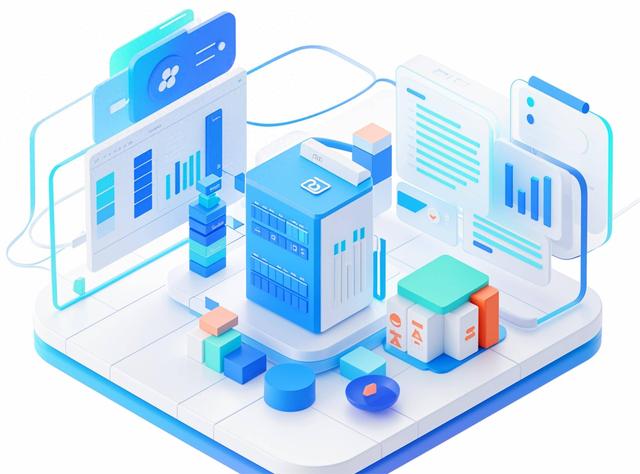
设备管理系统要实现预测性维护与故障预防,需借助数据收集与分析、智能算法、维护策略制定等多方面的技术和方法,以下是具体介绍:
1.数据收集与整合部署传感器:在设备关键部位安装各类传感器,如温度、振动、压力、电流等传感器,实时采集设备运行的状态数据。例如,在电机上安装振动传感器和温度传感器,可实时监测电机的振动幅度和温度变化,为判断电机运行状态提供数据支持。数据集成:将来自不同传感器、设备控制系统以及其他相关系统(如生产管理系统、质量管理系统等)的数据进行集成,建立统一的设备数据中心。这样可以全面、综合地了解设备的运行状况,避免数据孤岛,为后续的分析和决策提供完整的数据基础。
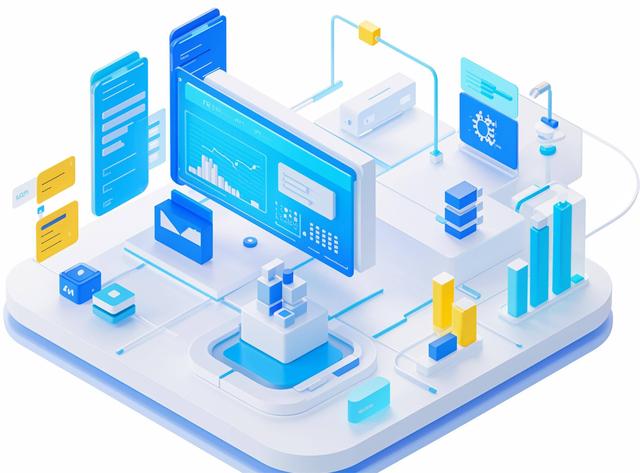
2.数据分析与建模建立设备模型:根据设备的工作原理、结构特点以及历史运行数据,建立设备的数学模型或物理模型。通过模型模拟设备在不同工况下的运行状态,预测设备性能变化趋势。以数控机床为例,可建立其加工精度与各轴运动参数之间的数学模型,通过分析模型参数变化来预测加工精度的变化。运用数据分析算法:利用机器学习、深度学习等数据分析算法,对大量的设备运行数据进行挖掘和分析。常见的算法包括决策树、支持向量机、神经网络等。通过这些算法,可以发现数据中隐藏的规律和特征,识别设备潜在的故障模式和异常行为。例如,基于神经网络算法建立设备故障预测模型,通过对大量历史故障数据和正常运行数据的学习,实现对设备未来故障的预测。3.设定预警阈值确定关键指标:根据设备的性能要求、运行特点以及历史故障数据,确定用于监测设备运行状态的关键指标。这些指标通常是与设备故障密切相关的参数,如设备的振动烈度、温度上升速率、零部件的磨损量等。设定阈值范围:为每个关键指标设定合理的预警阈值和报警阈值。预警阈值一般设定在设备正常运行范围与故障临界值之间,当指标数据超过预警阈值时,表明设备可能存在潜在问题,需要密切关注;当数据超过报警阈值时,则表示设备已经出现严重异常,需要立即采取措施进行处理。阈值的设定需要结合设备的实际运行情况和历史数据进行反复验证和调整,以确保其准确性和可靠性。
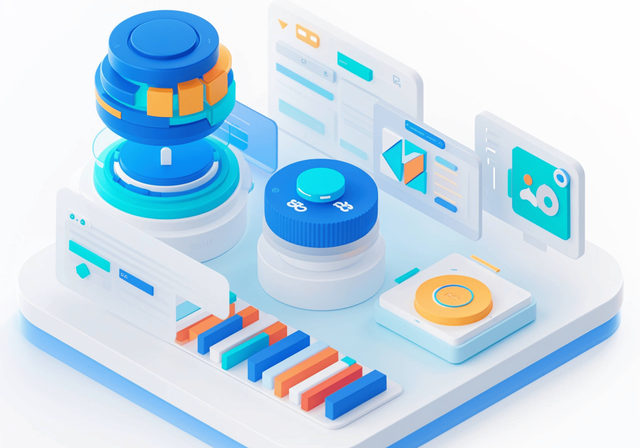
4.智能预警与通知实时监测与预警:设备管理系统实时监测设备运行数据,当关键指标数据达到预警阈值时,系统自动发出预警信息。预警信息可以通过多种方式呈现,如系统界面弹出窗口、电子邮件、短信、手机应用推送等,以便相关人员及时获取设备异常信息。智能通知与协同:根据预设的通知规则,系统将预警信息准确地发送给相应的设备维护人员、生产管理人员等相关人员。同时,系统还可以实现多部门之间的协同工作,例如,当设备出现故障预警时,系统自动通知设备维护部门准备维修资源,同时告知生产部门调整生产计划,以减少设备故障对生产的影响。5.维护策略制定与优化制定预测性维护计划:基于设备的故障预测结果和运行状态评估,制定个性化的预测性维护计划。维护计划应包括维护内容、维护时间、维护人员、所需备件等详细信息。例如,对于预测到即将出现故障的设备零部件,提前安排更换计划,确保在设备出现故障前完成维护工作,避免设备停机造成生产损失。动态优化维护策略:随着设备运行数据的不断积累和设备实际运行情况的变化,定期对维护策略进行评估和优化。根据新的数据和信息,调整维护计划的时间间隔、维护内容等,使维护策略更加符合设备的实际需求,提高维护效率和效果。
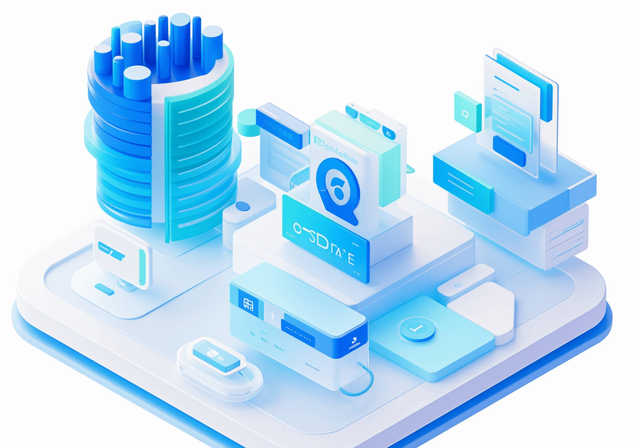
6.知识管理与经验积累建立故障案例库:将设备发生过的故障案例进行整理和记录,建立故障案例库。案例库中应包括故障现象、故障原因、诊断方法、解决措施等详细信息。通过对故障案例库的学习和分析,维护人员可以快速了解设备常见故障模式和解决方法,提高故障诊断和处理能力。经验传承与共享:鼓励设备维护人员和技术专家分享自己的经验和知识,通过组织培训、技术交流会议、在线论坛等方式,实现企业内部知识的传承和共享。同时,利用人工智能技术中的知识图谱等方法,将设备维护领域的专家知识进行结构化和数字化处理,形成可复用的知识资源,为设备管理系统提供智能决策支持。