气密性封装电子产品堵漏新工艺探究
李瑶,袁飞,周晓冬,潘舟,吴雪峰
(武汉环达电子科技有限公司)
摘要:
现今常用的气密性封装工艺有平行缝焊封装和储能焊封装等。在实际生产或科研中,封装材料、封装设备和人员操作的熟练性等都会影响封装质量,一旦气密性达不到要求,重新封装需拆除盖板,操作难度大,成本高。改良的双组份环氧树脂胶堵漏工艺,配胶工序繁琐,堵漏胶固化时间长,固化后残留在焊缝区域的环氧树脂胶无法去除,易造成产品外观不良。提出了采用渗透性厌氧胶对气密性封焊失效产品进行堵漏的新工艺,并通过试验及实际生产,验证了该方法的有效性和实用性。
集成电路的封装,简而言之就是把经过组装和电互联的器件芯片与相关的功能器件和电路等封入特制的管壳内。在微电子集成电路和光电器件的制造过程中,气密性封装技术得到了广泛的应用,尤其在军用电子器件中,产品的气密性是主要考核指标之一。气密性封装的意义在于让管壳内的器件与外部环境相隔离,避免外部空气中的水汽和二氧化硫等有害气体进入管壳内。
平行缝焊作为电子元器件主要封装形式之一,普遍应用于对水汽含量和气密性要求较高的集成电路封装中。平行缝焊封装合格的电子产品,能有效保护管腔内的IC、电阻和电容等元器件,使得IC引脚、电阻和电容端头等不易被氧化,保证产品长久持续地正常工作。
1 现有问题分析
在实际科研和生产过程中,平行缝焊的质量直接关系到电子元器件的气密性 [1-2] ,而影响平行缝焊质量的因素多种多样,如盖板热处理工艺、盖板与管座焊接处的工艺卫生、夹具的精度、电极表面的状态和工艺参数的设置等 [3-4] ,都会导致焊缝的气密性达不到要求,封焊失效。
封焊失效的模块需经过返修后方可使用,最直观的返修方法是拆除漏气的盖板,更换新盖板进行重新焊接。这种方法虽说一定程度上能解决封焊失效问题,但平行缝焊盖板厚度为0.08~0.30 mm之间,拆除难度大,易损伤管座。即使能有效拆除,重新封装前需对管座进行机械化抛光处理,平整度等质量难以控制,工序繁琐,效率低,成本高。
经气密性封装从业人员的不断摸索和试验,环氧树脂胶堵漏工艺已逐渐取代上述的拆盖板重封,并被应用到气密性封装失效返修中。以较常用的某透明环氧树脂胶为例,该环氧树脂胶为双组份,需进行配比、搅拌均匀后再涂抹于焊缝处。使用该环氧树脂胶进行封焊失效堵漏,缺点较为明显:1)使用前的配胶和搅拌工序操作繁琐,难以控制;2)在常温条件下固化24 h或40 ℃条件下固化16 h或80 ℃条件下固化2 h,固化时间太长;3)焊缝区域残留的胶液固化后硬度大,难以去除,易造成外观不良。
为了优化堵漏工艺,提高堵漏效率,本文提出了采用渗透性厌氧胶对气密性封装失效产品进行堵漏的新工艺,并通过前期试验及后续实际生产,验证了其有效性和实用性。
2 工艺方案及试验
2.1 厌氧胶固化机理
厌氧胶的反应机理 [5] 如图1所示。
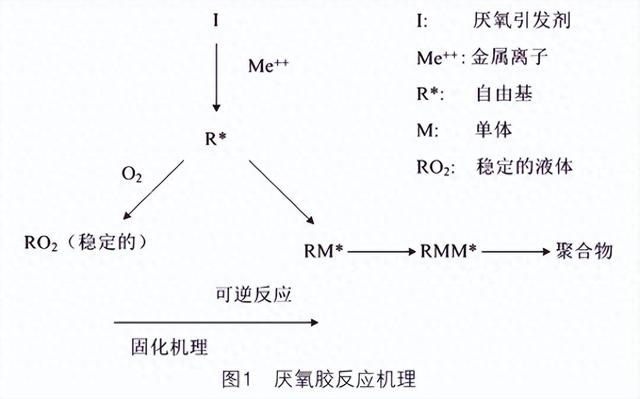
厌氧胶一般在常温下即可固化,温度升高时可以使其加速固化。根据图1可知,其固化需具备以下两个条件:
1)厌氧胶在固化过程中必须有金属离子参与,即厌氧胶必须涂抹在金属材料上才能固化;
2)厌氧胶必须在无氧条件下才能固化,未渗透到裂纹和微孔内的胶液是不固化的。
2.2 堵漏材料选择
在电子产品中常用的厌氧胶主要用于螺纹的锁固和密封。本文所使用的厌氧胶是一种单组份、低黏度的渗透性厌氧胶,由于它的低黏度和毛细管作用,使得它既可以应用于螺纹锁固和密封,也可以应用于填充密封缝焊焊接和浇铸等金属零件的空隙( d 0.125 mm以下),其常规特性见表1。

2.3 堵漏工艺流程
所使用的厌氧胶为单组份胶液,在胶液未被污染的条件下,可回收多次利用,具体堵漏工艺流程如下:
1)清洗:采用酒精等溶剂清洗漏气组件的焊缝;
2)烘烤:将漏气组件放入60 ℃的电热鼓风干燥箱中烘烤30 min后取出冷却到常温;
3)涂胶:用牙签蘸取厌氧胶刷涂到焊缝区,保证胶液完全覆盖焊缝区;
4)固化:常温条件下固化1 h或者40 ℃条件下固化30 min;
5)清理:用酒精等溶剂清洗焊缝区残留的余胶,回收多余未使用胶液。
2.4 试验步骤
2.4.1 气密性封装
选取管座和盖板皆为可伐合金的同一批管壳(数量大于30套)进行平行缝焊封装。
2.4.2 检漏
按GJB 360方法112试验条件D,试验条件选取下列其中一种执行:a)当样品引脚数≤16时,加压压力不低于40 N/cm 2 ,时间不小于2 h,氟油液体温度125±5 ℃;b)当样品引脚数大于16时,加压压力不低于20 N/cm 2 ,时间不小于4 h,氟油液体温度125±5 ℃;c)采用平行封焊的模块,加压压力不低于20 N/cm 2 ,时间不小于4 h,氟油液体温度125±5 ℃。
检漏过程中,如发现漏气模块,用红色记号笔在漏气位置做上标识,如图2所示,并分类放置。
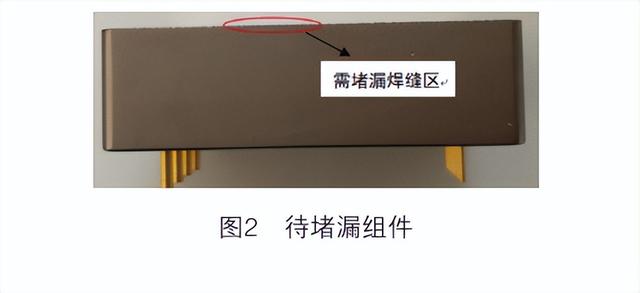
2.4.3 堵漏
按照2.3中堵漏工艺流程对漏气模块进行堵漏处理。
2.4.4 检漏
堵漏后的模块先按照GJB 360B方法112试验条件D进行粗检漏,漏率合格产品再应用氦质谱检漏仪进行细检漏,记录漏率数据。
2.4.5 筛选试验
将经检漏后漏率合格的产品依次进行高温贮存、温度循环和功率老炼等筛选试验。每完成一项筛选试验后,需恢复2 h再进行下一项试验。高温贮存试验按GJB 150.3试验方法进行,试验条件选为:
a)贮存温度:85±2 ℃;b)贮存时间:72 h;温度循环试验按照GJB 548方法1010进行,试验条件为-40±3 ℃~85±2 ℃,循环≥10次。功率老炼试验按照GJB 548方法1015进行,试验条件为85±2 ℃,时间96 h。
2.4.6 检漏
经过筛选试验后的模块先按照GJB 360B方法112试验条件D进行粗检漏,漏率合格产品再应用氦质谱检漏仪进行细检漏,记录漏率数据。
2.5 试验结果
堵漏后筛选试验前的模块,先经过氟油粗检漏,未发现漏气现象,再经过氦质谱细检漏后,发现漏率值皆小于1.05×10 -9 Pa·L/s,满足GJB 548B-2005的要求。
筛选试验后的模块,经过氟油粗检漏,未发现漏气现象,且经过氦质谱细检漏后,发现漏率值小于1.05×10 -9 Pa·L/s,满足GJB 548B-2005中的要求。
3 结论
通过本次试验结果可知,渗透性厌氧胶能有效填充气密性封装封焊失效产品中的焊缝( d 0.125 mm以下)。对比于拆除盖板重新封装的传统返修工艺和改良后的环氧树脂胶堵漏工艺,渗透性厌氧胶堵漏新工艺具有如下诸多优点:1)工艺流程更加简单,操作更便捷;2)堵漏胶固化条件易满足,固化时间短,能有效提高堵漏效率;3)焊缝区域多余的胶液不固化,可用酒精擦除,堵漏前后模块外观无明显变化,不会造成外观不良;4)堵漏结束后,未使用完的胶液可回收重复利用,节约返修成本。
4 实际应用效果
渗透性厌氧胶不仅适用于平行缝焊堵漏返修,还可将其应用于储能焊封装等空隙小于 d 0.125 mm的气密性封装产品的堵漏返修中。
参考2.4中的试验步骤,对同一批(数量大于30套)储能焊封装模块进行堵漏试验,堵漏后的模块先按照GJB360B方法112试验条件D进行粗检漏,未发现漏气现象,再经过氦质谱细检漏后,发现漏率值小于1.05×10 -9 Pa·L/s,能满足GJB 548B-2005中的要求。将堵漏合格的模块按照GJB相应标准,依次高温存储、温度循环和功率老炼等筛选试验后,再次进行氟油粗检漏和氦质谱细检漏,发现漏率值小于1.05×10 -9 Pa·L/s,亦可满足GJB548B-2005的要求。
5 结束语
采用渗透性厌氧胶堵漏新工艺,能有效解决气密性封装产品漏率不达标的问题,从而降低返修返工难度和成本,提高气密性封装封焊失效产品的返修效率。但是,根本上解决气密性封装问题,应从盖板热处理工艺、盖板与管座焊接处的工艺卫生、夹具的精度、电极表面的状态和工艺参数的设置等方面进行改进和优化,减少不良率,提高气密性封装产品的质量。