南极熊导读:随着产业应用的深入和规模的扩大,国内金属3D打印厂商开始各显神通。零件顺利成形是增材制造最基本的要求。然而受制于金属粉末床熔融技术极高的冷却速度特性,成形过程将产生很大内应力,导致零件极易产生形变。特别是工件的悬空结构区域,其悬空结构的翘曲变形导致打印失败的难题,经常困扰着工件设计人员。经过持续创新自主研发,目前,工业级3D打印领航企业华曙高科已攻克倒圆锥结构、水平圆孔等特殊结构成形难度大的技术难题,成功实现倒圆锥结构20°-25°倾斜角的无限高度成形,无支撑一体成形的水平圆孔最大可达Φ50mm。
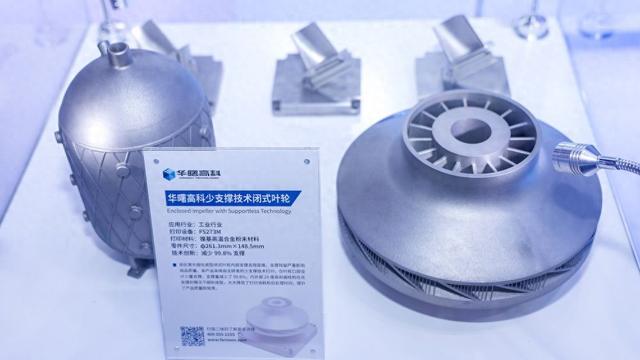
华曙高科于2023年在上海TCT亚洲展上现场展示了金属3D打印少支撑技术,并实现航空航天、汽车等行业关键复杂结构件高效率、高质量、批量化无支撑打印。该技术显著提升了金属3D打印低角度成形能力。
金属增材制造面临支撑设计难题合理的结构设计、合适的成形工艺是保证零件顺利成形的关键因素。在金属增材制造领域,为了使悬空结构顺利成型,通常需要添加额外的支撑结构,尤其是低悬空角度区域,业内通常将倾斜角45度以下的悬空区域添加支撑,以降低零件成形过程中失败的风险。首先,打印支撑需要耗费额外的粉末材料、增加额外的打印时间、提升后处理工序的难度和工作量,某些支撑无法去除,且易导致工件损伤而无法使用。其次,为了减少支撑数量并保证支撑能被去除,设计师不得不更多地考虑增材制造的工艺特性,做一些面向增材制造的结构修改,这在一定程度上给设计带来了更多约束条件。因此,改进成形工艺,提升材料和工艺的低角度成形能力意义重大。特殊结构实现无支撑华曙高科认为,成形能力受材料、层厚、工艺参数等因素的影响显著,且对于相同倾斜角的不同结构零件,其成形难度本身也会有较大的区别。例如同样倾斜角的倒圆锥与正空心圆锥,前者成形要相对更困难。因此,对于材料和工艺开发人员而言,建立成形能力的验证标准是非常必要的。华曙高科为材料成形工艺优化做了很多前瞻性研发工作,经过多年技术沉淀和创新研发,依托自研切片软件,采用自适应智能扫描策略,精准控制能量输入和零件局部热量,在保证零件致密性的前提下,其成形能力相对于传统扫描技术明显提升。
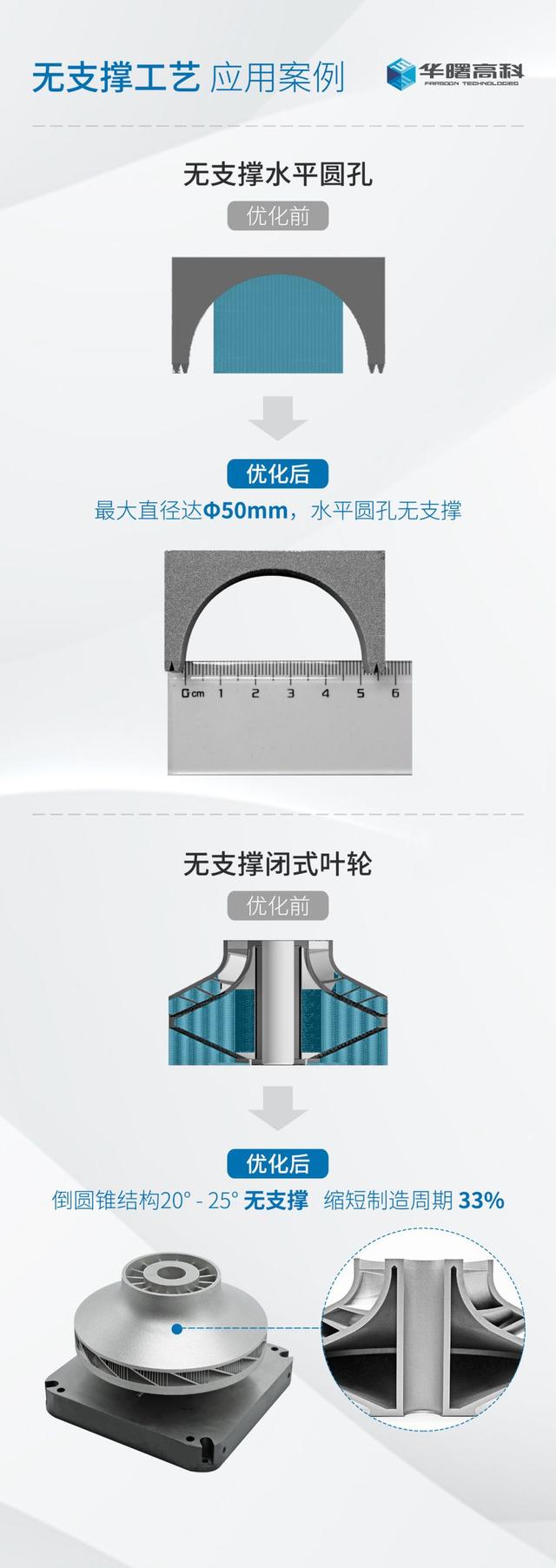
经过持续创新自主研发,华曙高科攻克倒圆锥结构、水平圆孔等特殊结构成形难度大的技术难题,成功实现倒圆锥结构20°-25°倾斜角的无限高度成形,无支撑一体成形的水平圆孔最大可达Φ50mm。工艺优化使此类零件不仅减少支撑数量,还提升了工件设计自由度,降低了对零件后处理的要求。超10种应用已批量生产华曙高科始终致力于推进粉末床熔融技术的应用,以解决用户的实际问题为导向,不断推进技术迭代升级。少支撑技术已应用于数十种工件并实现批量生产,材料涵盖钛合金、高温合金、铝合金、不锈钢等,典型应用包括燃料罐、闭式叶轮、阀体、喷嘴等零件,最大尺寸工件超过450mm。
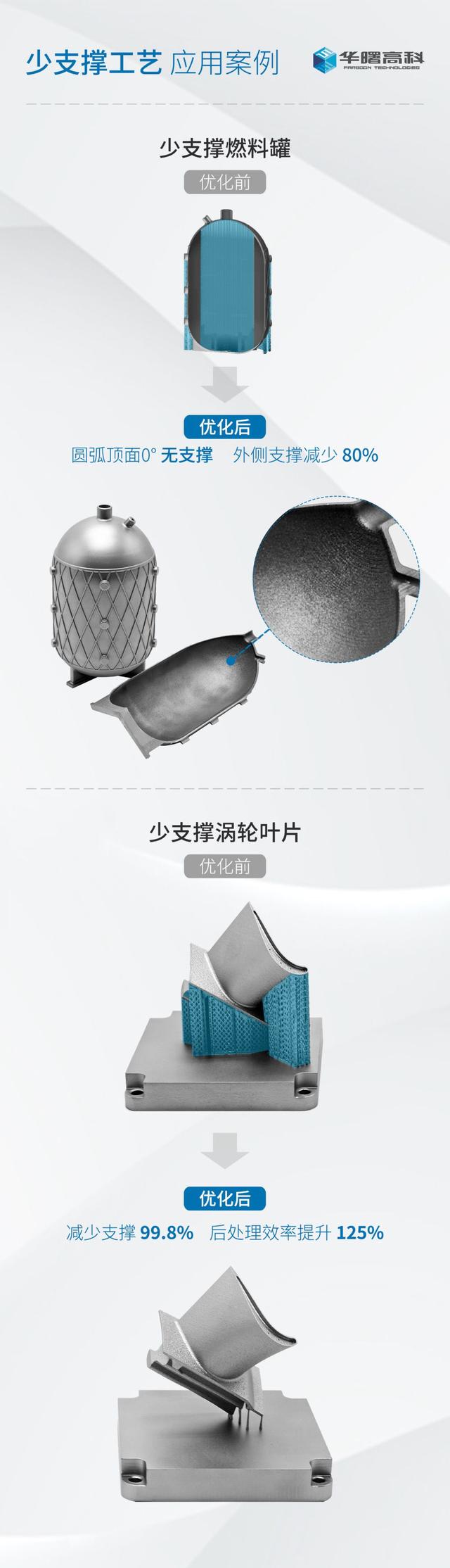
少支撑/无支撑工艺三大优势缩短生产及后处理时间,降低生产成本。以直径约130mm,高度约50mm的IN718材料闭式叶轮为例,打印时间可缩短33%,成本可降低约25%以上。对于支撑量更多的零件可节约更多时间及成本。

提升产品质量。支撑与工件结合处易产生冶金缺陷,去除支撑时易损伤工件本体,产生的碎屑若进入流道等狭腔结构,容易形成多余物,减少支撑量都能有效减少这些不利因素。提升设计自由度。突破传统45°成形角度限制,显著拓宽应用场景。如一些小尺寸零件具有复杂内腔结构,采用一般打印策略需修改设计或添加大量支撑,内腔易存在局部变形问题,如采用无支撑策略,可顺利成形。华曙高科认为,金属增材制造技术仍有很大潜力待挖掘。未来将持续对金属增材制造技术潜力和创新工艺进行深入研究与挖掘,进一步释放其创新活力和发展空间。欢迎有意向的先锋客户与其联系,共同探讨实践少支撑技术应用,推动3D打印产业化发展。