电子浆料用微细金属粉体材料研究进展
刘祥庆 孙海霞 江志 张煦 张彬 王建伟 贺会军 汪礼敏
(有研粉末新材料股份有限公司 金属粉体材料产业技术研究院 有研粉末新材料(合肥)有限公司 北京有研粉末新材料研究院有限公司)
摘要:
电子浆料是电子信息行业的基础材料,广泛应用于航空、航天、电子信息、通信设备、汽车工业等诸多领域。随着电子信息快速化、高集成化的发展趋势,作为导电相的金属粉体材料要求具备高纯、形貌可控、无团聚、粒径可控且分布窄、氧含量低等特点。本文总结了电子浆料的主要用途,并对微细金属粉体材料的制备方法进行分析,提出了球形、片状微细金属粉体材料制备技术及应用的发展方向。
微细金属粉体是指颗粒尺寸介于0.1~10 μm的粉末集合体,具有比表面积大、表面活性较强、烧结温度低、导电性和导热性较好等优点,在电子浆料[1-3]、润滑剂、催化剂、医学和生物等领域[4-6]都有广泛的应用,已成为特殊功能材料研究和开发的重要课题之一。近年来,随着电子行业的迅速发展,将微细金属粉体材料应用于导电浆料成为行业内外研究和开发的热点。
电子浆料通常是指自20 世纪60 年代以来开发的新型功能性浆料,是一种集冶金、化工、电子技术于一体的电子功能材料,广泛应用于关键电子元器件、光伏/新能源、新型显示、微电子封装等领域,对微电子器件的小型化起着重要作用。
20 世纪60 年代以来,美国先后有ESL、Englehard、Cermalley、Ferro、EMCA、杜邦等多个公司开发、制造、销售各类电子浆料。欧洲著名的公司有Heraeus、德固萨、菲利浦等。80 年代后,日本逐渐发展成世界上主要的浆料生产国,著名的浆料公司有住友金属矿山、昭荣化学、田中贵金属所、村田制作所、太阳诱电等。我国企业涉足电子浆料比较晚,主要是80 年代后期,以昆明贵金属和4310 厂为代表,应用上主要以导体浆料(银浆、铝银浆)为主。国内生产的电子浆料大多是中、低端产品,种类少、性能不稳定,高性能浆料仍处于发展初期。
1 电子浆料及其应用
1.1 电子浆料的组成
电子浆料主要由导电相、粘结相和有机载体三部分构成,此外还添加稀释剂和有机添加剂等。其制备工艺是首先将原料混合均匀,然后经三辊轧机均匀研磨,形成具有一定流变特性并且满足印刷要求的浆料。最终,通过丝网印刷印在玻璃片或陶瓷基片上,经激光、高温烧结等固化工艺制成厚度为几微米到几十微米的导电膜层。
按照电子浆料的用途不同可以分为导电浆料、电阻浆料、厚膜浆料、介质浆料和焊接浆料。按照浆料固化条件不同,又可以将其分为高温(大于1 000 ℃)烧结型电子浆料、中温(300~1 000 ℃)烧结型电子浆料和低温(100~300 ℃)固化型电子浆料。同时,又由于电子浆料的组成不同,分为贵金属浆料、非贵金属浆料及复合成分浆料。
导电相也称为功能相,决定了浆料的电性能,并影响着固化膜的物理和机械性能。电子浆料用的导电相有碳、金属、金属氧化物三大类。常用的金属导电相主要包括银、镍、铜、铝、合金等[7-10]。导电相对浆料性能有显著影响,主要表现在含量、形貌、粒径、表面性质等几个方面[11]。粘结剂的主要作用是为浆料提供粘附力,使浆料膜层与基板牢固结合,粘结剂的含量一般为2%~10%,主要有玻璃型、无玻璃型和混合物型三类。有机载体是溶解于有机溶剂的聚合物溶液,主要由有机溶剂和增稠剂等组成。
1.2 电子浆料的应用
电子浆料以高质量、高效益、技术先进、适用广等特点在信息、电子领域占有重要地位,是混合集成电路、敏感元件、表面组装技术、电阻网络、显示器、以及各种电子分立元件等的基础材料,可制成厚膜集成电路、电阻器、电阻网络、电容器、导体油墨、太阳能电池电极、LED冷光源、印刷及高分辨率导电体、薄膜开关/柔性电路、导电胶、敏感元器件及其他电子元器件[12],广泛应用于航空、航天、电子计算机、测量与控制系统、通信设备、医用设备、汽车工业、传感器、高温集成电路、民用电子产品等诸多领域。
1.2.1 关键电子元器件
电子浆料主要作为电极材料应用于RCL(电阻、电容、电感)元器件中,其中,片式多层陶瓷电容器(MLCC)、片式电感(MLCI)、片式电阻(R-Chip)应用最为广泛,此外,在微波器件、压电陶瓷、PTC元件、传感器件等领域也具有广阔的应用前景。
根据全球电子元件行业协会ECIA 的数据,2019 年电容、电感、电阻市场规模达277 亿美元,约占被动元件市场的89%,如图1 所示。其中电容市场占比为65%、电感市场占比为15%、电阻市场占比为9%。根据测算,预计2025 年全球MLCC 电极金属粉体市场规模将达到145 亿元,如图2 所示。
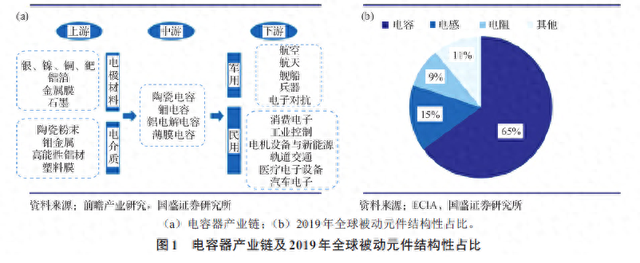
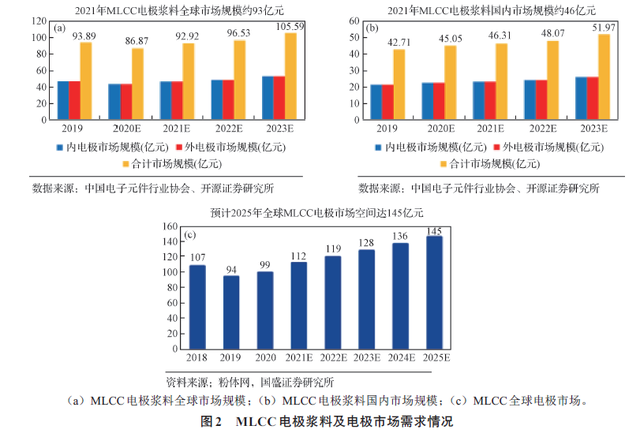
关键电子元器件市场和技术均掌握在日、韩、台等企业手中。目前MLCC 高端技术被日本企业掌握,已可生产800~1 000 层的MLCC,介质厚度逼近0.5 μm,国内厂商仅可提供300~700 层的MLCC,MLCC行业现状如表1 所示。
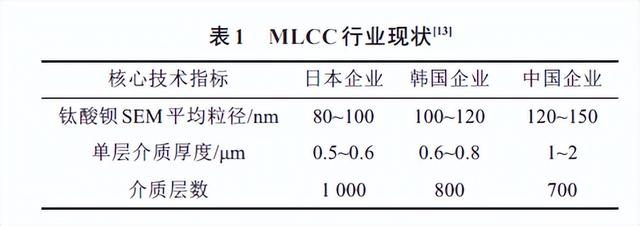
电极是电子器件的重要组成部分,决定了器件的导电性能。传统的内电极材料多为贵金属,Pd、Au、Ag等贵金属价格高,使其制作成本不断增加,限制了其发展和应用范围。目前研究最多、应用最为广泛的是银/镍内电极材料,铜在端电极方面应用广泛。
电阻浆方面,因其技术要求高,开发成本高的特点,国内尚没有进行产业化生产,处于高度垄断状态,目前只有住友、杜邦、田中贵金属等少数几家公司生产。
关键电子元器件领域主要产品及应用如表2所示。
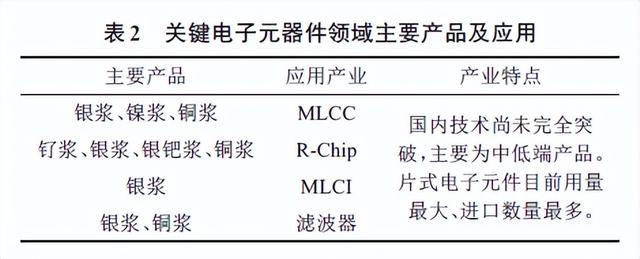
1.2.2 新型显示
新型显示泛指LCD、OLED、AMOLED、Mini/Micro-LED、QLED、印刷显示、激光显示、3D 显示、全息显示、电子纸柔性显示、石墨烯显示等技术。电子浆料广泛应用于新型显示、导电、导热、屏蔽等领域,例如触摸屏银浆、柔性线路板低温银浆等,新型显示领域的主要产品及应用如表3 所示。
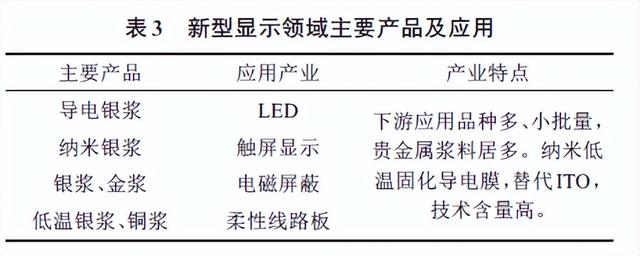
1.2.3 微电子封装
随着电子产品轻、薄、短、小的发展趋势和微电子技术的不断更新,微电子封装技术因其高密度和高性能的特点正逐渐进入超高速发展时期,已成为当前电子封装技术的主流。
目前的集成封装技术主要有薄膜技术、硅片半导体技术、多层电路板技术以及共烧陶瓷技术。其中共烧陶瓷技术分为两类,即高温共烧陶瓷(HighTemperature Co-fired Ceramic,HTCC)与低温共烧陶瓷(Low Temperature Co-fired Ceramic,LTCC)。HTCC因其烧成温度高,不能采用金、银、铜等低熔点金属材料,必须采用钨、钼、锰等难熔金属材料,但这些材料电导率低,会造成信号延迟等缺陷,所以不适合做高速或高频微组装电路的基板。但是,由于HTCC 基板具有结构强度高、热导率高、化学稳定性好与布线密度高等优点,在大功率微组装电路中具有广泛的应用前景。LTCC,是一种将未烧结的流延陶瓷材料叠层在一起而制成的多层电路,内有印制互联导体、元件与电路,并将该结构烧结成一个集成式陶瓷多层材料,内外电极可分别使用银、铜、金等金属,在900 ℃下烧结,成为目前最具潜力的电子元器件小型化、集成化和模块化的实现方式。
微电子封装领域主要产品及应用如表4 所示。
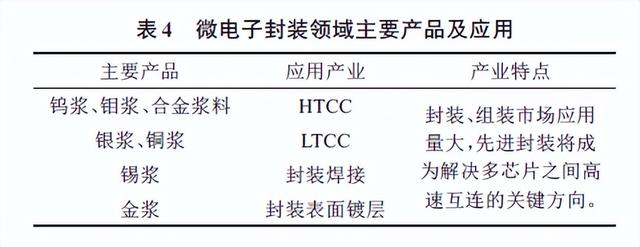
1.2.4 其他
电子浆料也可作为导电、导热相,应用于PCB线路板、导电胶等产品中。例如塞孔材料,主要为PCB 产品有高导热、高可靠性的需求而开发,可应用于手机、数码相机、车载导航、航空电子等电子产品,提高产品的散热性能及可靠性。金属网格填缝材料是运用金属网格技术制作大型触控屏的首选材料,作为导电油墨,打印导电电路图案,可适用PET 和PE 等基材,从而满足RFID和透明柔性电路等低成本规模制造。
2 微细金属粉体制备技术
微细金属粉体的制备方法主要包括气相沉积法、化学还原法、羰基法、电解法、雾化法、机械粉碎法等。为满足电子浆料的应用需求,对导电相金属粉的如下要求:纯度高、导电性好;粒径小、粒径分布窄;形貌规则,为球形或片状;表面抗氧化,与浆料适配性好。目前,开发的球形粉末制备技术主要有物理气相沉积(PVD)法、超高压水雾化法、化学还原法;片状粉末制备技术主要有机械破碎法、化学还原法。
2.1 物理气相沉积法
物理气相沉积(PVD)法,是一种使金属在气体状态下发生物理变化或者化学反应,最后在冷却过程中凝聚长大形成微纳米粒子的方法。金属粉体的形貌粒度受到其晶体结构、蒸发温度、惰性气体的压力和对流情况、装置内的温度梯度、基底及其散热设计等因素的影响[14]。加热方法可以是电阻、高频感应、电子束轰击、等离子轰击或激光和辉光等离子溅射等。
采用PVD 法制备金属粉末,主要分为三个阶段:首先,金属物料受热蒸发形成金属蒸气;其后,金属蒸气在惰性保护气氛中扩散进入冷凝区冷却为固态晶核并发生相互碰撞、融合、凝聚,形成金属颗粒,该过程中,晶核将在生长临界温度下的区域停止生长;最后,生成的金属颗粒随惰性气体在收集器中对流,缓慢沉积于收集器表面。
在PVD制粉工艺中,粉体颗粒的形成过程包括成核和生长两个阶段,按照成核理论,形成稳定核胚的临界半径为:

式中,r0 为表面自由能,Δgv 为气固两相的体积自由能之差。在气相形核过程中,δ 变化不明显,r0则主要取决于Δgv。在气相向固相转变过程中,Δgv直接决定于过饱和度P/P0,P0为一定温度下的平衡蒸气压,P 为实际蒸气压。在实际过程中,高过饱和度主要是靠造成大温差即高温蒸发低温冷凝来实现的。气相形核主要受到气固两相体积自由能的影响,只有过饱和度足够大的体系才能在气相中均匀成核而得到微纳米粒子。为了得到微纳米粉体颗粒,其晶核的长大过程必须严格控制,长大速率除与浓度有关外,更与温度相关[14]。
采用该方法,昭荣化学工业株式会社发明了一种金属粉末制造用等离子体装置,采用该装置,可以制造0.01~10 μm左右的导电性金属粉末,作为导体被膜、电极,在制造电子电路或配线基板、电阻、电容器、IC 组建等电子部件时使用[15]。博迁新材自主研发了PVD设备,主要用于MLCC电极用金属粉末的生产。Tony Addona 等采用PVD法制备金属粉末,通过调节工艺参数可制得粒径为0.1~1.5 μm的高结晶度球形金属粉体[16]。
2.2 超高压水雾化法
超高压水雾化法,是通过喷嘴由高速气流或超高压水流将金属液体雾化破碎成大量细小的金属液滴,获得超细金属粉体的方法。相比于普通水雾化制粉,超高压水雾化可以大大提高细粉收得率,且可制备得到粒度细小、振实密度高、球形度好的金属粉末。雾化制粉的核心技术是雾化器喷嘴设计、介质选择、流速、熔炼方式和漏嘴结构等。
雾化过程一般包括3 个步骤[17]:(1)最初颗粒的形成,即由熔融金属形成原始的液滴;(2)原始液滴破碎成颗粒,称为二次颗粒形成(二次雾化);(3)颗粒之间形成小的聚合。对于高压水雾化而言,在最初的液滴形成过程中,熔融的金属液流在雾化交点之前已经发生液体紊流,形成原始的液条带;原始的液带不断继续分离成原始的液滴,这个过程称为原始液滴的形成(一次颗粒)。原始液滴在水的冲击下发生破碎即二次雾化;形成的颗粒在飞行或下落时有少量的聚合,最终凝固形成粉末。雾化颗粒形成示意图如图3 所示[18]。
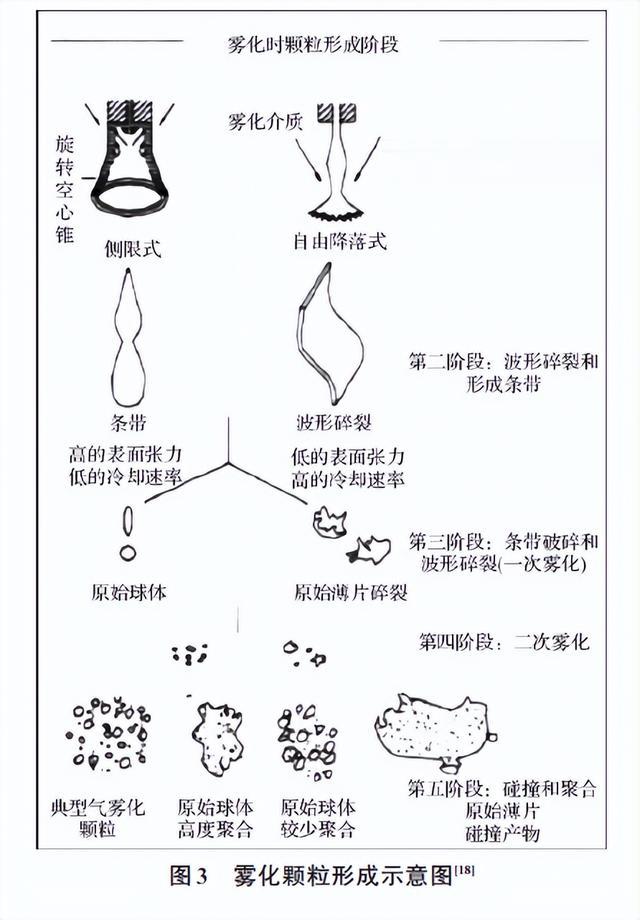
福田采用水压为90~150 Mpa、水流量为300~800 L/min 进行雾化,可制备出50%直径0.1~5 μm,球形度0.6~0.9 的粉[19]。国内企业在这方面也开展了大量研究和应用,钢研院用于不锈钢粉末的生产,超高压水雾化压力可达100 MPa,流量为150 L/min,可制备10~15 μm的316L 不锈钢粉末和10 μm的铜基胎体粉末[20]。日本雾化金属粉末公司采用高压水雾化制备铜、银等金属粉,可以商业化生产1.5 μm 的粉末,在80 MPa 压力时粉末粒度为5 μm,空气分级能够得到1 μm粉末[20]。
2.3 化学还原法
化学还原法,是将还原剂加入至可溶性金属盐溶液中,在一定酸/碱性条件下进行氧化还原,将金属离子还原成金属原子,进而成核生长成为形貌有所差异的单质金属颗粒的方法。利用还原剂还原氧化物及相应盐类制取金属粉,可用于球形、类球形、片状粉末等的合成。
在化学还原制粉过程中,反应是在液相或类液相状态下进行,金属盐以及还原剂的种类与浓度、反应温度、体系PH值、保护剂种类与投加量、反应时间等都对金属颗粒的粒径与形貌有重要的影响。因此,液相化学还原制粉的关键是稳定的反应体系。
同和、三井、福田等采用该方法进行了微细铜粉的制备,通过采用还原剂将铜源进行还原,得到超细铜粉,可制备不同形貌的超细铜粉以及铜纳米线[21-23]。国内,中国船舶重工集团公司第七一二研究所、中科院、中南大学等均有相关的研究和发明专利[24-27],可进行粒径可控的微纳米金属粉体制备,形貌为球形和多面体,产品应用于电子浆料、印刷电路、润滑剂、催化剂等,应用前景广阔。
2.4 机械法
机械法,是利用硬质媒介物的搅拌研磨,或是粉末在高速气流中强大的压缩力和摩擦力作用下来进行金属粉的磨碎的一种方法。常见的是球磨法,其原理是利用球状硬质材料对金属物料进行强烈的撞击,使物料经破碎、研磨后粒度减小,从而制得超细金属颗粒,已广泛应用于片状金属粉末的研发和生产[28-30]。采用该方法的优点是操作简便,产能较大;缺点是产品的粒径分布较宽,生产过程容易引入杂质;对设备进行改进后将有很广阔的应用前景。
采用该方法,三井进行湿法研磨,可制备片状粉,采用介质球,通过高能球磨使粉末发生塑性变形,从而制成片状,该方法须严格控制原料的粒径分布。中南大学在这方面也有研究,发明了一种水性体系下制备片状粉末的方法[31],其中,铜粉的加入量与球磨介质的质量为1:5.05~10.4,助磨剂可以是二乙醇胺、三乙醇胺、丙二醇或者六偏磷酸钠等。
2.5 粉体后处理技术
粉体后处理技术主要包括对粉末粒径的控制和表面抗氧化处理。
2.5.1 粒径控制
粉体被收集后成为原粉,原粉分级形成不同规格的分级粉产品,不同于常规粉末,超细金属粉的分选对精度要求较高。分级机结构示意图如图4 所示,粉体通过入口进入分级室,由分散叶片和圆盘两级分散系统充分分散;粗颗粒由于转子的离心力被带向出口方向,细颗粒被吸进由附属叶片引起的空气流中,并通过转子到涡型管罩中收集。分级机的切割粒径可通过改变转子速度或空气流速来调整。
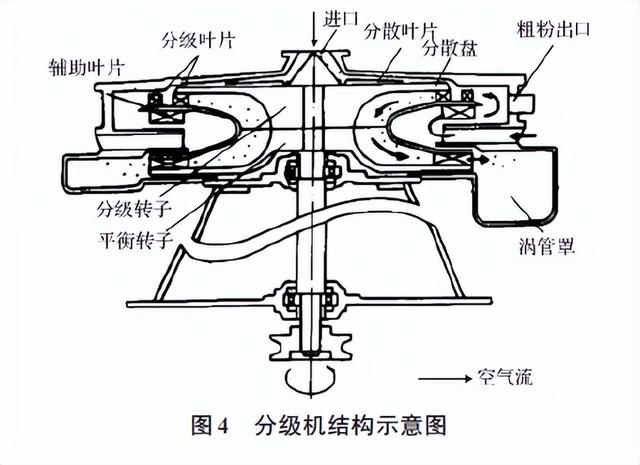
3.5.2 抗氧化处理
金属粉的抗氧化处理是通过对金属表面改性获得的,表面转化技术是用物理化学方法处理材料表面,使材料本身组成结构发生变化,从而使性能得到改变,常见的表面活性剂处理、表面包覆金属、偶联剂处理、高分子表面包覆、磷化处理等。
3 未来发展趋势
随着信息产业高速发展,电子浆料作为微电子技术领域关键材料占据着举足轻重的位置,为提高产品市场竞争力并推动其产业化发展,开发出性价比较高的贱金属浆料将是未来发展趋势。
微细金属粉体材料今后的发展将主要集中在制备方法、性能及应用三个方面:(1)制备方法方面主要在于新的原理、方法及设备等的探索,目的在于开发出高纯、高精度粒径分布、以及片状粉末制备技术。(2)性能方面,不断探索改性处理工艺技术,目的在于经过改性或表面处理,使粉体性能提升,同时降低制备成本,替代进口产品。(3)应用方面,积极探索光、电等新的应用领域,目的在于研究不同领域对金属粉体的需求,以满足不同行业的发展需要。
4 结语
中国是全球最大的电子信息产品制造中心及应用市场,具有巨大的消费需求。近年来,关键电子元器件、光伏、新型显示、微电子封装等行业发展景气,市场需求迫切,促进了电子浆料以及微细金属粉体材料的发展。由于我国在该领域起步较晚,硬件、软件不足,在初期限制了其发展,到目前为止,已经发展了近30 年,正处于从代工到技术创新的时期,恰逢全面转型升级和快速发展阶段。目前,正不断开发出球形、片状等微细金属粉体制备技术和设备,不断探索粉体处理技术,应用领域也从中低端向高端迈进。随着微细金属粉体材料的制备方法、工艺设备等的不断改进和升级,粉体处理技术不断推陈出新,粉体的性能将得到提升,应用领域和应用范围也将不断扩大,在未来,国产电子浆料及微细金属粉体材料的市场占有率和国际竞争力将不断提升。