异形结构盒体封装封焊的工艺优化
姜永娜,赵华
(中国电子科技集团公司)
摘要:
利用90°固定角度工作平台的平行封焊设备实现了对八边形异形结构盒体的封装。研究了封焊设备的电极宽度和角度、封焊轨迹的选择、封焊工艺参数的优化及焊缝宽度的控制对封装后的焊缝形态、盒体气密性和内部多余物等方面的影响。结果表明,通过改变设备电极尺寸,采用圆形封焊轨迹及优化工艺参数后,实现了对八边形异形盒体的平行缝焊。封焊后产品的气密性和粒子碰撞噪声检测合格率分别达到100%和95%。该封焊方法打破了90°固定角度平行缝焊机只能封装矩形和圆形盒体的固有认知,适合小批量多型号混合集成电路的封装。为实现低成本的多边形异形盒体的平行缝焊提供了思路和实践支撑,满足了工业生产要求。
针对不同盒体的材料和形状,微波混合集成电路封装通常采用的封焊方式有储能焊、钎焊、平行缝焊和激光焊等。储能焊适用于盒体或管帽结构一边有连续的金属凸起的盒体。但在封焊加压过程中容易产生多余物,从而造成产品失效 [1] 。钎焊适用于陶瓷盒体和金属陶瓷盒体,一般采用Au80Sn20焊料片,工艺温度至少达到280 ℃,不适用于盒体内部含有低温焊料或不耐高温的基板及电路元件的产品。激光封焊可用于铝等高热导率材料为主的金属材料盒体的封焊,封焊过程中温升小,且其封焊路径选择较为灵活,可兼容不同形状盒体,但要求盖板不能叠放于盒体封口环之上,且对盖板与盒体间的缝隙宽度要求严格,因此对盒体加工精度要求较高。其封焊速度取决于激光束的移动速度,效率低,对于20 mm×20 mm以下的盒体尺寸,封焊速度约为15 只/h,不能满足批量生产要求。平行缝焊适用盒体的材料以可伐等高热阻材料为主,无需焊料。只在封焊过程中由电极与盒体形成的回路中通以大电流而引起盒体的小幅度温升。适用于盒体内部电路元器件、基板材料及装配方式复杂的各类混合集成电路。平行缝焊的盒体能够承受高机械应力和热冲击,封焊成本低,效率高,适用于自动化生产 [2] 。
多边形异形盒体是目前小型化微波混合集成电路采用较多的盒体形式,主要是指封口环为多边形的盒体。多数平行缝焊设备采用脉冲马达,工作台只能实现90°固定角度旋转,因此可封焊的盒体形状以矩形或圆形为主,无法进行异形盒体的封装。日本某公司通过伺服马达360°旋转底座,工作台可任意设定旋转角度,实现异形盒体的平行缝焊。但该设备价格昂贵,成本高,适合单一品种的大批量生产,而众多中小企业则希望能在不增加设备成本的前提下,实现多品种小批量产品的封焊。
本文利用90°固定角的平行缝焊机对八边形盒体进行封焊实验,通过选择合适的封焊路径,优化平行缝焊机的电极结构和封焊工艺参数等,实现了对八边形异形盒体的封焊,并对封焊后的盒体进行了气密性实验和粒子碰撞噪声(PIND)实验等。
1 实验方法
盒体封口环为八边形轴对称图形,采用可伐材料加工,工作频率高,为减小盒体尺寸,将安装孔置于矩形盒体四个角的内侧,导致电路安装区域及封口环成为八边形,如图1所示,盒体尺寸为20 mm×14 mm,盒体输入输出端采用绝缘子引出,试验采用的平行封焊设备为某公司的平行缝焊机。
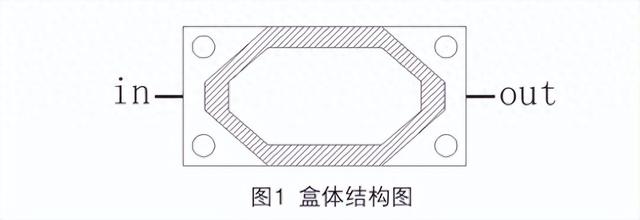
1.1 封焊轨迹的选择
该平行缝焊机电极只能做平行运动,无法改变角度,异形结构封焊图形不规则,大胆设想采用圆形封焊模式,利用圆形封焊的运动轨迹路径来实现异形结构的封焊。电极在封焊运动过程中,只要电极与异形结构边有交集点,就会产生接触电阻,从而实现封焊。如图2所示,电极按照圆的运行轨迹,以顺时针方向来实现异形封装。封焊过程中,不同的封焊位置,所用电极的位置是不同的,封焊 a 点所用电极位置和封焊 b 点所用电极位置是不一样的,这与矩形封焊模式是不同的。
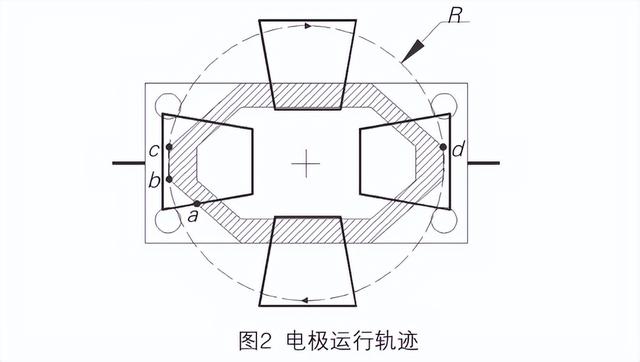
圆形封焊模式,要确定中心点和圆的直径,就可以确定电极封焊运动轨迹。由于盒体对称,根据盒体的中心点就可以确定封焊的中心点。图2中,十字标注为中心点,以异形盒体最长的两条边来确定封焊直径, b 点到 d 点的距离就是封焊的直径。保证覆盖所有的异形边都能封焊。
1.2 电极的优化
电极的优化,主要通过增加电极的宽度和改变电极角度两方面的改进,从而保证异形结构盒体封焊的质量。电极材料要导电性好,电极在工作过程中电流传递越快,焊点便能越好的形成,使用了铜合金的材料。
常规缝焊时,电极形状如图3所示,通用电极参数为:电极直径 d =12 mm,电极宽度 W =5 mm,电极角度 θ =10°。没有特殊要求,按照设备厂商提供的电极不会轻易改动。由于异形盒体封焊的特殊性,通用电极无法满足使用要求,因此对电极的形状做出改进。
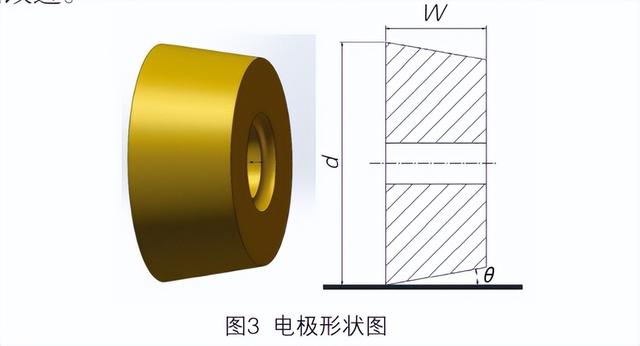
在试验中发现电极的宽度5 mm覆盖不了异形多边形的所有边,如图4所示。电极顺时针运动,接触不到异形的最长边,缝焊就会出错。故电极的宽度必须大于 H ,这样才能保证覆盖到每个边。
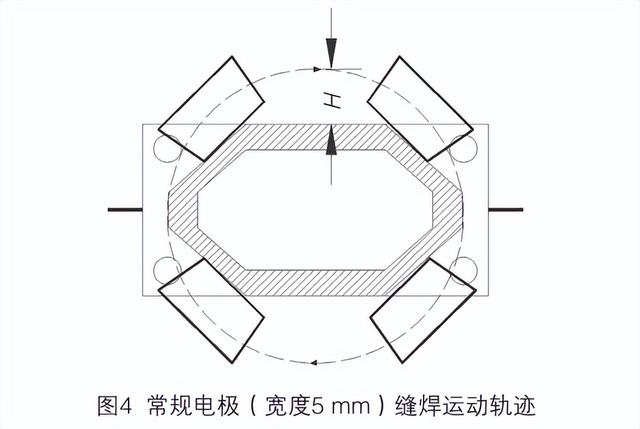
电极的角度指电极的斜切面与水平面直径的夹角 [3] θ 。电极的角度 θ 决定在封焊过程中电极与盖板接触面积的大小 [4] ,电极角度越小,在封焊参数不变的情况下,封焊过程中电极与盖板交集处的面积会越大,封焊的热量更能均匀地施加到封焊环处,封焊的高度(焊缝宽度)会变宽。反之 θ 越大,电极与盖板交集处接触面积小,封焊的高度(焊缝宽度)会变窄。
以设备厂商推荐电极直径 d =12 mm,电极宽带W =5 mm不变的情况下,通过改变不同电极角度来对比封焊的焊缝宽度,见表1。
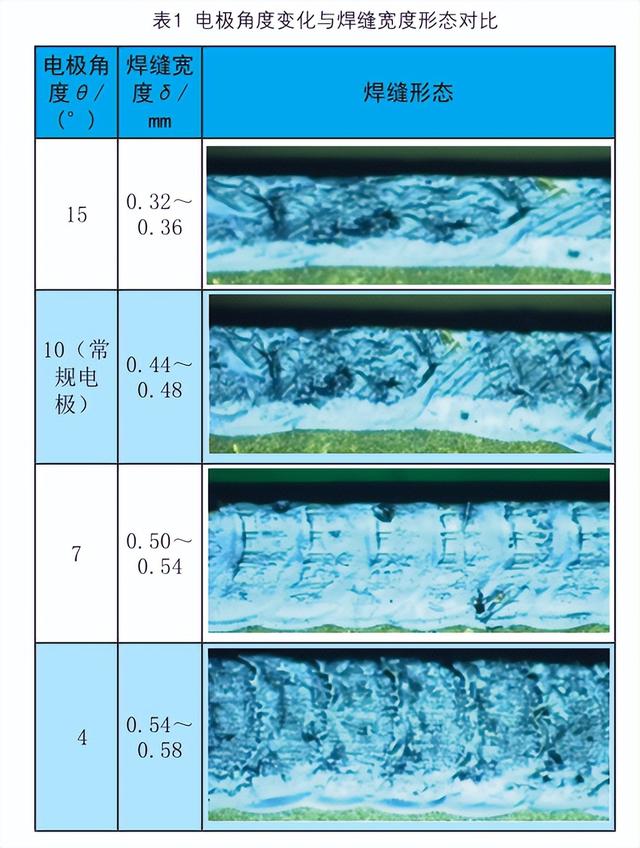
常规电极封焊的焊缝宽度在0.5±0.1 mm,适当减少电极角度,能保证异形每个边交集部位焊接的质量。由于电极是消耗器材,我们加大电极的直径,这样可以多次维修使用。最终从电极的角度,宽度,直径参数都做了改进,来保证异形结构每个边封焊质量。图5为电极改进前后对比图。
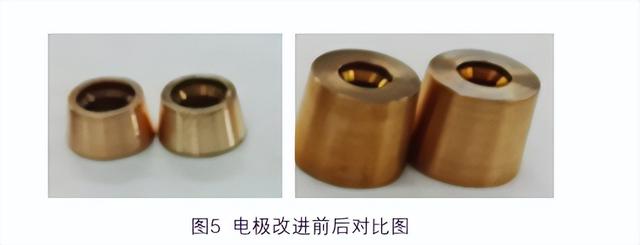
1.3 工艺参数优化
要获得封装合格的封焊,除气密性要求外,PIND也要满足用户要求,以最小的焊接能量获得最佳的熔焊效果,从而达到封焊的目的。焊接能量太小,气密性不合格,焊接能量太大,会有自由移动的粒子,PIND会不合格。
焊接能量指电极与盖板接触时形成闭合回路,接触瞬间产生接触电阻,产生大量的热量,从而完成盒体与盖板的熔融。焊接能量主要由几个工艺参数决定,与参数的关系如公式(1)所示。
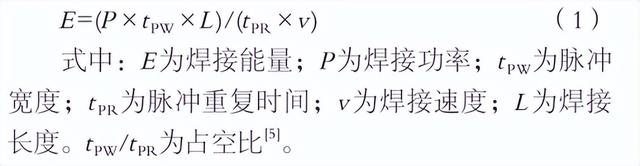
占空比是封焊中比较重要的参数。占空比越大,传送到盒体焊接的能量越大,封焊过程中的产生热量很高,盒体温升很高,持续温升会对盒体里面的电路造成热冲击,甚至损伤电路元器件而提前失效。焊接速度与焊接能量成反比,焊接速度越慢,其他条件不变情况下,所需焊接功率会变大。缝焊主要通过占空比、焊接速度和焊接功率等参数的调整,以最小的能量提供最佳的重叠熔化区,来完成封焊。
为了获得最佳的盒体温升,既能保证缝焊质量,又不影响盒体里面电路元器件的可靠性,试验中把Sn43Pb43Bi14焊料片(熔点为143 ℃)放入被封焊的盒体中,通过改变焊接工艺参数(焊接功率、占空比和焊接速度),来观察焊料片是否熔化,从而选择合适的工艺参数。焊接参数见表2。
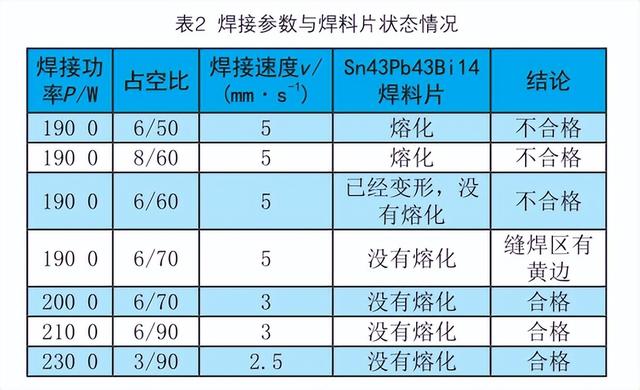
试验中发现,焊料片熔化,说明盒体温升大于焊料片的熔点,对于贴装元器件的产品可能存在二次熔化,可靠性存在隐患。而占空比小于1:10,再通过提高焊接功率以及降低焊接速度,能有效解决焊接过程中盒体的温升问题,同时保证封焊的质量。
1.4 工序参数的优化
在圆形封焊模式试验过程中,盖板的好坏,封焊工艺参数,以及程序中的小细节的变动,都会影响着封焊的质量。试验中经常碰到的问题主要有打火现象以及封焊有缺口等问题。针对这些问题现象描述,表3给出问题的定位分析以及解决方案。
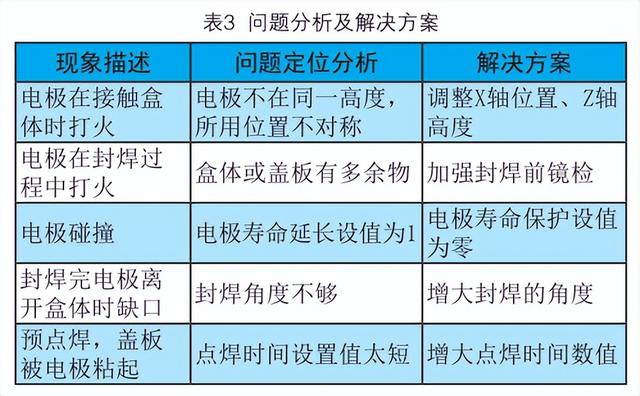
2 结果与分析
通过工艺参数和电极的改进,以及工作中工序参数的一系列改进措施,对20只异形结构产品封焊,封焊后的实物如图6所示,显微镜下观察,封焊盒体周围都能看到连续的熔融物,表明外观目检焊缝是合格的。
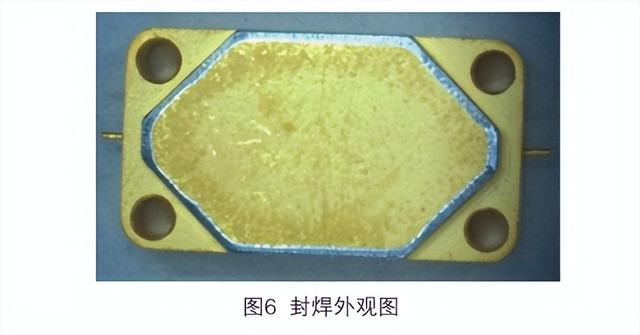
对实验的20只样品,按GJB548方法1014和GJB548方法2020条件A分别进行了气密性和PIND检测摸底。气密性合格率为100%,PIND合格率为95%,均满足要求。
图7为不同尺寸异形结构封焊外观图。
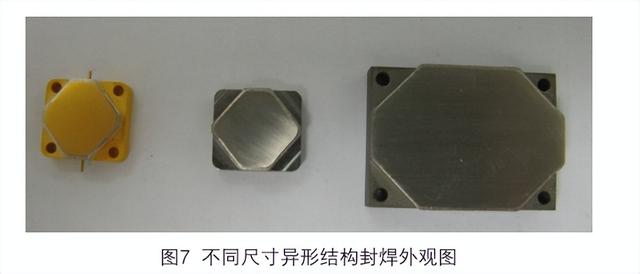
3 结论
本文通过对平行缝焊机选择合适的封焊轨迹,对电极结构和工艺参数等方面进行优化,实现了多边形盒体的封装,并对封焊后盒体气密性和多余物等方面性能进行了检测,验证了利用工作台旋转90°固定角的平行缝焊机封焊多边形盒体方法的可行性。结果表明,采用圆形封焊方式后气密性达到100%,PIND达到95%。打破常规平行封焊只能封装矩形和圆形盒体的认知,为低成本的多边形盒体的平行封焊提供了理论和实践支撑。