纽波特纽斯造船厂 NNS的造船厂,在新建的“杰拉尔德·R·福特”级航空母舰“企业号” CVN-80上,安装了首个采用增材制造,俗称D打印的技术,制造的阀门歧管组件,安装在泵房内。阀门歧管组件用于将单一来源的液体分配到舰上的多个位置,随着该技术在“企业号”的应用,他们还计划安装在“多里斯·米勒”号 CVN 81上的类似组件也将采用增材制造技术,而非传统铸造方法。
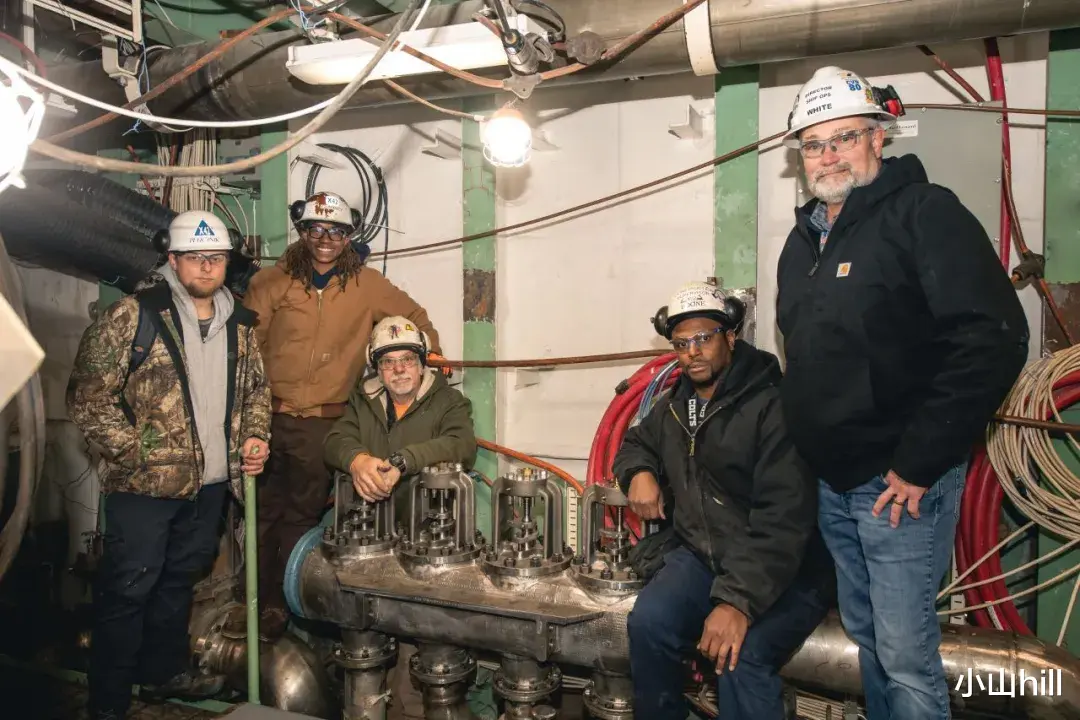
他们自己介绍:正是这一工艺变革从而降低工期风险并提高了相应零件的生产效率。截至目前,造船厂已经为新建舰艇和现役舰艇生产并安装了超过55个增材制造零部件,并计划在今年额外安装超过200个零部件。从中看到部分零件制造工艺变革也是一个逐步尝试的过程。
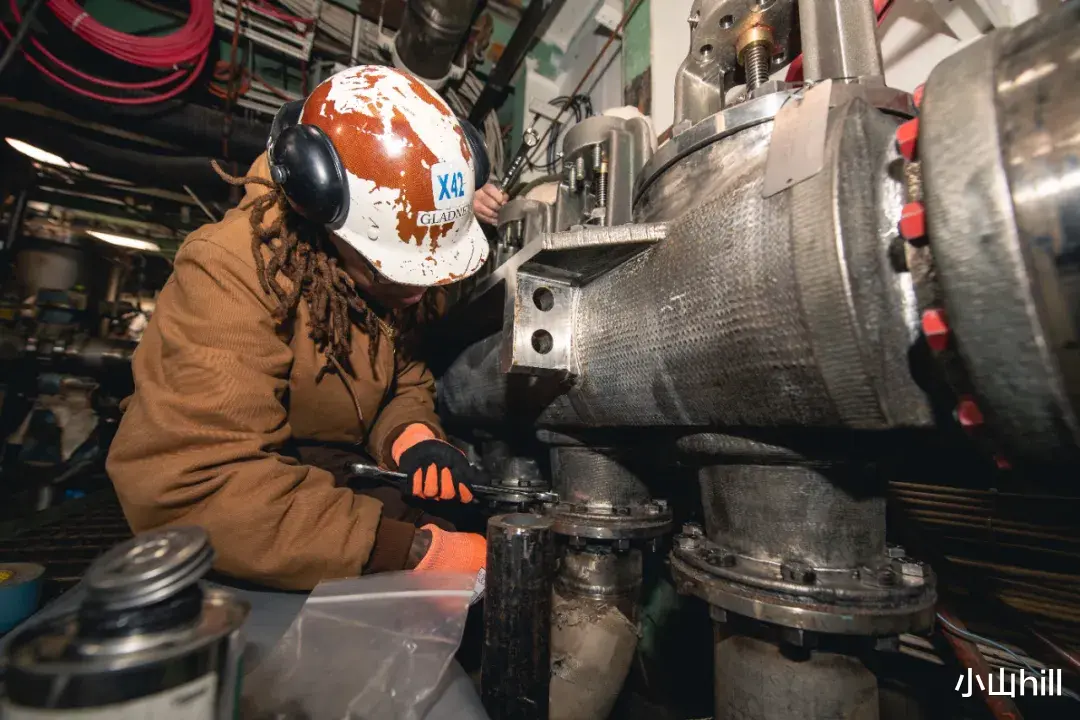
3D Systems 公司提供给纽波特纽斯造船厂的3D打印设备,能够实现±20-50微米(约0.001英寸)的精度和重复性,可以制造出传统加工方法无法加工的复杂形状。该3D打印机可使用的现成OEM材料包括:铝合金 AlSi12,马氏体不锈钢等,和多种钛合金。
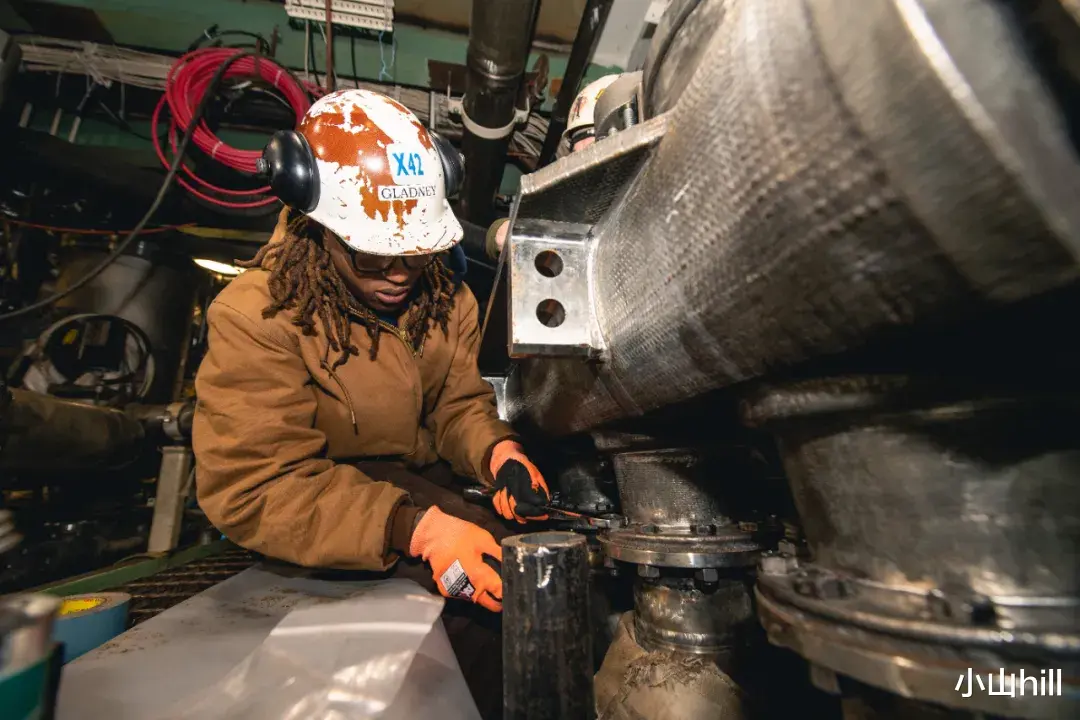
经过认证的3D打印零部件有望缩短舰艇建造和交付周期,减少生产前置时间,并提高关键部件的制造质量。美国海军长期以来一直对使用增材制造进行零件更换感兴趣,因为增材制造可以提供一种经济高效且更快速的方式来更换损坏的零件,尤其是当他们的舰船远离陆地,在海上航行时,设备维护保养过程中,往往急需零件应急。增材技术不失为一种不错的临时解决方案。
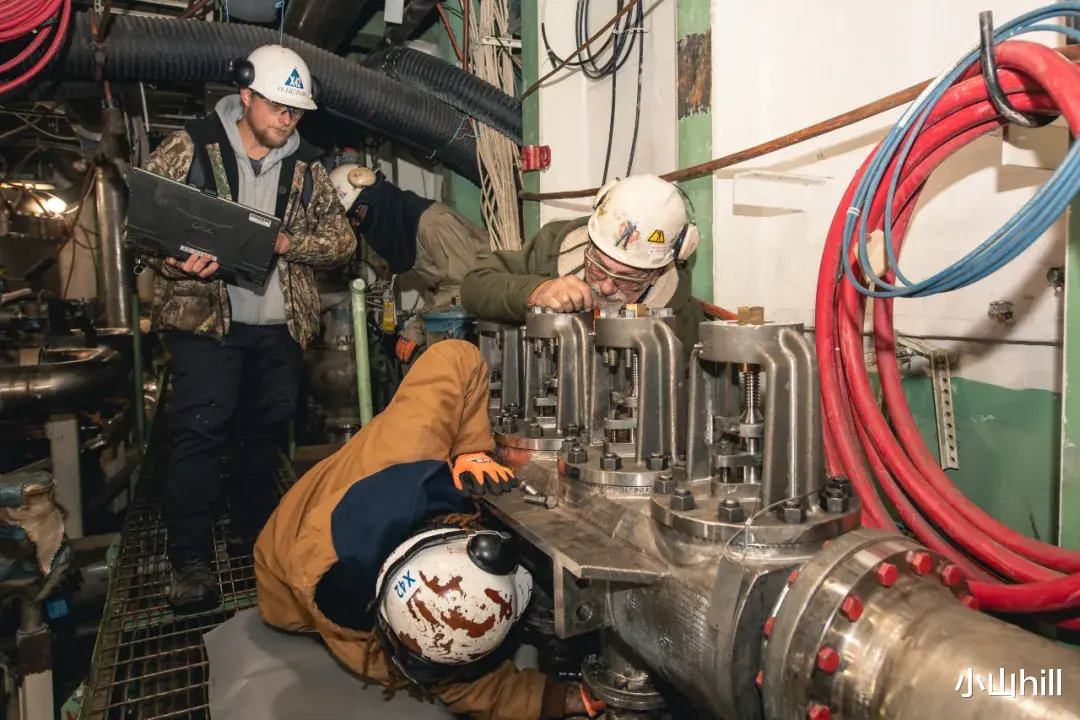
这也算一次工艺的合理选择,联合技术公司早年强调适宜技术适宜工艺,包括过度加工也是浪费,泵类箱体类零件通常先制作铸件毛坯,前期还需开发铸造用铝模,有了铸件毛坯后进行机加工,最后探伤捡漏,如果有结构复杂,尤其是加工死角,需要专用工装夹具,专门设计刀具加工,这又涉及刀具开发等,工程量之巨大和周期之长可想而知。而舰船上此类零件,通常批量又不大。
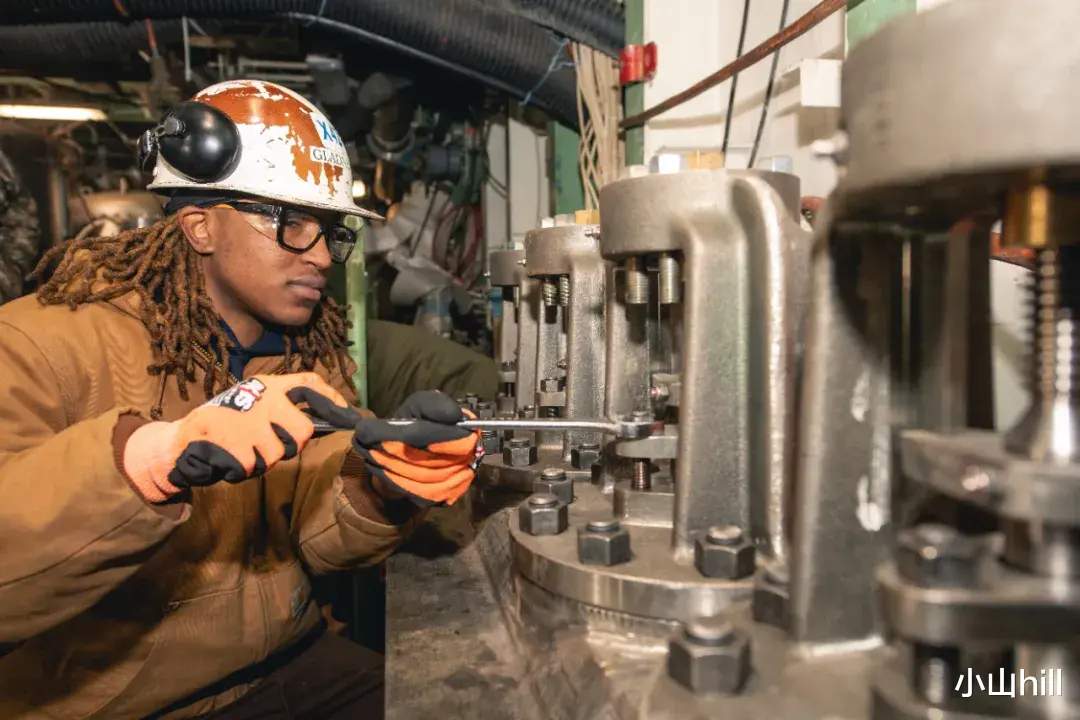
这类零件,精度对于精密零件而言可忽略,尤其是形位公差,属于比较简单的,没有严格的空间位置精度,关注点通常是O型圈槽等密封方面的细节,如槽的深度,槽三个面的光洁度,确保密封件工作完美,仅此而已。3D 增材工艺能减少工艺步骤,尤其是铸件,而且铸件工艺自带拔模斜度等,有一定材料浪费,如果发生装配干涉,有时候还需额外机加工。
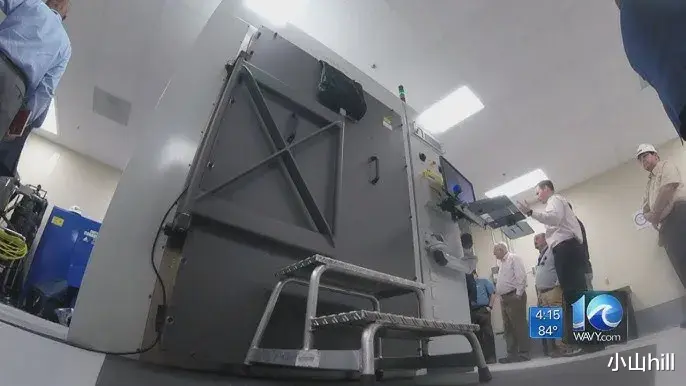
工艺选择还关联是否是压力容器,如果没有太大压力,那就再合适不过了。总之工艺选择是一门学科,每一种加工工艺都有其优缺点,合适的工艺选择,工艺路线,基于所在Facility 的现有设备,生产批量,经济与否,交付周期,经验和外部协作能力等。所以美国航母这类零件,批量小,介质工况一般,没太大管路压力,精度要求一般,体积不大,采用增材打印替换铸造是一个不错的方案。
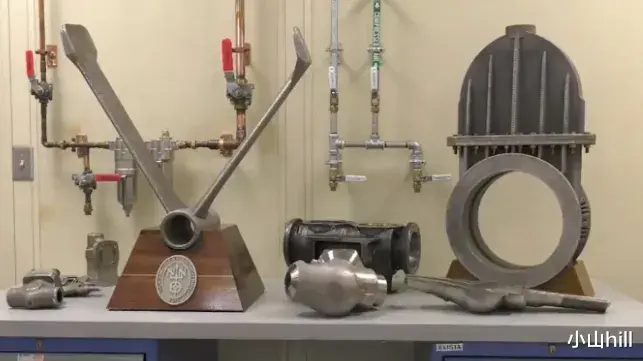