在建筑施工领域,混凝土的地位无可替代,这种关键的建筑材料对于确保建筑结构的稳固与持久起着举足轻重的作用。然而,在混凝土的配制与施工环节中,一个屡见不鲜的问题便是气泡的生成。
这些微小的气泡,虽然在初期看似无足轻重,但它们不仅会对混凝土的外观造成不良影响,更严重的是,这些气泡有可能会削弱混凝土的整体力学性能和耐久性,从而对建筑的安全性构成潜在威胁。
那么,究竟是什么原因导致了混凝土中气泡的频繁出现呢?本文砼界张博旨在深入剖析这一现象,详尽探讨气泡产生的根源,并针对这一问题提出有效的预防与治理策略。
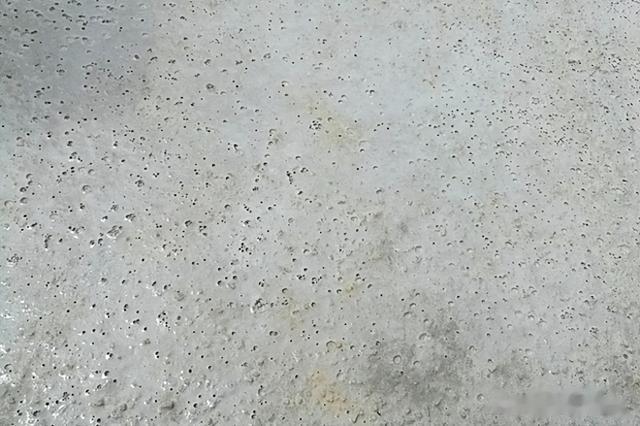

气泡的类别与特性
在深入探讨混凝土中气泡问题之前,我们首先需要了解气泡的不同类别。混凝土中生成的气泡,根据其直径大小,可以被细致地分类。
具体来说,直径超过100μm的气泡被称为“大害泡”,这类气泡对混凝土性能的影响最为显著。而直径在100~50μm之间的气泡,我们称之为“中害泡”,其影响虽不及大害泡,但仍需关注。
当气泡直径缩小到50~20μm范围时,它们被称作“低害泡”或“无害泡”。这类气泡在混凝土中的存在,通常不会对结构性能造成显著影响。更进一步,直径小于20μm的气泡甚至被视为“有益气泡”。这些微小的气泡在混凝土中以均匀且独立的形式存在,为混凝土提供了一定的稳定性。
值得强调的是,当混凝土中的含气量适中时,这些微小气泡能在混凝土内部形成一个稳定的系统。从混凝土结构的理论角度来看,这些由微小气泡形成的空隙实际上属于毛细孔的范围,也被称为“无害孔”或“少害孔”。它们的存在并不会降低混凝土的强度,反而能够在一定程度上增强其耐久性,使混凝土更加坚韧和长寿。
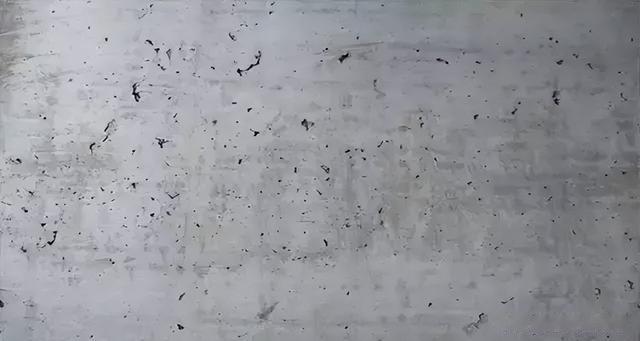

气泡产生的多元因素分析
混凝土中气泡的生成并非偶然,而是受到多种因素的共同影响。下面,我们就来深入探讨这些影响因素。
1.水泥特性对气泡生成的影响
水泥,作为混凝土的核心组成部分,其多项属性对气泡的生成具有显著影响。首先,值得注意的是,在水泥的生产流程中,助磨剂的使用往往会导致气泡的过度产生。这是因为助磨剂可能引入额外的气体或影响水泥颗粒的表面性质,从而增加气泡的形成。
此外,水泥中的碱含量也是一个关键因素。当碱含量偏高时,它不仅可能影响水泥的硬化过程,还会促进气泡的生成。同时,水泥的细度也不容忽视。过于细腻的水泥颗粒更容易包裹空气,导致含气量的上升。
除了上述因素,水泥和水的用量也直接关系到气泡的产生。水的加入量过多或过少都可能影响混凝土的稠度,进而影响气泡的释放和稳定。因此,在混凝土配制过程中,精确控制水泥和水的比例至关重要。
在混凝土的试配阶段,我们主要根据所需的强度来确定水泥的用量。有趣的是,如果在确保混凝土强度达标的基础上适度增加水泥的用量,可以有效地降低水灰比,进而显著减少气泡的数量。这一策略的核心思想是利用多余的灰浆来填补混凝土中的微小空隙,从而阻断气泡形成的空间,使混凝土结构更加密实和坚固。
2.外加剂对气泡生成的影响
在混凝土的制备过程中,外加剂的使用对气泡的生成具有显著的影响。当我们观察到混凝土中存在大量的大气泡时,这往往与外加剂中的引气成分密切相关。具体来说,一些常用的外加剂,如减水剂或复合型泵送剂,可能会掺入含有引气功能的成分。这些引气剂在混凝土中起到了引入气体的作用,从而导致气泡的产生。
值得注意的是,随着减水剂用量的增加,混凝土中的气泡数量也会相应上升。这是因为减水剂在改善混凝土工作性能的同时,也可能促进了气泡的形成和稳定。
3.粗细骨料对气泡生成的影响
在混凝土的构成中,粗细骨料的配比与选择对气泡的生成具有重要影响。根据粒料级配密实原理,合理的骨料级配能够有效减少混凝土内部的空隙,从而降低气泡产生的可能性。然而,在施工过程中,若材料级配不合理,便可能为气泡的生成提供条件。
具体来说,当粗骨料偏多或骨料大小选择不当时,会导致混凝土内部出现较大的空隙。这些空隙不仅影响混凝土的密实性,还为气泡的形成提供了空间。此外,针片状颗粒含量过多也是一个不利因素,因为它们难以有效填充空隙,进一步加剧了气泡问题。
另一方面,实际施工过程中使用的砂率也是一个关键因素。若实际使用的砂率低于试验室推荐的砂率,细粒料将无法充分填充粗粒料之间的空隙。这种不密实的结构不仅会降低混凝土的强度和耐久性,还会为气泡的生成创造有利条件。
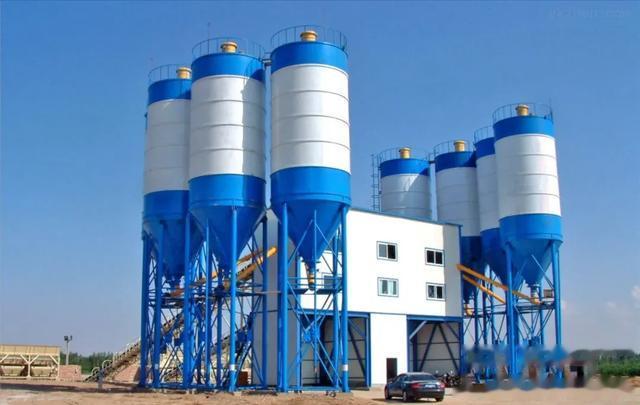
4.搅拌时间对气泡生成的影响
在混凝土的制备过程中,搅拌时间是一个至关重要的参数,它对混凝土内部气泡的生成有着显著且复杂的影响。适宜的搅拌能够确保混凝土各组分的均匀混合,进而形成均质、密实的结构。然而,搅拌的不均匀或搅拌时间的不足,都可能引发一系列问题。
当混凝土搅拌不匀时,即便水灰比保持一致,外加剂在混凝土中的分布也会变得不均匀。这种不均匀分布会导致外加剂富集的区域产生更多的气泡。相反,在未充分拌合到外加剂的部分,混凝土可能会出现坍落度不一致、坍损增大以及离析等质量问题。
然而,搅拌时间并非越长越好。过分的搅拌同样会带来问题,因为它会使混凝土在搅拌过程中吸入更多的空气,从而导致气泡数量不断增加。这些多余的气泡不仅会影响混凝土的密实性和强度,还可能在其硬化后形成可见的孔洞,影响结构的外观和耐久性。
5.脱模剂的选择对气泡生成的影响
在混凝土施工过程中,脱模剂的选择对气泡的生成和混凝土结构的最终质量具有不可忽视的影响。目前,一些施工单位仍然沿用纯油类脱模剂,尤其是常使用从机械厂回收的废机油。这种废机油对气泡展现出极强的吸附能力,一旦混凝土内部的气泡与之接触,便很容易被吸附在模板上,最终在混凝土结构的表面形成明显的气泡痕迹。
为了减少气泡的产生,施工单位在选择脱模剂时需要格外谨慎。除了避免使用对气泡吸附性强的废机油等纯油类脱模剂外,还应根据模板的材质和特性进行适配性选择。不同的模板材料对脱模剂的要求也不尽相同,因此,选用与模板相匹配的脱模剂至关重要。
通过合理选配脱模剂,并结合模板的类别进行适应性的选择,可以有效地降低混凝土中气泡的含量,提高混凝土结构的整体质量。
6.振捣操作对气泡生成的影响
在混凝土施工过程中,振捣操作是一个至关重要的环节,它不仅影响着混凝土内部的密实性,还对混凝土表面气泡的产生和排出有着显著的影响。由于施工现场的环境差异以及振捣操作人员的技能水平不同,振捣的效果也会有所差异,进而影响着混凝土表面气泡的数量和大小。
振捣的优劣直接关系到混凝土内部结构的密实性。从分层振捣的角度来看,分层的高度是一个关键因素。若分层过高,混凝土内部的气泡将更难以被有效排出,从而影响混凝土的整体质量。
此外,振捣器的插拔速度也是一个重要的操作要点。为了确保混凝土上下层能够均匀受振,振捣器在插入时应迅速,使得混凝土在几乎同一时间受到振捣作用。而在拔出时,则需要缓慢进行,以避免因振捣器拔出过快而形成的空隙,这样的空隙会阻碍气泡的顺利排出。
然而,在实际操作中,超振、欠振和漏振等现象时有发生,这些不当的振捣方式都会对混凝土表面气泡的产生造成不利影响。超振会导致混凝土内部的微小气泡在机械力的作用下破灭并重新组合,最终形成更大的气泡。而欠振和漏振则会使混凝土出现不密实的情况,进而产生自然空洞或不规则的大气泡,严重影响混凝土的结构性能和外观质量。
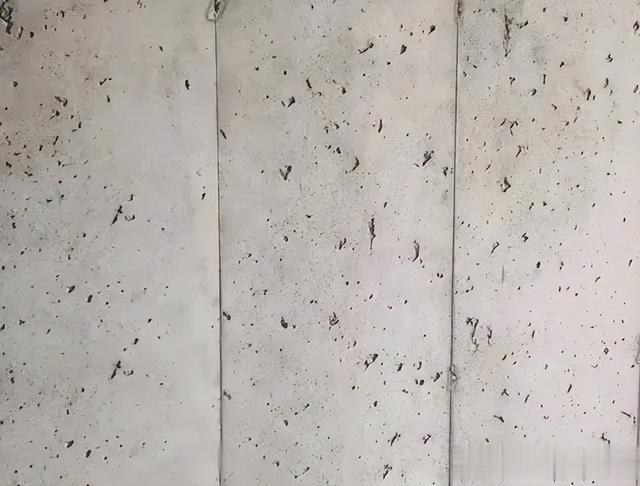

气泡的控制及预防改善策略
(1)原材料层面
1.强烈推荐选用在加工过程中气泡产生较少、含碱量低的水泥品种。这类水泥不仅能有效抑制气泡的生成,从源头上减少混凝土中的气泡数量,还能提高混凝土结构的稳定性和耐久性。通过选择这样的水泥,我们可以更好地控制混凝土的质量,确保其满足各种工程需求。
2.关于外加剂的使用,建议施工单位与外加剂生产厂家保持密切沟通。在配制过程中,双方应共同确保各种成分的掺量得到严格控制。这样做不仅可以优化混凝土的整体性能,包括提高其工作性、强度和耐久性,还能显著减少混凝土中气泡的产生。通过与生产厂家的紧密合作,施工单位可以更加精准地调整外加剂的配比,从而达到提升混凝土质量、减少气泡的目的。
3.骨料作为混凝土的重要组成部分,其选择同样不容忽视。我们必须对材料质量进行严格把关,特别是在骨料的粒径级配和针片状颗粒含量方面,要进行细致的筛选与控制。在备料环节,任何不符合标准的材料都应被剔除,以保证所选用骨料的品质。通过这样做,我们可以确保混凝土的骨料级配和砂率达到最优,进而提升混凝土的整体性能,并有效减少因骨料问题而引发的气泡等质量问题。
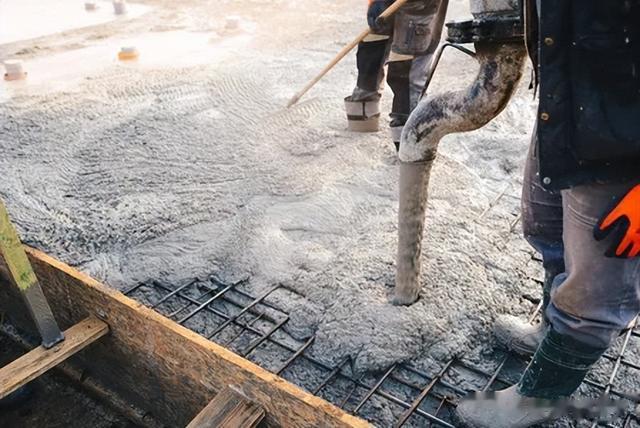
(2)施工工艺层面
1.搅拌时间的精确掌控在混凝土制备过程中占据着至关重要的地位,它直接关系到混凝土成品的质量。我们必须确保外加剂与混凝土中的其他原材料能够充分且均匀地混合。为了达到这一目的,我们必须严格遵守相关的行业标准。根据国家标准《预拌混凝土》GB/T14902的“7.5.2”条款,明确要求每盘混凝土的搅拌时间,自所有材料完全投入后开始计算,至少应持续30秒。当制备C50或更高强度级别的混凝土时,或者配方中加入了引气剂、膨胀剂、防水剂等特殊添加剂,搅拌时间还需要相应增加。这样的规定是为了保证混凝土内部各组分能够更充分地反应和结合,从而确保混凝土的最终强度和使用性能。因此,在实际操作中,我们必须严格遵守这些规定,以确保混凝土质量的稳定性和可靠性。
2.施工单位在挑选脱模剂时,应把品质放在首位,确保所选产品具有良好的脱模效果和稳定性。同时,施工单位还需仔细检查所使用的模板与所选脱模剂是否相互兼容、匹配。为了获得最佳的脱模效果,模板的表面必须保持光洁平滑,无任何瑕疵,这样可以减少混凝土表面出现瑕疵的可能性。在涂抹脱模剂时,施工人员需要确保涂抹均匀且量要适中,既不过厚也不过多,以避免脱模剂在混凝土表面形成残留,从而影响混凝土的外观质量和整体性能。通过这样的精细操作,可以保证混凝土构件顺利脱模,同时获得理想的表面效果。
3.在混凝土振捣环节中,施工单位必须高度重视操作技术的运用。建议采用分层布料与分层振捣的施工策略,且每层混凝土的厚度应控制在50厘米以内,这样的设计有助于混凝土内部的气泡更有效地逸出。此外,振捣作业过程中应严格遵守“快插慢拔”的操作原则,即振捣器应迅速插入混凝土中,然后缓慢拔出,以避免造成混凝土的欠振、漏振或超振等问题。通过这些精细化的操作管理,可以显著提升混凝土结构的密实度和整体性,进而保障工程质量和使用安全。
综上所述,混凝土中气泡的生成并非单一原因所致,而是由多种复杂因素交织影响的结果。为了制造出高品质的混凝土结构,我们必须从源头抓起,对原材料进行严格筛选与把控,同时,对施工工艺进行精细化管理和优化也至关重要。通过全方位的综合控制,我们可以有效减少混凝土中的气泡,进而提升建筑结构的稳固性和耐久性,确保建筑物能够安全、长久地服务于社会,满足人们的使用需求。

混凝土气泡的修复方法
针对混凝土气泡的修复工作,我们需要根据具体情况制定相应的策略。一旦发现混凝土表面出现气泡,我们首先要做的是对气泡的尺寸进行仔细的检查与评估。
对于那些尺寸较小的气泡,我们有一种高效且多功能的解决方案——使用混凝土色差修复剂。
这种特殊的修复剂不仅能精细地填补这些微小的气泡,还能增强混凝土的美观度,并为其增加防碳化等多重保护,实现了既修复又美化的双重效果。
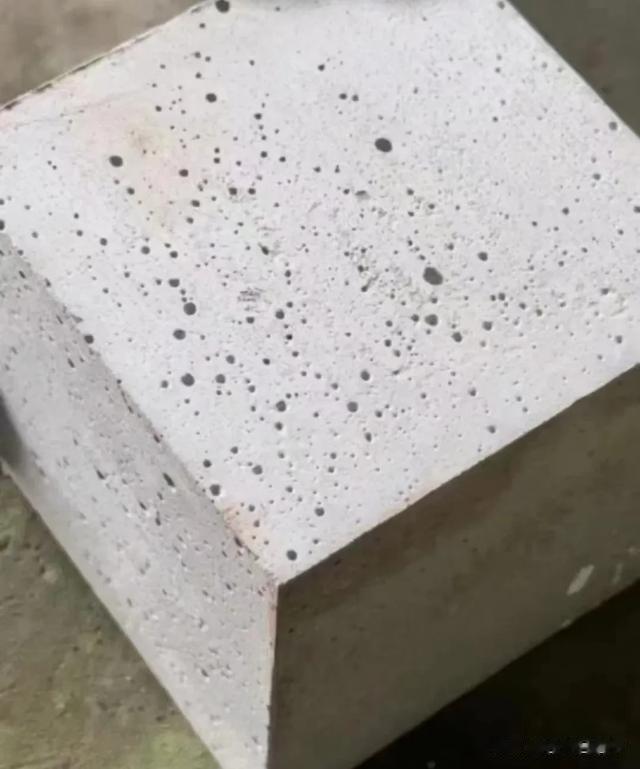
修复前

修复后
若遇到更大范围的气泡问题,我们会推荐采用整体喷涂的方法来进行处理。这种方法能确保修复后的混凝土表面呈现出更加统一、自然的外观,有效避免了局部修补可能带来的视觉上的不协调。
对于那些直径较大的气泡孔,我们有专门的修复方案。建议使用XB型快速修补料,通过3毫米的薄层进行精确的填补和修复。
为了提升修复效果,可以先对气泡孔表面进行凿毛预处理,增加修补料的粘附力。
如果在修复过程中出现表面痕迹或色差问题,混凝土色差修复剂将再次发挥关键作用,它能够轻松实现混凝土表面的统一和美化,确保修复效果的完美呈现。
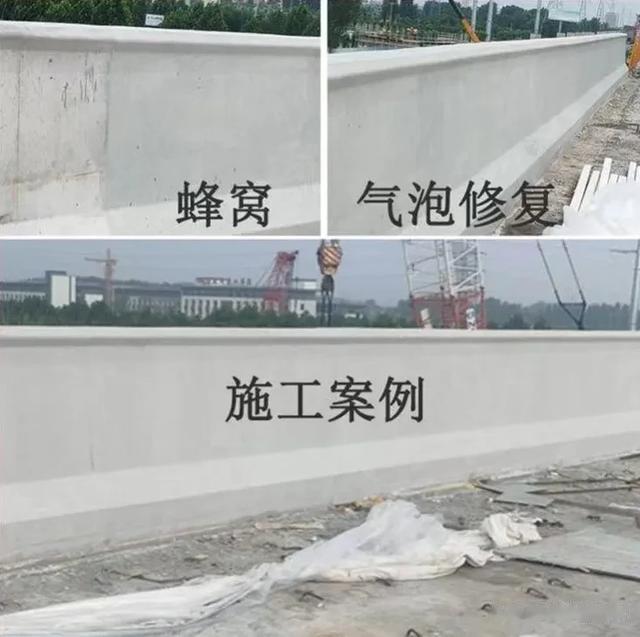