在日常工作中,应用价值管理的思想意味着要识别和优化那些能够为企业带来最大价值的流程环节:
识别价值环节:分析流程中的每个环节,确定哪些环节为客户创造了真正的价值。精简不增值环节:去除或简化那些不增加价值的步骤,减少浪费,提高效率。持续改进:通过持续的监控和评估,不断寻找提升流程价值的机会。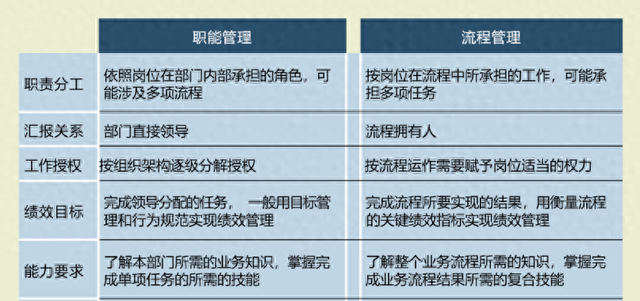
概念学习

流程评价


案例说明

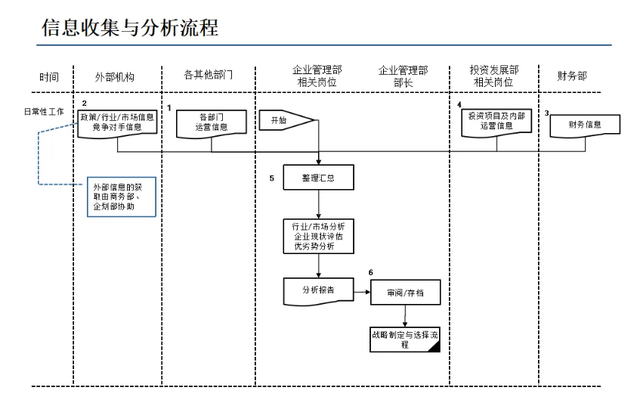
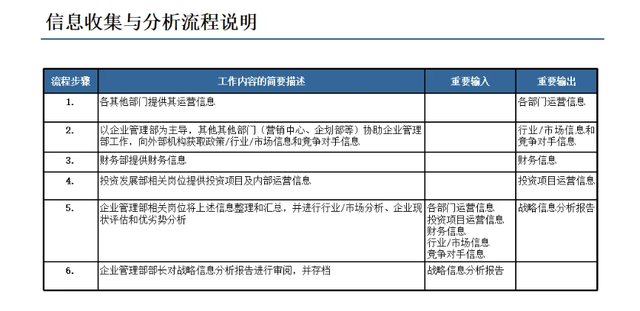
对加工工艺改进优化 精益生产要求人员按标准工艺工作,按节拍进行生产。根据精益生产方式、现代加工技术及工艺管理模式对零件“刷杆支架”的加工工艺进行合并调整,对加工工序中的50、60、80、90工序合并成一道工序,采用加工中心机床进行加工,仅此一项,不但节省了加工费用,更缩短加工时间,保证了质量,提高了产品的合格率。
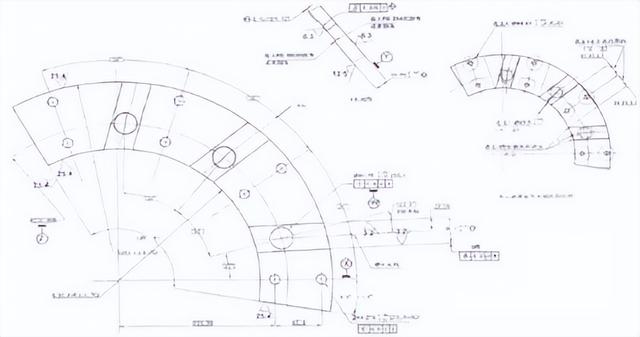
①生产成本分析。该零件工艺技术复杂程度中等,有形位公差要求。经过设备调整和工序调整后,增加了资金的投入,购置了立式加工中心。
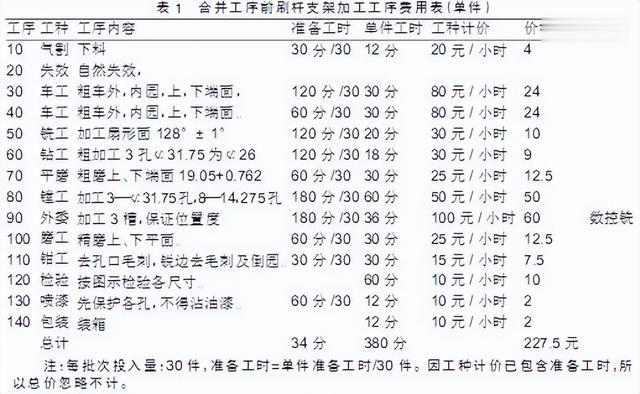
但是从表1与表2的对比中可以看出加工费用不但没有增加,还有所降低。更重要的是提升了企业的生产加工能力和扩大了生产范围。
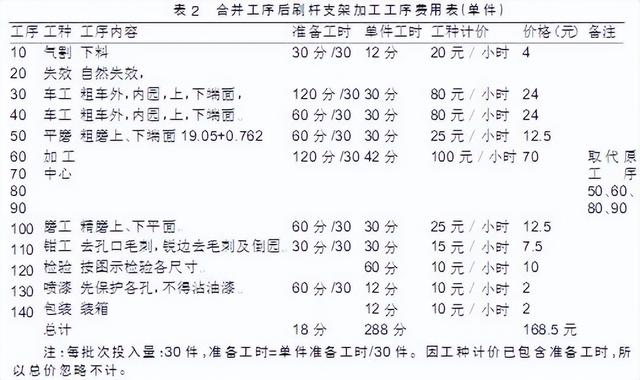
A. 原成本:
Q原工序费用=E50工序+E60工序+E80工序+E90工序=10+9+50+60=129元
B. 现成本:
Q加工中心=E加工中心工件单价·H工序时间=100x0.7=70元
②工序能力分析。从单件工时来看限制工序能力的瓶颈主要在80、90、120工序,而120工序直接通过增加检验人员可以解决,因为80、90工序则比较复杂,工艺要求较高,由于工人的加工技术参差不齐,造成产品质量极不稳定,合格率较低,更导致生产效率的低下。所以,必须通过改进工艺和调整加工设备,才能提高生产效率保证加工质量,直接提高产品零件合格率,使工序能力得到极大的提升。
③生产周期分析。由于50、60、80、90工序时间较长,加工内容多,存在不确定性,容易造成生产周期的延长和混乱,经过50、60、80、90工序的调整合并后,改由加工中心机床一道工序加工,工序时间也由原来134分钟/单件工时(合并前)缩短到现在42分钟/单件工时(合并后)。单件总工时也由原来“80分钟/单件总工时”缩短到“288分钟/单件总工时”,大大节约了工序加工时间,直接缩短了零件加工的生产周期。