金丝引线键合的影响因素探究
刘凤华
中电科思仪科技股份有限公司
摘要:
键合对设备性能和人员技能的要求极高,属于关键控制工序,键合质量的好坏直接影响电路的可靠性。工艺人员需对键合的影响因素进行整体把控,有针对性地控制好各个关键点,提升产品键合的质量和可靠性。通过对金丝引线键合整个生产过程的全面深入研究,分析了键合设备调试、劈刀选型、超声、温度、压力、劈刀清洗和产品的可键合性 7 个主要影响因素,并且通过实际经验针对各个影响因素给出了合理的改善建议。
1 研究背景
金丝引线键合始于1957年,是应用时间最早、应用范围最广的键合方式之一[1] 。金丝引线键合分为球焊和楔焊两种。球焊的难度较低,拉线灵活,适合键合高度差和线长变化大的产品,由于球点的存在,弧高无法做得足够低,对应的电路指标也会降低,适合低频电路,一般用于直流偏置线和接地线的键合。楔焊的焊点小且弧高可以对称渐变地控制在 75 μm 以内,电路指标特性好,一般应用于通路的电路互连。
键合的本质是两种材料之间形成原子间的相互融合和可靠连接。想要实现两种材料原子间的相互融合连接,需要增加额外的能量驱动,从而使得两种材料之间形成键合形成层。
如图 1 所示,经过超声热压的键合作用,材料 1和材料 2 在接触面形成了牢固的键合形成层,从而可靠地连接在一起。键合点的拉力测试和剪切力测试也是为了测试键合形成层的强度,如何保证键合形成层的可靠性是金丝引线键合技术的关键。
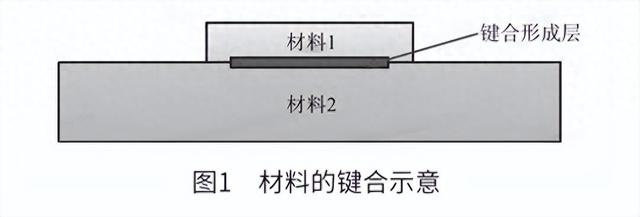
2 金丝引线键合的影响因素探究
对整个键合过程进行研究分析,金丝引线键合有 7 个主要影响因素:键合设备调试、劈刀选型、超声、温度、压力、劈刀清洗和产品的可键合性。
2.1 键合设备调试
手动球焊机调试的关键点是打火杆与劈刀的间距、尾丝长度、打火电流和打火时间。打火杆与劈刀的间距应在1 mm左右,间距过大会导致送丝参数和打火参数的数值设置偏大,键合过程中的不稳定性增加。尾丝长度应合适,太小会导致球点偏小、送丝不稳定,太大会使金丝碰触打火杆导致打火失败。打火电流和打火时间应有合适的区间,太小会导致球点偏小、球不成型,太大会导致球点偏大、根部伤线。类似于Westbond 机型的键合机通过凸轮带动线夹的机械往复运动进行送丝,会存在凸轮复位点偏移导致送丝量变化的问题。针对这一问题,可以在凸轮上画线标记复位点,如果出现复位点偏移可以手动进行恢复。
自动球焊机对送丝的要求更高,其通过气控送线和真空回吸的共同作用进行线控,设备整体输入气压不能太大,太大会导致整体线控不稳定,同时回吸真空量设置应合适,能够始终使金丝在键合过程中呈现直线送丝状态。
楔焊机调试最重要的是劈刀的垂直度调试和断丝参数的设置。楔焊难度大,对劈刀垂直度的要求极高,如果劈刀键合面与产品被键合面之间接触不充分,会严重影响键合效果。断丝参数的设置应以尽量形成最完整的焊点,同时又不会导致第二焊点后异常断线和跳线为宜。
2.2 劈刀选型
球焊一般选用陶瓷劈刀,劈刀选型的关键是劈刀前端的形状。如图 2 所示,球焊劈刀根据前端的形状变化分为很多种。对于键合效果来说,劈刀前端的整体形状变化越剧烈,键合稳定性越差。因此,没有深腔近壁键合需求的产品可首选常规款的劈刀。
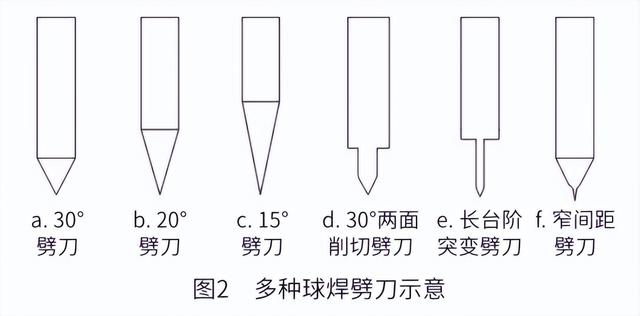
楔焊劈刀根据材料的不同也分为多种:硬金属陶瓷劈刀、软金属陶瓷劈刀、碳化钛劈刀、碳化钨劈刀及其他类合金钢劈刀。不同材质的劈刀键合特性也不同,工艺人员需要根据自身产品有针对性地进行选型。一般来说硬金属陶瓷劈刀耐脏、耐磨,但是键合效果差,适合可键合性高的产品;碳化钛和碳化钨劈刀性能相对均衡,适合大多数产品;其他类合金钢劈刀根据材料的不同会有各自不同的键合特性。工艺人员需要以产品的实际键合效果为选型依据,选择最适合自身产品的劈刀。如果自身产品的可键合性差,可以尝试采用某些特殊材质的劈
刀。例如,深圳市海志亿半导体工具有限公司生产的一款国产合金钢劈刀,在应对某些可键合性差的镀层时,其键合适配特性就表现得非常优异。
2.3 超声对键合的影响
键合设备最核心的部分是超声功能,包括超声触发和超声传递。
如图 3 所示,超声板中进行特定频率电压的发生与转化,最终形成交流电压作用到压电陶瓷换能器;压电陶瓷换能器经过交流电压的激励后,会根据电压幅度的变化产生前后的伸缩振动;前后的伸缩振动再通过劈刀作用到键合面,从而实现超声能量的传递,过程中能量的转化是电能转化为机械能[2] 。
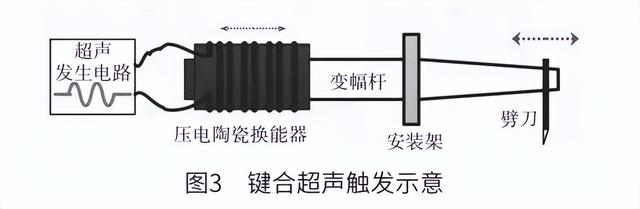
键合机的超声发生器一般分为 3 种:65 kHz 的低频超声发生器、110 kHz 的高频超声发生器和自动楔焊机用的 140 kHz 超声发生器,不同频率的超声发生器匹配不同的换能器。频率低的键合机通用广泛性更高、稳定性更强,指标窗口范围更广;频率越高的键合机指标窗口范围越窄,需要更强的阻抗匹配、劈刀选型和机械调试。
对于球焊来说,低频键合机在针对一些特殊的长柱状结构面的键合时,存在超声损耗的问题,需要采用高频的球焊机进行解决。除特殊情况外,球焊和楔焊都应在满足自身产品键合要求的情况下,尽量选择低频键合机,以降低使用难度。
2.4 温度对键合的影响
温度是金丝引线键合过程中重要的外加能量驱动,特别是对楔焊来说,键合机环形加热丝可以加热软化金丝,加热台可以加热活化产品键合面,均有利于产品的键合。需要注意的是,键合机加热丝的温度设置不能太高,太高会影响换能器的性能,而且加热丝不能碰触劈刀,否则将会影响超声的键合作用。
加热台的温度设置需要根据产品内部实际情况、锡焊的耐受温度以及各种器件的耐受温度等进行综合考量,在楔焊过程中尽量提高键合温度。此外,加热台需要定期进行测试,当显示温度和实际测试温度差异较大时,需要进行温度补偿校准。
2.5 压力对键合的影响
压力在键合过程中用于将劈刀的超声能量、加热丝和加热台热能进行综合驱动。影响压力效果的因素有机械结构稳定性和劈刀垂直度两个方面。如果是单纯采用机械弹簧进行手动调节压力,则应定期检查压力的稳定性和准确性;如果是电子校准的压力系统则须通过键合前的压力校准进行确认。另外,键合压力与键合超声功率之间有合适的匹配区间,并不是固定
不变的。键合压力过大会影响超声的运动,键合压力过小会导致超声作用不稳定,因此,工艺人员需要根据劈刀特性和最终的键合点情况综合考量设置合适的键合压力。在实际运用中经常犯的错误就是针对所有劈刀采用同样的固定键合压力,在键合过程中只是调节键合功率和键合时间的大小,此方法明显未考虑到不同材质的劈刀具有不同的键合特性。
键合过程中一定要保证劈刀的前端键合面与产品的被键合面充分接触、摩擦,以充分进行超声能量的传递。实际操作过程中可以在实验板上进行不穿线的空打,调节键合功率的大小并观察键合印迹的变化,如果键合印迹与劈刀端面的形状不相符,则判定劈刀垂直度有问题。
如图 4 所示,键合时的劈刀垂直度不良,会影响焊点的形状和可靠性。如果是设备的机械轴垂直度不良,可以用直角规进行换能器垂直度的调节;如果是劈刀本身的原因,则应更换合格的劈刀。经过实际经验验证,采购的劈刀会有一定比例存在垂直度不良的问题,工艺人员可以根据实际情况,对采购的劈刀进行入库前的检验筛选。
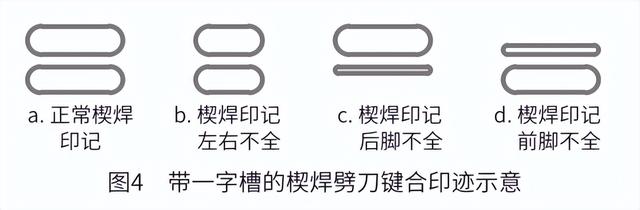
2.6 劈刀清洗
楔焊劈刀和球焊劈刀在使用一定时间后,前端键合面均会出现污染物和氧化膜层,在显微镜下观察表现为发黑、发灰。
如图 5 所示,球焊劈刀在使用一段时间后前端键合面粘污严重,进行清洗后又恢复到干净的状态。劈刀键合面出现污染物和氧化膜层会导致键合过程中抓线不牢,劈刀与线的相对滑动增大,有效作用到焊点上的超声能量减少,可能会出现打不上、打不牢、焊点不全等各种异常现象。对于楔焊来说这一问题则更加明显,劈刀粘污严重会直接导致无法键合。因此,劈刀使用一段时间后需要根据实际情况采用专门的劈刀清洗液进行清洗。劈刀清洗液分为碱性和酸性两种,目的都是去除劈刀键合面的污染物和氧化膜层。应根据劈刀的材质选择合适的清洗方法,清洗不当可能会导致劈刀腐蚀。另外,劈刀有使用寿命限制,如果在显微镜下观察到劈刀端面磨损严重,则应及时做废弃处理,磨损严重的劈刀不能反复清洗使用。
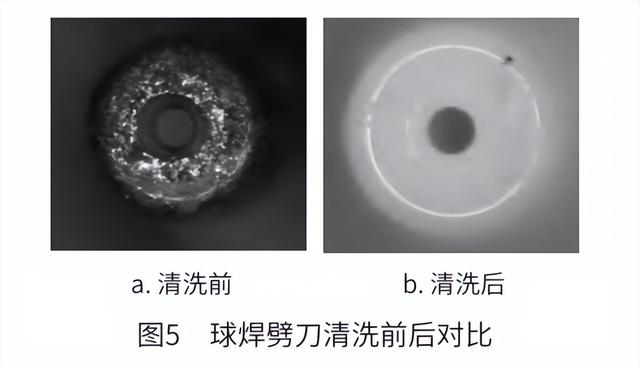
2.7 提升产品的可键合性
产品的可键合性主要体现在镀层的加工控制、组装过程中的镀层污染控制、键合前的等离子清洗3 个方面。
镀层的加工控制是提升可键合性最关键的措施:合适的电镀电流可以保证键合时镀层表面的附着力;合适的镀层厚度可以改善键合的指标;纯净单一的电镀槽环境可以改善镀层的软硬度,防止出现多种离子的电镀污染,使镀层光滑坚硬。当然,对整个电镀过程进行完全有效的控制非常困难,产品镀层难免会出现批次性的波动,因此对电镀产出品及时进行有效的可键合性测试跟踪非常有必要。
镀层在组装过程中需要经历焊接、胶粘、高温固化等各种工艺。其中,在控制组装过程中防止镀层表面的污染非常重要,需要根据各自的产品特点对组装过程加以控制。焊接完成后应有效清除镀层表面的松香等污染物,以及在胶粘过程中控制胶水印的污染。此外,在高温固化过程中选择厌氧洁净型烘箱,可减少镀层在高温下的氧化污染。
键合前的等离子清洗可以提高键合点的黏接力,增强键合可靠性。等离子清洗机一般有中频等离子清洗机和射频等离子清洗机两种。中频等离子清洗机单颗离子的能量大,整体密度低,更适合宏观的粗洗;射频等离子清洗机单颗离子的能量和整体密度都相对适中,更适合微观的改性清洗,一般应用于键合前镀层表面的清洗。
另外,也要重视键合金丝的存储,建议采用专用的氮气柜进行厌氧干燥环境下的密封保存。产品的可键合性提升属于微观概念,涉及的范围非常广,任何细小环节的改善都会对产品的可键合性起到提升效果。如果所有前端的过程均不加以有效控制,全部累积到最后的键合工序,那么键合难度会非常大,问题会难以解决。
3 键合生产过程中的管理问题
键合要求高,难度大,属于关键控制工序,键合生产过程中的管理问题同样需要引起高度重视,主要体现在以下 4 个方面。
(1)冗长繁杂的过程记录。一味追求书面的严谨性将导致实际生产过程很难操作,书面的过程记录时间占比太大,在最终操作层面得到的结果往往是失真的。
(2)操作人员缺乏对键合本质和键合设备原理的基础认知。虽然实际生产过程受制于追求人员低成本和产品赶进度等现实要求,但是想办法提高操作员对于键合本质和键合设备原理的基础认知水平也有较高收益率,可以提高产品的质量水平和正向激励操作效率。
(3)键合设备混用。基于现实考量,键合设备往往是多人混用,很容易造成键合设备管理的混乱和失控,因此应设立键合设备专人专用制度。
(4)键合质量问题的处理措施。键合出问题可能是多个方面导致的,不进行充分的分析和预防措施的改进,而只是一味地处罚操作人员或者是重复进行产品返工,往往会导致操作人员发现问题后担心被处罚或者增加个人工作量而不敢上报,最终导致很多隐性质量问题的发生。
键合生产过程中的管理问题最容易被忽视,隐秘性更强,对键合生产的实际影响也较大。相较于管理人员单纯催生产进度的模式,采用键合综合能力强的人员进行专管的有效性会更强。
4 结论
金丝引线键合已经深入应用到电子组装类的各个行业,由金丝引线键合作为基础,又延伸出了金带键合、铝丝键合和铜丝键合等多种方式[3] 。键合效果的影响因素众多,在实际运用过程中不能有思维定式,如果简单直接地引用国外或者其他单位的相关工艺,很可能会存在不适用的情况。工艺人员需要以各自的实际情况为出发点,从细节上进行全面的分析处理。在半导体产业链国产化的趋势下,建议工艺人员优先选择国产相关键合设备与国产相关耗材,并在国产技术支持下,探寻更加有利于自身键合工艺研究和发展的道路。