摘要:本文将针对小开孔设计的焊膏印刷应用要求,重点讨论008004"/0201(公制)元件的具有挑战性的开孔的印刷实验设计结果。随着摩尔定律继续应用于元件小型化,下一步减小封装尺寸的电阻和电容尺寸将是008004"/0201。大约一粒沙子大小的元件,对焊膏印刷工艺提出了明确的挑战。为了应对这一挑战,需要检查印刷过程的各个方面。为了满足苛刻的技术规范要求,基本的设备要求包括正确的刮刀、工装支撑和校准。我们将讨论材料的正确匹配和设计,重点是模板和基板设计以及对焊膏和清洗溶剂的要求,还将报告一个实验设计,它应用了所讨论的设备和材料,包括印刷机和焊膏检测(SPI)设置以及使用的特定设备参数。并仔细研究这些实验设计的结果。
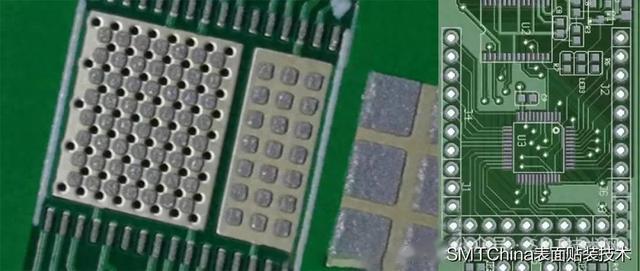
引言
摩尔定律指出,一个微芯片可以容纳的晶体管数量预计每两年翻一番。同样的趋势也适用于元件的小型化。移动设备、智能手表、可穿戴机器、军事、医疗和音频技术对高功能性的需求,继续推动着元件向小型化方向发展。SMT行业每4~7年就会引入下一代的小型化元件,最新推出的元件尺寸为008004″(0201 mm)。与01005″(0402 mm)封装尺寸相比,其面积减小了6%,体积减小了1.6%,设备制造商已很快适应了这个下一代挑战。然而,在将微型器件引入制造过程时,需要解决的问题是印刷工艺。为了成功地将008004″(0201 mm)元件引入制造过程,需要解决与其相关的材料、设备和工艺问题。开发了一种可以生产含有008004″(0201 mm)元件的产品工艺,当该工艺的每个要素协同工作时,其Cp值可以达到其能力的两倍。这将要求工程师重新评估其目前的工艺流程,以满足008004″(0201 mm)元件的挑战需求,实现成功组装。这可能会要求洁净室环境。本文的重点是印刷工艺的各个要素以及在马萨诸塞州霍普金顿的ITW EAE工艺实验室进行的测试结果。
元件现状
大多数产品制造已经适应了0402″(1005 mm)元件。最近0201″(0603 mm)元件的使用也越来越普遍,01005″(0402 mm)刚刚进入产品制造的主流。每一步,我们都对模板设计和材料进行了调整,以便在我们的设计中应用这些元件,但很少或没有考虑其他的关键要素。印刷008004″(0201 mm),要求我们在制造第一个基板之前,要检查每一个工艺要素,以确保每个要素的设计都考虑了该元件所带来的挑战性。微型元件印刷解决方案是一个多要素的集合体,需要通过每个要素的最佳实践来获得最佳结果。任何偏差或忽略任何要素都将导致不可重复的工艺过程。
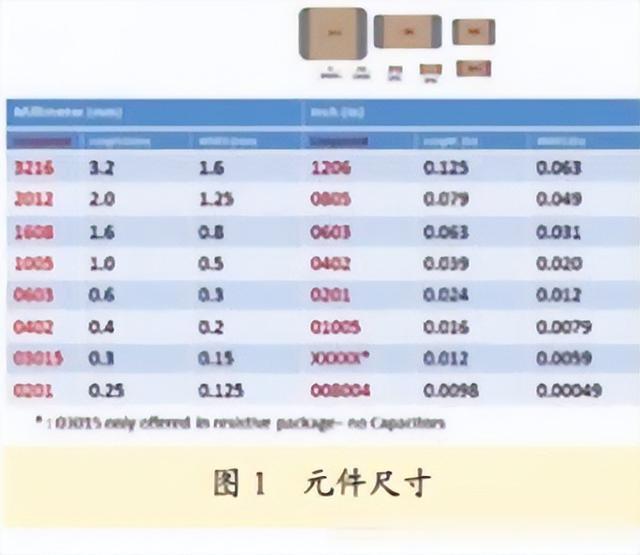
印制电路板(PCB)
大多数PCB设计在产品制造之前就已经完成了。面向制造的设计往往被成本要求所忽略。我们经常面临的问题是,必须根据电路板来设计工艺,而不是根据制造工艺来设计PCB,因此,我们需要做出调整和妥协,以适应PCB设计中的不足。确保成功设计的PCB实现可重复的制造结果,这是工艺工程师发挥作用的地方。到目前为止,主要应用的大多数基板都几乎没有采用微型元件的混合技术。混合技术问题也称为宽幅印刷问题,不是本文的重点,尽管在继续向前发展之前需要解决这个问题。到目前为止,大多数应用使用的PCB厚度为0.030″(0.762 mm)或更小,这是意料之中的。根据PCB的厚度和布线的数量,可能需要特殊的载体将产品从一台设备转移到另一台设备,并在回流焊过程中使产品保持稳定。成功印刷中PCB起主要作用的关键要素之一,是在模板和PCB之间形成密封的能力,通常称为密封。密封在工艺过程中所发挥的作用是,将焊膏从模板开孔中高效且可重复地转移到PCB焊盘上。通过消除不同PCB之间掩模厚度的差异,保持一致的板厚是关键,因为这决定了PCB到模板底部表面的位置。应消除对焊盘表面的掩模侵蚀,掩模侵蚀将极大地影响开孔的密封能力。在PCB设计中应避免使用丝网印刷的字符。当丝网印刷的字符等于或大于所应用的模板厚度时,并且位于元件附近,就会出现问题。标识和标识信息应显示在PCB背面,或放置在对关键元件造成最小影响的位置。应避免使用条形码标签,条形码标签是许多较小的具有挑战性元件发生印刷问题的根源,如果可能,应在印刷过程完成后再施加条形码标签。在设计微型元件印刷的印制电路板时,确保焊盘没有明显低于掩模高度是一大误解。当设计一个带有裸铜焊盘的基板时,焊盘应刚好低于或等于掩模高度。如果焊盘低于掩模,这就产生了一个间隙,当焊膏印刷进入开孔时,必须克服这个间隙。由于焊膏必须从模板底部的开孔流动到焊盘表面,焊膏将无法与焊盘表面保持良好的附着力。其结果是不稳定的印刷结果,表现为无焊膏和焊膏量不足或没有充分覆盖焊盘。在某些情况下,由于印刷机的结果不稳定,有此问题的PCB将会变得不可制造。为了确保焊盘的位置与掩模的高度一致,并且具有平坦的平面,应考虑化学镍金(ENIG)工艺。ENIG电镀在化学镀镍层上覆盖一层薄层浸金,保护镍免受氧化的效果是最好的。在电路板设计中,使用掩膜限定焊盘经常会出现问题。在使用掩膜限定焊盘时,焊盘位置的准确性以及焊盘尺寸大于技术规范一直是问题。基准点的位置,特别是在进行多面板组装时,对于机器视觉系统正确执行对准至关重要。基准点应该是原图的一部分,并出现在PCB图像上,以获得最佳效果。避免在面板连接处定位基准点,因为这往往会增加对准误差。应避免拉伸、台阶和重复误差,因为我们所组装的焊盘的推荐尺寸为0.005″×0.006″(0.127×0.152 4 mm2),其中0.001″(0.025 4 mm)的误差可能会造成严重的后果。在PCB设计和制造方面的前期工作是确保成功组装的关键,因为之前描述的一些问题通常很难克服甚至不可能克服。
刮刀/封闭头
最佳做法是分离一套专用于微型元件印刷的刮刀。这样可以确保所使用的刀片没有损坏和磨损。微型元件印刷的刮刀要求很简单,方边的弹簧钢刀片就可以了。如果标准刮刀角度设置为60°,建议使用55°的刮刀角度。这一角度可使刮刀在开孔上有更多的表面积,以促进开孔填充。当刮刀通过开孔时,这个角度也改善了焊膏剪切,以防止焊膏拖出和不稳定的开孔填充。刮刀长度应尽可能与PCB匹配,在X方向上最大尺寸范围在PCB尺寸的2″之内。这将使刮刀压力集中在印刷电路板上,并防止对模板的长期损伤。每次使用前都要检查刮刀的清洁度和损坏情况。值得注意的是,密封式刀头在今天的精细印刷应用中取得了巨大的成功。从加压室挤出的流体适合于微型元件印刷的可重复的开孔填充。有些6型焊膏的模板寿命是有限的,封闭腔解决了这个问题,并最大限度地减少了焊膏浪费。在这次测试中,我们主要关注的是刮刀,因为它代表了市场上大部分的工艺应用。
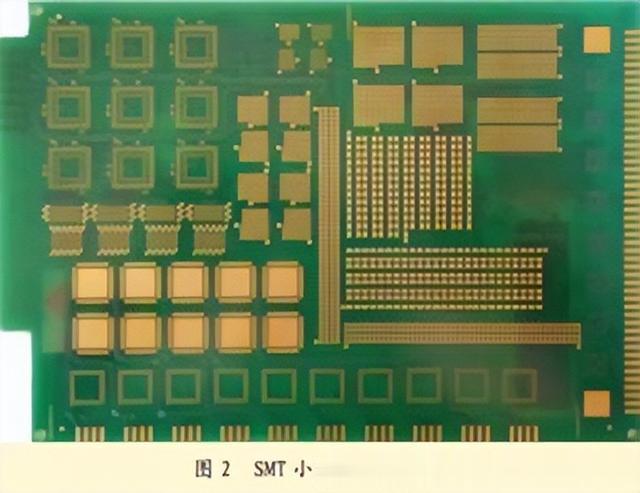
模板
在本实验中,我们使用了一个29″×29″(736×736 mm2)的细晶粒激光切割模板,并涂有纳米涂层,模板厚度为0.002″(0.050 8 mm)。矩形开孔尺寸为0.005″×0.006″(0.127×0.152 4 mm2),形状是一比一的,没有缩小或变化。根据之前的实验,我们确定0.002″厚的模板具有最佳的转移效率。当指定模板厚度时,我们通常会更多地考虑焊膏要求范围的两端,并在两者之间找到一个折衷方案。到目前为止,使用微型元件印刷的大多数应用都有兼容元件的混合技术,在要求上没有显著差异。我们使用的框架尺寸为29″×29″(736×736mm2),但是,根据008004″(0201mm)应用的常见平均模板尺寸和下面概述的模板张紧要求,23″×23″(584×584 mm2)模板可能更适合。建议使用激光切割的细晶粒不锈钢模板。电铸模板已经不受欢迎,据报道存在开孔尺寸和箔厚变化问题,以及将拉伸引入图像的问题。建议使用高张紧箔板。模板的拉伸张力范围通常为28~40 N/cm²。大多数模板张力在30 N/cm²范围内。将张力增加到30 N/cm²的上限,可以防止模板拖动。模具拖动是指当你使用一个有大量开孔的箔模板时发生的拖动。现在焊膏已经粘附在PCB上,由于表面张力,在模板释放过程中会拉扯模板,导致较低的焊膏转移效率。更高的张力带来更清洁更平衡的没有转移问题的模板释放。建议使用纳米涂层,研究证明,纳米涂层可以提高转移效率。模板制造商已经改进了模板纳米涂层的应用方法,提高了模板的制造寿命。然而,腐蚀性焊剂和反复的强力擦拭最终会磨损涂层。应强调小心处理薄模板,因为它们很容易损坏。存放、在机器上加装和卸载时应特别小心。在机器上操作刮刀时也要小心,因为刮刀掉落会损坏模板。印刷后用超声波清洗模板,对模板延长使用寿命至关重要。6型焊膏很难清洗,如果使用后不及时清洗,会变得难以清洗掉。
焊膏
这一开孔尺寸的推荐焊膏为6型粉末焊膏。6型粉末的技术参数为+635目,粒径范围小于20 μm,平均粒径10 μm。4型粉末是目前SMT市场上常用的焊膏粉末。粉末粒度成品率的显著提高降低了4型和5型粉末的定价。然而,6型粉末定价一直保持不变,相对价格是目前正在使用的4型粉末的三倍。刮刀速度和释放参数取决于焊膏配方和助焊剂的类型。从印刷的角度来看,6型粉末焊膏的印刷和任何其他焊膏一样,但还需要考虑在下游方向的要求。在使用6型粉末焊膏时,还必须考虑焊膏与拾取和放置元件的匹配以及回流焊期间使用氮气的要求。对于0.005″×0.006″(0.127×0.152 4 mm2)开孔的最佳做法是使用6型粉末焊膏,需要进行进一步的实验,看看混合5.5型粉末或5型粉末是否可以替代6型粉末。
PCB支撑
印刷方面的共识是,工装支撑对于成功的、可重复的印刷结果至关重要。铝制工装板仍然是所有其他形式的支撑测试的检验标准。由于大多数微型元件印刷应用,使用0.030″(0.762 mm)或更薄的印刷电路板,需工装与真空辅助相结合,这将产生最佳效果,以确保PCB是平整的、水平的和有支撑的。该支撑板的设计应使PCB正好在凹坑内,PCB表面位于工装表面之上。还建议使用支撑翼,支撑印刷区域外的刮刀,以防止对模板的长期损害。建议使用文丘里(Venturi)真空系统,因为标准真空系统产生的Hg(英寸汞柱)可能不足以压平PCB。当在支撑板上实施真空开孔时,开孔尺寸应考虑相关的PCB厚度,以防止PCB表面发生挠曲或“凹陷”。需要特别注意工装板夹具底部的找平。这将影响PCB到模板的密封。为了解决如何在印刷过程中保持印制电路板的位置,真空是确保厚度低于0.030″(0.508 mm)印制电路板表面平坦或侧面夹紧的首选方法。
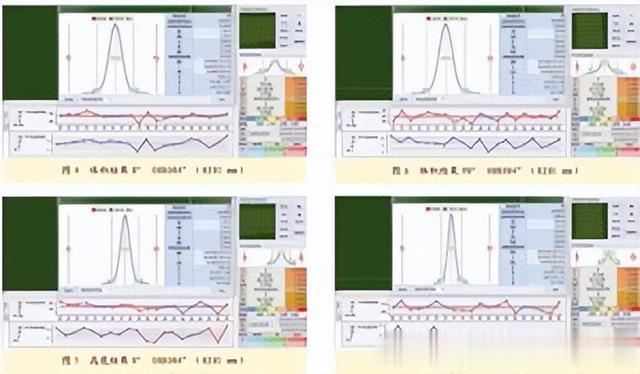
擦拭
擦拭是防止缺陷的第一道防线,但是也可以对工艺过程产生积极的或消极的影响。确定正确的频率、擦拭顺序、兼容的化学品和材料将提高印刷重复性并消除潜在缺陷。微小尺寸的开孔需要更频繁的擦拭,通过一个简单的实验就可以确定擦拭频率起始点,然而,过度的溶剂擦拭会产生与不充分擦拭相同的负面影响。简单的实验测试:每印刷一块基板,然后驱动模板下面的视觉摄像头,检查开孔中是否有焊膏挤出或开孔堵塞。注意,根据转移效率和模板质量,开孔中会有一些未释放的焊膏。在大多数情况下,这些焊膏会在下一次印刷工序中被推出,不需要擦拭,应相应地进行判断。继续这个检查过程,直到开始形成缺陷。从总数中减去一块板,这就是你的起始频率。如果有焊膏检测设备,可以根据检测结果确定正确的擦拭频率。建议的顺序是真空/真空/干燥。组合真空的擦拭消除了从开孔中抽出的和遗留的任何焊膏,这是第一次真空的结果。溶剂的使用频率应降低,因为这种材料的目的是解决开孔周围可能积聚的焊剂。溶剂擦拭的建议频率为每4~6块板擦拭一次。推荐的溶剂擦拭顺序是溶剂/真空/干燥,总是从溶剂开始。请咨询您的焊膏制造商以获得推荐的溶剂,以确保使用的溶剂与焊膏助焊剂相兼容。应使用高质量的纸张,因为6型粉末焊膏可能很难清除,在这种情况下,经济型纸张可能会留下锡球和污染问题。
印刷机
印刷机在成功印刷008004″(0201 mm)元件方面起着重要作用。建议在印刷微型开孔之前,确保所有预防性维护和校准都是最新的。机器的对准能力对于处理小焊盘至关重要。机器视觉的可重复性和准确性的进步与微型元件的推出是保持同步的。然而,如果你的机器是在20世纪90年代设计的,那么它很可能就没有处理这些元件的精度分辨率。建议在开发工艺过程之前测试机器的视觉对准能力,这样机器经过验证后,能够更快地隔离和解决对准问题。这可以通过印刷验证过程来完成,使用嵌入机器的软件来测量焊膏沉积的准确性和重复性,结果将确定是否需要进行视觉校准。印刷机上另一个经常被忽略的关键校准是工作台与模板导轨的平行度。由于在印刷微型开孔时,密封是最重要的,因此该校准考虑了对模板导轨有影响的工作台的四个角,以确保PCB和模板之间的正确固定。这一被忽略的校准,很可能是在机器由制造商制造时完成的,并且在安装后再也没有处理过。进行这种校准的问题之一是其流程困难。用塞尺测量工作台到相邻模板导轨底部的距离。为了测量这四个点,量具被可重复地从一个角移动到另一个角,以使其距离在规范范围内。这个过程需要机器彻底停机,通常需要数小时才能完成。MPM开发的一种新工具,通过同时调整四个角来解决这一问题。到目前为止,工作台到模板的调平规范在+/-0.004″(0.101 6 mm)范围内。然而,研究表明,当规范降到+/-0.001″(0.025 4 mm)时,效果最好。为了消除工作台和工装板之间的任何公差问题,在此校准过程中,可以使用工装板作为参考。使用这种校准工具可以实现这一规范要求,并在成功印刷微型开孔中发挥重要作用。完成校准的时间已减少到大约1小时。最后,要彻底检查印刷机的清洁度,并清除所发现的任何焊膏残留物。许多问题的根本原因可以追溯到随机的焊膏沉积或随着时间推移而形成的残余焊膏。