AEC-Q006 标准解读及可靠性要求研究
吴钰凤 沈殷 吴仕煌 郑宇 王斌 王之哲
(工业和信息化部电子第五研究所)
摘要:
探讨了铜线键合器件在汽车电子认证中的可靠性要求。铜线键合器件在电子封装域已得到一定的推广及应用,然而,相比金线键合,由于铜线特殊的材料属性和键合工艺,其可靠应用面临一定的挑战。为了确保汽车电子系统的高可靠性和稳定性,汽车电子委员会制定了一系列标准和认证要求,其中针对铜线键合器件于2016年发布了AEC-Q006标准。对AEC-Q006标准进行了解读,重点探讨了铜线器件在汽车电子认证中的可靠性要求,并对可靠性试验中的主要失效机制进行分析,以帮助厂商和工程师在设计、制造和检测认证铜线键合器件的过程中能够确保器件满足标准的要求。
0引言
随着汽车电子技术的快速发展和智能化水平的提高,车载电子系统在现代汽车中起着愈发重要的作用。这些电子系统涵盖了从发动机控制、驾驶辅助到娱乐和安全等多个方面。在这些系统中,集成电路器件起着关键的作用,而键合技术作为集成电路封装过程中的重要环节,直接影响着器件的可靠性和性能。在不同的应用领域中,金线和铜线键合器件都扮演着重要角色。
1铜线键合的优势及面临的挑战和问题
铜线键合器件作为一种新兴的键合方式,具备许多优势。首先,铜线具有优异的导电性能,其低电阻率能够提供更好的电流传输能力,这在高功率电子器件和汽车电子中尤为重要。其次,铜线的热导率较高,有助于散热,降低器件的工作温度,提高整体可靠性。再者,相对于金线,铜线具有成本更低的优势,有助于降低生产成本并推动市场普及。
尽管铜线键合器件具备许多优势,但仍然面临一些挑战和问题。首先,市场普及是一个关键问题,相较于传统的金线键合器件,铜线键合器件在市场上的应用相对较新,因此受到一些行业习惯和标准的限制。为了广泛推广和应用铜线键合器件,需要推动行业的变革和认可,并逐步建立相应的标准和规范。其次,汽车电子应用是铜线键合器件面临的另一个重要挑战。汽车电子领域对电子器件的可靠性和稳定性要求极高,需在恶劣的环境条件下工作,如高温、高湿、振动和冲击等。以塑封铜线键合器件为例,需要满足汽车行业的特殊要求,如耐高温和耐湿热,以确保其在汽车电子系统中的可靠性和使用寿命。最后,对铜线键合器件进行可靠性评估也是当前面临的挑战之一。为了验证和保证铜线键合器件在各种应力环境下的可靠性,需要开展一系列的可靠性评估和测试,包括温度循环、湿热应力等测试,并结合物理(破坏性/非破坏性)分析进行评估。此外,还需要建立相应的可靠性模型和方法,以提前预测和评估器件在实际应用中的寿命和失效机制。
针对车规元器件采用铜线键合工艺,汽车电子委员会(AEC:AutomotiveElectronicsCouncil)于2016年发布了AEC-Q006-Rev-A标准,制定车规元器件使用铜线互连部件的合格要求,以验证铜线键合的质量水平和可靠性。本文将重点解读AEC-Q006标准与AEC-Q100、AEC-Q101标准相比,针对铜线键合器件规定的可靠性评价要求。
2AEC-Q006标准解读
AEC-Q006是由AEC制定的一项针对汽车电子器件可靠性的标准,旨在明确规定铜线键合器件的可靠性最低资格要求。该标准涵盖了铜线器件在温度循环、湿热应力和高温存储等条件下的可靠性测试要求。与应用于金线键合器件的AEC-Q100和AEC-Q101标准相比,AEC-Q006对铜线器件的可靠性试验要求更为严苛,具体如表1所示。
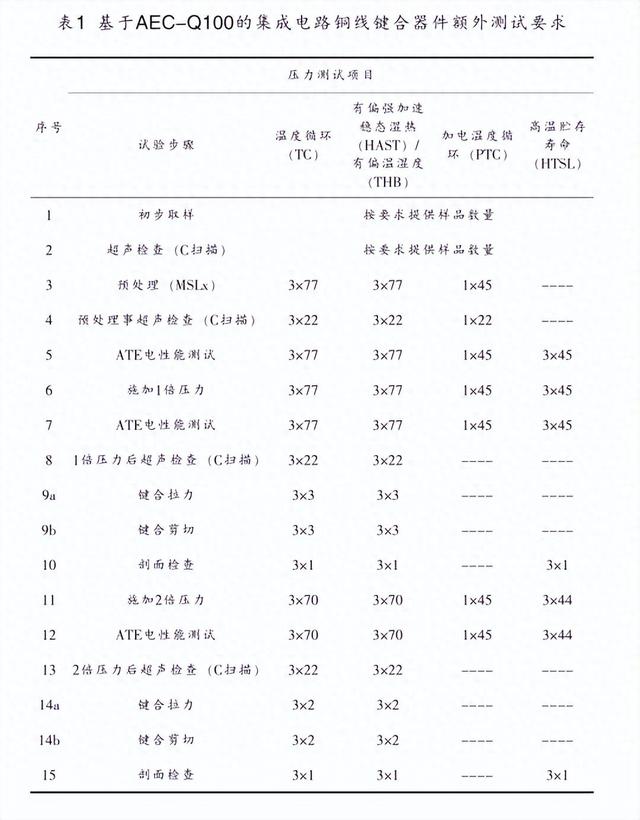
标准中明确规定了可靠性测试的条件、持续时间和相关的物理分析。通过指定的压力测试,该标准旨在确保铜线键合器件能够在应用中提供一定水平的质量和可靠性。为了满足标准的要求,铜线键合器件的设计和制造过程需要遵循严格的可靠性设计原则。以集成电路器件认证为例,AEC-Q006中对TC、HAST/THB、PTC和HTSL试验提出了额外要求,TC、HAST/THB、PTC、HTSL试验需做两倍应力(2X),即应力累积时间为金线键合器件的两倍;同时,也提出需增加进行CSAM、键合剪切/拉力和剖面检查等物理分析试验,以完善整体的可靠性评估流程方案。
2.1温度循环试验和加电温度循环试验
TC旨在评估器件在温度变化环境下的耐久性和稳定性;PTC旨在评估器件在通电/断电和温度变化环境下的耐久性和稳定性。在AEC-Q006标准中,规定了这两项试验均需进行2次应力叠加,以考核铜线互连的可靠性。在AEC-Q100和AEC-Q101标准中,这两项试验均只要求进行1次应力试验,与之相比,AEC-Q006标准对于铜线键合产品在TC和PTC上要求更为严苛。
从失效机理角度分析,在TC和PTC中,铜线(1.7×10-5℃)与硅芯片(3.0×10-6℃)之间的热膨胀系数(CTE:CoefficientofThermalExpansion)不匹配,导致它们在温度变化过程中出现不同的热膨胀和收缩率。在热循环(150℃)期间,发生不同的热膨胀率,在冷循环(-55℃)期间则产生不同的收缩率。这种CTE不匹配引起了界面处的差异膨胀和应力集中现象。微裂纹可能在键合球与铝焊盘之间的IMC处形成。
图2a为由于铜球键合与铝焊盘的CTE不匹配而导致的键合微裂纹[1]。这些微裂纹在温度循环过程中逐渐扩展,最终导致键合点的失效。
另外,环氧模塑料(模塑料)与铜线之间的CTE不匹配也可能导致在温度循环期间出现铜键合线颈部和楔形键合处的裂纹。由于电子封装中广泛使用了许多具有不同CTE和玻璃化温度(Tg)的模塑料,这些材料与铜线之间存在不同的相互作用,导致线颈部出现不同程度的裂纹。图2b为模塑料与铜线之间的CTE不匹配而导致的颈部微裂纹[2]。
故在TC和PTC这两项试验中,对铜线键合期间提出更加严苛的可靠性评价要求是有必要的。
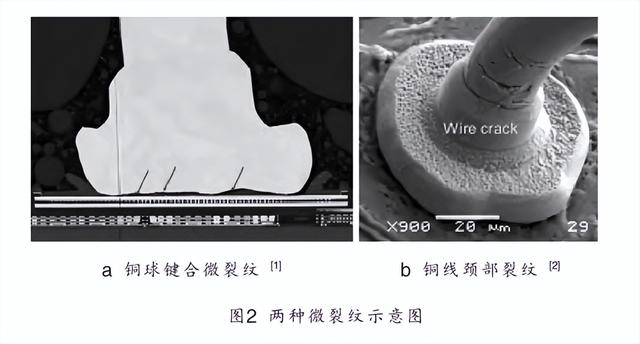
2.2强加速稳态湿热试验
HAST旨在模拟器件在高温高湿的环境中工作,以评估其在湿热条件下的耐久性和抗氧化腐蚀性。在AEC-Q006标准中,规定了HAST需进行2次应力叠加,以考核铜线互连的可靠性。在AEC-Q100和AEC-Q101标准中,该项试验只要求进行1次应力试验,与之相比,AEC-Q006标准对于铜线键合产品在HAST上要求更为严苛。
HAST对铜线器件可能特别重要,因为铜线在湿热环境下更容易受到封装材料中卤族元素扩散引起的氧化腐蚀,导致失效。从材料角度来看,首先对于环氧模塑料(EMC:EpoxyMoldingCom-pound)而言:大多数模塑料的玻璃化转变温度(Tg)介于120~140℃之间,且玻璃化转变通常在一定的温度范围内发生,有时起始温度甚至低至100℃。吸湿会进一步使Tg降低10~15℃。并且,在HAST期间,大多数模塑料会进入甚至超过其玻璃化转变区域。在严酷的HAST条件下,即高温和潮湿共同作用下,封装材料可能会发生不可逆的降解。虽然在85℃时材料的行为相对稳定,但在较高温度下(例如:110℃和130℃),材料会因水解而开始降解,导致有机阴离子(如乙酸根和甲酸根)的含量逐渐升高,同时也导致材料内部pH值的降低。此外,添加剂如缓蚀剂(CI)和阻燃剂(FR)会导致模塑料内部卤素离子浓度的增加。模塑料的体积电阻率(VR)可用作衡量离子迁移率的指标。在HAST条件下,实际吸湿量比THB的85℃/85%RH条件下高约75%。当材料处于玻璃化转变区域时,其VR值会显著下降,因此HAST条件下的较高湿度和温度会降低VR值,树脂基质内的自由体积增加,从而使离子在系统中更容易移动,这为Cu-Al界面发生腐蚀创造了条件[3]。
2.2.1有偏强加速稳态湿热试验氧化腐蚀过程
在HAST的恶劣条件下,会出现由氯引起的微电偶腐蚀,并且会发生选择性的Cu-Al金属间化合物(IMC:IntermetallicCompound)腐蚀,即Cu3Al2和Cu9Al4相持续发生腐蚀,而富铝的CuAl2相保持免疫。
首先,由于Cu-Al界面存在较高的表面张力(表面能),Al在Cu9Al4中的化学势达到较大的负值,有利于在氧化铝的钝化过程中形成阳离子空位。这说明Al在Al2O3中的迁移速度最快,从而导致Cu9Al4相中腐蚀最为迅速,使金属间化合物中的Cu9Al4相首先发生氧化。这些富含Cu的层面的侵蚀会导致键合边界的断裂。在湿气和正偏置销的加速作用下,键合材料中的Cu9Al4腐蚀速度比其他周围材料更快。其次,当湿气与来自模塑料的氯离子共同迁移时,在高温下,Cu9Al4的微观结构发生变化,缝隙腐蚀促进微裂纹的扩展。Cu9Al4的IMC与氯离子的反应性比CuAl2更高,并且当氯离子与Cu9Al4反应时,IMC位于晶格缺陷处。因此,在Cu/Cu9Al4界面容易观察到缝隙腐蚀。富含铝的IMC内部或之上的氧化铝钝化层会阻碍卤素离子的进入,从而为进一步的侵蚀行为创造了离子扩散路径。这导致了腐蚀区域的形成,该区域由两相微观结构、Al2O3晶体,以及嵌入的结晶Au和Cu金属颗粒构成。由此产生的氧化界面非常脆弱,容易断裂。最终,受损的Cu-AlIMC会完全破裂,这是Cu-Al系统在湿度应力测试过程中不可避免的结果。这种Cu-Al界面的缝隙腐蚀/点蚀机制如图3所示[4-5]。
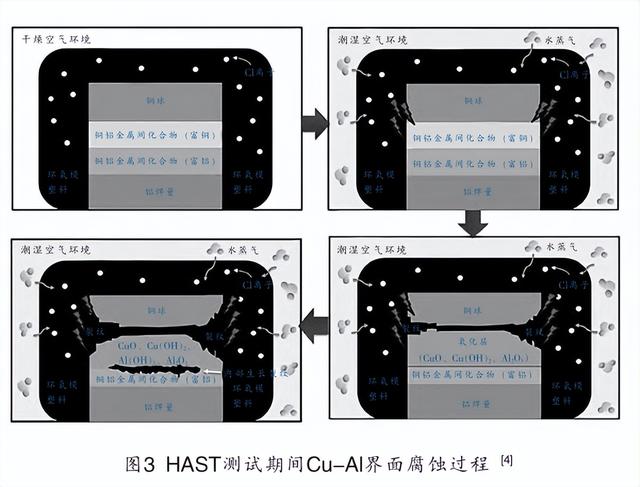
与金线键合相比,铜线键合存在以下特点:根据界面金属颗粒的空间分布,铜颗粒分布更均匀,导致Cu-AlIMC比Au-AlIMC更容易受到湿气的侵袭。卤化物的存在也可能加速这种效应[6]。Au-Al的IMC厚度比Cu-Al高3~5倍,Au球下方有良好的Au覆盖层和金属间化合物的形成,这增强了Au和Al之间的结合。IMC覆盖层比Cu-Al更坚固,这增强了界面的稳定性。由于氯离子不易渗透并建立电化学反应导致IMC腐蚀,因此Au-Al的腐蚀速率远低于Cu-Al[7]。
2.2.2施加偏置的影响
偏置电压会加速故障率,发生离子迁移,导致处于正偏置的引脚在HAST期间会吸引卤素离子。偏置和接地键合点之间的电场会驱动氯离子优先从一个方向向IMC区域迁移。在未施加偏置下,IMC降解更加轴对称,因为氯离子的移动来自各个侧面,如图4所示。
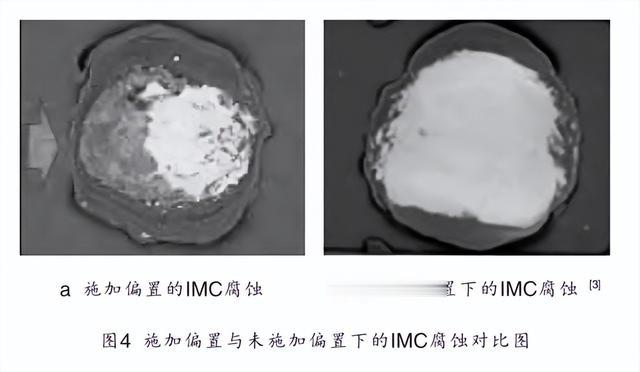
深入了解HAST中的失效机制对于改善铜线键合器件的可靠性非常重要。通过采取合适的设计和制造措施,通过优化模塑料材料配比、减少键合制程中卤素离子的引入,可以降低微电偶腐蚀、缝隙腐蚀和断裂的风险,提高铜线键合器件在湿热环境下的性能和可靠性。这对于在汽车电子应用中确保器件的长期稳定运行至关重要。
2.3高温贮存寿命试验
HTSL用于评估器件在高温条件下的长期储存稳定性。与TC不同,HTSL试验处于高温等温状态。在AEC-Q006标准中,规定了该项试验需进行2次应力叠加,以考核铜线互连的可靠性。在AEC-Q100和AEC-Q101标准中,该项只要求进行1次应力试验,与之相比,AEC-Q006标准对于铜线键合产品在HTSL试验上要求更为严苛。
在该试验中,由于Cu-AlIMC的密度不同,存在应力集中点。在高温条件下,由于CTE的差异,键合球边缘的应力集中,这导致裂纹从键合球边缘开始形成。随着高温时间的推移,这些裂纹会扩展并与IMC的生长和演化过程相互关联。其次,在键合形成过程中,球键会发生严重变形,键合界面在其周边出现最大变形量,这是微裂纹从球周边开始的主要原因之一。变形微观结构特征,例如细胞、位错和滑移带在接合界面附近形成,特别是在键合球外围。此外,键合后这些严重变形区域储存了大量能量。不均匀的球变形以及键合球和键合垫材料的不同导致存在不均匀的残余应力分布,伴随着IMC的生长和演化,会发生应力的积累和释放,裂纹在整个键合区域的连续IMC间隙中逐渐演变,并最终贯穿整个键合区域,导致开路失效。如图5所示。
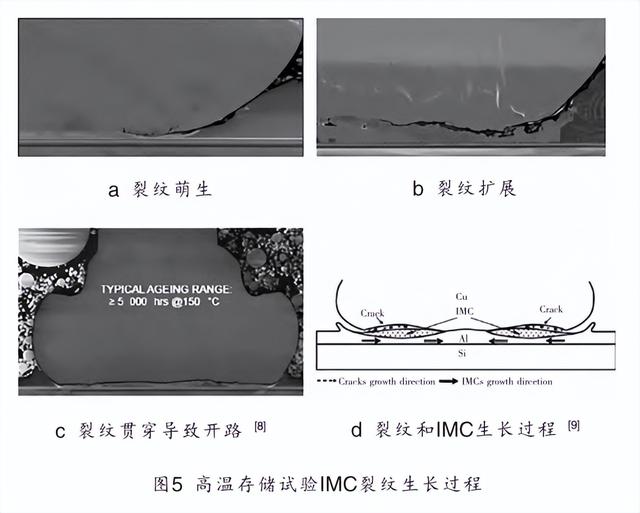
而铜线与金线键合器件在IMC生长速率和界面的最终失效模式存在一些差异:Au-AlIMC的生长速率比Cu-AlIMC高10倍以上,导致铜线键合在高温下的键合失效原因为裂纹扩展,而金线为柯肯德尔空洞的聚集。
这种失效机制表明,在高温储存条件下,铜线键合器件中的IMC生长和演化过程是导致键合失效的主要因素。相较于AEC-Q100、AEC-Q101标准中金丝键合器件在高温存储试验中要求的一次应力考核要求,AEC-Q006标准要求两倍应力叠加的考核要求,对铜线键合器件可靠性进行进一步验证考核。
2.4物理分析试验
除了可靠性测试要求外,AEC-Q006标准还强调了进行物理分析的重要性。铜线键合器件的可靠性测试中还包含试验前后的物理分析试验,这些物理试验为功能失效前兆的物理退化分析,包括非破坏性试验CSAM、破坏性试验(例如:键合球剪切、键合球和第二键合点拉力试验,以及切片观察分析),图6中给出了部分破坏性和非破坏性方法的示例。利用这些分析结果可以评估器件在测试过程中出现的失效模式和机制,有助于了解器件的可靠性特性,指导设计和制造过程中的改进,并提高铜线器件在汽车电子应用中的可靠性水平。
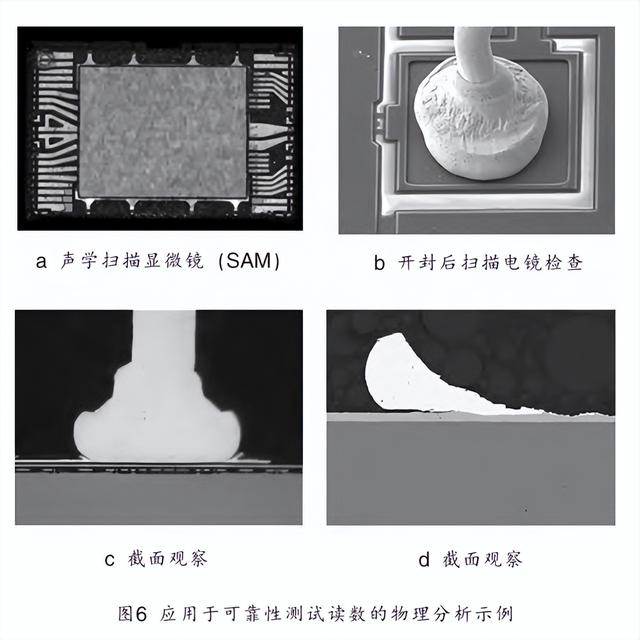
3结束语
综上所述,AEC-Q006标准为铜线键合器件在汽车电子认证中的可靠性要求提供了指导。本文解读了标准中关于铜线键合器件的要求,并对铜线与金线键合器件进行优劣对比,分析了铜线器件在TC、HAST和HTSL中的失效机制,以期为相关领域的研究和应用提供指导和参考。随着技术的不断进步和标准的不断完善,铜线键合器件有望在更多应用领域得到广泛应用,并提升其可靠性和性能。铜线键合器件在电子领域具备许多优势和潜力,但也面临市场普及、汽车电子应用和可靠性评估等挑战。通过深入研究和解决这些问题,铜线键合器件有望在不久的将来得到更广泛的应用和推广,从而提高汽车电子行业的可靠性水平。