2月23日,大连金州重型机器集团正式交付两台千吨级锻焊加氢反应器,将应用于某总投资42.8亿元的炼化项目核心装置。这一突破标志着我国在高端石化装备制造领域实现重要跨越,跻身全球少数掌握超大型锻焊反应器技术的国家行列。
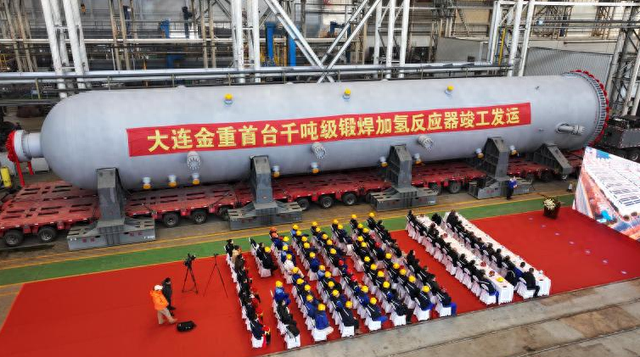
作为炼化装置的核心设备,加氢反应器的制造涉及材料、工艺、检测等多领域协同攻关。此次下线的设备直径5米,单台重量达1187吨,壁厚达270毫米,需在550℃高温、20MPa高压环境下稳定运行。项目技术总工程师刘静介绍,团队重点攻克五大技术难点:材料控制:12Cr2Mo1V锻板纯净度达99.99%,确保抗氢腐蚀性能;焊接工艺:筒体环缝窄间隙埋弧焊技术,实现270毫米厚壁焊接零缺陷;温度控制:研发环形聚能加热器,层间温度波动控制在±3℃以内;智能检测:采用相控阵超声技术,可识别0.4毫米级微小缺陷;结构优化:封头过渡段圆滑度误差小于0.5毫米,降低应力集中风险。经测试,设备焊缝一次合格率达99.3%,抗氢致裂纹寿命超过15年,性能达到国际领先水平。
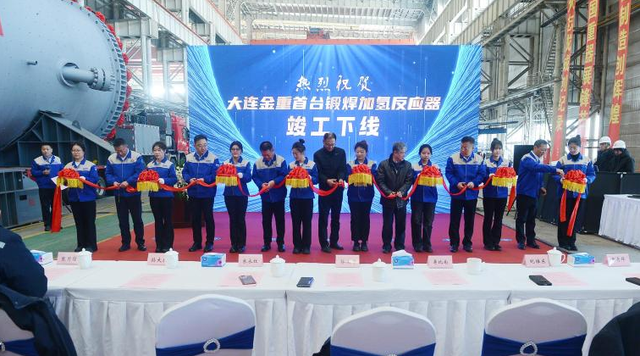
过去,同类高端加氢反应器长期依赖进口。大连金重通过自主创新,实现三大突破性进展:制造周期缩短:相比进口设备,交付时间压缩8个月;成本降低:设备造价较进口产品减少1.2亿元;能效提升:配套装置投用后,柴油硫含量可降至10ppm以下,年减碳2.3万吨。“这是国内首台完全自主设计制造的千吨级锻焊加氢反应器。”项目业主方负责人表示,设备投用后将推动炼化工艺向绿色化、高效化升级。

大连金重党委书记、董事长才红广指出,此次突破使企业成为国内第二家具备千吨级锻焊反应器制造能力的企业,填补了三项行业空白:实现直径5米级锻焊筒体整体成型;掌握12Cr2Mo1V厚壁锻板焊接工艺;建立临氢设备全生命周期质量管控体系。目前,企业已启动2000吨级反应器研发,并布局智能焊接机器人系统,推动厚壁容器制造向数字化、智能化转型。
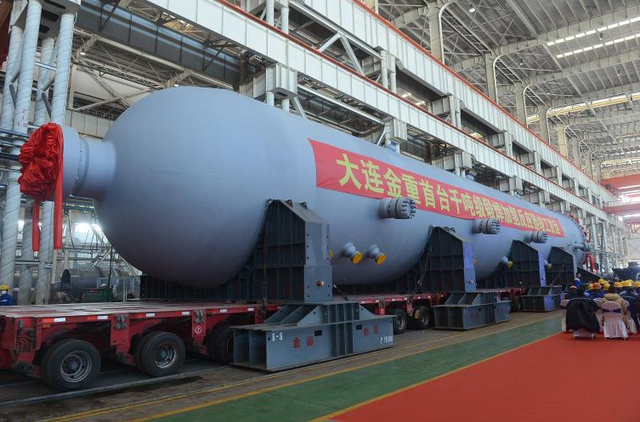
这台“钢铁巨轮”的下线,不仅是装备制造技术的突破,更折射出中国工业的深层变革——从追赶到并跑,从单一设备攻关到全产业链自主可控。当它们驶入炼化装置时,承载的是中国制造向高端攀升的坚实脚步,也是实现能源领域绿色转型的关键支撑。