如果不引进创新和开发突破性技术,创造有前景的市场和有竞争力的产品,确保国家安全,现阶段国内(俄罗斯)造船业的发展是不可想象的。
目前,由于俄罗斯在西伯利亚、北部海域大陆架开发油气田计划的实施,对优质低碳低合金普通钢、增强钢和高强度钢的需求有所增加。
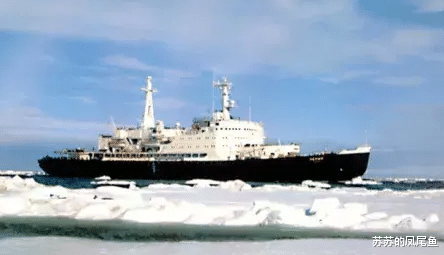
传统上,提高造船用钢的强度是通过增加碳含量来实现的,但今后,由于希望在提高强度的同时保持高延展性,因此必须使用合金钢。50年代,随着广为人知的AK25级钢材的开发,第一批船体钢材的制造工作达到了顶峰。第一代潜艇的艇体、“列宁 ”号(图 1)等核动力破冰船的建造以及 “瓦尔沙维扬卡 ”型潜艇的大规模建造都使用了这种钢材。70 年代初,随着电渣重熔技术的开发和引进,合金钢的技术和物理机械性能得到了显著改善。使用电弧炉生产船体钢的技术取代了以前使用的主要露天炉冶炼技术,以及同时过渡到在大功率轧机 “Quarto ”上轧制钢材而不是在过时的轧机 “Duo ”上轧制钢材,使得钢材的质量及其技术性能大幅提高,尤其是焊接性。得益于这些工程,70-80 年代,国内造船业获得了世界上强度最高、质量最好、技术最先进的船体材料。与此同时,还对钢的精细结构、合金与结构和力学性能的关系进行了研究,从而使碳和合金元素的含量降至最低,以确保通过淬透性和削弱回火脆性。利用创建和应用高强度钢的经验,进一步开发了屈服强度高达620MPa的AB级高强度可焊接钢,在加工性(焊接)方面甚至超过了上述AK25牌号钢。为了解决开发北极大陆架油气田的任务,考虑到俄罗斯西北部地区主要造船厂的地理位置,几年前就开始着手开发各种强度等级的耐寒钢材。开发的钢材可用于各种类型的平台、冰上航行船舶的建造以及在北极和远北地区运行的基础设施。对结构材料的要求非常高:—屈服强度从235MPa到690MPa;—高可焊性,可在低环境气温下对钢材进行无加热焊接,以便在开放式船坞或在近海条件下组装结构,这就要求减少碳当量;—具有各向同性的特性,在焊接过程中,在板材厚度方向的拉伸应力作用下,可防止金属分层断裂;—在低温和一次性暴露于风浪载荷、地震活动造成的静态、循环和动态载荷时,具有很强的抗脆性破裂能力。—在过去整个造船用可焊接船体钢材的发展历程中,我们制定了科学的材料制造原则,并在此基础上为在极端条件下使用的经济型合金船体钢材开发了新的冶金和焊接工艺。在实现高焊接性能的同时达到高强度,这就要求:—用镍、铜等元素进行合金化,同时降低碳含量;—使用改性添加剂细化晶粒(使用 Al、Al+Ti、Nb、V 微合金化);—热增强;—采用各种温控轧制或热机械加工(TMO);—大大减少S和P的含量,以及引入杂质:H、N、O;—在电弧炉和转炉中进行冶炼,并进行炉外精炼和真空处理。造船业的经验表明,特定牌号的船体钢材能否成功应用在很大程度上取决于其焊接性。