中国科学院金属研究所(以下简称金属所)研究员李殿中永远也忘不了2020年的一天当他走进某国内盾构机制造企业的仓库时眼前的一切给他的震撼彼时大型盾构机已实现大部分部件的国产化但最关键的核心部件——主轴承却长期依赖进口如果将大型盾构机比作一个人主轴承的作用堪比心脏当“心脏”被攥在别人手心盾构机制造企业所承受的压力以及为我国基础设施建设带来的潜在风险可想而知为了规避可能的“断供”盾构机制造企业只能不惜成本囤积上亿元的主轴承
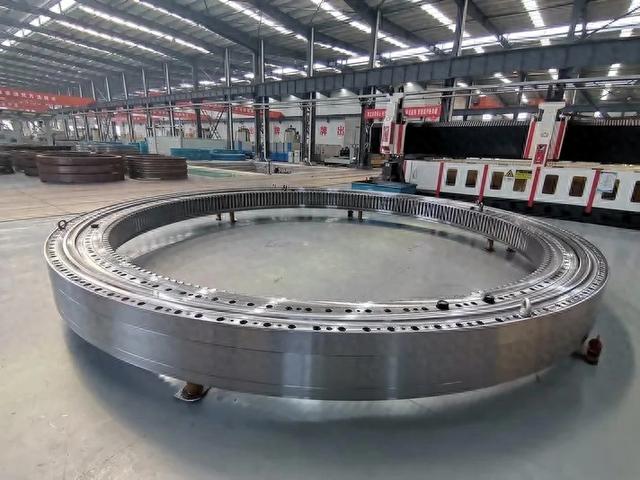
▲自研超大型盾构机用直径8米级主轴承。那段时间恰逢中国科学院组织实施战略性先导科技专项调研中金属所团队意识到攻克主轴承的国产化问题给国产大型盾构机装上一颗“中国心”已刻不容缓但难度非比寻常科研人员总结研发主轴承必须克服三大困难其一大型主轴承最大直径达8米承载几万吨但加工精度却要达到微米级别其技术难度可想而知其二盾构机在施工过程中不能后退主轴承一旦出现问题将无法更换导致在实际应用场景中试验风险特别高其三大型主轴承的攻关链条特别长涉及结构设计、材料制备、加工装配等诸多环节关联到20多家单位仅制造过程就有130多道工序要解决这一问题必须从基础理论做起向上整合各研发生产链“也正因如此,就需要我们‘国家队’站出来”李殿中说2020年2月先导专项“高端轴承自主可控制造”正式启动一场新的“战役”就此打响
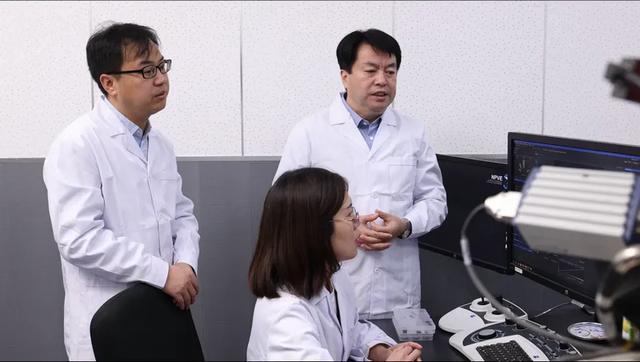
▲金属所研究员胡小强(左)、李殿中(右)在实验室。在此之前金属所科研人员对盾构机主轴承研究较少但他们与这项事业早有渊源自20世纪50年代起金属所几代科研人员接力攻关力图解决老大难问题——研发稀土钢所谓稀土钢即在钢材的制造过程中加入一定比例稀土元素从而改变钢材的某些特性这看似容易,实则困难重重直到2007年科研团队成功研发出“双低氧稀土钢”关键技术采用该技术研制出的稀土钢拉压疲劳寿命延长40多倍滚动接触非疲劳寿命提升40%稀土钢的问题被彻底解决这项技术后来成为大型盾构机主轴承攻关的重要基石尽管有了技术支撑但研究团队知道他们在设计盾构机主轴承上还没有太多经验正因如此他们从不放弃任何学习合作的机会当时受国外技术限制我国大型滚子的加工精度只能达到二级即直径误差不大于正负2.5微米但符合盾构机要求的滚子柱体直径误差不能大于正负1微米两者之间1.5微米的差距在科研团队的眼中却无异于一条“天堑”要跨过它只能联合企业攻关
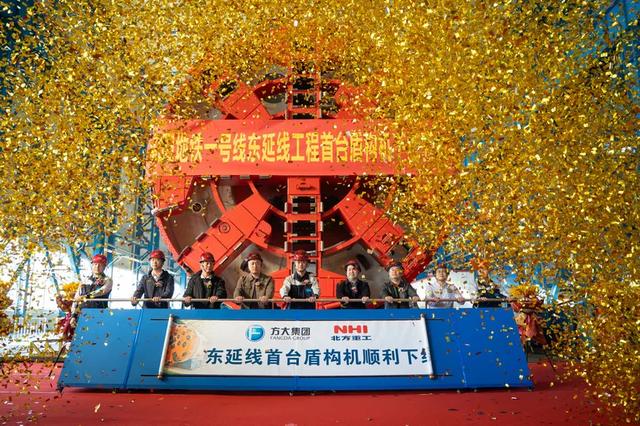
▲2021年11月,装有自研直径3米级主轴承的盾构机下线仪式。与金属所合作的企业此前从未加工过直径这么大、精度这么高的滚子起初,几乎每次技术升级尝试都失败以至于合作企业的现场负责人开始怀疑其工艺和生产线是否能实现加工要求经过反复论证和计算科研团队坚信其精度要求可以达到企业最终选择相信他们的论断最终完全符合要求的滚子被成功加工出来由此,我国企业彻底掌握了大型滚子的一级精度加工技术耗时3年20多家科研机构和企业通力合作12项核心关键技术问题先后被解决使用1467.4吨稀土轴承钢研究团队成功生产出直径3米级到8米级共10套4个型号国产盾构机主轴承2021年11月装有自研直径3米主轴承的盾构机正式下线并且在沈阳地铁工程成功应用2022年9月30日超大型盾构机用直径8米主轴承验收合格标志着由金属所领衔的“高端轴承自主可控制造”先导专项任务圆满完成
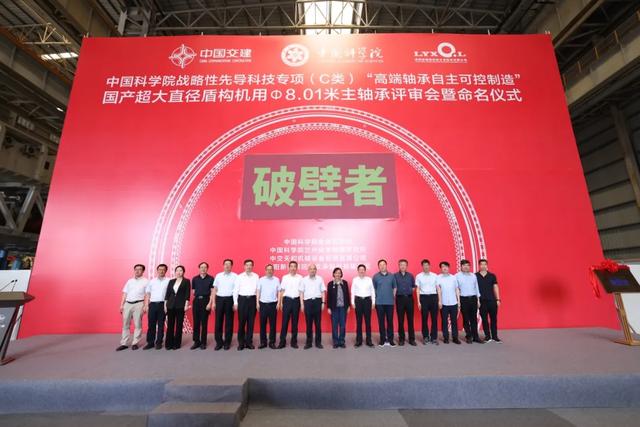
▲自研的直径8.01米主轴承通过评审并被正式命名为“破壁者”。在这一过程中高效协同的管理架构最大化激发了科研人员的工作热情如今大型盾构机主轴承项目已尘埃落定但这并不代表所有的任务都已完成正如李殿中所言针对“卡脖子”问题的科研只有落实到产业构建完整的产业生态链才能彻底解决问题目前,主轴承产业化基地正式落地为打通盾构机国产化“最后一公里” 奠定坚实基础来源:中国科学报责任编辑:曹旸