器管件电磁胀形 (a)二维轴对称模型 (b)成形管件形貌
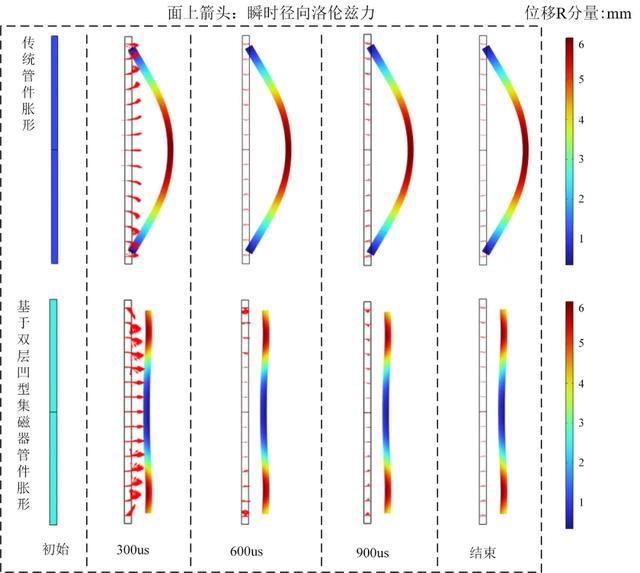
图3 两种成形模式下管件胀形过程对比
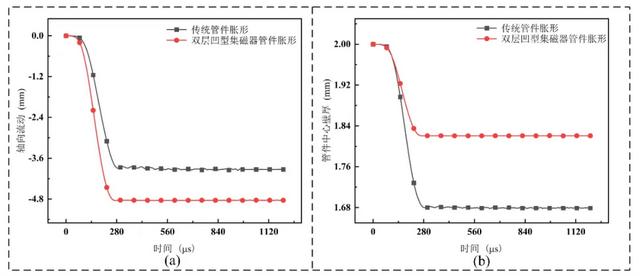
图4 两种胀形模式下管件端部流动对比 (a)轴向流动对比 (b)管件中心壁厚对比
引入双层凹型集磁器之后,管件端部区域感应涡流显著增加,从而增大了管件端部材料流动,抑制了管件壁厚减薄现象。两种成形模式下,管件端部区域流动及中心壁厚变化对比分别如图4(a), (b)所示。可以看出引入双层凹型集磁器之后管件端部区域材料流动显著提升,管件壁厚也显著增加。
结论
对比两种成形模式下管件变形数据可以得到,引入双层凹型集磁器之后,管件轴向变形均匀性提升了2.31倍;管件壁厚减薄量从传统管件电磁胀形的22.07%降低至8.30%。因此所提出的基于双层凹型集磁器管件电磁胀形方案能够同时改善传统管件电磁胀模式下管件轴向变形不均匀及壁厚减薄严重现象。
团队介绍
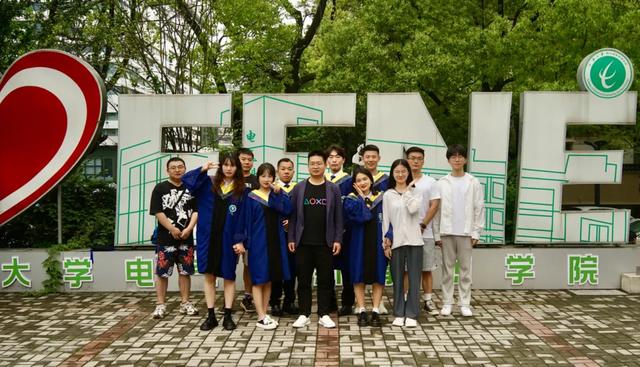

本文由三峡大学电气与新能源学院邱立课题组完成。课题组主要开展高电压技术、电磁成形、电磁场分析及应用等研究,主持参与了多项国家自然科学基金。近年来,以第一作者或通讯作者在国内外SCI/EI期刊发表学术论文30余篇,申请国家发明专利80余项,已获授权发明专利40项。

邵子豪,硕士研究生,研究方向为磁操控技术,包括电磁成形及磁控软体机器人。
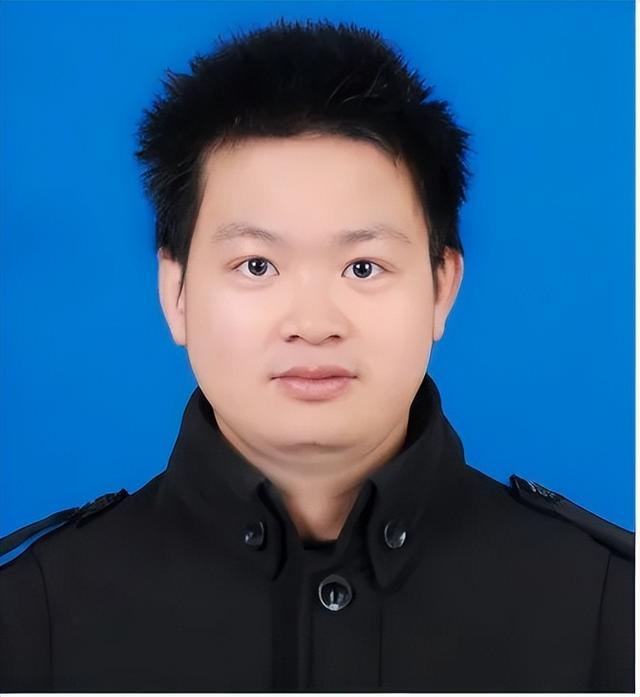
邱立,副教授,博士生导师,研究方向为高电压技术、脉冲功率技术、输电线路设备电磁场分析及应用。
本工作成果已发表在2024年第5期《电工技术学报》,论文标题为“基于双层凹型集磁器的管件电磁胀形电磁力特性及变形行为研究”。本课题得到国家自然科学基金的支持。