摘要:
在过去的十年里,印制电路板(PCB)上通孔元件的数量大幅下降。电子产品的小型化导致了通孔技术(THT)的应用越来越少,而且通孔元件的引线间距越来越细。因此,这些元件的焊接也从波峰焊接转变为点对点的选择性焊接。当表面贴装元件(SMD)的位置非常接近PCB布局上的通孔(THT)元件时,焊接这些小的、细间距的元件是一个挑战。这项研究是与一家大型汽车EMS客户合作完成的,它定义了细间距元件的通孔焊接的工艺窗口。它确定了焊接的可行性,并定义了布局设计参数,使得在有SMD和其他元件的组件上进行焊接成为可能。
关键词:选择焊,细间距,SMD元件
引言点对点选择性焊接有三个主要目标:良好的通孔填充、无桥接和最低程度的锡球。在电路板设计中有许多参数都会影响焊接效果。通孔的直径与元件的引线尺寸有关。如果通孔直径太小,引线不能顺利插入,可能会损坏。当通孔直径太大时,间隙太大,以致于无法保持焊料,焊料可能会流出。
桥接受焊盘和通孔直径、引线伸出长度、引线直径/尺寸和引线间距的影响。间距越小,实现无桥接焊接的挑战就越大。有些引线是圆的,有些是方的。该设计是否会产生桥接取决于焊料的毛细管作用。这是焊料在重力等外力的帮助下在狭窄空间内流动的能力。焊料的性能,如温度和流动性,对毛细管作用有影响。
锡球是另一个挑战。不管什么情况,如果在离开焊锡波时,锡球没有粘附在焊料掩膜上,这个问题基本上是可以消除的。选择最佳的焊料掩模是使电路板设计更稳健的最佳解决方案。
测试板焊接细间距元件的主要挑战是无桥接焊接。对于一些高热容组件,通孔填充也可能是很困难的。为了了解不同设计参数的影响,制作了不同层数(2、4、6、8和10层)的测试板,以研究焊料的通孔填充情况。这个测试板包括了扩大焊接工艺窗口可能需要支持的所有设计特性。这些特性包括焊料掩模、偷锡焊盘、适用于五个不同间距(1.00、1.27、1.50、1.75和2.00mm)的不同通孔和焊盘直径。由于可焊性受金属表面状况的影响,本文对两种不同的金属化方法浸渍Sn和CuOSP(有机可焊性保护剂)进行了比较。测试板尺寸为285×184×1.6mm3。组件上总共有3370个通孔。为了保持基板的平整,使用了一个托盘。
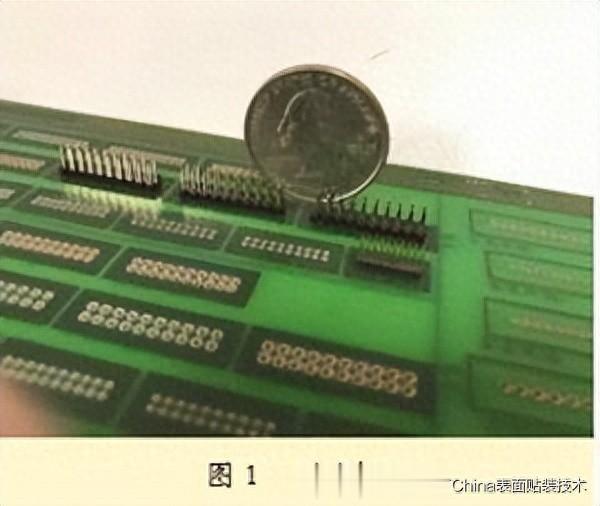
测试是在一台选择性点对点焊接机上进行的。这台设备有一个高频滴喷式焊剂装置,一个红外加热器和一个磁力泵驱动的焊锡锅。焊料喷嘴是研究的参数之一。在试验中,将可润湿喷嘴与不可润湿喷嘴进行了比较。为了避免桥接,在焊料喷嘴后面安装了一个焊料排放调节器(SDC)。这个装置在连接器的引线之间吹热空气。气体温度远高于焊料的熔点,流量固定在7L/min。实验过程中焊料温度为300℃,合金为Sn3.0Ag0.5Cu。预热器功率为45%,持续51s,使基板上表面温度为120℃。
实验设计--通孔填充第一个实验重点是通孔填充。选择了一个具有五个不同参数的全因子试验设计,这些参数在历史上已经证明对可焊性有影响。这些因素包括焊剂和焊接参数。在两个水平上选择焊剂量和焊剂类型。拖焊速度(接触时间)、喷嘴类型和焊料角度是其他因素。尽管焊料温度是影响通孔填充的另一个因素,但这里保持了恒定的300℃。预热设置也保持恒定不变(参见上面的数据)。
测试板焊接区域有不同的间距、通孔和焊盘尺寸、铜层、偷锡焊盘和去除的阻焊剂。这项实验的目的是给工程师提供正确的工具来设计电路板和工艺条件,使高热容电路板上的细间距连接器实现充分的通孔填充。根据IPC-A-610的要求,统计填充良好的通孔数。每块印制板上焊接360根引线。
基板的设计是为了显示不同之处。要在10铜层印制板上实现100%的通孔填充是非常困难的,可能不是对所有组件都是可行的。这个测试板的目的是找出极限。焊接了1.00、1.27和2.00mm的不同双排插针连接器,以及一个1.50mm的10根引线单排插针连接器。
有两个因素影响很大。焊剂量和铜层数。应该有足够的焊剂来支持焊料流入铜通孔。铜层的热容吸收了太多的热量,以至于焊料在到达基板顶部之前就凝固了。结论:较高的热容需要更高活性的焊剂。在焊剂量与铜层之间也存在相互作用。图3显示,有足够的焊剂活性,所有的通孔都将有很好的通孔填充。甚至10层铜层的通孔。
不可润湿的喷嘴使焊料朝一个方向流动。在相同的拖焊速度下,与基板的接触时间更长,有更多的能量迫使焊料进入通孔内。因此,不可润湿喷嘴表现出更好的通孔填充。
相对于通孔填充而言,浸渍Sn是一个比较好的基板表面涂饰。润湿性略好于CuOSP。由于电路板在焊接前回流两次,铜可能会有一些小的氧化层,影响润湿速度。
通孔直径也很重要。基板对于不同间距有着不同的通孔直径。对于1.27和1.50mm间距,0.80mm通孔直径的通孔填充效果最好。对于2.00mm间距,首选通孔直径为1.10mm。
所有元件都是方形引线。间距为1.27、1.50和2.00mm时,尺寸分别为0.35、0.40和0.50。

除了良好的通孔填充外,避免焊点桥接也是至关重要的。虽然桥接可以通过元件上较小的突出长度来减少,但是需要一个去除桥接的工具来消除此缺陷。由于使用者对突出长度没有影响,而且切割所有元件的成本非常高,因此设备必须处理较长的引线。经验表明,所有间距小于1.75mm的件都需要一个SDC装置。SDC装置在引线离开液态焊料的地方吹热风。
在实验中,有一些附加的参数对桥接有影响。设计偷锡焊盘的目的就是消除桥接,但在一些无铅应用中,这一好处尚未得到证实。
利用实验设计的数据,还可以检查桥接。结果如图6所示。分数越高越好。360分意味着没有桥接。
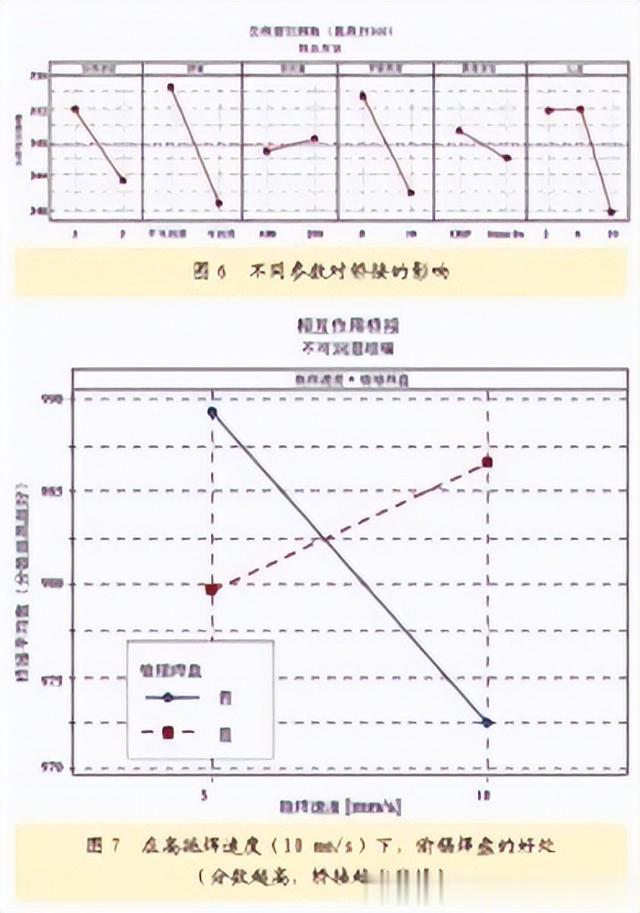
数据显示,采用不可润湿喷嘴的桥接较少。拖焊速度以3mm/s为佳。倾斜的传送带对通孔填充有利,但对桥接有一定的负面影响。这可以通过改变SDC角来改善,优化SDC角实现平面焊接。
铜层的影响是显著的。显然,10层铜层结构吸收了来自焊接区的大量热量,使焊料更快地凝固,从而形成桥接。
另外,我们还做了一个实验来研究偷锡焊盘和不同焊剂的影响。焊盘直径是另一个被研究的因素。由于SDC是消除桥接的有力工具,因此导线突出长度的影响并不显著。如果不使用SDC,则导线突出部分必须较短,以避免桥接。
对于非常细的间距,焊盘直径是至关重要的。间距为1.27mm,焊盘外径为1.00mm,缺陷最低。直径越大,对桥接越敏感。对于2.00mm间距,1.50~1.70mm的焊盘外径没有显著差异。1.80和1.90mm的焊盘外径对桥接更为敏感。
实验设计表明,在较高的焊接速度下,偷锡焊盘可以减少桥接。在较低的焊接速度下,焊料会自行排出。
偷锡焊盘使基板持有焊料时间更长。可润湿性喷嘴设计就是为了从基板上剥离焊料,避免桥接。在一些无铅焊料合金应用中,可润湿性喷嘴和偷锡焊盘的结合并不是很好。实验证实了这一点。