2月18日,中国石化工业迎来里程碑式突破——广州石化采用自主研发的茂金属催化剂,在国内首套三井工艺聚丙烯装置上成功试产出高端茂金属聚丙烯(mPP)。这一成果不仅填补了国产催化剂在该工艺领域的应用空白,更标志着我国在聚丙烯高端化赛道上实现关键技术突围。
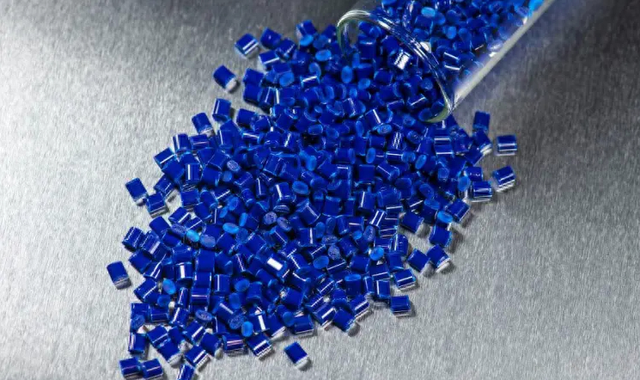
茂金属聚丙烯因其独特的分子结构设计,被誉为“塑料黄金”。相比传统聚丙烯,其分子量分布窄至1.5-2.0(传统工艺为3-5),熔点降低10-15℃,透光率提升至93%以上,同时兼具高强度、低析出等特性。这些性能优势源自中国石化科研团队对催化剂配位结构的精准调控——通过优化锆、钛等过渡金属与环戊二烯的配位模式,实现聚合物链的定向生长。
四大场景重构产业生态此次试产的mPP产品正在打开万亿级市场空间:医疗防护革命:0.5微米级超细纤维制成的医用口罩过滤效率提升20%,手术服抗静水压值突破65cmH2O,打破高端医疗耗材依赖进口的局面;绿色包装升级:食品级mPP薄膜厚度可减薄30%仍保持相同强度,单吨材料减少碳排放12%;精密制造突破:化妆品瓶胚注塑成型周期缩短15%,透光率媲美玻璃却具备抗摔特性;健康消费蓝海:婴儿奶瓶用mPP通过FDA认证,耐温范围扩展至-20℃~140℃。从实验室到生产线的硬核突围。
从实验室到生产线的硬核突围面对三井工艺严苛的氢气敏感性(控制精度需达±0.5ppm),广州石化组建30人攻坚专班,历时18个月完成三大技术创新:开发催化剂在线活化系统,活性稳定性提升40%;优化流化床反应器气速分布模型,产品等规度波动范围收窄至±1%;首创“双峰分子量调控”工艺,兼顾加工性能与机械强度。试产期间,装置运行负荷率稳定在95%以上,产品关键指标全部达到欧盟REACH标准。
高端聚烯烃的国产化冲锋号当前全球茂金属聚丙烯年需求超500万吨,我国自给率不足30%。广州石化的突破,使国产mPP生产成本降低25%,预计到2026年将建成5万吨/年产能,从催化剂到工艺包的完全自主化,意味着中国企业在高端聚烯烃领域拥有了定义标准的能力。
这场硬核科技突围战,不仅为“中国制造”撕开了高端材料市场的突破口,更在“双碳”战略下书写了石化行业高质量发展的新注脚——当实验室的分子设计转化为生产线的澎湃动能,一个属于中国新材料创新的黄金时代正在加速到来。