摘 要: 随着对电化学储能需求量的增加,锂离子电池行业面临着提高生产效率、降低能耗和提高电池性能等新挑战,尤其是在先进的下一代锂离子电池制造技术方面。其中,电极制造工艺发挥着关键作用,直接影响着电池的能量密度、制造成本和产量。干法电极是一种新型的电极制造工艺,由于其不需要添加任何溶剂,且具有高面密度、低内阻、长循环性能等优点,在超级电容器和锂离子电池中展现出巨大的应用潜力。本文首先介绍了干法电极的制备方法和特性,然后详细探讨了干法电极在超级电容器和锂离子电池领域的应用研究进展,包括提高电极负载和提升电化学 性能等方面的研究成果。最后,总结了当前干法电极在超级电容器和锂离子电池中的应用过程中存在的问题与挑战,并提出了未来研究的方向。
关键词:干法电极;超级电容器;锂离子电池;固态电解质;粉末喷涂;黏结剂纤维化
锂离子电池和超级电容器在新能源汽车、便携式电子设备和规模化储能等领域中起着至关重要的作用,这使它们成为电化学能源储存系统中两种最重要的储能器件。目前针对锂离子电池和超级电容器的研究主要集中在新型电极材料和高性能器件的研发。然而,在电极制造过程中仍然广泛采用传统的涂覆技术,即将电极活性材料、导电添加剂、黏结剂和溶剂混合成浆料后均匀涂覆到集流体上。对于采用高表面积的材料体系,这种方法会导致浆料稳定性不佳、高黏结剂含量、高孔隙率、低压实密度、低体积能量密度和性能均一性不足等问题。此外,涂覆方法还存在着电极中的溶剂难以去除、机械性能差和附着力低等固有缺陷。
近年来,干法电极制备技术备受关注,在超级电容器和锂离子电池领域具有广阔的应用前景。干法电极技术是一种新兴的电极制造方法,它不需要溶剂、无需高能耗的干燥设备和 N-甲基吡咯烷酮(NMP)回收装置,同时设备投资少、能源消耗低,所需场地面积也较小。制备的干法电极具有面密度高、倍率和循环性能优异以及内电阻低等优点。2004 年,麦斯韦尔技术(Maxwell Technologies)公司首先提出这种无需溶剂的干法电极制造工艺,其工艺成本、综合性能和环保效益均优于湿法涂覆工艺。研究人员还成功制备了循环性能优良的磷酸铁锂/活性炭(LFP//AC)复合电极和混合型锂离子电容器,以及利用干法电极制造技术开发锂离子电池和固态电池等。
本文主要综述了干法电极的制备方法及特性,并重点探讨了其在超级电容器和锂离子电池中展现出的优异性能。在超级电容器方面,干法电极能够提高器件的能量密度、功率密度和循环寿命;而在锂离子电池方面,干法电极可以提高电池容量、改善循环稳定性以及实现快速充放电等。最后,文中对干法电极在超级电容器和锂离子电池领域的应用进行了总结,明确了其取得的进展和存在的局限性,并提出了未来的研究方向和前景展望。
1 干法电极制备方法
1.1 干法电极制备方法概述
干法电极制备方法是在无溶剂或极少溶剂条件下制备电极材料的一种技术。相较于湿法涂覆制备,这种方法不仅可以消除溶剂的使用、降低对环境影响,还可以减少电极制备过程中杂质成分的混入。干法电极制备方法主要有粉末喷涂法、黏结剂纤维化成膜法和干压法等。
粉末喷涂法是通过使用静电喷涂系统(图 1(A))将完全干燥的电极颗粒沉积到集流体上(图1(B)),然后加热黏结剂至熔点将粉末黏结固定在集流体上形成电极膜。这种方法包括粉末拾取和分配单元以及静电喷枪。喷枪用于对干燥颗粒进行充电,带电的干燥颗粒将在接地集流体上沉积。热辊用于控制电极的厚度和压实密度(图 1(C), (D)),代替了用于控制浆料涂覆厚度的刮刀,使用热辊可以快速实现黏结剂的热活化,取代了传统浆料涂覆电极中蒸发溶剂所需的烘箱。喷涂电极具有良好的柔韧性,能够大面积涂覆并具有可塑性(图 1(E))。
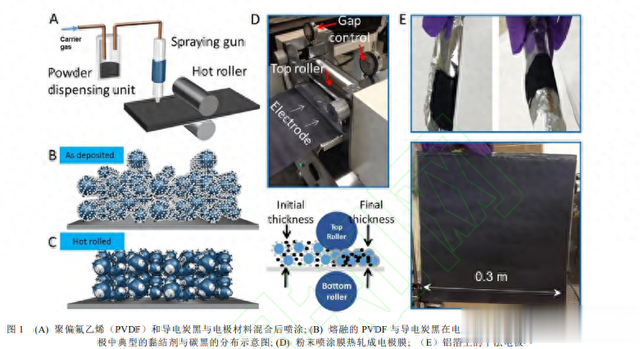
黏结剂纤维化成膜法是指在电极活性材料和导电添加剂粉末均匀混合后,向其中添加改性的聚四氟乙烯(PTFE)黏结剂,粉末在经过混合和强剪切力作用后形成团聚体。强剪切力使聚四氟乙烯微球变成原纤维、形成基质,从而将电极粉末混合和支撑在一起。这一过程被称为黏结剂原纤维化,其效果受设备和工艺参数的影响,并直接影响电池的电化学性能。若黏结剂未能充分混合和剪切,则可能导致无法形成自支撑膜;或由于黏结剂团聚而增加自支撑膜的阻抗。
如图 2 所示,黏结剂纤维化成膜法制备电极膜包括以下四个步骤:首先,电极组分应均匀混合;然后,加入黏结剂将它们捏合在一起,形成混合物的块状结构;第三步,将块状结构挤压或轧制成自支撑膜;最后,将自支撑膜加载到两个轧辊之间的集流体上,形成电极片。类似地,干压法将电极材料(镍钴锰酸锂 NCM712)、导电添加剂(多壁碳纳米管 MWNT)和干燥的 PVDF 粉末等进行预混合,然后将混合物压覆在腐蚀铝箔上,再通过辊压进一步热压制备出干法电极。与传统湿法涂覆工艺相比,这种方法制备的电极具有更高的机械强度和性能,并且能够实现高负载量。
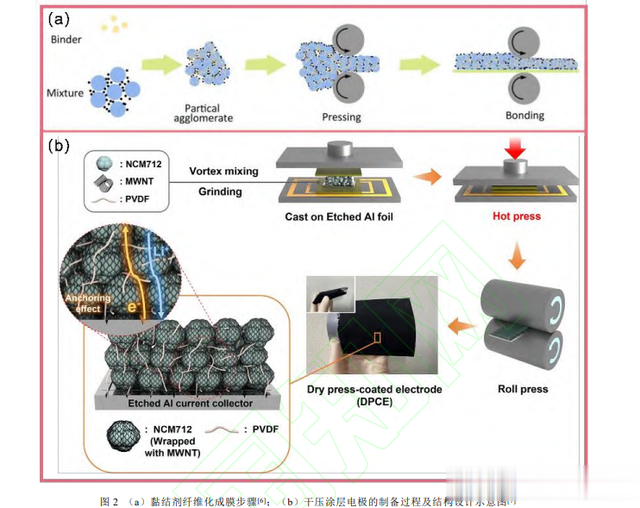
黏结剂的纤维化是干法电极工艺的核心环节,其完善程度直接关乎后续成膜的稳定性以及黏结剂 PTFE 的用量。目前,商用 PTFE 纤维化方法较多,主要包括气流磨法、高速混合机法及双螺杆法,但核心目标都是实现 PTFE 的均匀分散和精细拉丝。在 PTFE 的分子链结构中,氟和碳主链通过 C—F键的高键合能紧密相连(485 kJ·mol-1)并在 C—C 主链周围形成一层低表面能的致密保护层,这使PTFE 具有较高的热稳定性、耐溶剂性、低摩擦系数以及许多其他出色的特性。黏结剂原纤化过程受黏结剂的物理化学性质、活性材料的粒径、设备类型和力传递参数的影响。温度也会影响 PTFE 原纤化,在 19 ℃以上通过不同的阶段过渡,使分子链变得柔韧,易于以最小的剪切力提取为原纤维。
尽管 PTFE 黏结剂有可能实现用于干电极设计的无溶剂系统,但集流体和干电极膜之间的附着力差,因此需要提前在集流体上引入底胶涂层。这种涂层需要湿法工艺,从而产生挥发性有机化合物(VOC),因此目前无法使用 PTFE 实现完全无溶剂的工艺。此外,采用 PTFE 黏结剂的干电极正趋向于厚的大面积电极设计,这引发了人们对电解液润湿性差的担忧。这归因于氟的强电负性、低表面能和 PTFE 黏结剂的疏水特性,这可能会降低电解液和电极之间的亲和力。PTFE 的最低未占据分子轨道(LUMO)值较低,使其在热力学上容易受到负极低电位下电化学副反应的影响,从而导致电池充电过程中的结构退化。因此,负极处的不可逆还原为在负极和正极同时使用 PTFE 作为多功能黏结剂带来了挑战。
辊压已经成为设计干电池电极中备受关注的工序之一。通过调整辊压机对辊的间隙、压制力和辊子旋转比,产生的剪切力会导致干混料额外混合和分散,从而形成表面光滑的电极膜。保证电极厚度均匀一致的关键步骤是辊压,设置不同作用的辊直接实现电极的压制和层压,实现电池电极的连续生产。基于辊压机的方法可能成为干电池电极制备的主流方向。例如,为了达到量产速度,超级电容活性炭电极通常采用卧式大辊粗压与立式精压相结合的方式;而电池干法电极则更倾向于采用多级差速连续辊压模式。然而,剪切力受颗粒大小影响,需要精确控制以最大限度地减少整个过程中的薄膜破裂、膨胀和边缘变形。
1.2 干法电极优势
与传统的湿法涂层方法相比,干法电极具有环境友好、成本低、相容性增强、生产效率高、电极性能改善等独特优势。根据阿贡国家实验室和 Wood 等的调查显示,电极涂布、干燥和溶剂回收的工艺成本占电极制造总成本的 48%~50.2%(如图 3(a)所示),在考虑到集流体及其后续电池组装和老化的总材料成本时,包括模切、叠片、焊接、封装、成型等制造过程,涂布、干燥和溶剂回收的制造成本也占据了整体成本的 19.56%。在整个电池制造过程中,干燥和溶剂回收步骤占据了与能源消耗相关的大部分成本,干燥过程和溶剂回收步骤的能耗占比达到 45%~47%(图 3(b))。为了生产 10 kW·h 的电池,需要 420 kW·h 的电力来蒸发和回收 NMP,当量二氧化碳排放量为1000 kg。
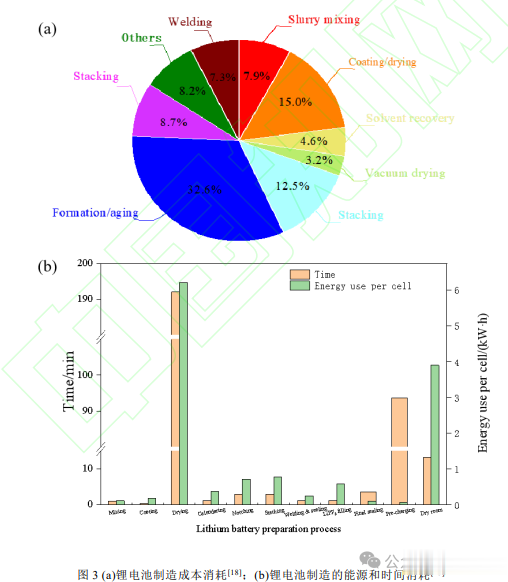
除去能源消耗外,浆料制备也需要更多的材料成本。溶剂 NMP 的单价约为 1.5~3 $·L-1 。此外,NMP 回收还要考虑 NMP 回收设施的设备成本,包括空气加热器、冷凝器、沸石转轮、冷却器等设备。每 10 kW·h 的电池组装需要约 4400 kg 的 NMP 作为溶剂,根据估计,基于 NMP 的总成本(包括材料、制造等)占电池总成本的 1%~2%。这些设施不仅需要高昂的资本成本,还需要大面积的厂房。使用干法可以为 MW·h 级生产工厂节省 300~600 万美元的资本成本。预计这些调整能够总计减少资本成本 14.2%~19.0%,并且节省 13.1%~16.5%的厂房面积。采用干法电极后,预计锂离子电池制造的总成本将降低 10%~15%(图 4)。
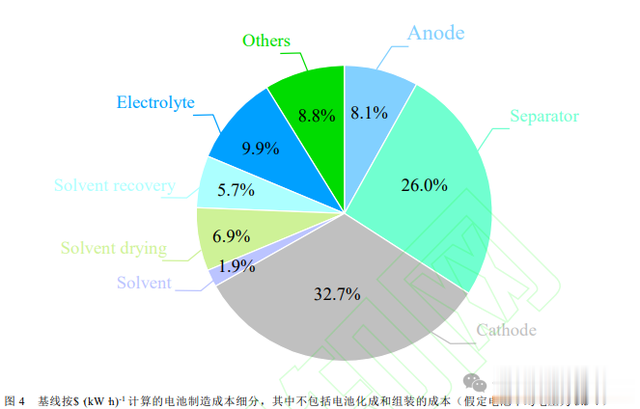
固态电解质和电极的孔隙率是影响离子迂曲度的重要参数,而孔隙率的最小化则依赖于制造技术。如果没有适当的辊压处理,溶剂蒸发可能会导致电极的平均孔隙率高达 56%。相比之下,采用干法电极方法有望降低电极或电解质的孔隙率。实验结果表明,粉末喷涂法沉积可使电极的孔隙率降低 4%~10%。
然而,采用传统涂覆方法制备的高负载的厚电极过程中,由于黏结剂倾向于富集在涂覆层的表层而出现浓度梯度,在溶剂蒸发过程中容易出现极片发脆和掉粉落现象。而采用干法电极技术可以实现高负载量的镍钴锰三元(NCM)电极,面容量可达 4 mA·h·cm-2 (面密度 27 mg·cm-2)或 6.8 mA·h·cm-2 (麦斯韦尔型),甚至可以达到>13 mA·h·cm-2 (100 mg·cm-2,熔融挤压到500 mm 厚度),干法电极具有相当的附着力,结合强度可达 148.8 kPa(粉末喷涂工艺),是常规湿法涂布电极的 1.8 倍(84.3 kPa)。
此外,采用干法技术可以减少 16.2%~21.4%工艺时间。由于干法电极技术优异的兼容性,该方法可以应用于许多对液体敏感的场合,例如全固态电池硫化物固态电解质及其大片制备,以及使用锂粉的电极预锂化。
据 Maxwell Technology 声称,干法电极的生产效率有望达到 25 m·min-1,与传统涂布工艺(20~60 m·min-1)相当。而且,干法电极工艺还可以应用于中试规模卷对卷设备中,具有整合到传统生产链中的潜力。传统的电极制造过程包括浆料混合、涂布、干燥、溶剂回收、辊压、分切和真空干燥等步骤。研究表明,生产工艺中干燥工序所需时间占电极制造时间的 90%以上。采用干法制造过程,可以简化为仅包括干粉混合、制膜、压覆复合、分切和真空干燥,干燥过程的耗时可以大幅缩短,从而使得整体生产效率得以提升。采用干法电极技术可以实现低黏结剂含量的自支撑膜,允许电极在折叠和提拉过程中不损坏(采用麦斯韦尔工艺);减少黏结剂含量和部分团聚的分布,将导致更活跃的表面,从而加快离子传输速度,降低电极中离子传输的迂曲度,进而提高倍率性能。
此外,干法制造也是实现负极预锂化的理想方法。锂粉是作为合成锂碳、锂硅复合材料等锂化负极材料的典型锂源。由于锂粉具有极高的反应活性,湿法混合时加入有机液体将导致寄生反应形成过度钝化的固体电解质界面(SEI),从而导致严重的锂损失。干法可以避免这一问题,提高锂金属源的锂化效率,使得锂颗粒尺寸具有更广的分布,从而进一步优化电极的性能。此外,锂的大颗粒和锂箔也可应用于干混预锂化。干粉混合过程将逐渐粉碎锂颗粒,并与碳或硅反应形成锂化复合材料,而复合材料可制造成锂化电极直接使用。干法电极作为一种新兴工艺,为电极生产提供了更可持续、更高效的方式。
干法工艺通过不使用有毒溶剂大大减少了对环境的危害,同时降低了能源消耗,从而降低成本。由于干法工艺不含极性溶剂,可以防止溶剂与某些固态电解质发生反应。此外,干法工艺有助于制造超过 5 mA·h·cm−2 的厚电极,因为没有碳–黏结剂结构域(CBD)的迁移,这对提高电池的能量密度至关重要。更重要的是,其纤维化的聚四氟乙烯(PTFE)不会堵塞电解液浸润通道,对于高镍三元等不易均匀分散的材料有更高的适应性,因此成为实现电极高比能和高功率的必要途径。此外,干法电极无涂布电极的边缘缺陷,更适用于大圆柱电池,有助于提高成品率。表 1 显示了干法电极和湿法电极制造的综合比较结果。
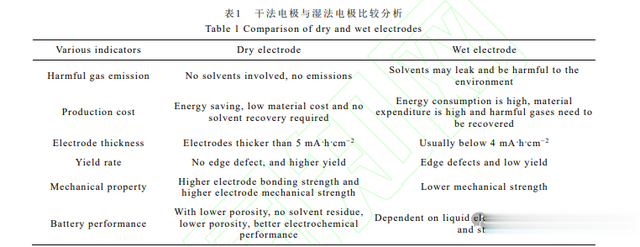
尽管干法电极具有众多优势,但其劣势也不可忽视。静电喷涂方法由于无法实现均匀的负载,仅适用于实验室研究水平,至今尚未投入量产。PTFE 纤维化生产方式对环境条件要求极高,选择合适的生产地点至关重要,可帮助降低成本并提高效率。此外,锂电自支撑膜辊压制膜的过程会导致辊面磨损严重,需要研究更适合的辊面处理工艺,并优化干法电极工艺。未来需持续优化工艺和设备,提升生产效率、降低成本,使干法电极更具竞争力。
2 干法电极在超级电容器和锂离子电池中的应用
干法电极技术在超级电容器和锂离子电池中有着广泛应用,可以制备各种碳材料、钴酸锂 (LCO)材料、三元锂材料(NCM)、磷酸铁锂(LFP)材料的干法电极以及固态电解质等。通过优化制备过程和结构设计,可以进一步提高干法电极的性能。
2.1 碳材料干法电极
Gao 等干法(如图 5 所示)制备了高表面积活性炭电极,通过循环伏安法对其进行了电化学性 能表征。即使在高扫描速率下,循环伏安曲线仍呈现出相对矩形的形状,并没有任何氧化还原峰,表明该活性炭具有良好的电容特性。郑超等采用干法电极工艺制备了活性石墨烯/活性炭复合电极片,将活性石墨烯应用于超级电容器器件,并且显著提升活性炭基超级电容器的性能,相较于纯活性炭电极,比容量提高了 10.8%。
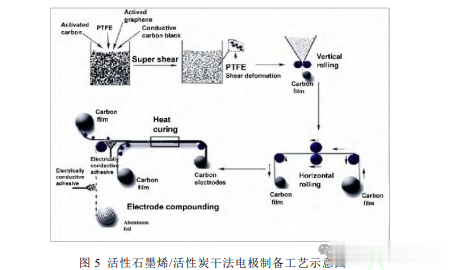
由于在快速充电过程中石墨负极表面的电化学反应和镀锂不均匀,同时满足电池拥有优越倍率性 能和高容量的要求具有挑战性。Suh 等采用聚四氟乙烯黏结剂的无溶剂电极制造工艺制作了干法石墨负极,其在倍率性能和容量保持率方面优于传统的湿法工艺电极,干法石墨负极比湿法负极表现出更少的镀锂,这意味着即使在高负载量的条件下,干法电极也能够快速充电。干法石墨负极在 300 次循环后仍能保持 88.2%的容量,表明全电池运行稳定。如图 6 所示,传统的湿法处理电极用聚合物粘合剂(SBR/CMC)包裹石墨颗粒,阻止锂离子直接移动到活性材料表面。而干法处理电极在不覆盖其表面的情况下形成 PTFE 原纤维网络,有助于活性材料表面积更大地暴露,使得锂离子与石墨颗粒立即相互作用,锂离子得到快速传输,从而使极片表现出出色的电化学性能。
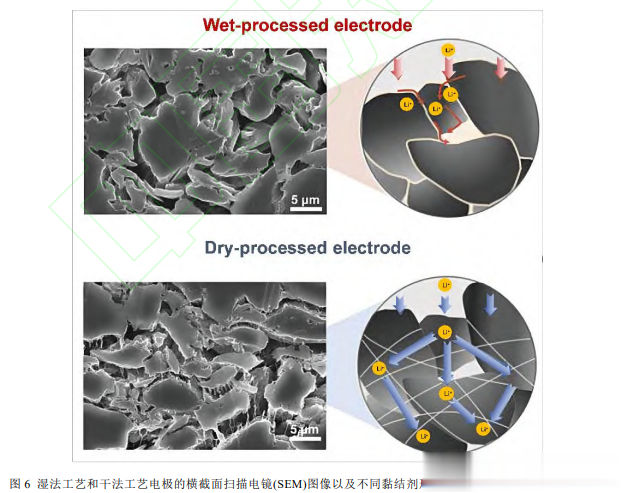
Ank 等对特斯拉 4680 圆柱形锂离子电池进行了拆解和表征,电池拆解过程如图 7 所示。该款电池正负极均采用了全极耳结构,干法工艺制备了石墨负极。Cu 集流体和单面膜层厚度分别为 9 m和 125 m,面载量约为 18.0 mg·cm-2,电极层与铜箔集流体之间有水溶性底涂导电胶或涂碳层;可观察到纤维化黏结剂形貌,红外光谱和热重分析等表明该电池采用了聚四氟乙烯类黏结剂和无溶剂干法工艺。通过能谱、微分电压、增量容量和三电极分析证实该电池采用了 NCM811 正极和不含 Si 元素的石墨负极。同时利用单个电池数据计算出能量密度为 622.4 W·h·L-1 和 232.5 W·h·kg-1。
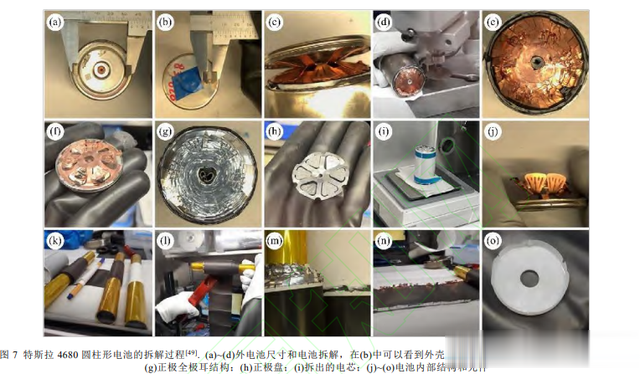
Zhang 等研究了不同碳材料的干法负极,包括石墨、硬炭和软炭,并通过负极在充放电循环过程中的厚度变化来确定负极的稳定性。虽然黏结剂 PTFE 会发生不可逆的脱氟而转变为无定形碳,但干法硬炭负极和干法软炭负极在充放电过程中仍展现出良好的循环稳定性,而干法石墨负极却由于其较大的体积变化而稳定性变差。采用这种方法可以较容易地制备出高负载碳材料负极,负载量可达 25 mg·cm-2,从而降低制造成本的同时提高电池的能量密度。Palanisamy 等提出了一种简单、高效的喷涂工艺,使用不同黏结剂含量和不同粒径的硬炭在铜集流上制备出硬炭复合电极,并将这种喷涂硬炭复合负极用于钠离子电池。
2.2 锂离子电池干法正极
与传统电极相比,干涂电极具有更强的黏合力。Ludwig 等通过静电喷涂和热压法制备了钴酸锂 (LiCoO2,LCO)正极片。图 8 比较了干法电极和传统湿法电极在电极—集流体界面处的微结构差异。此干法工艺首先用 PVDF 覆盖 LCO(图 8(A)),待 PVDF 热活化后完全润湿 LCO(图 8(B)),而加入的导电炭黑会剥落 LCO 上的 PVDF 颗粒(图 8(C)),在混合电极材料进行干涂工艺时,导电炭黑与 PVDF 颗粒形成团聚物(图 8(D)),实际表现为导电炭黑包覆在 PVDF 颗粒周围(图 8(E)),最后进行热轧过程,形成的电极表面非常平整(图 8(F)),此过程形成了熔融的 PVDF(图 8(G))。
由于机械压制的使用,在集流体上形成了口袋状结构。与湿法涂布工艺相比,这提供了额外的接触面积,从而使干法工艺电极具有更高的黏合强度。通过采用倍率、循环伏安和电化学阻抗谱等分析表征,对比了钴酸锂干法电极和传统湿法电极。研究结果显示,干法电极在容量和循环稳定性方面均优于传统湿法电极,同时具有更低的电化学极化和更强的倍率能力,其界面电阻也较低。
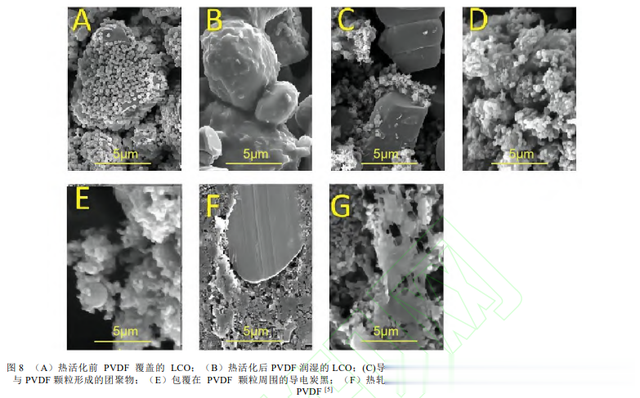
Matthews 等制备了 NCM622 基干法电极和湿法涂覆电极,厚度和面负载量分别为 100 μm 和30~32 mA·h·cm-2,两者表现出显著的微观结构差异和相应的电化学性能差异。干法电极在 0.1C~2C的倍率范围内具有更好的倍率性能,特别是在高倍率下放电容量比湿法涂覆电极提高了 150%,干法电极中的电荷转移电阻和离子扩散电阻更低,对活性材料表面的遮挡最小且无孔隙堵塞。郭德超等采用干法电极技术成功制备了锂离子电池用 LiNi0.8Co0.1Mn0.1O2(NCM811)干法电极片。纤维状 PTFE 广泛分布在 NCM811 颗粒周围,干法电极内部形成致密、完整且柔软的网状黏结剂结构,有效提升了电极的耐热性能。
Liu 等采用“粉末印刷技术”制备了 NCM 干法正极,与石墨负极组装成全电池在 0.5C 倍率下循环 500 次后容量保持率 80%。Zhen 等利用静电喷涂法制备了 NCM523 干法电极,研究了不同的黏结剂含量对干法电极的影响。湿法电极中的黏结剂容易覆盖活性材料表面,形成致密的电极结构,但不利于实现高倍率电池性能。相反,干法电极中黏结剂和导电剂以点接触方式分布,有利于离子快速传输,同时有利于循环过程中保持电极的完整性。
在众多干法电极制备方法中,黏结剂纤维化法因为具备大规模生产的潜力而被认为是最有发展前景的一种。然而,LFP 的硬度使得 PTFE 纤维化制备干法电极变得困难。Zhang 等添加多壁碳纳米管(MWCNTs)制备了 SF LFP 电极(无溶剂干法磷酸铁锂电极),图 9 显示了基于 PTFE 纤维化制备 LFP 干法电极的过程。碳纳米管提高了电极的电导率,同时充当 LFP 颗粒的基底,在干粉混合物热轧过程中促进 PTFE 纤维化,形成自支撑电极膜。通过这种方法制备的干法 LFP/硬碳全电池,展现出与传统湿法制备的 LFP 电极相媲美的电化学性能。经过预锂化处理后,全电池的初始库仑效率(ICE)提高至 95%以上。Zhang 等采用聚碳酸丙烯酯(PPC)替代 PVDF,采用球磨混料和粉末干压法制备了磷酸铁锂正极,其表现出稳定的循环性能,经过 800 次循环后仍然保持 79.1%的容量保持率,平均每循环容量仅衰减 0.026%。
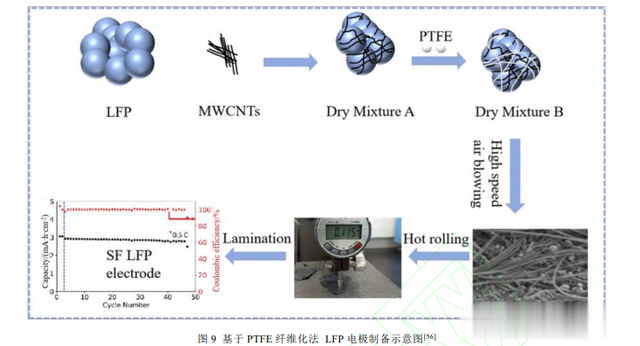
干法电极还可以减少电极干燥时的体积变化,从而减少裂纹的形成,提高电极微结构的稳定性。Ni 和 Zhao采用铝掺杂锰酸锂(LMA)制备负载量高达 20.6 mg·cm-2 的干法电极,通过羧甲基纤维素和硅氧烷的协同作用,不仅改善了正极组分的分布、提高了电极膜的机械强度,还使得电极更具柔韧性。这种特性使得电极能够有效地适应剧烈的体积膨胀,在反复充放电循环中保持结构完整性。制备的锰酸锂//钛酸锂全电池在经过 1000 次循环后容量保持率仍高达 89.2%。
2.3 固态电池
全固态电池以其高能量密度和固有安全性被认为是下一代的锂电池。硫化物固体电解质作为关键材料,因其离子电导率高、晶界电阻小而受到广泛关注。Li 等以 PTFE 和 Li6PS5Cl 粉末为原料,采用热轧技术制备出厚度为 40 m 的自支撑硫化物固体电解质薄膜,离子电导率高达 8.4 mS·cm-1, 同时,无需溶剂采用干法电极技术制备了 NCM622 正极薄膜。以无电解液的干法正极、固体电解质薄膜和 Li–In 合金组装成全固态电池,在 1C 下具有 120 mA·h·g-1 的高放电比容量,在 1000 次循环后具有 86.4%容量保持率(如图 10 所示),在室温下具有较好的倍率性能(4C 时为 40 mA·h·g-1 )。
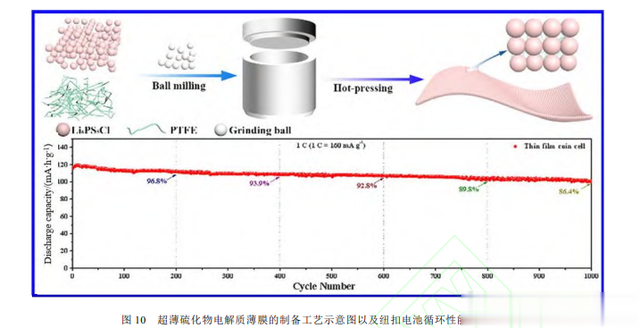
Hippauf 等提出通过采用干法工艺使纤维状 PTFE 黏结剂代替黏结剂乳液,可将 NCM 电极的黏结剂用量(质量分数)降低至 0.1%(目前报道的最小用量);黏结剂质量分数低至 0.3% 的固态电解质薄膜可以承受折叠和提升而无明显损伤;制作的 NCM 极片具有相当大的机械强度,面负载量高达 6.5 mA·h·cm-2,并制备面积为 9 cm2 的摇椅型的全固态电池。
Zhang 等采用室温离子电导率为10 mS·cm-1 的 Li5.4PS4.4Cl1.6 粉末制备出高性能的干法固态电解质,干燥固态电解质薄膜可以在有限厚度(30 m)、低黏结剂含量(质量分数 0.2%)和大尺寸(>10 cm×10 cm)下实现 8.4 mS·cm-1 的高离子电导率。然而对于附着力较低的氧化物,通常需要更高的黏结剂含量。
Jiang 等报道了一种石榴石基复合固体电解质,通过加入丁二腈使黏结剂质量分数为 5% 的电解质离子电导率提高至 0.12 mS·cm-1。Jiang 等通过干法制备了 Li10GeP2S12 电解质薄膜,具有良好的可操作性、高离子电导率(0.36 mS·cm-1)和高能量密度等优点,适用于固态锂金属电池。使用干法电极的黏结剂纤维化方法,在金属锂负极上形成一层保护膜,以抑制锂枝晶的生长。
采用干法将活性材料与固态电解质膜预混合,可以提前形成固态电解质与活性材料之间的协同离子输运,有助于提高固态电池的性能。干法同样适合于制造富集聚合物的电极和电解质。Helmers 等通过干粉混合、挤压和压延工艺制备了 PEO–LiTFSI 基固态电池,该电池在 80 ℃时具 有 140 mA·h·g-1 的比容量。3D 打印工艺也可用于固态电池的制作,通过该方法制备的 PEO/LiTFSI 固态电解质在 90 ℃下具有 2.18 mS·cm-1 的高离子电导率。Froboese 等报道了可规模化的无溶剂生产流程,包括干燥、造粒、塑化和压缩等过程,可生产离子导电率为 2.4 mS·cm-1(在 90 ℃下)的固态电解质。
干法技术为制备能量密度大于 400W·h·kg-1 的电池提供了可行性,NCA//Li、富锂锰基(Lirich)//Li、LCO//Li和 NCM//Li 体系的能量密度均有希望达到 400 W·h·kg-1。要达到 400W·h·kg-1的目标,正极负载量要达到 5mA·h·cm-2 以上,活性物质质量分数为 90%,NCA//Li、Li-rich//Li、LCO//Li 和 NCM811//Li 体系硫化物固态电池则分别要求固态电解质膜厚度小于 26、35、38 和 88 m。干法技术的优点之一是制备出黏结剂分布均匀的厚膜。据报道,通过干压法可以制备出 500 m 的超厚 LFP 正极,面容量可达 13.7 mA·h·cm-2。因此从实际制造的角度来看,将现有的干法电极技术应用于优化的电极组合,实现 400 W·h·kg-1 的性能指标是可行的。
3 未来挑战与展望
在干法电极制备方面,虽然可以采用麦斯韦尔法、静电喷涂法和干压法等不同方法,但各种方法的力学分布尚未得到充分研究。不同的干法电极制备方法需要特定的黏结剂,而不同的黏结机制也会导致内部黏结剂分布的差异,因此,针对不同干法电极制备方法的黏结剂筛选是当前亟需解决的问题。在干法电极制备过程中,还需要考虑到电解液中某些成分可能与黏结剂发生反应,以及 PTFE 与金属锂的脱氟反应和 PTFE 在高电压下的稳定性。黏结剂降解会消耗额外的活性锂,从而降低库仑效率,同时也会导致机械强度损失、离子传输减慢和电极结构破坏,最终导致高负荷电极循环后体积膨胀、机械劣化和比容量下降情况。
目前,干法技术主要用于超级电容器和液态锂离子电池的电极制备。然而,有必要将其应用范围扩展到全固态电池、锂硫电池中的电极、电解质膜以及金属空气电池(例如锌空气电池)中催化层/防水透气层的制备过程。未来的研究方向包括:
开发低成本、易于均匀有效分散粉体的新型黏结剂或改性 PTFE 黏结剂;研究开发具有高离子电导率的黏结剂,以改善电极和电解质膜的动力学性能;研发更精密可控制薄膜厚度的制膜设备,以提高电极厚度的可控性和一致性。
来源:工程科学学报注:本站转载的文章大部分收集于互联网,文章版权归原作者及原出处所有。文中观点仅供分享交流,不代表本站立场以及对其内容负责,如涉及版权等问题,请您告知,我将及时处理。